-
No.66 Gaojia, Xingfu Village, Sanqi Town, Yuyao, Ningbo,China
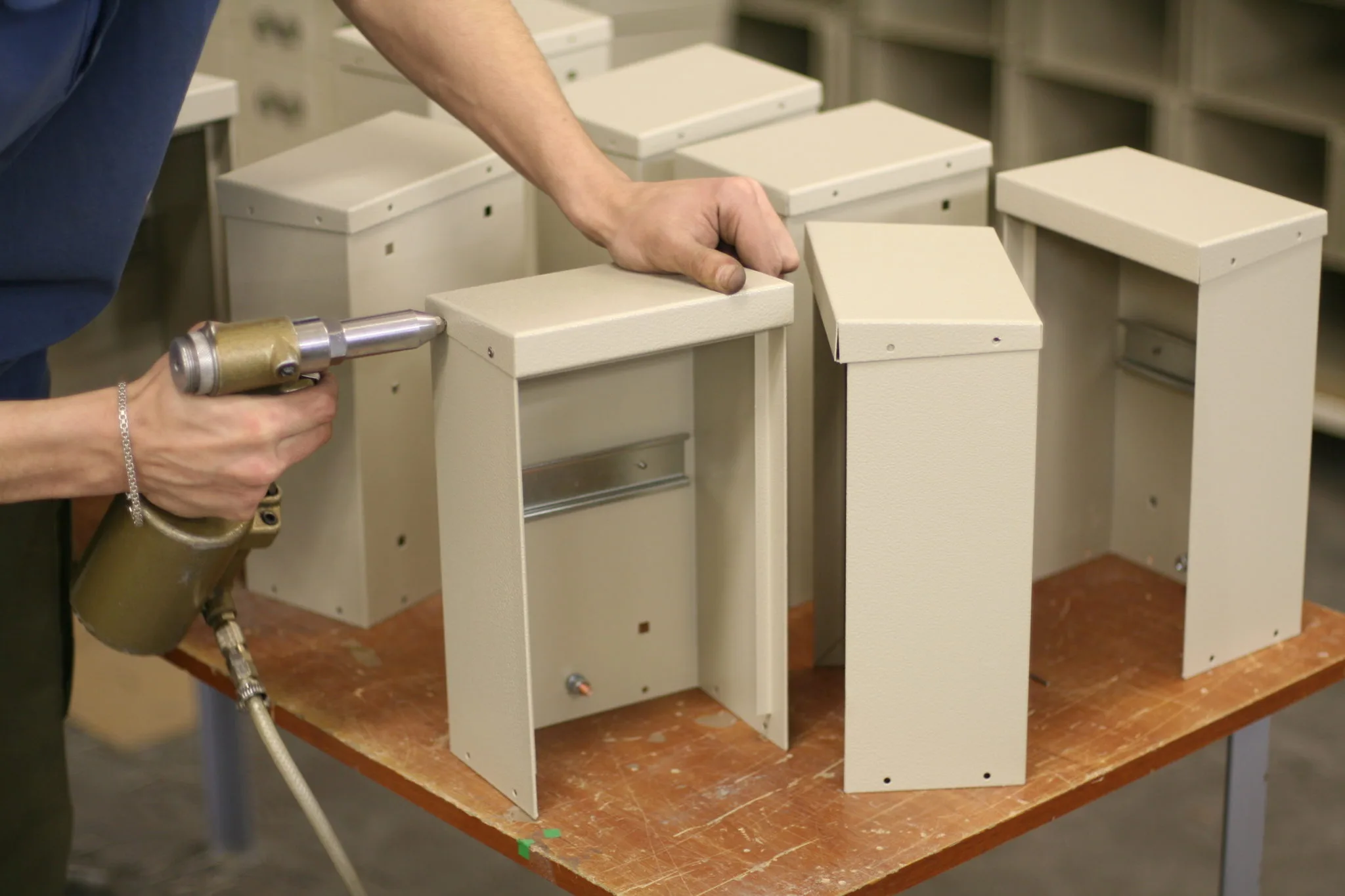
Essential Sheet Metal Design Guidelines for Perfect Enclosure Manufacturing in 2024
Creating effective sheet metal enclosures requires a deep understanding of design principles, material properties, and manufacturing processes. This comprehensive guide will walk you through everything you need to know about designing sheet metal enclosures that are both functional and cost-effective to manufacture.
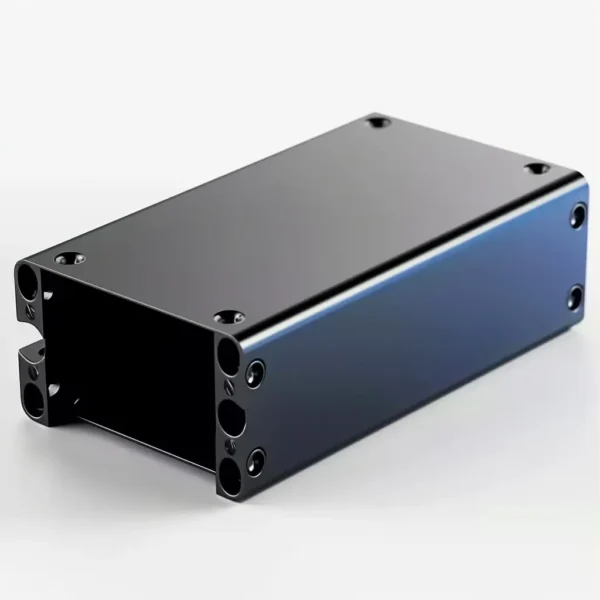
Professional steel sheet metal enclosure showcasing precision manufacturing capabilities
Understanding Sheet Metal Design Basics
Sheet metal design combines engineering principles with practical manufacturing considerations. The process begins with:
- Material selection
- Thickness determination
- Bend radius calculations
- Surface finish requirements
When designing sheet metal parts, it’s crucial to consider both the functional requirements and manufacturing limitations. Sheet metal enclosures must balance structural integrity with producibility.
What Are the Key Material Considerations for Sheet Metal Enclosures?
The choice of material significantly impacts your enclosure’s performance:
Material | Advantages | Common Applications |
---|---|---|
Stainless Steel | Corrosion resistant, durable | Outdoor enclosures |
Aluminum | Lightweight, good thermal conductivity | Electronic housings |
Cold-rolled Steel | Cost-effective, easy to form | Indoor applications |
Essential Design Requirements for Sheet Metal Fabrication
Minimum Bend Radius
- Should be at least 1-1.5 times the material thickness
- Affects material stress and tooling requirements
- Impacts overall design feasibility
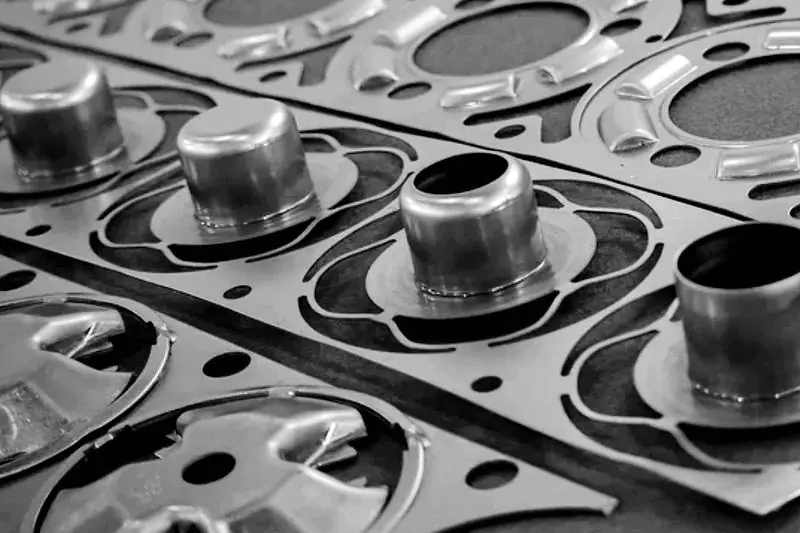
Wall Thickness Considerations
The thickness of sheet metal affects:
- Structural integrity
- Heat dissipation
- Cost of manufacturing
- Weight of final product
How to Optimize Sheet Metal Enclosure Design?
Consider these design elements:
- Structural Integrity
- Proper reinforcement placement
- Adequate material thickness
- Strategic bend locations
- Manufacturing Efficiency
- Minimize complex bends
- Optimize material usage
- Reduce assembly steps
Advanced Sheet Metal Design Guidelines
Key considerations include:
- Bend Relief Requirements
- Minimum distance from edges
- Proper spacing between features
- Corner treatment specifications
- Hole Placement Rules
- Distance from bends
- Minimum hole diameter
- Edge distance requirements
What Are Common Sheet Metal Design Mistakes to Avoid?
- Insufficient bend radius
- Poor hole placement
- Inadequate tolerances
- Improper material selection
Manufacturing Considerations for Sheet Metal Enclosures
Important factors include:
- Tooling Requirements
- Production Volume
- Surface Finish Options
- Assembly Methods
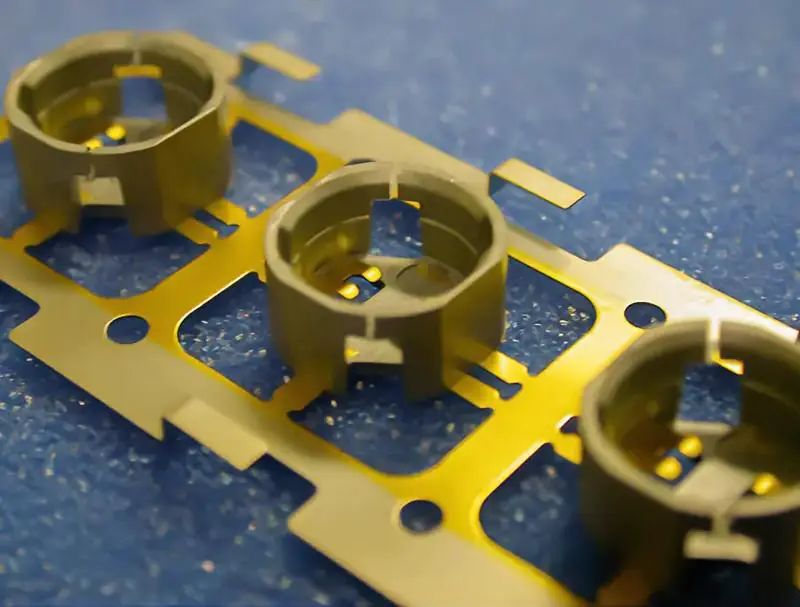
Design for Manufacturability (DFM) in Sheet Metal
DFM principles ensure:
- Cost-effective production
- Consistent quality
- Efficient assembly
- Reduced waste
Future Trends in Sheet Metal Enclosure Design
Emerging technologies include:
- Advanced CAD/CAM integration
- Automated design validation
- Smart manufacturing processes
- Sustainable materials
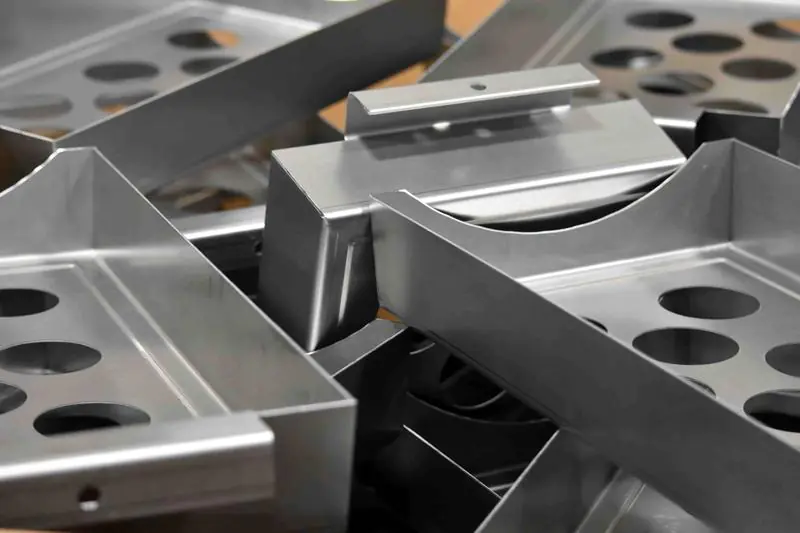
Key Takeaways:
• Always consider material properties and limitations • Follow proper bend radius guidelines • Maintain appropriate hole placement • Consider manufacturing processes early in design • Implement DFM principles • Plan for assembly requirements
Internal Links Used: