-
No.66 Gaojia, Xingfu Village, Sanqi Town, Yuyao, Ningbo,China
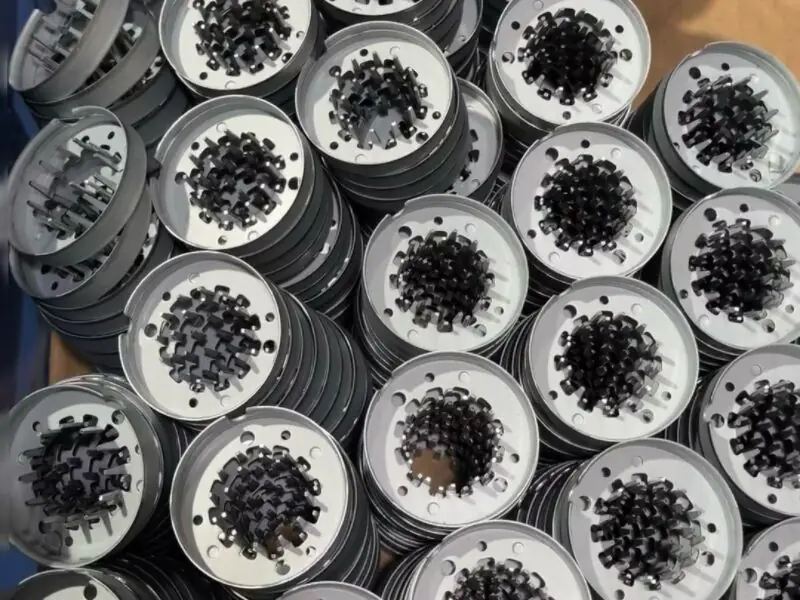
3 Proven Ways to Reduce Metal Stamping Costs While Optimizing Turnaround Time
In today’s competitive manufacturing landscape, optimizing metal stamping costs and turnaround time is crucial for business success. This comprehensive guide explores practical strategies to reduce expenses while maintaining quality and efficiency in metal stamping operations. Whether you’re a manufacturing engineer or a business owner, you’ll discover actionable insights to streamline your metal stamping process and achieve substantial cost savings.
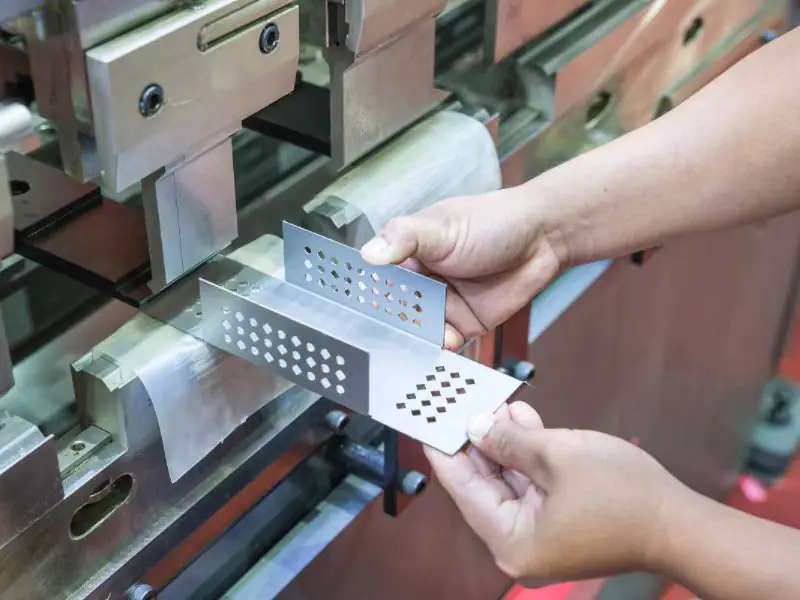
What Factors Impact Metal Stamping Costs?
The metal stamping process involves various cost components, from raw material selection to tooling costs. Understanding these elements is crucial for cost optimization. Material costs often represent the largest expense in metal stamping, while tool design and maintenance also significantly impact overall costs. A manufacturing engineer must consider these factors when planning production runs.
How Does Progressive Die Stamping Reduce Production Costs?
Progressive die stamping represents a significant advancement in metal fabrication technology. This efficient process reduces material waste and optimizes production time by performing multiple operations in sequence. By implementing progressive die stamping, companies can achieve substantial cost savings through reduced labor costs and improved cycle times. The precision metal stamping process ensures consistent quality while minimizing the need for secondary processes.
Can Material Selection Impact Your Bottom Line?
Choosing the right metal for your stamping project can dramatically affect costs. While exotic metal options might seem attractive, cheaper material alternatives often provide similar performance characteristics. A metal stamping company can help evaluate material options that balance cost-effectiveness with quality requirements. Smart material selection can lead to lower cost production without compromising product integrity.
What Role Does Tool Design Play in Cost Reduction?
Proper tool design is fundamental to reducing metal stamping costs. An experienced metal stamping professional can optimize die design to minimize scrap and enhance manufacturability. Well-designed stamping dies not only improve product quality but also extend tool life, resulting in significant cost benefit over time. Regular maintenance and design updates can prevent costly production interruptions.
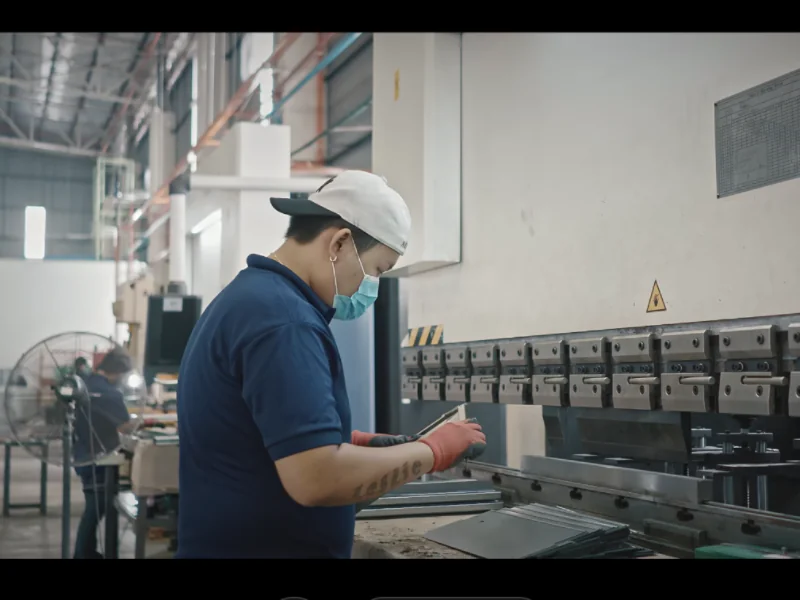
How Can Scrap Reduction Optimize Material Usage?
Implementing strategies to reduce scrap is essential in metal stamping manufacturing. By optimizing material usage through careful parts per sheet planning and efficient nesting, manufacturers can minimize waste. Keats Manufacturing and other industry leaders emphasize the importance of scrap reduction programs in achieving cost-effective production runs.
What Are the Benefits of Partnering with an Experienced Metal Stamper?
Working with an experienced metal stamping partner provides access to specialized knowledge and advanced metal stamping equipment. These professionals offer valuable design and planning assistance, helping optimize every step of the production process. Their expertise in compensating tolerances in design can prevent costly mistakes and reduce overall costs.
How Does Production Volume Affect Costs?
Understanding the relationship between production volume and costs is crucial for metal stamping projects. Higher production runs typically result in lower per-piece costs due to improved efficiency and distributed tooling costs. A metal stamping provider can help determine optimal production quantities to maximize cost-effectiveness.
What Role Does Technology Play in Cost Reduction?
Modern stamping machines and four-slide stamping equipment can significantly impact production efficiency. Investing in advanced metal stamping technology often leads to reduced labor costs and improved quality control. The right combination of technology and expertise can optimize the entire manufacturing process.

How Can Design Changes Impact Manufacturing Costs?
Strategic design modifications can lead to substantial cost savings in metal stamping. Working with a manufacturing engineer to test design changes early in the process can prevent expensive modifications later. Simple adjustments in product design may reduce the number of operations required, leading to lower production costs.
What Are the Best Practices for Reducing Turnaround Time?
Implementing efficient workflows and optimizing cycle times are essential for reducing turnaround time. Using progressive die techniques and minimizing secondary processes can significantly speed up production. Ways to reduce turnaround time include careful production planning and maintaining optimal machine settings.Key Takeaways:
- Progressive die stamping offers significant cost advantages through reduced labor and improved efficiency
- Material selection and scrap reduction are crucial for controlling costs
- Proper tool design and maintenance extend equipment life and reduce long-term expenses
- Partnering with experienced metal stamping professionals provides valuable expertise and cost-saving opportunities
- Technology investment and design optimization can significantly reduce production costs
- Volume considerations impact per-piece costs and overall project economics
- Regular evaluation of processes and materials can identify new cost-saving opportunities
- Efficient workflow management reduces turnaround time without compromising quality
- Design modifications early in the process prevent costly changes later
- Balancing quality requirements with cost-effective solutions ensures optimal results