-
No.66 Gaojia, Xingfu Village, Sanqi Town, Yuyao, Ningbo,China
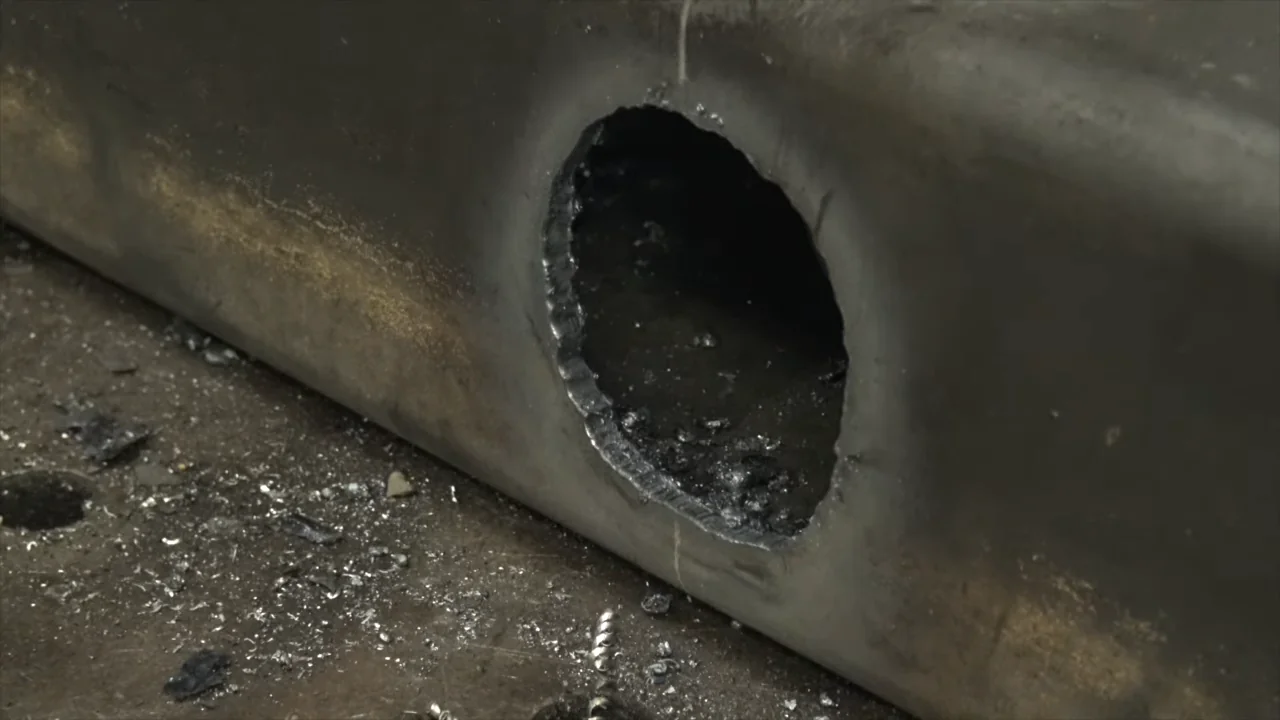
Common Metal Stamping Defects: A Comprehensive Guide to Quality Control
Metal stamping is a complex manufacturing process that requires precision and attention to detail. Understanding common defects and their causes is crucial for maintaining quality control and reducing scrap rates. This comprehensive guide will help you identify, prevent, and troubleshoot common metal stamping defects to ensure consistent product quality.
