-
No.66 Gaojia, Xingfu Village, Sanqi Town, Yuyao, Ningbo,China
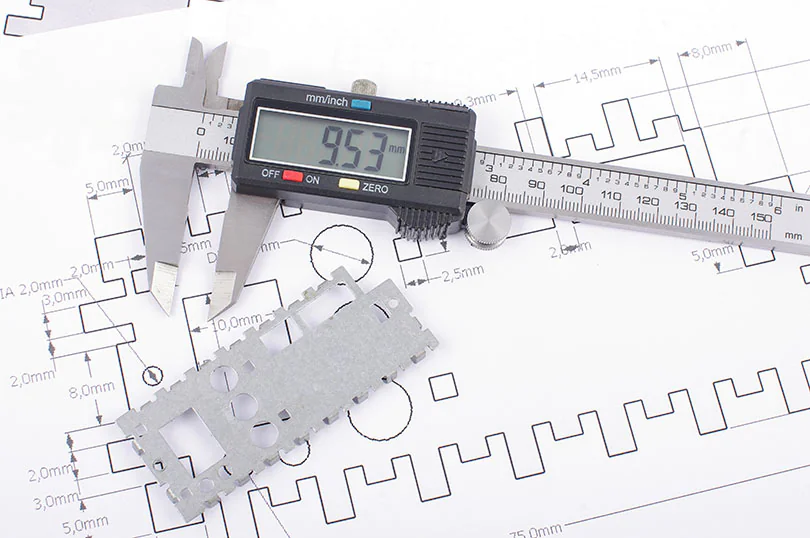
Essential Metal Stamping Design Guidelines: A Comprehensive Guide for Manufacturers
Metal stamping design is a critical process that can make or break your manufacturing project. This comprehensive guide will walk you through essential design guidelines, best practices, and expert insights to help you achieve optimal results in your metal stamping projects. Whether you’re an experienced engineer or new to the field, this article will provide valuable knowledge to enhance your design capabilities and avoid common pitfalls.
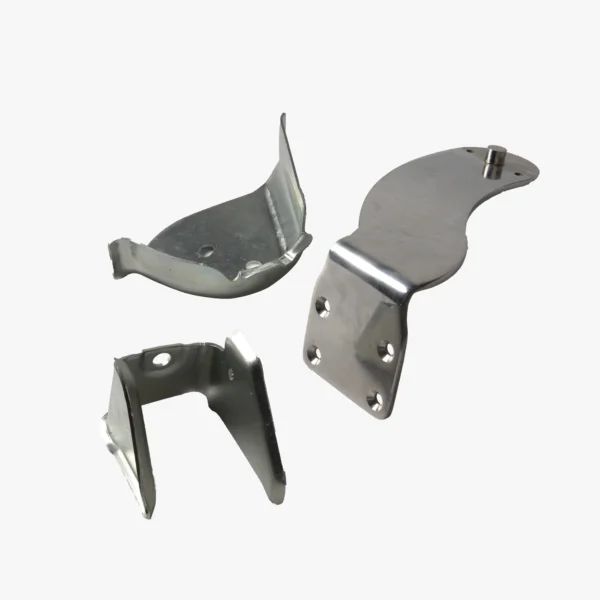
Precision-engineered stamped chassis brackets demonstrating optimal design principles
What Are the Fundamental Principles of Metal Stamping Design?
The foundation of successful metal stamping begins with understanding core principles. The stamping process involves transforming flat metal sheets into various shapes through mechanical force. Two critical factors influence design success:
- Material Selection: Choose appropriate metal material based on application requirements
- Design Parameters: Consider material thickness, bend radius, and tolerance specifications
“Thoughtful design in the early stages can reduce manufacturing costs by up to 70% and minimize production issues.” – Manufacturing Engineering Quarterly
How Does Material Thickness Affect Design Decisions?
Material thickness plays a crucial role in metal stamping design guidelines. The thickness of the material impacts several key aspects:
- Minimum bend radius requirements
- Tool and die specifications
- Overall part manufacturability
Best Practice Table for Material Thickness Considerations:
Material Thickness (mm) | Minimum Bend Radius | Recommended Hole Diameter |
---|---|---|
0.5 – 1.0 | 1x thickness | 2x thickness |
1.0 – 2.0 | 1.5x thickness | 2.5x thickness |
2.0 – 3.0 | 2x thickness | 3x thickness |
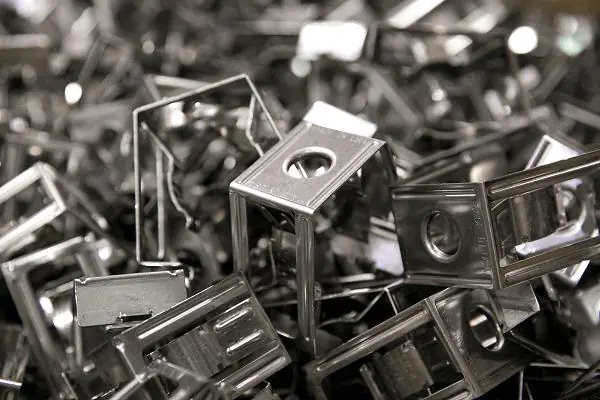
What Are the Critical Design Features for Holes and Slots?
When designing holes and slots for stamped parts, several key considerations ensure optimal manufacturability:
- Maintain a distance of at least twice the material thickness between holes
- Avoid placing slots too close to bends
- Consider grain direction when positioning holes
The punch and die relationship must be carefully planned to prevent burr formation and achieve tight tolerances.
Why Is Bend Radius Essential in Metal Stamping Design?
Proper bend radius design is crucial for successful metal forming. The bend radius affects:
- Material stress distribution
- Tool life and performance
- Final part quality
A general rule of thumb: maintain a minimum bend radius of 1.5 times the material thickness to prevent cracking and ensure consistent forming.
What Types of Metal Stamping Processes Should You Consider?
Modern metal stamping encompasses several specialized techniques:
- Progressive Die Stamping
- Ideal for high-volume production
- Multiple operations in sequence
- Cost-effective for large runs
- Transfer Die Stamping
- Suitable for complex parts
- Flexible tooling options
- Medium to high volumes
- Four-slide Stamping
- Perfect for intricate bends
- Multiple forming operations
- Excellent for small parts
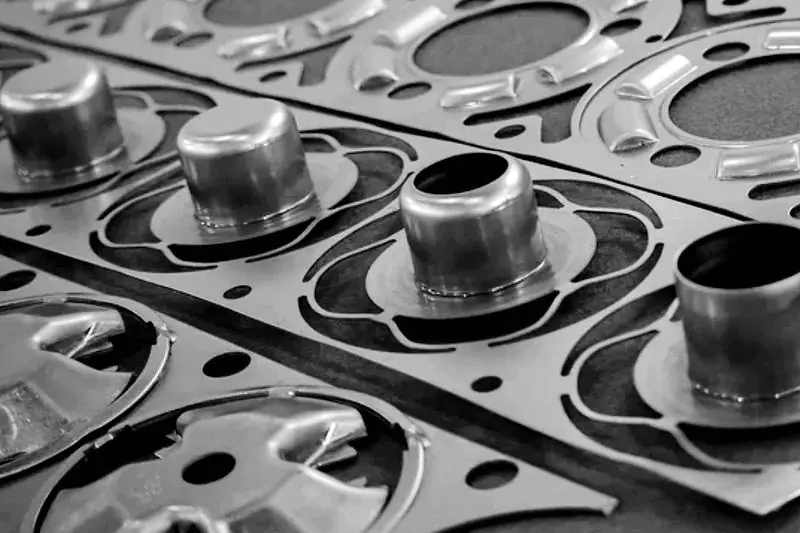
How Can Design Features Impact Manufacturing Costs?
Smart design choices can significantly affect component stamping cost savings:
- Optimize material usage through thoughtful blank design
- Minimize secondary operations
- Consider creative tool design solutions
Cost Reduction Strategies:
- Standardize corner radii
- Eliminate unnecessary features
- Design for optimal material utilization
What Are Common Design Mistakes to Avoid?
Understanding potential pitfalls helps prevent costly errors:
- Sharp Corners
- Increase stress concentration
- Reduce tool life
- Risk of cracking
- Improper Hole Placement
- Too close to edges
- Insufficient spacing
- Poor alignment with bends
- Inadequate Relief
- Causes material deformation
- Creates assembly issues
- Increases scrap rate
How Does Material Selection Impact Design Requirements?
Different materials require specific design considerations:
Material Type | Design Considerations | Typical Applications |
---|---|---|
Stainless Steel | Larger bend radii | Medical devices |
Aluminum | Lower forming forces | Electronics |
Carbon Steel | Standard tolerances | Automotive parts |
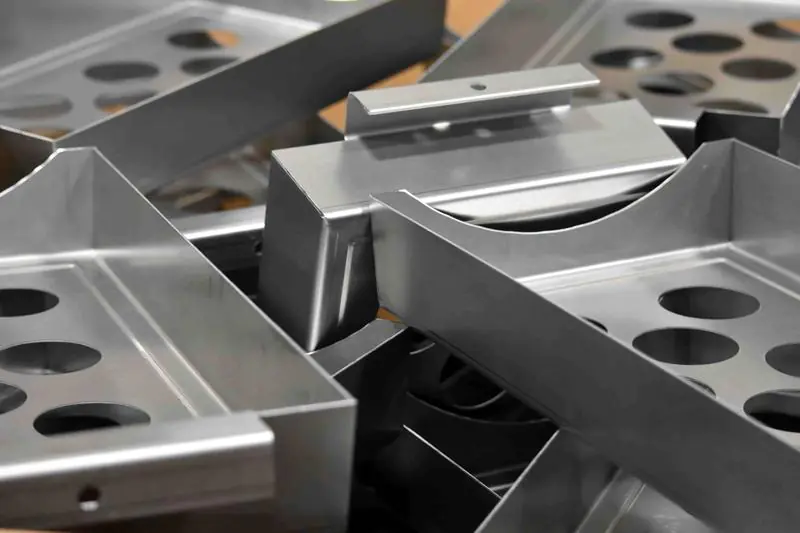
What Role Does Process Control Play in Design Success?
Maintaining precise process control in metal stamping ensures:
- Consistent part quality
- Reduced scrap rates
- Improved tool life
- Meeting tight tolerances
How to Optimize Design for High-Volume Production?
For efficient high-volume manufacturing:
- Standardize Features
- Use common hole sizes
- Maintain consistent bend radii
- Implement repeatable processes
- Consider Automation
- Design for progressive dies
- Plan for material handling
- Optimize part orientation
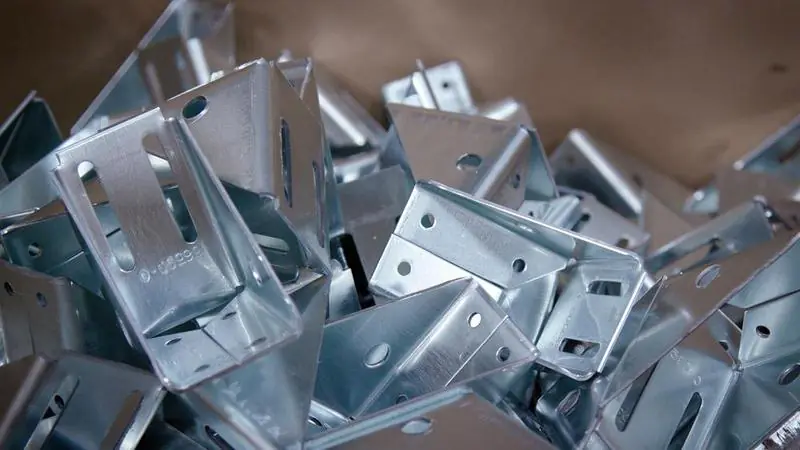
Key Takeaways:
- Always consider material thickness when determining design parameters
- Maintain minimum bend radius requirements
- Keep adequate spacing between features
- Consider grain direction in design
- Choose appropriate stamping processes
- Optimize for cost-effective production
- Implement proper process controls
- Design for manufacturability
Internal Links: