-
No.66 Gaojia, Xingfu Village, Sanqi Town, Yuyao, Ningbo,China
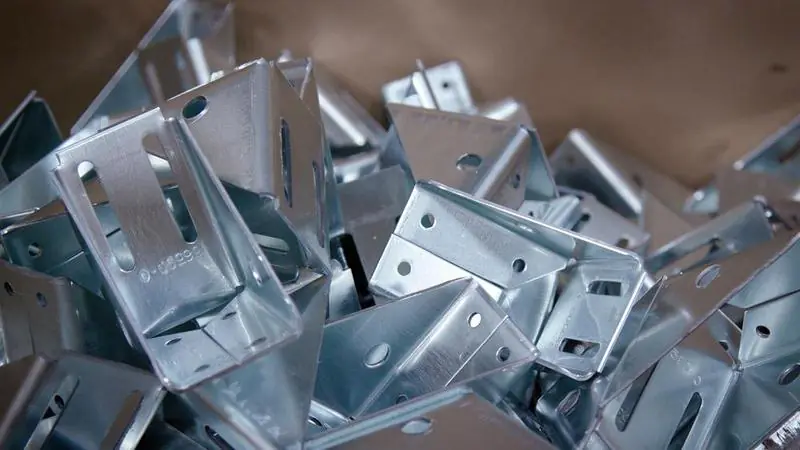
Deep Draw Stamping vs Traditional Metal Stamping: Understanding the Key Differences
Deep draw stamping and metal stamping are two fundamental metal forming processes that shape the manufacturing industry. This comprehensive guide explores their unique characteristics, applications, and key differences to help you make informed decisions for your manufacturing needs. Whether you’re an engineer, manufacturer, or procurement specialist, understanding these processes is crucial for optimizing your production methods.
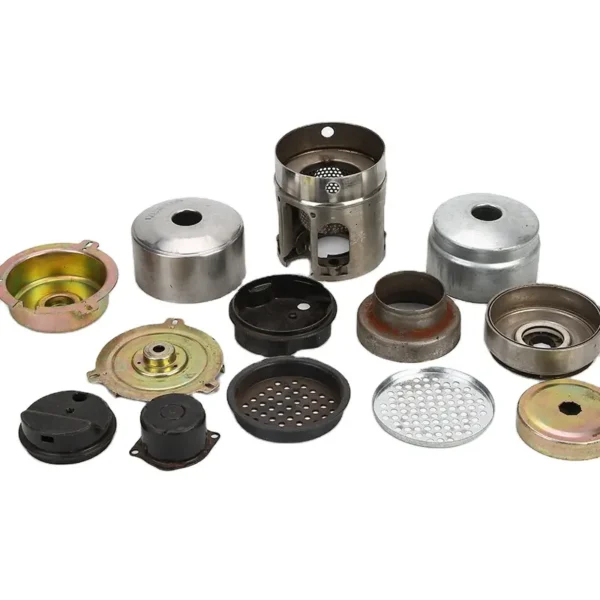
Deep draw stamping components showing precision forming capabilities
What is Deep Draw Stamping?
