-
No.66 Gaojia, Xingfu Village, Sanqi Town, Yuyao, Ningbo,China
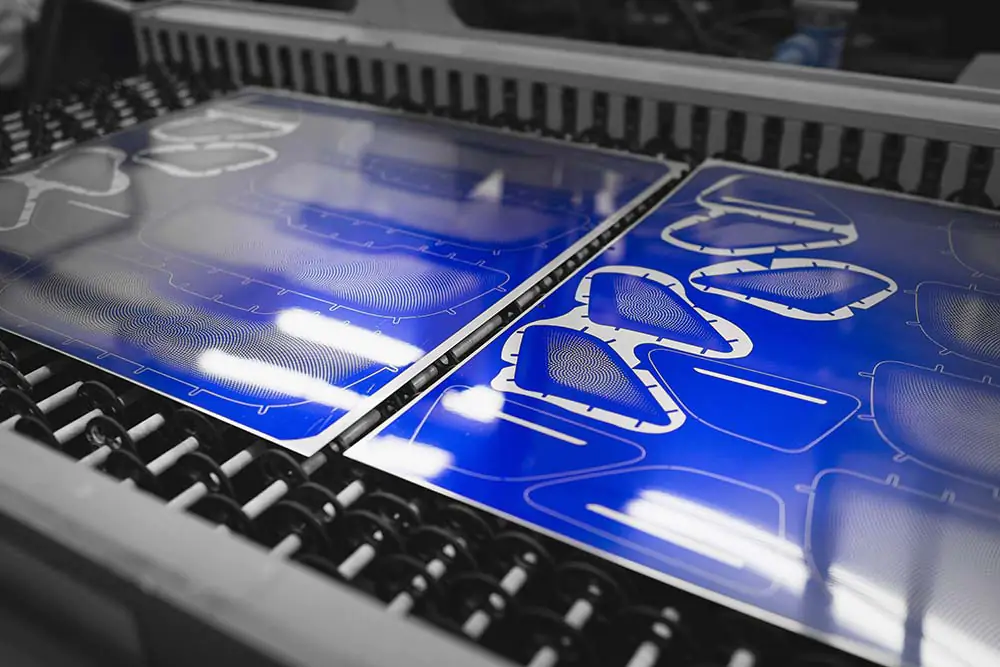
Chemical Etching vs Stamping: Which Metal Fabrication Process Is Right for Your Project?
When it comes to precision metal fabrication, choosing between chemical etching and stamping can significantly impact your project’s success. This comprehensive guide explores the key differences, advantages, and applications of both processes to help you make an informed decision for your next manufacturing endeavor.
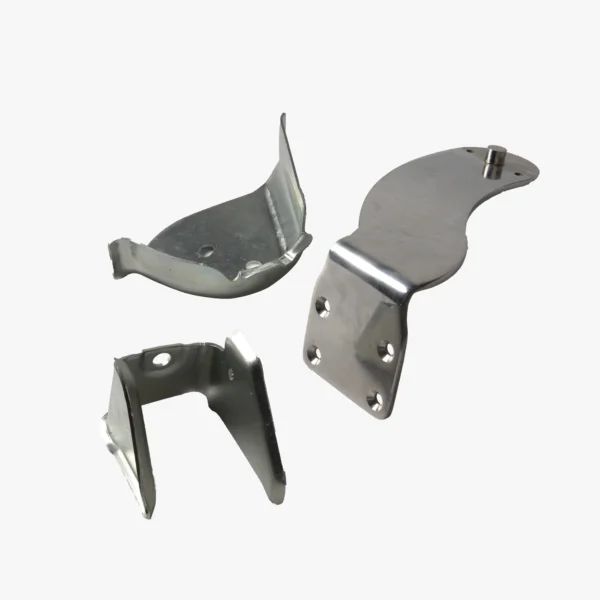
Precision-engineered stamped chassis brackets demonstrating the capabilities of metal stamping
What Is Chemical Etching and How Does It Work?
Chemical etching is a sophisticated metal fabrication process that uses chemical solutions to selectively remove material from metal surfaces. This process, also known as photo etching or photochemical machining, involves:
- Applying a photoresist coating to the metal surface
- Using UV light to transfer the desired pattern
- Exposing the metal to ferric chloride or other acid solutions
- Removing unwanted material through controlled chemical reactions
The process is particularly well suited for creating intricate designs and complex parts with high precision.
Understanding Metal Stamping: The Traditional Approach
Metal stamping is a manufacturing process where a stamping press and die surface forms the metal into desired shapes. This traditional method:
- Uses specialized tooling in the stamping press
- Forms parts through mechanical force
- Creates consistent, repeatable results
- Is ideal for high-volume production
Learn more about our stamping capabilities for precision components.
How Do Lead Times Compare Between Chemical Etching and Stamping?
One of the most significant differences between these processes lies in their lead times:Stamping Lead Times:
- Tool and die creation: 6-8 weeks
- Production setup: 1-2 weeks
- Total lead time: Can exceed 2 months
Chemical Etching Lead Times:
- Tooling preparation: 1-3 days
- Production setup: 2-4 days
- Total lead time: Matter of days
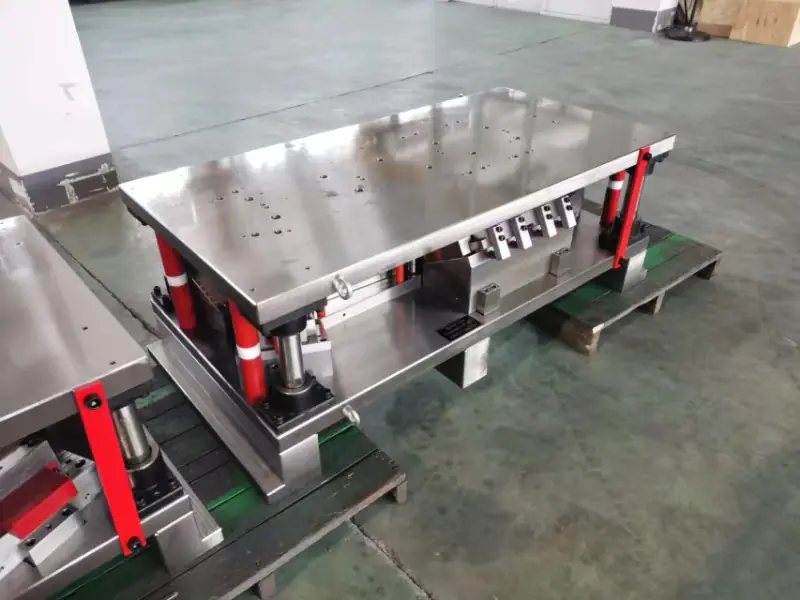
What Are the Cost Implications of Each Process?
The cost efficiency of each process varies significantly:Stamping Costs:
- One stamping die can easily cost thousands of dollars
- High setup costs
- More economical for large production runs
Chemical Etching Costs:
- Features no tooling cost
- Lower initial investment
- Cost-effective for prototypes and small runs
Which Process Offers Better Design Flexibility?
Chemical etching allows for greater design flexibility compared to stamping:
- Ability to create complex geometries
- No tool wear concerns
- Easy design modifications
- Perfect for intricate designs
Explore our precision metal components for examples of complex geometries.
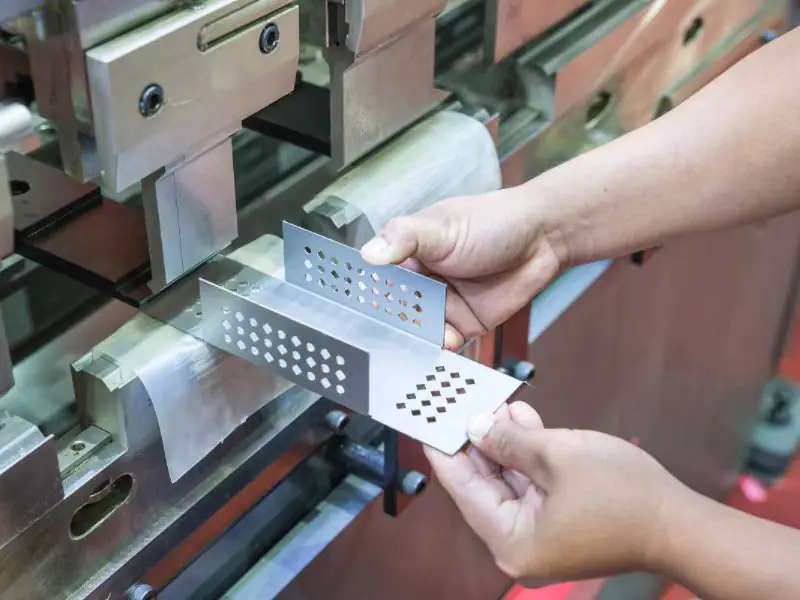
What Materials Work Best with Each Process?
Both processes can handle a wide range of materials, but their suitability varies:Chemical Etching Materials:
- Stainless steel
- Copper
- Brass
- Aluminum
- Nickel alloys
Stamping Materials:
- Carbon steel
- Aluminum
- Brass
- Stainless steel
- Precious metals
How Does Quality Control Compare?
Quality considerations for both processes include:Chemical Etching:
- Consistent material properties
- No mechanical stress
- No burr formation
- Excellent surface finish
Stamping:
- Potential for burr formation
- May require secondary operations
- Consistent part-to-part accuracy
- Excellent for high-volume precision
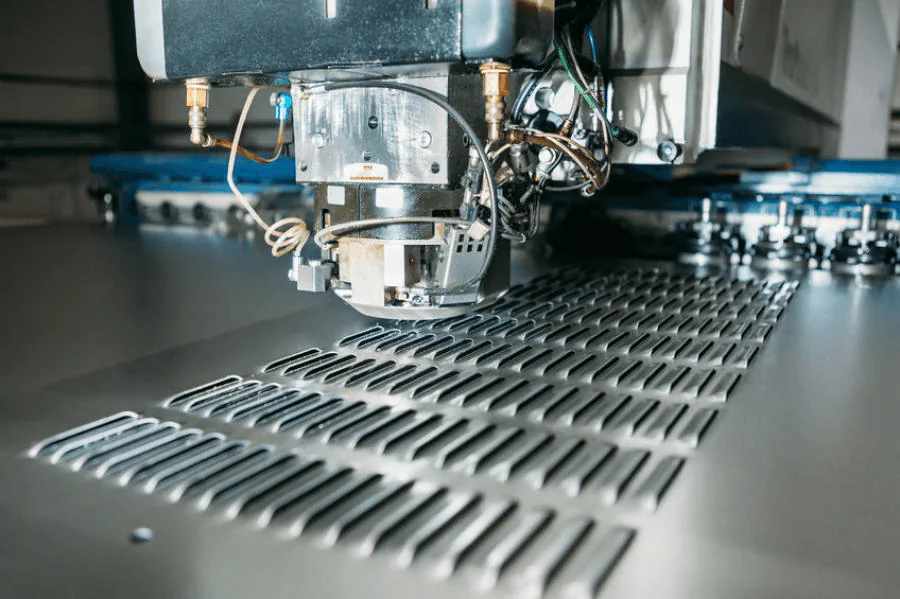
What Are the Environmental Considerations?
Environmental impact varies between processes:Chemical Etching:
- Requires chemical waste management
- Uses ferric chloride solutions
- Needs proper ventilation
- Regulated disposal procedures
Stamping:
- Generates metal scrap
- Higher energy consumption
- Noise pollution
- Material efficiency concerns
When Should You Choose Chemical Etching vs Stamping?
Selection criteria for each process:Choose Chemical Etching When:
- Producing prototypes
- Creating complex designs
- Requiring short lead times
- Working with thin materials
Choose Stamping When:
- Manufacturing high volumes
- Needing structural strength
- Producing simple geometries
- Cost per unit is crucial
View our metal stamping solutions for high-volume applications.
What Are the Future Trends in Both Technologies?
Industry developments have driven the industry to micro level precision:
- Integration of CAD/CAM systems
- Automation improvements
- Enhanced process controls
- Environmental sustainability
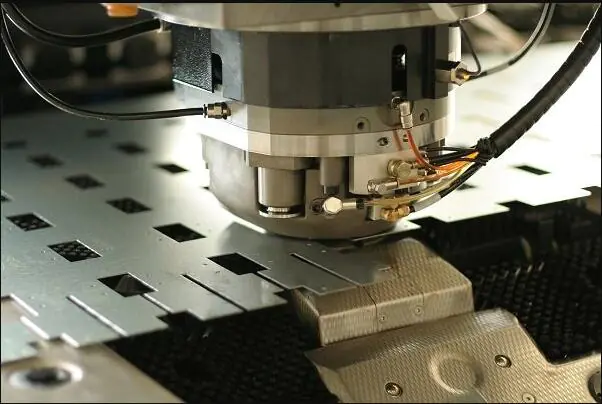
Key Takeaways:
• Chemical etching offers faster prototyping and complex design capabilities • Stamping excels in high-volume production and cost efficiency • Lead times are significantly shorter with chemical etching • Material selection affects process suitability • Environmental considerations play a crucial role in process selection • Each process has specific quality control advantages • Future trends point toward increased precision and automationRemember to contribute to your next R&D project by carefully evaluating these factors when choosing between chemical etching and stamping for your precision metal components.