-
No.66 Gaojia, Xingfu Village, Sanqi Town, Yuyao, Ningbo,China
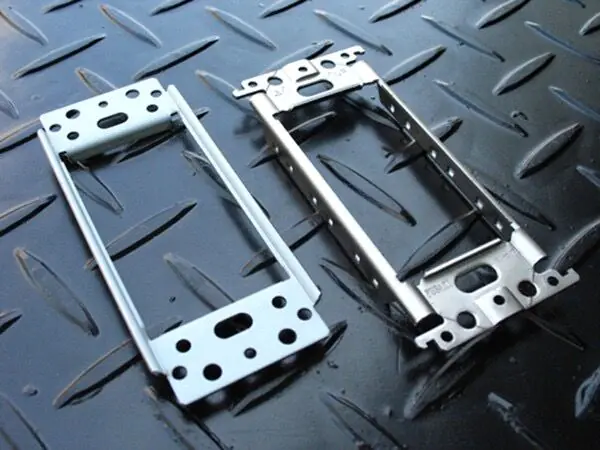
Common Metal Stamping Defects: Identification, Prevention, and Solutions
Metal stamping defects can significantly impact product quality and manufacturing efficiency. This comprehensive guide explores common sheet metal stamping defects, their causes, and practical solutions to prevent them. Whether you’re a quality control specialist, process engineer, or manufacturing manager, understanding these defects is crucial for maintaining high-quality production standards.
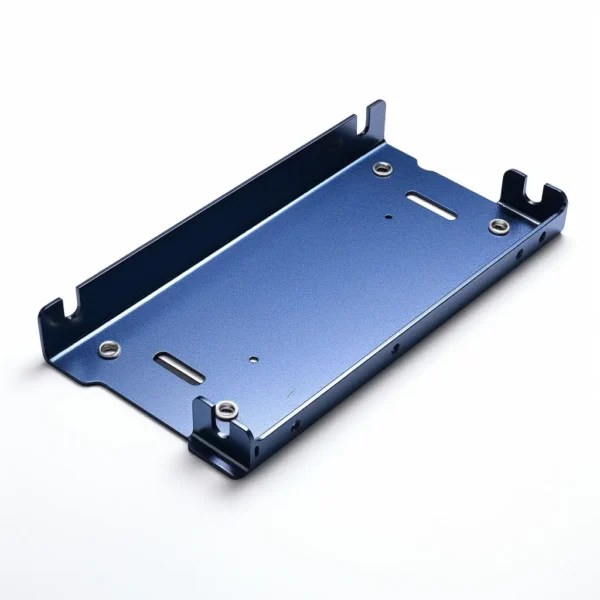
Common metal stamping defects and quality control inspection
What Are the Most Common Metal Stamping Defects?
Metal stamping defects can occur in various forms, with some being more prevalent than others. The most common defects include:
- Wrinkling: Unwanted folds in the material
- Burrs: Sharp edges or excess material
- Scratches: Surface damage during handling
- Tearing: Material separation due to excessive force
- Dimensional inaccuracies: Parts out of specification
Understanding Material Selection and Its Impact on Defects
Proper material selection plays a crucial role in preventing defects. Consider these factors:
- Material Properties
- Tensile strength
- Material thickness
- Work hardening characteristics
- Application Requirements
- Load-bearing capacity
- Environmental conditions
- Surface finish requirements
How Do Tool Design Issues Cause Stamping Defects?
Improper tool design is a leading cause of metal stamping defects. Key considerations include:
- Die clearance optimization
- Proper tool design and maintenance
- Punch and die alignment
- Surface finish of tooling
Learn more about proper tool design
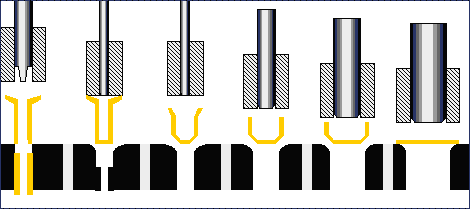
Process Parameters and Their Role in Defect Prevention
The right process parameters are essential for quality control:
Parameter | Impact | Optimal Range |
---|---|---|
Speed | Material flow | Application-specific |
Pressure | Part formation | Material-dependent |
Lubrication | Friction reduction | Process-specific |
Common Sheet Metal Forming Defects and Solutions
Wrinkling
Wrinkles typically occur due to improper blank holding force or material flow. Solutions include:
- Adjusting blank holder pressure
- Optimizing lubrication
- Modifying die design
Burrs
Burrs form when there’s excessive clearance between punch and die. Prevention methods:
- Regular tool maintenance
- Proper die clearance
- Sharp cutting edges
Explore metal stamping services
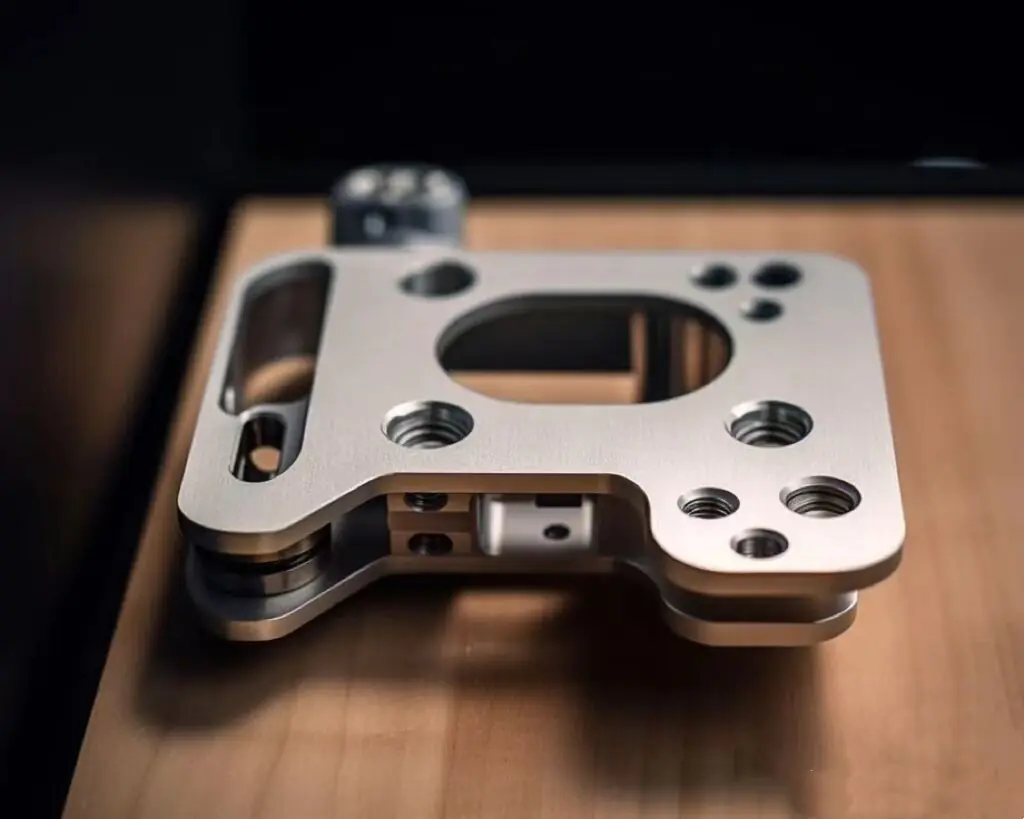
Quality Control Measures for Defect Detection
Implement these quality control measures:
- Visual Inspection
- Surface quality
- Dimensional accuracy
- Finish requirements
- Measurement Tools
- Micrometers
- Calipers
- CMM machines
Advanced Techniques for Defect Prevention
Modern approaches to prevent sheet metal defects include:
- Forming simulation software
- Statistical process control
- Preventive maintenance schedules
- Regular tool inspection
View sheet metal fabrication processes
The Role of Maintenance in Defect Prevention
Regular maintenance helps prevent common problems:
- Tool wear monitoring
- Die alignment checks
- Lubrication system maintenance
- Machine calibration
Economic Impact of Metal Stamping Defects
Understanding the cost implications:
- Scrap material costs
- Production downtime
- Quality control expenses
- Customer satisfaction impact
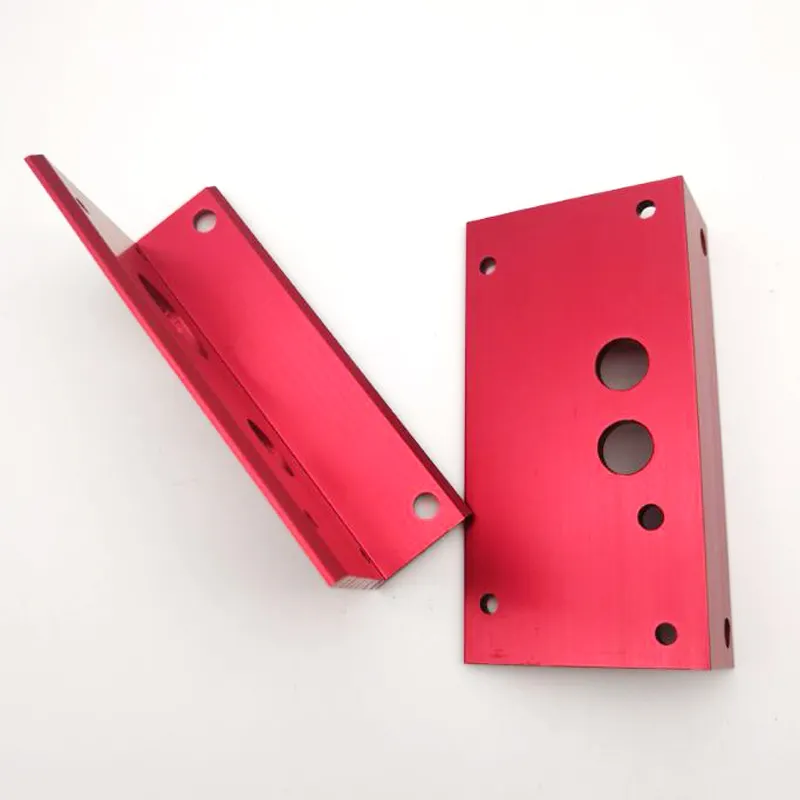
Key Takeaways
- Proper material selection is crucial for defect prevention
- Regular tool maintenance reduces defect occurrence
- Process parameters must be optimized for each application
- Quality control measures should be implemented at all stages
- Advanced prevention techniques can significantly reduce defects
- Regular maintenance is essential for consistent quality
- Understanding economic impact helps justify prevention measures