Deep draw stamping is a specialized metal forming process that produces cylindrical, box-shaped, or complex-geometry parts from flat sheet metal. This manufacturing process transforms flat sheet metal into three-dimensional shapes by stretching the metal into a forming die cavity. The process creates parts with depth that exceeds their diameter, making it ideal for producing components like:
- Cylindrical containers
- Electronic enclosures
- Automotive components
- Aerospace parts
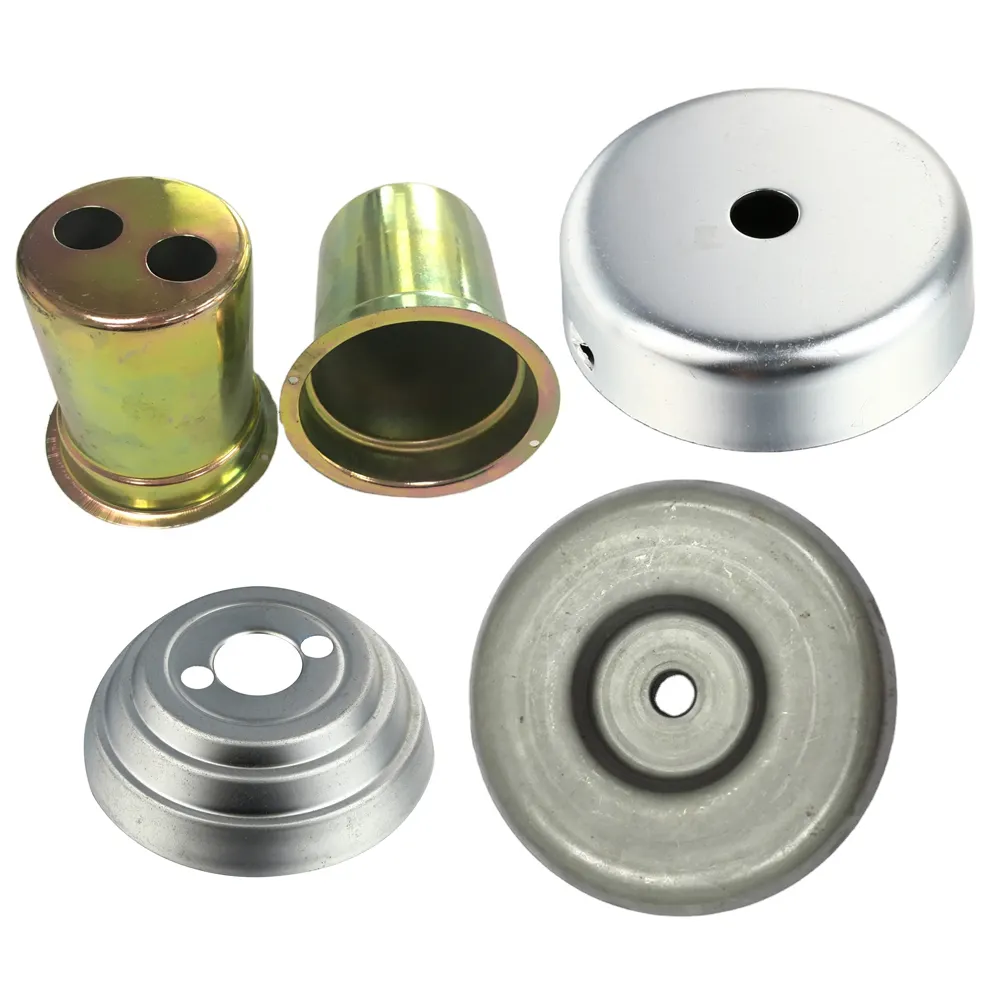
How Does Deep Drawing Differ from Traditional Metal Stamping?
The main differences between deep drawing and traditional metal stamping lie in their fundamental approaches:
Feature | Deep Drawing | Metal Stamping |
---|---|---|
Process Depth | Creates deep vessels | Typically shallow forms |
Material Flow | Controlled stretching | Cutting and forming |
Tooling | Complex die sets | Simpler tooling |
Applications | Complex 3D shapes | Flat or shallow parts |
View our deep drawn lighting components
What Are the Key Advantages of Deep Draw Processing?
Deep draw process offers several unique benefits:
- Material Efficiency
- Minimal material waste
- Uniform wall thickness
- Better material utilization
- Product Quality
- Superior surface finish
- Consistent part geometry
- Enhanced structural integrity
When Should You Choose Deep Drawing Over Metal Stamping?
Consider deep drawing when your project requires:
- Complex three-dimensional shapes
- Seamless construction
- High strength-to-weight ratio
- Precise tolerances
- Uniform wall thickness
Explore our metal stamping capabilities
What Materials Are Suitable for Deep Drawing?
Deep drawing requires materials with specific characteristics:
- Common Materials Used:
- Aluminum
- Stainless steel
- Brass
- Copper
- Low-carbon steel
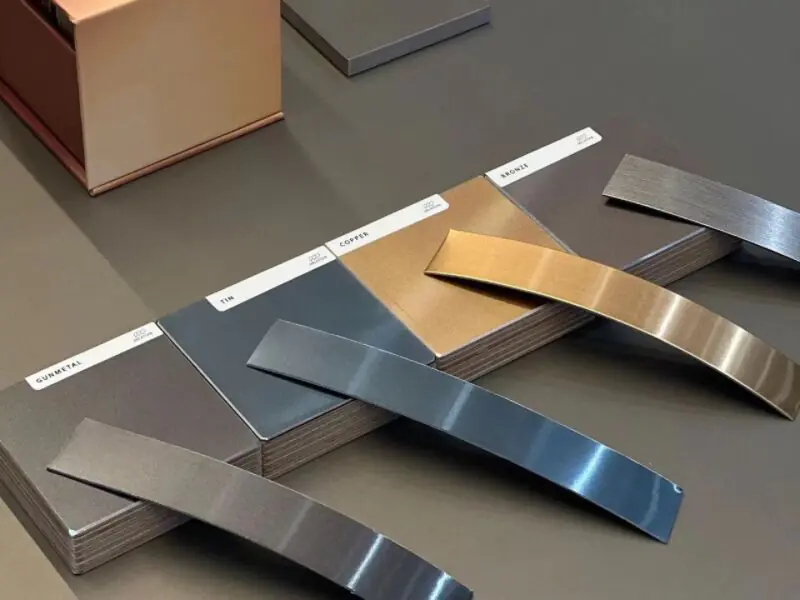
How Does the Manufacturing Process Compare?
The manufacturing process for deep drawing differs significantly from traditional stamping:
- Deep Drawing Steps:
- Material preparation
- Blank holding
- Drawing operation
- Final forming
- Traditional Stamping Steps:
- Material feeding
- Blanking
- Forming/bending
- Finishing
Check out our custom stamping solutions
What Industries Benefit Most from Deep Draw Technology?
Deep drawing serves various industries:
- Automotive (fuel tanks, oil pans)
- Aerospace (housings, components)
- Electronics (enclosures, shields)
- Consumer goods (cookware, containers)
- Medical (surgical instruments)
How to Choose Between Deep Drawing and Metal Stamping?
Consider these factors when selecting your process:
- Part Design Requirements
- Depth-to-diameter ratio
- Wall thickness needs
- Surface finish requirements
- Production Factors
- Volume requirements
- Cost considerations
- Timeline constraints
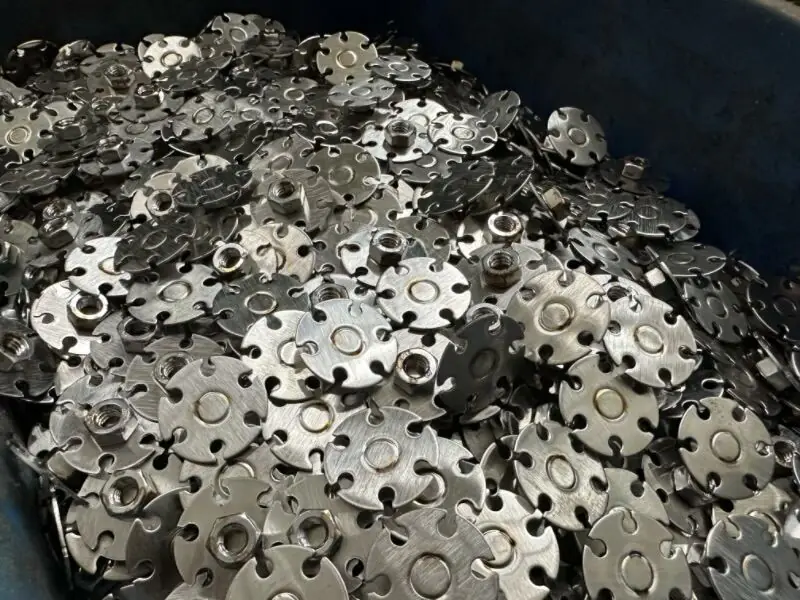
Key Points to Remember:
- Deep drawing creates deeper vessels than traditional stamping
- Material selection is crucial for successful deep drawing
- Consider part geometry when choosing between processes
- Production volume affects process selection
- Cost implications vary between methods
- Quality requirements influence choice
This comprehensive guide has covered the essential aspects of deep draw stamping and its comparison with traditional metal stamping. Understanding these differences will help you make informed decisions for your manufacturing needs.