-
No.66 Gaojia, Xingfu Village, Sanqi Town, Yuyao, Ningbo,China
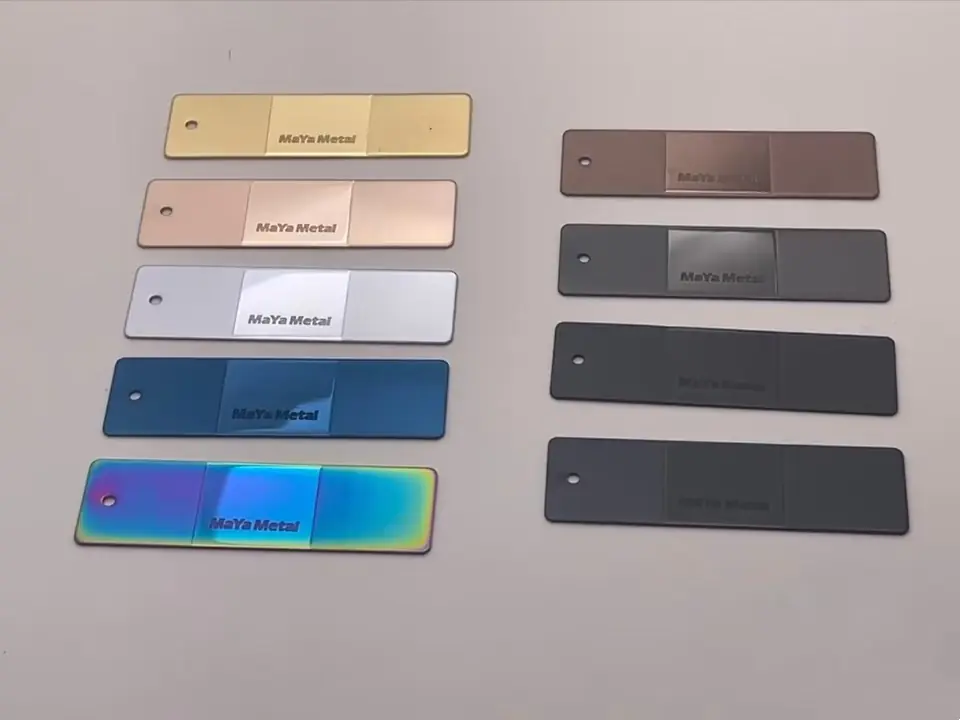
Choosing the Right Metal for Stamping Projects in 2024
Selecting the right metal for your stamping project is crucial for achieving optimal results in manufacturing. This comprehensive guide will help you understand different metal options, their properties, and how to make informed decisions for your specific application. Whether you’re in automotive, aerospace, or general manufacturing, this article will serve as your roadmap to successful metal stamping projects.
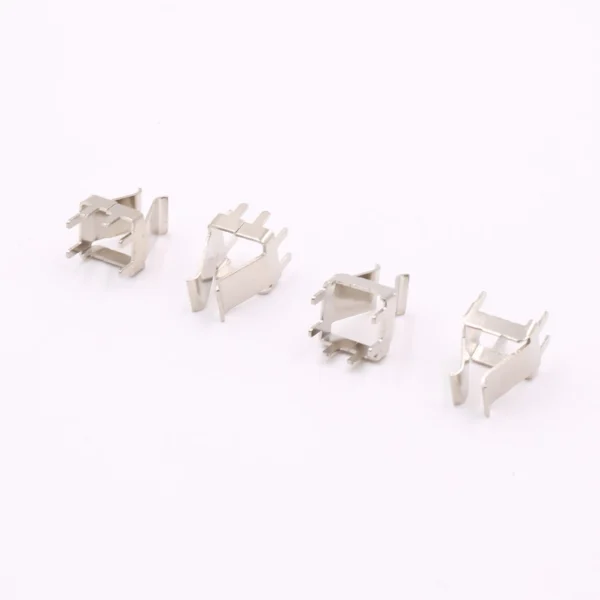
What Are the Most Common Materials Used in Metal Stamping?
The metal stamping process relies heavily on material selection. Common materials include:
- Carbon Steel
- Stainless Steel
- Aluminum
- Copper and its alloys
- Brass
- Bronze
Each material offers unique properties that make it suitable for specific applications. For instance, precision metal stamping often requires materials with excellent formability and surface finish capabilities.
How Do Material Properties Affect the Stamping Process?
Understanding material properties is essential for successful stamping:
Property | Impact on Stamping |
---|---|
Hardness | Tool wear and force required |
Ductility | Formability and design options |
Thickness | Die design and process parameters |
Surface Finish | Final product appearance |
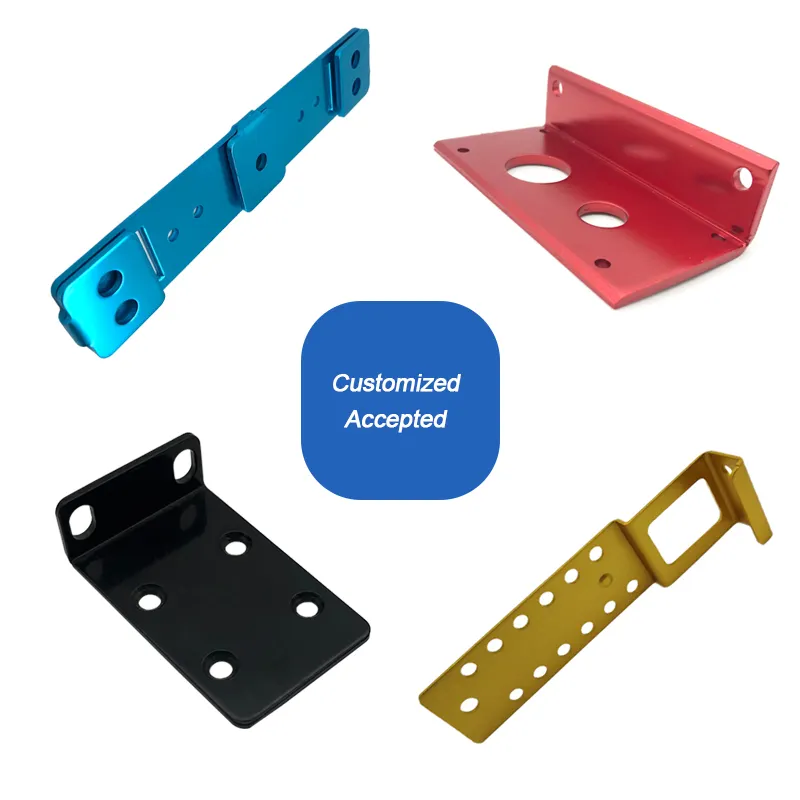
What Role Does Corrosion Resistance Play?
Corrosion resistance is crucial for many metal stamping applications. Different metals offer varying levels of protection:
- Stainless Steel: Excellent inherent resistance
- Aluminum: Forms protective oxide layer
- Copper Alloys: Good resistance with proper coating
- Zinc-coated Steel: Enhanced protection through galvanization
How to Choose Between Different Steel Alloys?
Steel alloys are among the most versatile materials for metal stamping:
- Low Carbon Steel: Excellent formability
- Medium Carbon Steel: Better strength
- High Carbon Steel: Maximum hardness
- Tool Steel: Superior wear resistance
What Are the Benefits of Using Aluminum in Stamping?
Aluminum offers several advantages for custom metal components:
- Lightweight construction
- Good corrosion resistance
- Excellent thermal conductivity
- Cost-effective processing
- High strength-to-weight ratio
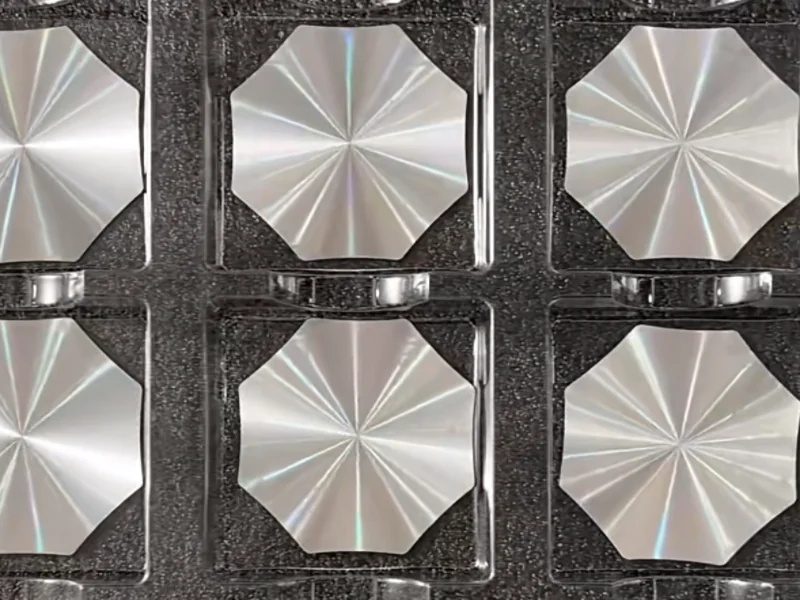
How Does Material Cost Impact Selection?
Material cost considerations include:
- Raw material prices
- Processing requirements
- Tooling costs
- Production volume
- Scrap rates
What Role Does Surface Finish Play?
Surface finish requirements affect material selection:
- Aesthetic requirements
- Functional needs
- Post-processing options
- Coating compatibility
How Do Industry Standards Influence Material Selection?
Different industries have specific requirements:
- Automotive: Strength and durability
- Aerospace: Weight and precision
- Electronics: Conductivity and finish
- Medical: Cleanliness and biocompatibility
What Are the Latest Trends in Metal Stamping Materials?
Current trends include:
- Advanced high-strength steels
- Lightweight alloys
- Sustainable materials
- Smart coatings
- Hybrid materials
How to Optimize Material Selection for Cost and Performance?
Consider these factors:
- Application requirements
- Production volume
- Budget constraints
- Quality standards
- Environmental conditions
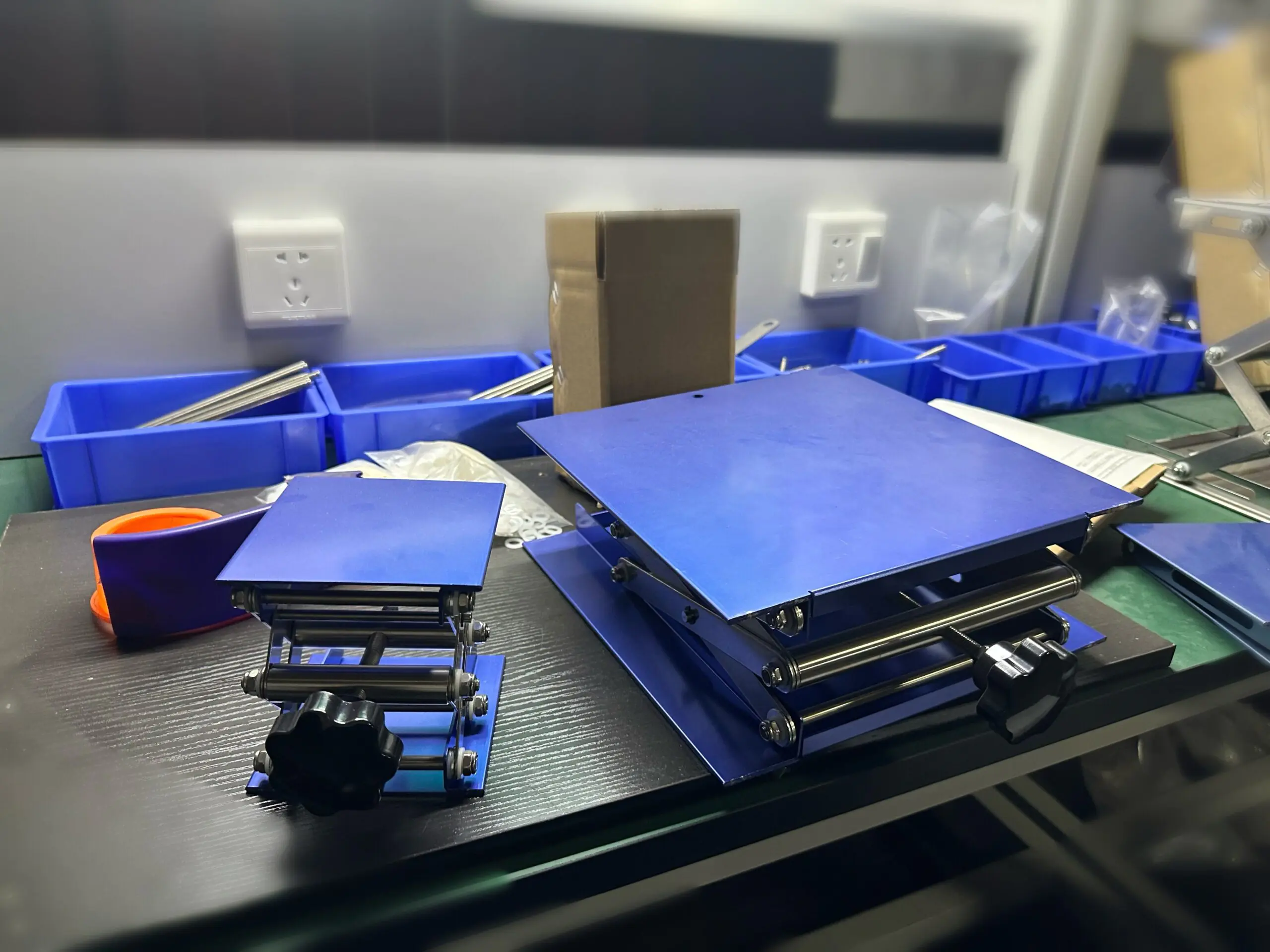
Key Takeaways:
- Material properties significantly impact stamping success
- Corrosion resistance is crucial for longevity
- Cost considerations must balance with performance
- Industry standards guide material selection
- Surface finish affects final product quality
- Material trends continue to evolve
Internal Links: