-
No.66 Gaojia, Xingfu Village, Sanqi Town, Yuyao, Ningbo, Kiina
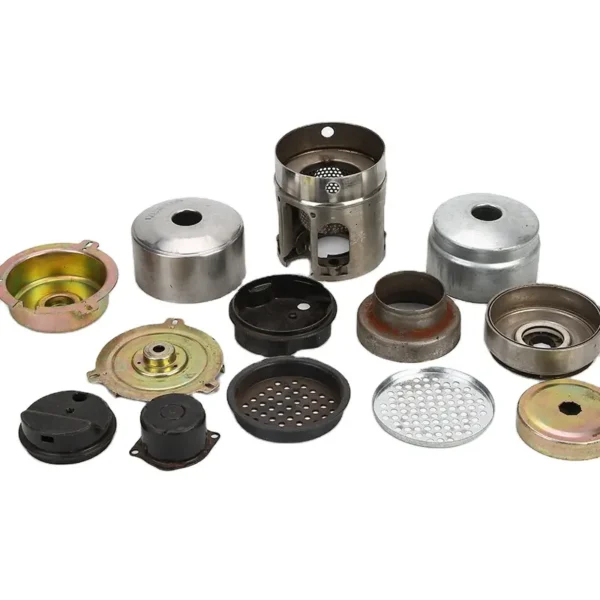
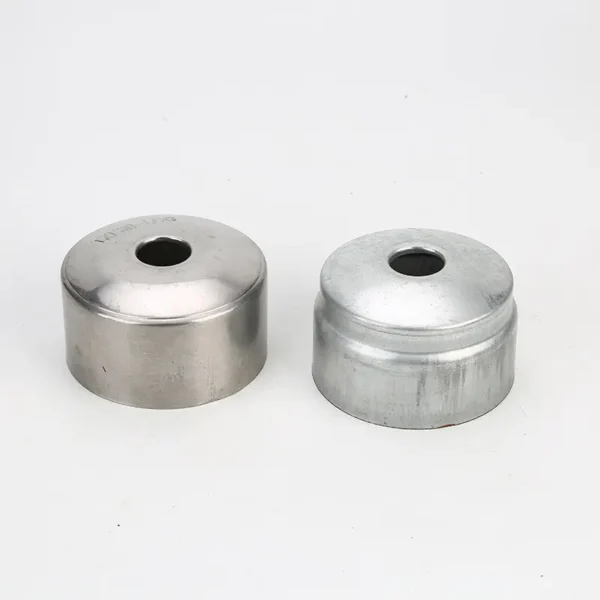
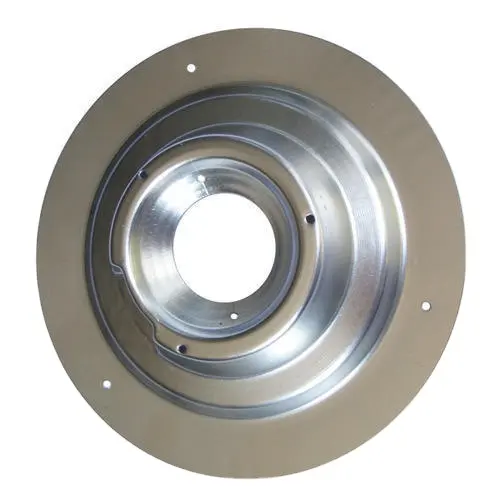
Deep Draw leimausosa valaistukseen
Tuotteen nimi Metallilevyjen valmistus Leimaus taivutushitsausosat
Paksuus cuatomoitu
Materiaalit Sinkki, alumiini, kupari, teräs, jauhemaalaus jne.
Pinta hoitoon Sähköpinnoitus, jauhemaalattu, hiekkapuhallus, lakka
Käsitellä Lävistys, leimaaminen, taivutus, niittaus jne.
Testaus Suolasumutetta
OEM/ODM Hyväksyä
Väri Mukautettu Hyväksytty
Piirustusmuoto 2D/3D/CAD/DWG//STEP/PDF/IGS
Mullistaa valaistus Deep Draw -leimausosilla: Ultimate Guide
Syvävetoleimaus on huippuluokan metallinmuovausprosessi, joka on mullistanut valaisinkomponenttien tuotannon. Tämä kattava opas tutkii valaistuksen syvävetoleimausosien monimutkaisuutta, korostaa niiden etuja ja miksi ne ovat välttämätön investointi valaisinteollisuuden valmistajille.
Syväveto leimausprosessi toiminnassa, luoden tarkkoja metallikomponentteja
Mikä on Deep Draw -leimaus ja kuinka se hyödyttää valaistuksen valmistusta?
Syväveto leimaus on erikoistunut metallin muovausprosessi, joka luo monimutkaisia, kolmiulotteisia osia litteistä metallilevyistä
. Tämä tekniikka on erityisen arvokasta valaistusteollisuudessa, jossa tarkkuus ja kestävyys ovat ensiarvoisen tärkeitä. Prosessissa venytetään ohutlevyä, jota kutsutaan yleisesti aihioksi, tulpan ympärille joko hydraulisessa tai mekaanisessa puristimessa.
.Valaistusosien syvävetoleimauksen etuja ovat:
- Korkea tarkkuus ja johdonmukaisuus: Syvävetoleimaus mahdollistaa tiukat toleranssit ja toistettavat tulokset varmistaen, että jokainen valaistuskomponentti täyttää tarkat vaatimukset.
- Kustannustehokas suurien volyymien tuotantoon: Kun työkalut on asennettu, syvävetoleimaus voi tuottaa suuria määriä osia nopeasti ja tehokkaasti.
- Materiaalien monipuolisuus: Tämä prosessi voi toimia useiden metallien, mukaan lukien alumiinin ja ruostumattoman teräksen, kanssa, mikä tarjoaa vaihtoehtoja erilaisiin valaistussovelluksiin.
- Parannettu rakenteellinen eheys: Muovausprosessilla voidaan luoda osia, joilla on parempi lujuus-painosuhde, jotka ovat ihanteellisia kestäviin valaisimiin.
Kuinka Deep Draw -leimausprosessi toimii valaisinkomponenttien kohdalla?
Valaistuskomponenttien syvävetoleimausprosessi seuraa tyypillisesti seuraavia vaiheita:
- Suunnittelun arvostelu: Insinöörit analysoivat osasuunnittelun varmistaakseen, että se on optimoitu syvävetoprosessia varten.
- Työkalujen suunnittelu ja valmistus: Mukautetut työkalut, mukaan lukien rei'itys ja meisti, luodaan tiettyä valaistusosaa varten.
- Materiaalin valinta: Sopiva metallilevy valitaan valaisinkomponentin vaatimusten perusteella.
- Leimaaminen: Metalli vedetään suuttimeen mekaanisella vaikutuksella, jolloin muodostuu haluttu muoto.
- Viimeistely: Kaikki tarvittavat jälkileimaustoimenpiteet suoritetaan osan viimeistelemiseksi.
Tämän prosessin avulla valmistajat voivat tuottaa monimutkaisia valaistusosia erittäin tarkasti ja tehokkaasti.
Mitä materiaaleja käytetään yleisesti valaistuksen syvävetoleimauksessa?
Syvävetoleimaus voi sovittaa useita metalleja, mikä tekee siitä monipuolisen erilaisiin valaistussovelluksiin. Yleisiä materiaaleja ovat:
- Alumiini: Ihanteellinen kevyisiin, korroosionkestäviin valaisimiin
- Ruostumaton teräs: Täydellinen kestäville, pitkäikäisille ulkovalaistuskomponenteille
- Kupari: Erinomainen lämmönpoistoon LED-valaistusjärjestelmissä
- Messinki: Käytetään usein koristeellisissa valaistuselementeissä
Materiaalin valinta riippuu valaisinosan erityisvaatimuksista, kuten lämmönkestävyys, paino ja esteettinen ulkonäkö.
Miten Deep Draw -leimaus verrattuna muihin valaistusosien metallinmuovausprosesseihin?
Syvävetoleimauksella on useita etuja muihin metallinmuovausprosesseihin verrattuna valaistuskomponenttien osalta:
Käsitellä | Edut | Haitat |
---|---|---|
Deep Draw -leimaus | Suuri tarkkuus, kustannustehokas suurille määrille, monimutkaiset muodot mahdollisia | Korkeammat alkutyökalukustannukset |
Perinteinen leimaus | Yksinkertainen asennus, sopii litteisiin osiin | Rajoitettu syvyys, vähemmän sopiva monimutkaisiin muotoihin |
Kehruu | Sopii hyvin symmetrisille osille | Hitaampi tuotanto, rajoitettu pyöreisiin muotoihin |
Hydromuovaus | Tasainen paksuus, monimutkaiset muodot | Korkeammat laitekustannukset, hitaampi tuotanto |
Syvävetoleimaus on erinomainen monimutkaisten, kolmiulotteisten valaistusosien tuottamisessa erittäin tarkasti ja tehokkaasti, joten se on monien valmistajien suosikkivalinta.
Mitkä ovat tärkeimmät seikat suunniteltaessa valaistusosia syvävetoleimausta varten?
Kun suunnittelet valaistusosia syvävetoleimausta varten, ota huomioon seuraavat tekijät:
- Materiaalin ominaisuudet: Metallin muovattavuuden ja lujuuden ymmärtäminen on ratkaisevan tärkeää onnistuneen syvävedon kannalta.
- Osan geometria: Suunnittele osat, joiden seinämäpaksuus on tasainen ja vältä teräviä kulmia repeytymisen estämiseksi.
- Piirtosuhde: Aihion halkaisijan suhde valmiin osan halkaisijaan tulee optimoida materiaalin ja puristusominaisuuksien mukaan.
- Voitelu: Oikea voitelu on välttämätöntä kitkan ja lämmön vähentämiseksi leimausprosessin aikana.
- Työkalujen suunnittelu: Rei'itys ja meisti on suunniteltava huolellisesti, jotta saavutetaan haluttu osan muoto ilman vikoja.
Nämä tekijät huomioon ottaen suunnittelijat voivat luoda valaistusosia, jotka on optimoitu syvävetoleimausprosessiin ja varmistavat laadukkaan lopputuloksen.
Miten Deep Draw -leimaus edistää kestävyyttä valaistuksen valmistuksessa?
Syvävetoleimaus voi edistää kestävyyttä valaistuksen valmistuksessa useilla tavoilla:
- Materiaalitehokkuus: Prosessi minimoi materiaalihukan verrattuna vähentäviin valmistusmenetelmiin.
- Energiatehokkuus: Kun syväveto leimaus on asennettu, se voi tuottaa osia nopeasti suhteellisen alhaisella energiankulutuksella.
- Kestävyys: Valmistetut korkealaatuiset osat voivat johtaa pidempään kestäviin valaistustuotteisiin, mikä vähentää toistuvien vaihtojen tarvetta.
- Kierrätettävyys: Monet syvävetoleimauksessa käytetyt metallit, kuten alumiini, ovat helposti kierrätettävissä tuotteen käyttöiän lopussa.
Nämä tekijät tekevät syvävetoleimauksesta ympäristöystävällisen valinnan kestävään kehitykseen sitoutuneille valaisinvalmistajille.
Mitkä laadunvalvontatoimenpiteet ovat välttämättömiä valaistusosien syvävetoleimauksessa?
Syvävedettyjen valaistusosien laadun varmistaminen on ratkaisevan tärkeää tuotteen suorituskyvyn ja luotettavuuden ylläpitämiseksi. Keskeisiä laadunvalvontatoimenpiteitä ovat:
- Materiaalin tarkastus: Metallilevyn laadun ja ominaisuuksien tarkistaminen ennen leimaamista.
- Prosessinaikainen seuranta: Antureiden ja kameroiden käyttö vikojen havaitsemiseen leimausprosessin aikana.
- Mittatarkistukset: Mittaa osia säännöllisesti varmistaaksesi, että ne täyttävät määritetyt toleranssit.
- Pintakäsittelyn tarkastus: Osien tutkiminen naarmujen, kolhujen tai muiden pinnan epätasaisuuksien varalta.
- Toiminnallinen testaus: Varmistetaan, että leimatut osat toimivat lopullisessa valaistuskokoonpanossa tarkoitetulla tavalla.
Näiden laadunvalvontatoimenpiteiden toteuttaminen auttaa ylläpitämään valaistuskomponenttien korkeita standardeja.
Kuinka valmistajat voivat optimoida Deep Draw -leimausprosessinsa valaistusosille?
Valaisinosien syvävetoleimausprosessin optimoimiseksi valmistajat voivat:
- Investoi edistyneisiin työkaluihin: Laadukkaat työkalut voivat parantaa osien yhtenäisyyttä ja vähentää kulumista.
- Toteuta simulointiohjelmisto: Käytä tietokonesimulaatioita mahdollisten ongelmien ennustamiseen ja estämiseen ennen tuotantoa.
- Optimoi voitelu: Valitse oikeat voiteluaineet kitkan ja lämmön vähentämiseksi leimaamisen aikana.
- Automatisoi mahdollisuuksien mukaan: Ota käyttöön automaatio tehokkuuden lisäämiseksi ja inhimillisten virheiden vähentämiseksi.
- Jatkuva koulutus: Pidä käyttäjät ajan tasalla uusimmista syvävetoleimaustekniikoista ja parhaista käytännöistä.
Keskittymällä näihin alueisiin valmistajat voivat parantaa syvävetoleimauskykyään ja tuottaa laadukkaampia valaistusosia tehokkaammin.
Mitkä ovat valaistusteollisuuden syväpiirtoleimauksen tulevaisuuden trendit?
Syvävetoleimauksen tulevaisuus valaistusteollisuudessa näyttää valoisalta, ja siinä on useita nousevia trendejä:
- Integrointi älykkääseen tuotantoon: Sisältää IoT-antureita ja data-analytiikkaa prosessien reaaliaikaista optimointia varten.
- Edistyneet materiaalit: Uusien metalliseosten ja komposiittien tutkiminen, jotka tarjoavat parempia ominaisuuksia valaistussovelluksiin.
- Miniatyrisointi: Kehitetään tekniikoita pienempien, monimutkaisempien osien tuottamiseksi kompakteja valaistusmalleja varten.
- Kestävän kehityksen painopiste: Ympäristöystävällisten materiaalien ja energiatehokkaiden tuotantomenetelmien korostaminen.
- Räätälöinti: Syvävetoleimausprosessien mukauttaminen pienempiä eriä ja henkilökohtaisia valaistustuotteita varten.
Nämä suuntaukset osoittavat, että syvävetoleimauksella on jatkossakin ratkaiseva rooli valaisinten valmistuksen kehityksessä.Yhteenvetona voidaan todeta, että syvävetoleimaus on tehokas ja monipuolinen prosessi, joka tarjoaa lukuisia etuja valaistuskomponenttien valmistukseen. Sen kyky luoda monimutkaisia, tarkkoja osia tehokkaasti tekee siitä korvaamattoman työkalun valmistajille, jotka haluavat pysyä kilpailukykyisinä nopeasti kehittyvässä valaistusteollisuudessa. Ymmärtämällä syvävetoleimauksen monimutkaisuudet ja pysymällä ajan tasalla nousevista trendeistä, valaistusvalmistajat voivat hyödyntää tätä tekniikkaa tuottaakseen korkealaatuisia, innovatiivisia tuotteita, jotka täyttävät nykyajan kuluttajien vaatimukset.Lisätietoja siitä, kuinka syvävetoleimaus voi mullistaa valaisimien valmistusprosessin, ota yhteyttä metallileimausasiantuntijoihimme tänään. Tiimimme klo Metallileimamestari on valmis auttamaan sinua tutkimaan syvävetoleimauksen mahdollisuuksia erityisissä valaistussovelluksissasi.