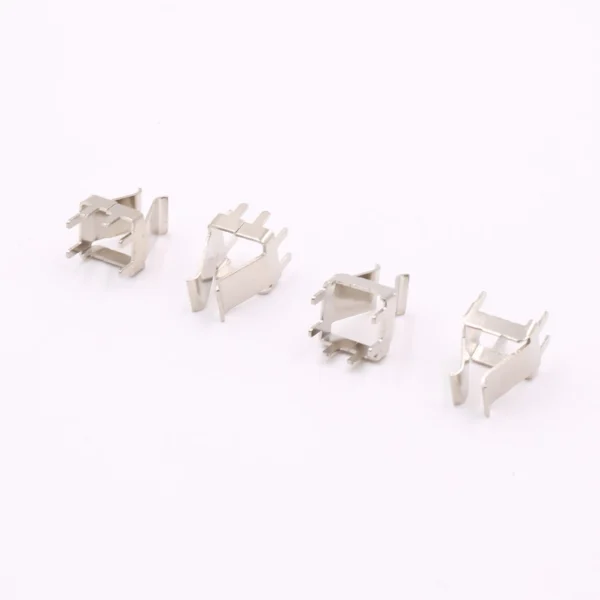
Precision metal stamping terminal showcasing optimal quality control standards
What Are the Most Common Metal Stamping Defects?
Metal stamping defects can occur due to various factors including improper tool setup, material properties, or process parameters. The most frequent defects include:
- Burrs: Rough edges or excess metal
- Wrinkles: Surface deformation
- Splitting: Material separation
- Springback: Material returning to original shape
- Die roll: Edge deformation
“Up to 60% of metal stamping defects can be prevented through proper tooling design and maintenance.” – Manufacturing Quality Quarterly
How Does Material Selection Impact Defect Formation?
The choice of metal materials significantly influences the likelihood of defects:Material Properties Table:
Material Type | Common Defects | Prevention Methods |
---|---|---|
Stainless Steel | Galling, Burrs | Proper lubrication |
Aluminum | Wrinkles, Springback | Optimized blank holder force |
Carbon Steel | Splitting, Die roll | Correct die clearance |
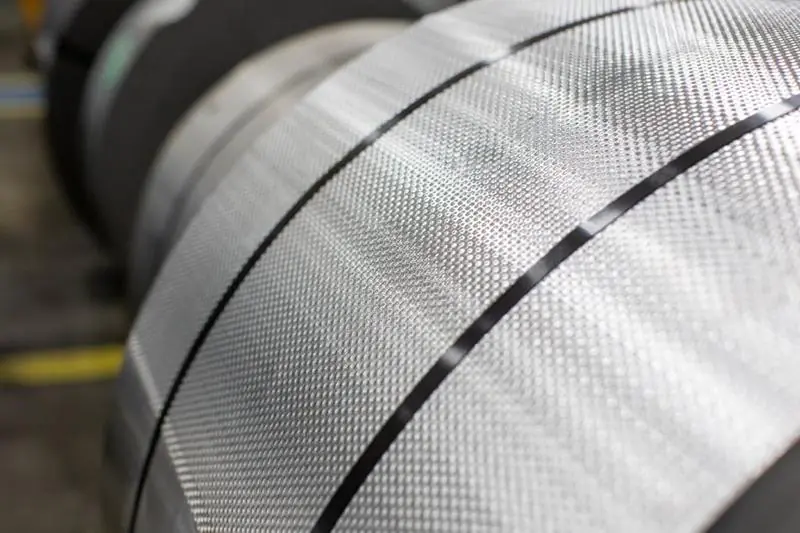
What Role Does Lubrication Play in Preventing Defects?
Proper lubrication is essential for quality metal stamping processes. Two critical aspects include:
- Lubricant Selection
- Viscosity requirements
- Material compatibility
- Application method
- Maintenance Schedule
- Regular monitoring
- Consistent application
- Contamination prevention
How Can Tool Wear Affect Part Quality?
Tool wear significantly impacts stamped part quality. Key considerations include:
- Regular tool inspection schedules
- Wear pattern monitoring
- Preventive maintenance programs
- Die geometry optimization
What Quality Control Measures Prevent Common Defects?
Implementing robust quality control involves several key strategies:
- Statistical Process Control (SPC)
- Dimensional monitoring
- Surface finish inspection
- Defect tracking
- Preventive Maintenance
- Tool condition monitoring
- Die alignment checks
- Regular calibration
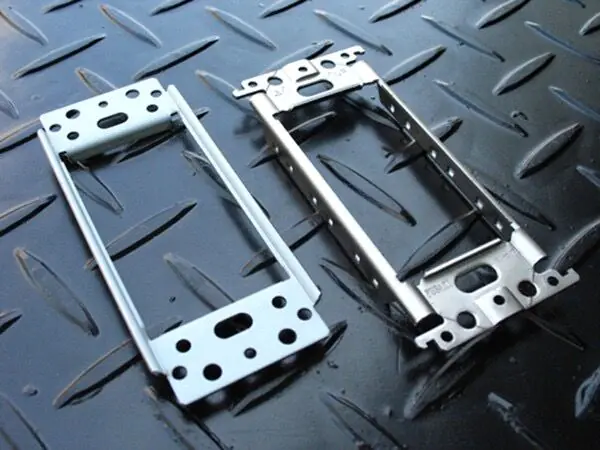
How Do Process Parameters Influence Defect Formation?
Critical process parameters that affect part quality include:
- Stamping press speed
- Blank holder force
- Die clearance
- Material feed rate
Optimal Parameter Ranges:
- Press Speed: 20-60 strokes per minute
- Die Clearance: 5-10% of material thickness
- Blank Holder Force: 30-40% of drawing force
What Are the Best Practices for High-Speed Stamping?
For precision metal components, consider:
- Equipment Optimization
- Press alignment
- Feed system setup
- Die protection systems
- Material Handling
- Proper coil feeding
- Material straightening
- Scrap removal
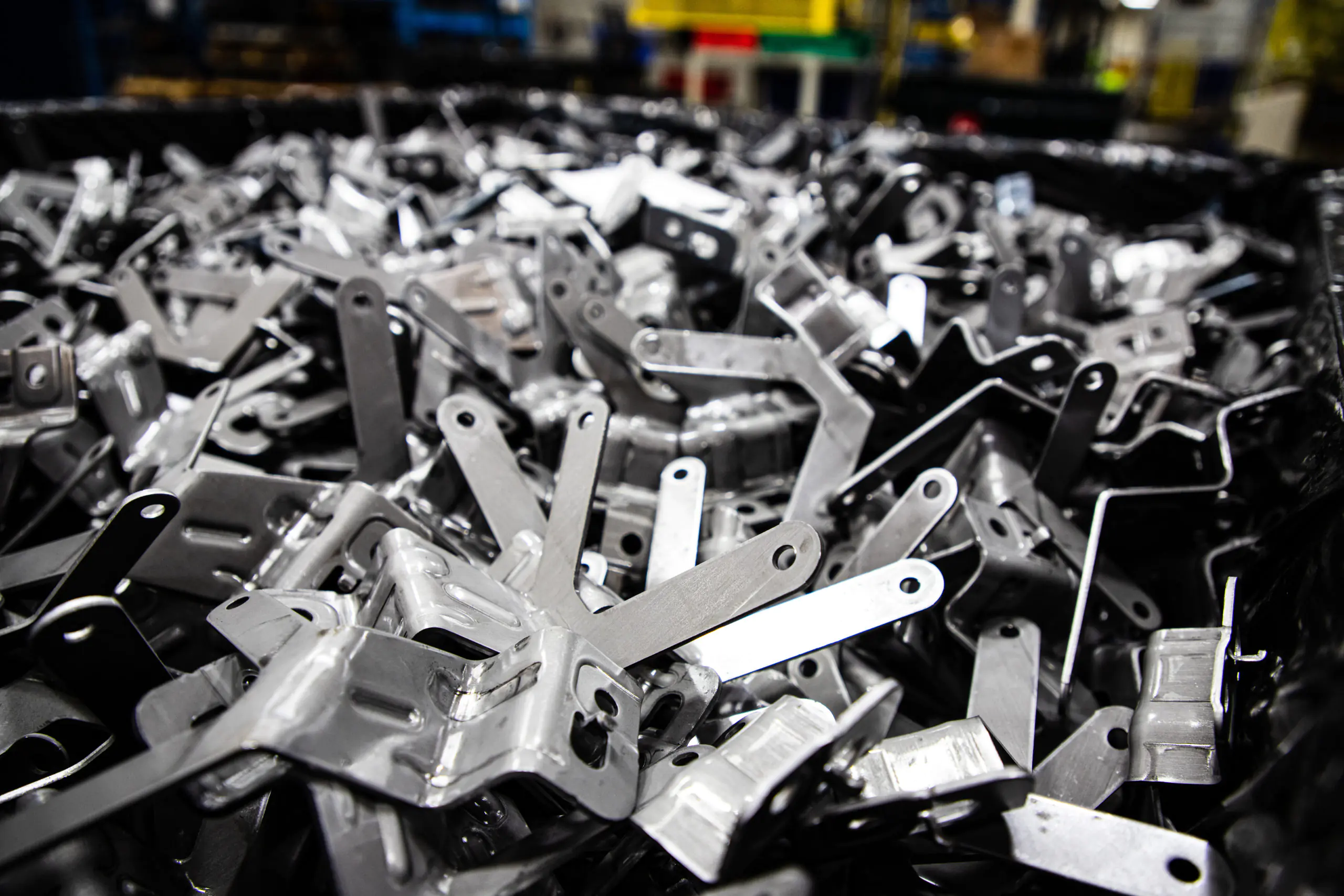
How to Troubleshoot Improperly Formed Holes?
Common issues with hole formation include:
- Oversized or undersized holes
- Burr formation
- Edge deformation
- Improper placement
What Causes Galling and Scratching?
Surface defects like galling often result from:
- Insufficient lubrication
- Improper die clearance
- Material incompatibility
- Excessive tool wear
How to Prevent Die Roll and Edge Deformation?
Effective strategies include:
- Optimizing die radius
- Maintaining proper clearances
- Regular tool maintenance
- Material grain direction consideration
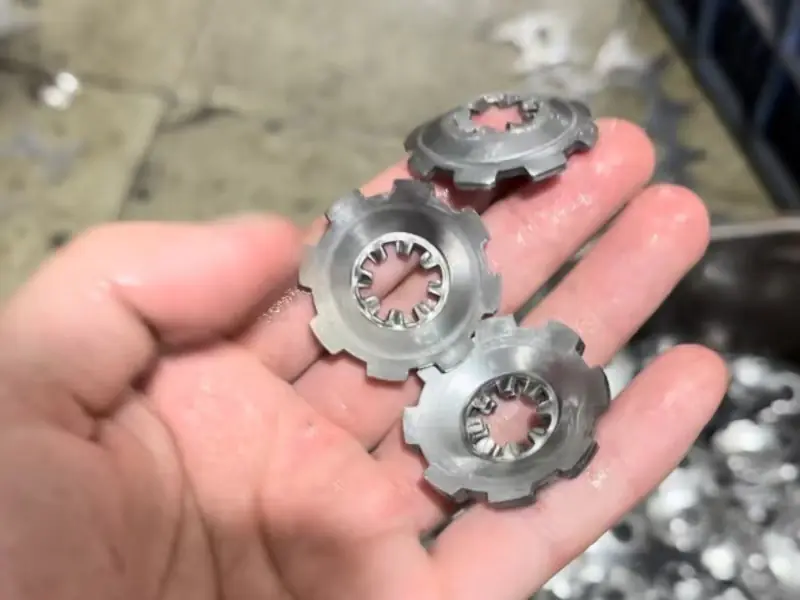
Key Takeaways:
- Implement comprehensive quality control measures
- Maintain proper lubrication practices
- Monitor tool wear regularly
- Optimize process parameters
- Consider material properties
- Perform regular maintenance
- Document and track defects
- Train operators properly
Internal Links: