-
No.66 Gaojia, village de Xingfu, ville de Sanqi, Yuyao, Ningbo, Chine
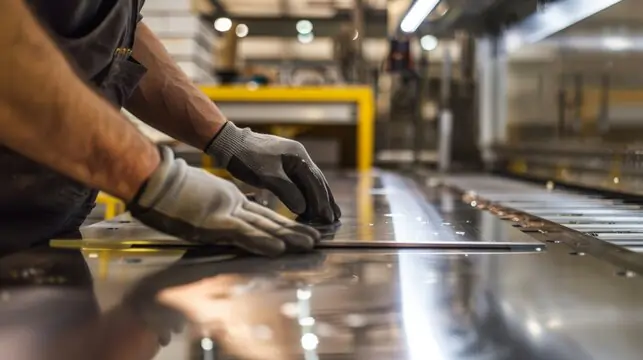
Emboutissage des métaux, moulage et moulage sous pression : un guide complet
Le formage des métaux est essentiel pour créer d'innombrables produits que nous utilisons au quotidien. Mais avec les différentes méthodes disponibles, choisir la bonne peut être délicat. Cet article se penche en profondeur sur trois techniques populaires – l'emboutissage, le moulage et le moulage sous pression – pour vous aider à comprendre leurs différences, leurs avantages et leurs applications idéales. Que vous soyez ingénieur, concepteur de produits ou simplement curieux de la fabrication, vous trouverez ici des informations précieuses. Explorons ensemble le monde fascinant du formage des métaux !
Qu'est-ce que l'emboutissage des métaux exactement ?
L'emboutissage des métaux est un procédé de fabrication polyvalent qui consiste à façonner des tôles plates dans les formes souhaitées à l'aide d'une presse à emboutir et d'outils spécialisés. Pensez-y comme à l'utilisation d'emporte-pièces, mais avec beaucoup plus de force et de précision ! processus d'estampage commence par une feuille de métal, ferreux ou non ferreux, introduite dans une presse à emboutir. La presse est équipée d'un outil, ou matrice, qui contient la forme souhaitée. Lorsque la presse se ferme, la outil coupe et façonne le métal avec force. Ce processus est également connu sous le nom de pressage. La force utilisée peut être hydraulique ou mécanique, selon la complexité et l'épaisseur du métal. métal. Emboutissage de métal offre une grande précision, une répétabilité et est idéal pour volume élevé production de pièces avec une épaisseur de paroi constante et des conceptions complexes. Par exemple, Pinces pour faisceaux de câbles d'alimentation sont fabriqués à l'aide d'un emboutissage précis du métal, soulignant la capacité de la méthode à produire des composants détaillés et cohérents.
L’un des principaux avantages de emboutissage de métal est sa capacité à produire des pièces avec une grande précision et une excellente finition de surface. métal est façonné à froid, le risque de déformation ou de déformation est minime. Cela rend estampillage un excellent choix pour les applications où des tolérances serrées sont requises. estampillage Le procédé permet également la création de formes complexes, notamment des coudes, des brides et des éléments en relief. emboutissage de métal est très efficace pour grandes séries de production parce qu'une fois que le outil est mis en place, le processus peut être automatisé pour produire un grande quantité des pièces rapidement.
Cependant, emboutissage de métal n'est pas sans limites. Le coût initial de la outil et matrice peut être important, en particulier pour les pièces complexes. En outre, estampillage est idéal pour produire des pièces d'épaisseur uniforme, il peut ne pas convenir aux pièces qui nécessitent des variations d'épaisseur importantes ou des géométries internes complexes. Enfin, le estampillage le processus peut générer un grande quantité de ferraille matériau, en particulier lors de la création de pièces avec des découpes complexes ou des formes irrégulières, bien qu'une grande partie de ces déchets puisse être recyclée.
Comprendre le processus de casting : un aperçu
Le casting, également connu sous le nom de moulage de métal, est l'un des plus anciens procédés de fabrication, datant de plusieurs milliers d'années. Contrairement à estampillage, qui façonne le solide tôle, le moulage consiste à faire fondre le métal et le verser dans une cavité de moule qui correspond à la forme souhaitée. Une fois le métal en fusion refroidit et se solidifie, le moule est retiré, révélant la pièce moulée. processus de moulage permet la création de formes complexes et convient à une large gamme de pièces et composants métalliquesIl existe plusieurs variantes du procédé de moulage, notamment le moulage au sable, le moulage à la cire perdue et le moulage sous pression, chacun ayant ses propres avantages et inconvénients. Par exemple, le procédé de création d'un Base de support (fonte) 14,75 po (375 mm) met en évidence la polyvalence du moulage dans la production de formes robustes et complexes.
Le choix de processus de moulage dépend de plusieurs facteurs, notamment du type de métal, la complexité de la pièce, la finition de surface requise et le volume de production. Le moulage au sable, par exemple, est un procédé polyvalent et relativement peu coûteux qui utilise des moules en sable, ce qui le rend adapté aux grandes pièces et aux volumes de production faibles à moyens. Le moulage à la cire perdue, quant à lui, utilise un moule en céramique créé à partir d'un modèle en cire, ce qui permet d'obtenir des détails très complexes et une excellente finition de surface. Ce procédé est souvent utilisé pour les pièces de haute précision, telles que celles utilisées dans les industries aérospatiale et médicale. processus de moulage utilise des matériaux ferreux et non ferreux.
Un avantage important du moulage est sa capacité à créer des pièces avec des géométries internes complexes et des épaisseurs de paroi variables qui seraient difficiles ou impossibles à réaliser avec estampillage. De plus, le moulage peut s'adapter à une large gamme de métal alliages, y compris ceux ayant des points de fusion élevés qui ne sont pas facilement formés par d'autres procédés. Cependant, fonderie peut entraîner une précision dimensionnelle inférieure et une finition de surface plus rugueuse par rapport à estampillage ou moulage sous pression. Fonderie La fabrication de pièces moulées en métal a également tendance à nécessiter davantage de main-d'œuvre et peut nécessiter des opérations d'usinage ou de finition supplémentaires pour obtenir les tolérances et la qualité de surface souhaitées. La porosité peut parfois être un problème avec le métal coulé.
Plongée dans le moulage sous pression : précision et efficacité
Le moulage sous pression est une spécialité processus de moulage qui utilise un moule ou une matrice réutilisable pour produire pièces métalliques. Dans le processus de moulage sous pression, métal en fusion est injecté dans la cavité de la matrice sous haute pression. Cette pression garantit que le métal en fusion remplit toute la cavité et produit une pièce aux détails fins et à la finition de surface lisse. Le moule est généralement en acier trempé et peut supporter plusieurs cycles de coulée. machine de moulage sous pression contrôle avec précision la vitesse d'injection, la pression et le taux de refroidissement pour garantir une qualité constante des pièces. Le moulage sous pression produit des pièces métalliques complexes en grande quantité.
L’un des principaux avantages du moulage sous pression est sa capacité à produire des pièces avec une excellente précision dimensionnelle et une finition de surface supérieure. haute pression l'injection garantit que le métal en fusion remplit chaque coin de la matrice, ce qui donne des pièces aux bords tranchants et aux détails complexes. Coulée sous pression est également très efficace pour production à grande échelle, car les cycles d'injection et de refroidissement rapides permettent un taux de production élevé. moulage sous pression produit des pièces avec de bonnes propriétés mécaniques, car la solidification rapide donne un grain fin microstructure.
Cependant, moulage sous pression présente également certaines limites. Le coût initial de la matrice est élevé, ce qui la rend économique uniquement pour grande production fonctionne. Aussi, moulage sous pression La coulée sous pression est principalement adaptée aux métaux non ferreux à bas point de fusion, tels que les alliages d'aluminium, de zinc et de magnésium. Les métaux ferreux, comme l'acier, nécessitent des matériaux de moulage spéciaux et des pressions d'injection plus élevées, ce qui peut augmenter le coût et la complexité du processus. Enfin, la taille et le poids des pièces moulées sous pression sont limités par la capacité de la machine de coulée sous pression. Les pièces qui mettent beaucoup de temps à refroidir peuvent ne pas convenir à ce processus.
Moulage et emboutissage : une comparaison détaillée
Au moment de choisir entre fonderie et estampillage, plusieurs facteurs doivent être pris en compte. Voici une analyse détaillée pour vous aider à faire le bon choix :
Fonctionnalité | Fonderie | Estampillage |
---|---|---|
Métal Formulaire | Fondu | Feuille solide |
Complexité des pièces | Haut (géométries internes complexes) | Modéré (épaisseur uniforme) |
Précision dimensionnelle | Inférieur | Plus haut |
Finition de surface | Plus rugueux (peut nécessiter une finition) | Plus lisse |
Volume de production | De faible à élevé (selon le processus) | Élevé (surtout pour les grandes séries) |
Coût de l'outillage | Plus bas pour le moulage au sable, plus haut pour le moulage sous pression | Élevé pour les matrices complexes |
Gamme de matériaux | Large (y compris les alliages à point de fusion élevé) | Principalement des métaux ductiles |
Délai de mise en œuvre | Plus long | Plus court |
Coût par pièce | Plus bas pour les gros volumes, plus haut pour les petites séries | Plus bas pour les gros volumes, plus haut pour les petites séries |
Fonderie est généralement préféré pour les pièces aux formes complexes, aux cavités internes ou aux épaisseurs de paroi variables. Le métal en fusion peut s'écouler dans des formes de moule complexes, permettant des conceptions qui seraient difficiles ou impossibles à réaliser avec estampillage. D'autre part, estampillage est mieux adapté aux pièces qui nécessitent une grande précision dimensionnelle, une excellente finition de surface et qui sont produites en grandes quantités. La nature de travail à froid de estampillage assure une qualité constante des pièces et minimise le besoin d'opérations de finition secondaires. Supports de télécommunication illustrent des pièces idéalement adaptées à l'emboutissage des métaux en raison de leur besoin d'uniformité et de dimensions précises dans la production à grande échelle.
Par exemple, les blocs moteurs, les carters de pompe et les sculptures complexes sont souvent produits par fonderie, tandis que les panneaux de carrosserie, les supports et les connecteurs électriques des automobiles sont généralement fabriqués par estampillage. Le choix dépend également du type de métal, le volume de production requis et le budget global du projet. Le moulage implique une fonderie pour les grandes pièces métalliques moulées. Le moulage est également un moyen rentable de créer une pièce en acier.
Moulage sous pression ou emboutissage : quand choisir ?
Coulée sous pression et estampillage sont tous deux des procédés de fabrication à haut volume, mais ils présentent des avantages et des inconvénients distincts. Voici une comparaison :
Fonctionnalité | Coulée sous pression | Estampillage |
---|---|---|
Métal Formulaire | Fondu | Feuille solide |
Complexité des pièces | Haut (détails complexes, parois minces) | Modéré (épaisseur uniforme) |
Précision dimensionnelle | Excellent | Haut |
Finition de surface | Excellent | Lisse |
Volume de production | Très haut | Haut |
Coût de l'outillage | Très haut | Haut |
Gamme de matériaux | Principalement des métaux non ferreux (Al, Zn, Mg) | Métaux ductiles, ferreux et non ferreux |
Délai de mise en œuvre | Plus long | Plus court |
Coût par pièce | Faible pour un volume très élevé | Faible pour un volume élevé |
Coulée sous pression excelle dans la production de pièces aux détails complexes, aux parois minces et à l'excellente finition de surface. à haute pression l'injection garantit que le métal en fusion remplit complètement la cavité de la matrice, ce qui permet d'obtenir des pièces aux caractéristiques nettes et aux tolérances serrées. Coulée sous pression est idéal pour les applications où l'esthétique et la précision sont essentielles, telles que les composants automobiles, les boîtiers électroniques et les produits de consommation. C'est un très rentable Procédé de fabrication de grandes séries, souvent utilisé pour les pièces automobiles et aérospatiales. Le coût réduit est dû à l'automatisation et aux capacités de production en grandes séries.
Estampillage, en revanche, est plus polyvalent en termes de sélection de matériaux et de taille de pièces. Il peut traiter à la fois des métaux ferreux et matériaux non ferreux et convient à une plus large gamme de géométries de pièces. estampillage peut ne pas atteindre le même niveau de détail complexe que le moulage sous pression, il offre une excellente précision dimensionnelle et est très efficace pour grandes séries de production. Estampillage Le moulage sous pression est souvent privilégié pour les pièces qui nécessitent une résistance, une ductilité et une intégrité structurelle élevées. Le choix entre le moulage sous pression et l'emboutissage est dicté par des facteurs tels que l'alliage utilisé, la précision souhaitée, le volume de production et les considérations de coût.
À titre d’exemple, un dissipateur thermique délicat avec de nombreuses ailettes et des parois minces serait mieux produit par moulage sous pression, tandis qu'un support structurel avec des trous de montage et des coudes serait plus adapté pour estampillage. Les deux nécessitent des machines et des outils différents, machine de moulage sous pression et le estampillage presse et composants d'outillage associés. Il est également important de prendre en compte les coûts des matériaux, car les alliages moulés sous pression sont souvent plus chers que les tôles métal.
Moulage sous pression et moulage : exploration des nuances
Alors que les deux moulage sous pression et général fonderie impliquer de verser métal en fusion dans un moule, il existe des différences significatives entre les deux procédés :
Fonctionnalité | Coulée sous pression | Coulée (par exemple, moulage au sable) |
---|---|---|
Type de moule | Matrice en acier réutilisable | Moule jetable (par exemple, sable, céramique) |
Pression | Injection haute pression | Gravité ou basse pression |
Précision dimensionnelle | Excellent | Inférieur |
Finition de surface | Excellent | Plus rugueux |
Volume de production | Très haut | Faible à moyen |
Coût de l'outillage | Très haut | Inférieur |
Complexité des pièces | Haut (parois fines, détails complexes) | Élevé (géométries internes complexes) |
Gamme de matériaux | Principalement des métaux non ferreux | Large gamme (ferreux et non ferreux) |
Délai de mise en œuvre | Plus court (une fois la matrice réalisée) | Plus long |
Coût par pièce | Faible pour un volume très élevé | Plus élevé pour les petites séries, plus bas pour les grandes séries |
Coulée sous pression, avec sa matrice en acier réutilisable et à haute pression L'injection sous pression offre une précision dimensionnelle, une finition de surface et des taux de production supérieurs. Le moulage sous pression utilise des machines spécialisées pour injecter du métal en fusion dans un moule sous haute pression, ce qui nécessite un type de métal spécifique. La vitesse de refroidissement rapide permet également d'obtenir des pièces dotées d'excellentes propriétés mécaniques. Cependant, le coût élevé du moule limite son utilisation à production à grande échelle. Coulée sous pression produit des pièces qui ont un niveau élevé de répétabilité. Il s'agit d'un aspect important de la fabrication, qui moulage sous pression a sur d'autres méthodes de moulage.
Général fonderie Les procédés de moulage au sable et à la cire perdue utilisent des moules jetables et des pressions plus faibles. Cela permet une plus grande flexibilité dans la taille et la complexité des pièces, ainsi que la possibilité de mouler une plus large gamme de matériaux, y compris des alliages ferreux à points de fusion élevés. Les coûts d'outillage inférieurs rendent le moulage adapté aux petites séries de production et aux pièces prototypes. Cependant, la précision dimensionnelle et la finition de surface sont généralement inférieures à celles obtenues avec le moulage sous pression, et des opérations d'usinage ou de finition supplémentaires peuvent être nécessaires. le casting est deux différents procédés adaptés à différentes tâches. Le moulage permet au fabricant de produire des pièces plus grandes. De plus, vous disposez d'un plus grand choix de métaux lorsque vous utilisez un fonderie processus.
Le choix entre moulage sous pression et général fonderie dépend des exigences spécifiques de l'application. Si une haute précision, une excellente finition de surface et production à grande échelle Si des géométries internes complexes, une large gamme de matériaux ou des volumes de production plus faibles sont nécessaires, le moulage sous pression est le choix privilégié. fonderie peut être plus approprié. Pensez également à coût des matrices, car des moules de plus grande précision se traduisent par un coût de production plus élevé. Les composants des matrices doivent être plus durables et fabriqués à partir de métaux et d'alliages plus résistants. Cela augmente le coût des matrices.
Acier embouti et métal moulé : une perspective de résistance et de durabilité
L'acier estampé et le métal moulé présentent des propriétés mécaniques différentes en raison de leurs processus de fabrication distincts et des microstructures qui en résultent.
L'acier embouti, étant travaillé à froid, possède généralement une résistance et une ductilité supérieures à celles du métal moulé. Le processus de travail à froid introduit un écrouissage, ce qui augmente le rendement et la résistance à la traction du matériau. Les pièces en acier embouti ont également tendance à avoir une forme plus uniforme. microstructure, ce qui contribue à leurs propriétés mécaniques constantes. La capacité de contrôler le flux de grains pendant la processus d'estampage améliore encore la résistance et la résistance à la fatigue des composants en acier embouti. Supports de châssis estampés Les pièces en acier embouties présentent la résistance et la durabilité que permet l'emboutissage des métaux, ce qui les rend idéales pour les applications exigeantes. L'emboutissage de l'acier présente un avantage considérable en termes de coût et de rapidité.
Le métal coulé, en revanche, peut présenter des propriétés mécaniques variables en fonction du procédé de coulée et de l'alliage utilisé. Les pièces moulées au sable, par exemple, peuvent avoir une résistance et une ductilité inférieures en raison de leur structure à grains plus grossiers et de leur potentiel de porosité. Cependant, les pièces moulées à la cire perdue et les pièces moulées sous pression peuvent atteindre des propriétés mécaniques comparables, voire supérieures à celles de l'acier embouti, en particulier lors de l'utilisation d'alliages à haute résistance. La microstructure du métal coulé est également plus isotrope, ce qui signifie qu'elle présente des propriétés uniformes dans toutes les directions, ce qui peut être bénéfique dans certaines applications. Le métal fondu est souvent utilisé avec divers alliages afin d'améliorer les propriétés physiques de l'acier. pièce moulée.
En général, si la résistance et la ductilité sont des critères importants, l'acier embouti est souvent le choix préféré. Cependant, le métal moulé offre une plus grande flexibilité en termes de sélection d'alliages et la possibilité de créer des formes complexes avec des épaisseurs de paroi variables. La décision finale dépend des exigences spécifiques de l'application, notamment la capacité de charge, la résistance aux chocs et la durée de vie en fatigue.
Le rôle des moules et des matrices dans le formage des métaux
Les moules et les matrices sont des éléments d'outillage essentiels dans les processus de moulage et d'emboutissage. Cependant, leur fonction et leur construction diffèrent considérablement.
En fonderie, un moule est une cavité qui définit la forme extérieure de la pièce. Les moules peuvent être permanents, comme dans le moulage sous pression, ou jetables, comme dans le moulage au sable et le moulage à la cire perdue. Le moule doit pouvoir résister à la température et à la pression du métal en fusion et permettre un retrait facile de la pièce solidifiée. La conception du moule doit également tenir compte du retrait du métal pendant la solidification et inclure des caractéristiques telles que des portes, des rehausses et des évents pour assurer un remplissage correct et minimiser les défauts. matrices de moulage nécessitent un processus de chauffage et de refroidissement pour augmenter les temps de fabrication. surface de la matrice doit être lubrifié afin d'éviter d'endommager la matrice.
En emboutissage, une matrice est un ensemble d'outils qui coupe, façonne et forme la tôle plate. Une matrice se compose généralement d'un poinçon et d'un bloc matrice, qui fonctionnent ensemble pour créer la forme souhaitée. Les matrices peuvent être simples, pour les opérations de découpage et de perçage de base, ou complexes, pour les opérations de formage en plusieurs étapes. La conception de la matrice doit tenir compte de l'épaisseur du matériau, du retour élastique et des tolérances souhaitées de la pièce finie. Mourir nécessite Un entretien minutieux est nécessaire pour garantir la continuité de la production des pièces selon les spécifications requises. Les outilleurs-ajusteurs jouent un rôle important dans le processus de fabrication.
La qualité et la précision du moule ou de la matrice ont un impact direct sur la qualité de la pièce finale. Des moules et des matrices mal conçus ou fabriqués peuvent entraîner des défauts, des imprécisions dimensionnelles et une mauvaise finition de surface. Par conséquent, des investissements importants sont réalisés dans la conception et la fabrication de ces composants d'outillage. coût des matrices Le coût de la matrice peut être un facteur déterminant dans le coût global du processus de fabrication, en particulier pour les pièces complexes ou les productions en grande série. Le coût de la matrice est l'un des facteurs déterminants dans le choix du procédé. Coûts d'outillage sont un facteur important à garder à l’esprit au moment de décider quel processus de fabrication utiliser.
Sélection des matériaux : choisir le métal adapté à la tâche à accomplir
Le choix du matériau est crucial dans les processus de moulage et d'emboutissage. Différents métaux et alliages ont des propriétés différentes, telles que la résistance, la ductilité, le point de fusion et la résistance à la corrosion, qui affectent l'adéquation du matériau à une application particulière. Le choix du type de métal et de ses propriétés physiques est un aspect important de la fabrication.
Pour fonderie, une large gamme d'alliages ferreux et non ferreux peut être utilisée. Les alliages ferreux, tels que la fonte et l'acier, sont connus pour leur grande résistance et leur résistance à l'usure, ce qui les rend adaptés aux composants structurels, aux blocs moteurs et aux engrenages. Les alliages non ferreux, tels que l'aluminium, le zinc et le magnésium, offrent des avantages tels que la légèreté, une bonne résistance à la corrosion et une excellente aptitude à la coulée, ce qui les rend adaptés à des applications telles que les pièces automobiles, les boîtiers électroniques et les produits de consommation. Le casting utilise différents types de métaux et peut utiliser des métaux ferreux et métaux non ferreux. Le métal en fusion est injecté dans un moule et on le laisse refroidir. le casting permet le fabricant de produire des pièces très complexes qui ne peuvent pas être fabriquées par d'autres méthodes. Le casting implique verser métal en fusion dans un moule.
Pour estampillage, le choix des matériaux se limite principalement aux métaux ductiles qui peuvent être facilement façonnés en formes complexes sans se fissurer ni se déchirer. Les matériaux d'emboutissage courants comprennent l'acier, l'aluminium, le cuivre et le laiton. L'acier est souvent choisi pour sa grande résistance, tandis que l'aluminium offre un bon équilibre entre résistance et légèreté. Le cuivre et le laiton sont privilégiés pour leur conductivité électrique et leur résistance à la corrosion. Les alliages d'acier à haute résistance sont souvent utilisés pour les composants automobiles, tandis que les alliages d'aluminium sont couramment utilisés pour les boîtiers électroniques et les produits de consommation. Estampillage utilise souvent un tôle de acier ou aluminium, le feuille de métal est ensuite formé à l'aide d'une presse d'emboutissage. Estampillage est un processus très efficace pour grandes séries de production, et est un populaire processus de fabrication pour diverses industries. Différents métaux les types peuvent être utilisés dans le estampillage processus.
Le choix du matériau dépend de plusieurs facteurs, notamment l'application prévue, les propriétés mécaniques requises, la résistance à la corrosion et le coût. Par exemple, si une résistance élevée à l'usure et à la solidité est requise, un alliage ferreux comme l'acier serait un bon choix pour la coulée. Si la légèreté et la résistance à la corrosion sont des priorités, un alliage non ferreux comme l'aluminium serait plus adapté. Pour l'emboutissage, le matériau doit être suffisamment ductile pour subir le processus de formage sans se fissurer. De plus, estampillage crée pièces métalliques avec très stabilité dimensionnelle. Emboutissage et moulage sous pression Les pièces en acier embouti sont généralement choisies lorsque l'on s'attend à ce que les volumes de production soient plus élevés que d'habitude. Les pièces en acier embouti sont souvent utilisées dans les applications automobiles et de construction. Les pièces en acier moulé sont également utilisées dans l'industrie automobile.
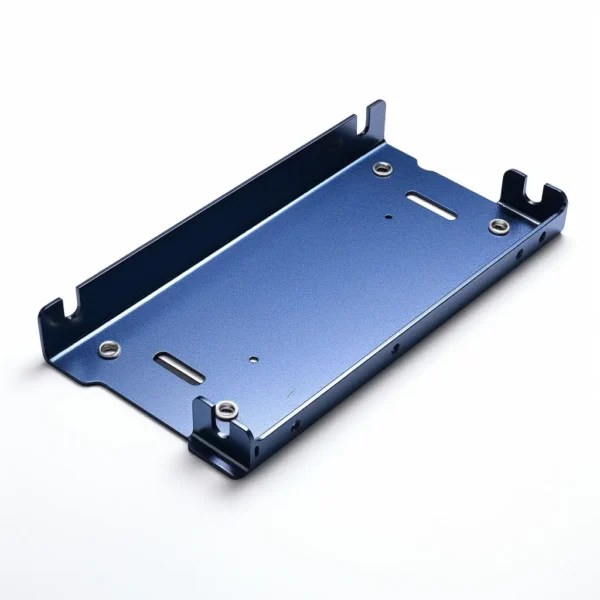
Considérations sur les coûts dans le formage des métaux
Le coût est un facteur critique dans tout processus de fabrication, et le moulage et l'emboutissage ont chacun leur propre structure de coûts. Le coût global d'une pièce dépend de plusieurs facteurs, notamment le coût des matériaux, le coût de l'outillage, le coût de la main-d'œuvre et les frais généraux.
En fonderie, le coût du matériau est directement proportionnel au poids de la pièce et au coût de l'alliage utilisé. Les coûts d'outillage pour la coulée au sable sont relativement faibles, car les moules en sable sont jetables. En revanche, les coûts d'outillage pour la coulée sous pression sont nettement plus élevés, car les matrices en acier permanentes sont coûteuses à concevoir et à fabriquer. Les coûts de main-d'œuvre peuvent varier en fonction du niveau d'automatisation et de la complexité du processus. La coulée au sable nécessite souvent plus de travail manuel que la coulée sous pression, qui peut être hautement automatisée. Utilisations du moulage sous pression un machine de moulage sous pression qui injecte métal en fusion dans une matrice permanente. La matrice est généralement fabriquée en acier trempé et représente un facteur de coût important. Le casting est également utilisé en conjonction avec le moulage sous pression pour certaines applications. Pour les très grandes pièces qui nécessitent un temps de refroidissement rapide, moulage au sable peuvent être utilisés. Les matrices de moulage pour le moulage au sable peuvent être très rentableLe moulage au sable est souvent utilisé pour les petites séries de production.
Dans l'emboutissage, le coût du matériau est déterminé par la surface de la tôle utilisée et le coût du matériau. Les coûts d'outillage peuvent être élevés pour les matrices complexes, mais le coût par pièce diminue à mesure que le volume de production augmente. Les coûts de main-d'œuvre dans l'emboutissage sont généralement inférieurs à ceux du moulage, car le processus est hautement automatisé. Estampillage est un procédé de formage à froid qui crée pièces métalliques d'un tôle vide. Le blanc est placé entre deux meurt et ensuite une presse hydraulique donne forme au métal. L'emboutissage permet formes complexes et des tolérances élevées et stabilité dimensionnelleLes coûts d'outillage peuvent être très élevés, mais le coût unitaire de production est faible et en fait un rentable solution pour production à grande échelle.
Pour la fonderie et l'emboutissage, les frais généraux incluent des facteurs tels que la location des installations, les services publics et l'entretien de l'équipement. Le volume de production joue un rôle important dans le coût global par pièce. Pour une production en grande série, le coût de l'outillage est amorti sur un grand nombre de pièces, ce qui se traduit par un coût par pièce inférieur. Pour une production en faible série, le coût de l'outillage a un impact plus important sur le coût global par pièce. Lors de la fabrication de pièces en grande série à l'aide de la méthode de moulage sous pression, les matrices doivent être soigneusement conçues pour minimiser l'usure des pièces. surface de la matrice.
Tendances émergentes dans le domaine du formage des métaux
Le domaine du formage des métaux est en constante évolution, avec de nouvelles technologies et techniques émergeant pour améliorer l'efficacité, la précision et la durabilité.
La fabrication additive, également connue sous le nom d'impression 3D, est de plus en plus utilisée pour créer des pièces métalliques complexes directement à partir de conceptions numériques. Cette technologie permet un prototypage rapide et la production de formes complexes qui seraient difficiles, voire impossibles à réaliser avec les méthodes traditionnelles de moulage ou d'emboutissage.
Les procédés de fabrication hybrides, qui combinent des techniques additives et soustractives, gagnent également du terrain. Ces procédés offrent une plus grande flexibilité et permettent de créer des pièces aux caractéristiques internes complexes et aux géométries externes complexes.
De plus, l'accent est de plus en plus mis sur les pratiques de fabrication durables. Cela comprend l'utilisation de matériaux recyclés, la réduction de la consommation d'énergie et la minimisation des déchets. De nouvelles techniques telles que le moulage en forme quasi-définitive et l'emboutissage de précision sont en cours de développement pour réduire le besoin d'opérations d'usinage secondaires et minimiser le gaspillage de matériaux.
Points clés à retenir : choisir le bon procédé de formage des métaux
- Emboutissage de métal est idéal pour la production en grande série de pièces d'épaisseur uniforme et de dimensions précises.
- Fonderie est polyvalent pour créer des formes complexes avec des épaisseurs de paroi variables, mais peut nécessiter une finition supplémentaire.
- Coulée sous pression produit des pièces de haute précision avec une excellente finition de surface, mais se limite généralement aux métaux non ferreux et aux volumes élevés.
- Le choix des matériaux dépend des propriétés mécaniques souhaitées, de la résistance à la corrosion et du coût.
- Les coûts d’outillage constituent un facteur majeur dans le coût global du processus de fabrication.
- Les tendances émergentes telles que la fabrication additive et les processus hybrides façonnent l’avenir du formage des métaux.
Pour toute demande concernant vos besoins spécifiques en matière de formage de métaux, pensez à contacter une entreprise possédant une vaste expérience, telle que Metal Stamp Master, qui se vante 30 ans d'expérienceIls peuvent fournir des conseils d'experts et des solutions personnalisées pour vos projets.