-
No.66 Gaojia, Xingfu Village, Sanqi Town, Yuyao, Ningbo,China
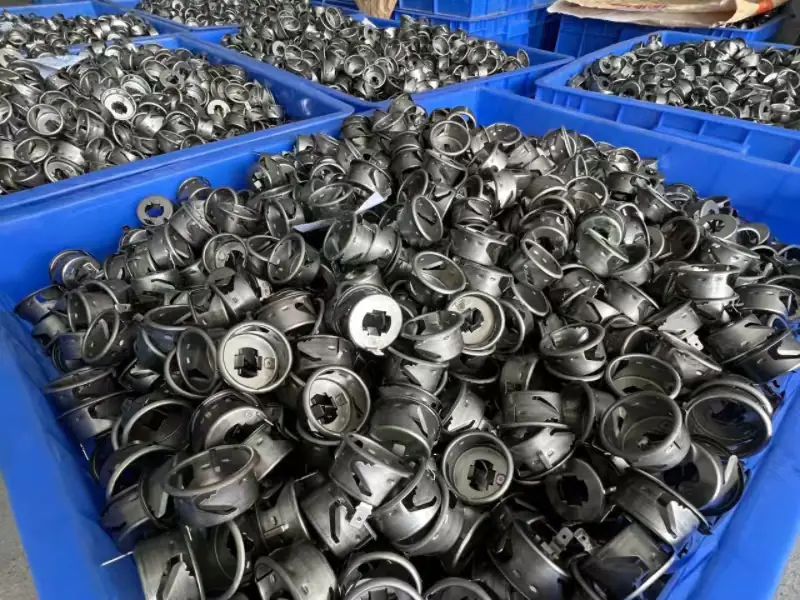
3 Critical Solutions to Eliminate High-Volume Metal Stamping Defects
In today’s fast-paced manufacturing landscape, understanding and preventing metal stamping defects is crucial for maintaining quality and efficiency in high-volume production. This comprehensive guide explores the most common challenges in metal stamping processes and provides practical solutions to help manufacturers achieve consistent, high-quality results.
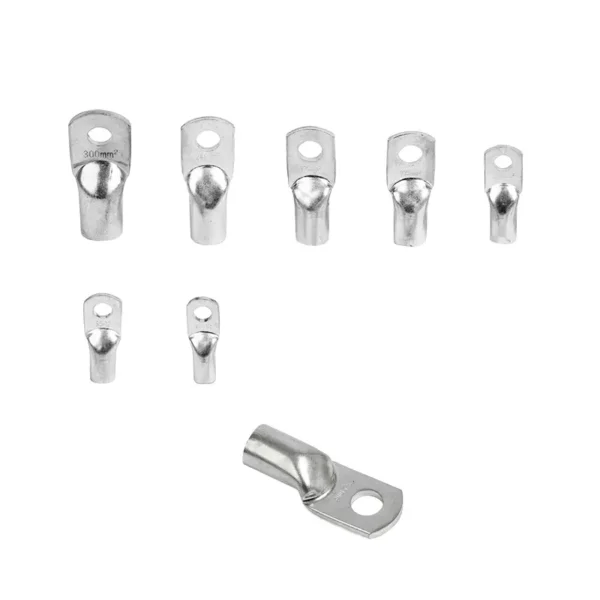
Precision metal stamping components require careful quality control
What Are the Most Common Metal Stamping Defects?
Metal stamping defects can significantly impact production quality and efficiency. The most common issues include:
- Material deformation
- Dimensional inaccuracies
- Surface finish problems
- Tool wear and breakage
These challenges become particularly evident in high-volume production of complex parts, where consistent output is crucial.
How Does Tool Wear Affect Stamping Quality?
The relationship between tool wear and stamping quality is direct and significant. Stamping dies experience wear and tear under extreme conditions, leading to:
- Reduced dimensional accuracy
- Inconsistent surface finish
- Increased downtime
- Higher production costs
Regular maintenance and monitoring of stamping tools are essential for maintaining quality standards.
The Role of Material Selection in Defect Prevention
Choosing the right material plays a vital role in preventing defects. Consider these factors:
- Material ductility
- High tensile strength requirements
- Surface finish specifications
Sheet metal fabrication products require careful material selection to ensure optimal results.
Quality Control Measures in High-Volume Production
Implementing robust quality control processes is essential for:
- Real-time monitoring
- Statistical process control
- Dimensional verification
- Surface quality inspection
Advanced Technologies in Defect Prevention
Modern metal stamping benefits from technological advancements including:
Technology | Benefit |
---|---|
Computer-aided design | Improved accuracy |
Real-time monitoring | Instant feedback |
Automation systems | Consistent results |
Why is Process Control Critical?
Process control in metal stamping requires:
- Precise parameter monitoring
- Regular equipment calibration
- Standardized procedures
- Documentation and tracking
How to Address Common Challenges in Metal Forming?
Effective solutions include:
- Implementation of preventive maintenance schedules
- Regular tool inspection and replacement
- Operator training programs
- Quality assurance protocols
The Impact of Automation on Quality Assurance
Modern stamping techniques benefit from automation through:
- Reduced human error
- Consistent output
- Improved productivity
- Better quality control
Solutions for Optimizing Stamping Results
Three key solutions for eliminating defects:
- Advanced Process Monitoring
- Real-time data collection
- Predictive maintenance
- Quality tracking systems
- Material and Tool Management
- Regular tool maintenance
- Optimal material selection
- Proper storage conditions
- Training and Documentation
- Comprehensive operator training
- Standard operating procedures
- Quality control documentation
Future Trends in Metal Stamping Quality Control
The manufacturing industry continues to evolve with:
- AI-powered quality control
- Smart sensors and IoT integration
- Advanced materials development
- Improved automation systems
Key Takeaways:
- Implement robust quality control measures
- Maintain regular tool inspection and maintenance
- Choose appropriate materials for specific applications
- Utilize advanced monitoring technologies
- Invest in operator training and documentation
- Stay updated with technological advancements
The success of high-volume metal stamping operations depends on addressing these challenges proactively while maintaining focus on quality and efficiency. By implementing these solutions, manufacturers can significantly reduce the risk of defects and improve their production outcomes.