-
No.66 Gaojia, Xingfu Village, Sanqi Town, Yuyao, Ningbo,China
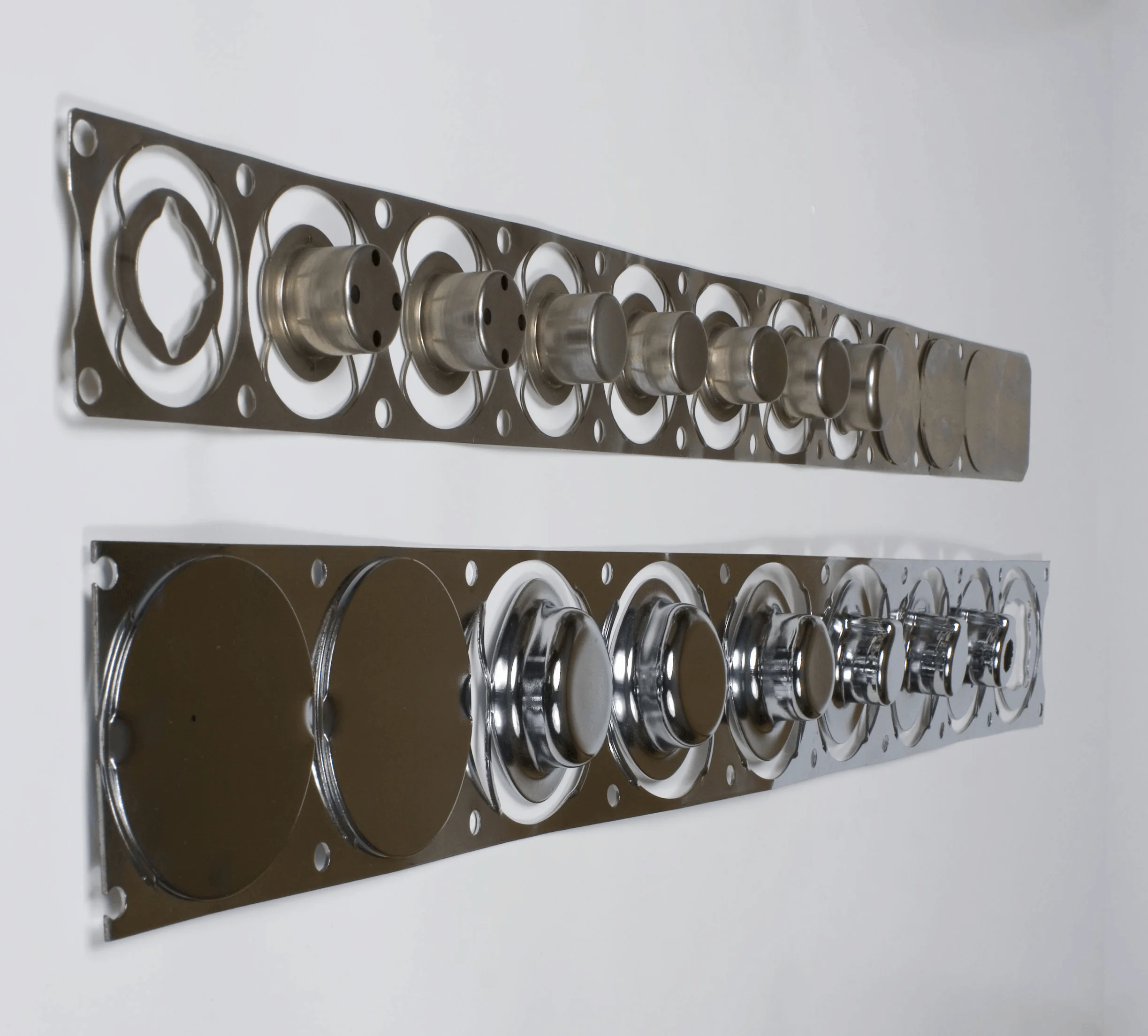
Expert Guide: How to Reduce Metal Stamping Costs Without Sacrificing Quality
In today’s competitive manufacturing landscape, balancing cost efficiency with quality is crucial. This comprehensive guide explores proven strategies to optimize metal stamping costs while maintaining the highest standards of production. Whether you’re a manufacturing engineer or a business owner, you’ll discover practical tips to reduce expenses without compromising on quality.
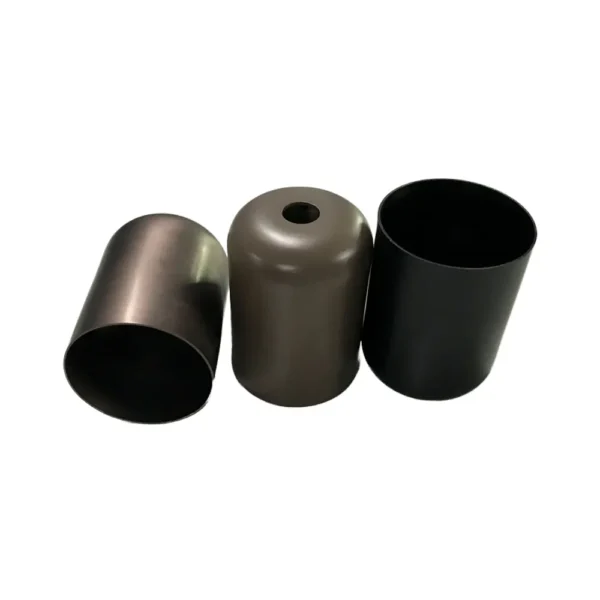
1. What Are the Key Factors Affecting Metal Stamping Costs?
The cost of metal stamping projects depends on several crucial factors. Raw material selection and prices play a significant role, often accounting for 40-60% of total production costs. Production volume also heavily influences pricing – higher volumes typically result in lower per-piece costs. Additionally, tooling requirements and manufacturing process complexity can substantially impact the final price.Manufacturing engineers must consider both direct and indirect costs, including material waste, labor, and secondary processes. Our precision metal stamping services help optimize these factors for maximum cost-effectiveness.
2. How Can Material Selection Impact Your Bottom Line?
Choosing the right material is crucial for cost-effective metal stamping. While cheaper materials might seem attractive initially, they can lead to higher costs due to increased scrap rates or quality issues. Consider factors like:
- Material thickness requirements
- Strength and durability needs
- Processing characteristics
- Material costs and availability
3. Optimizing Design for Cost-Effective Production
Smart design optimization can significantly reduce production costs. Working closely with a manufacturing engineer early in the design phase helps identify potential issues before they become expensive problems. Key considerations include:
- Simplifying complex geometries
- Reducing the number of secondary processes
- Optimizing tolerances where possible
- Minimizing material waste
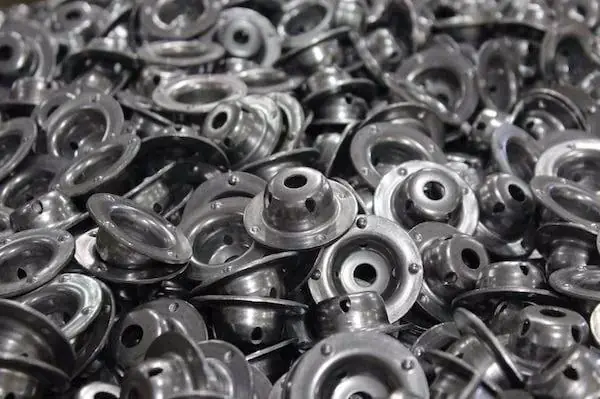
4. The Role of Tooling in Cost Management
Tooling represents a significant initial investment in metal stamping projects. Progressive die stamping, while more expensive upfront, can dramatically reduce per-piece costs in high-volume production. Consider these factors:
- Production volume requirements
- Part complexity
- Expected tool life
- Maintenance costs
5. How to Reduce Scrap and Maximize Material Usage?
Minimizing scrap is crucial for controlling material costs. Modern stamping techniques can help optimize material usage through:
- Efficient nesting of parts
- Optimized strip layout
- Regular tool maintenance
- Quality control measures
6. Quality Control Measures That Save Money
Investing in quality control actually saves money in the long run. Implementing proper inspection procedures helps:
- Reduce defective parts
- Minimize rework costs
- Prevent costly shipping returns
- Maintain customer satisfaction
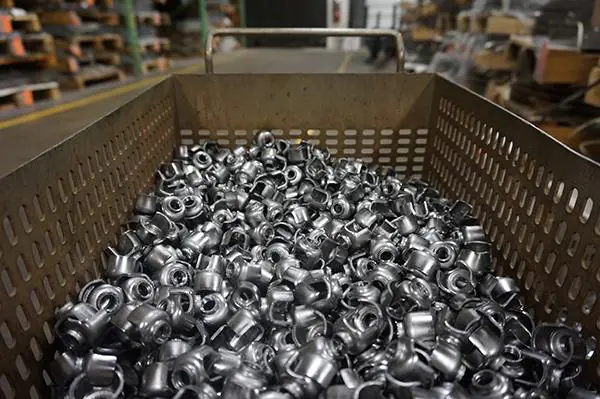
7. The Impact of Production Volume on Costs
Understanding how production volume affects costs is crucial for budget planning. Consider:
- Minimum order quantities
- Setup costs amortization
- Material bulk purchasing
- Production run optimization
8. Automation and Its Cost Benefits
Implementing automation in metal stamping processes can significantly reduce labor costs and improve consistency. Benefits include:
- Reduced labor costs
- Improved quality control
- Increased production speed
- Lower per-piece costs
9. Managing Secondary Operations Costs
Secondary operations like deburring or edge grinding can add significant costs to metal stamped parts. Strategies to manage these costs include:
- Designing parts to minimize secondary operations
- Combining operations where possible
- Evaluating automation options
- Optimizing process flow
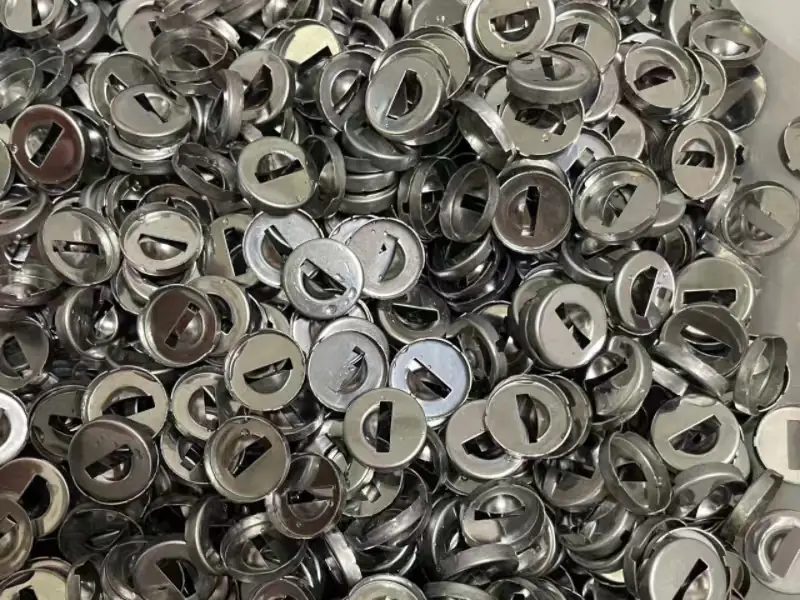
10. Long-term Cost Reduction Strategies
Implementing sustainable cost reduction strategies requires a comprehensive approach:
- Regular tool maintenance programs
- Employee training initiatives
- Process improvement systems
- Quality management systems
Key Takeaways:
- Material selection and optimization are crucial for cost control
- Early design collaboration can prevent expensive modifications later
- Quality control investments pay off through reduced waste and rework
- Production volume significantly impacts per-piece costs
- Automation can provide substantial long-term savings
- Regular maintenance and process optimization are essential
Contact our metal stamping experts to learn how we can help optimize your production costs while maintaining the highest quality standards.