-
No.66 Gaojia, Xingfu Village, Sanqi Town, Yuyao, Ningbo,China
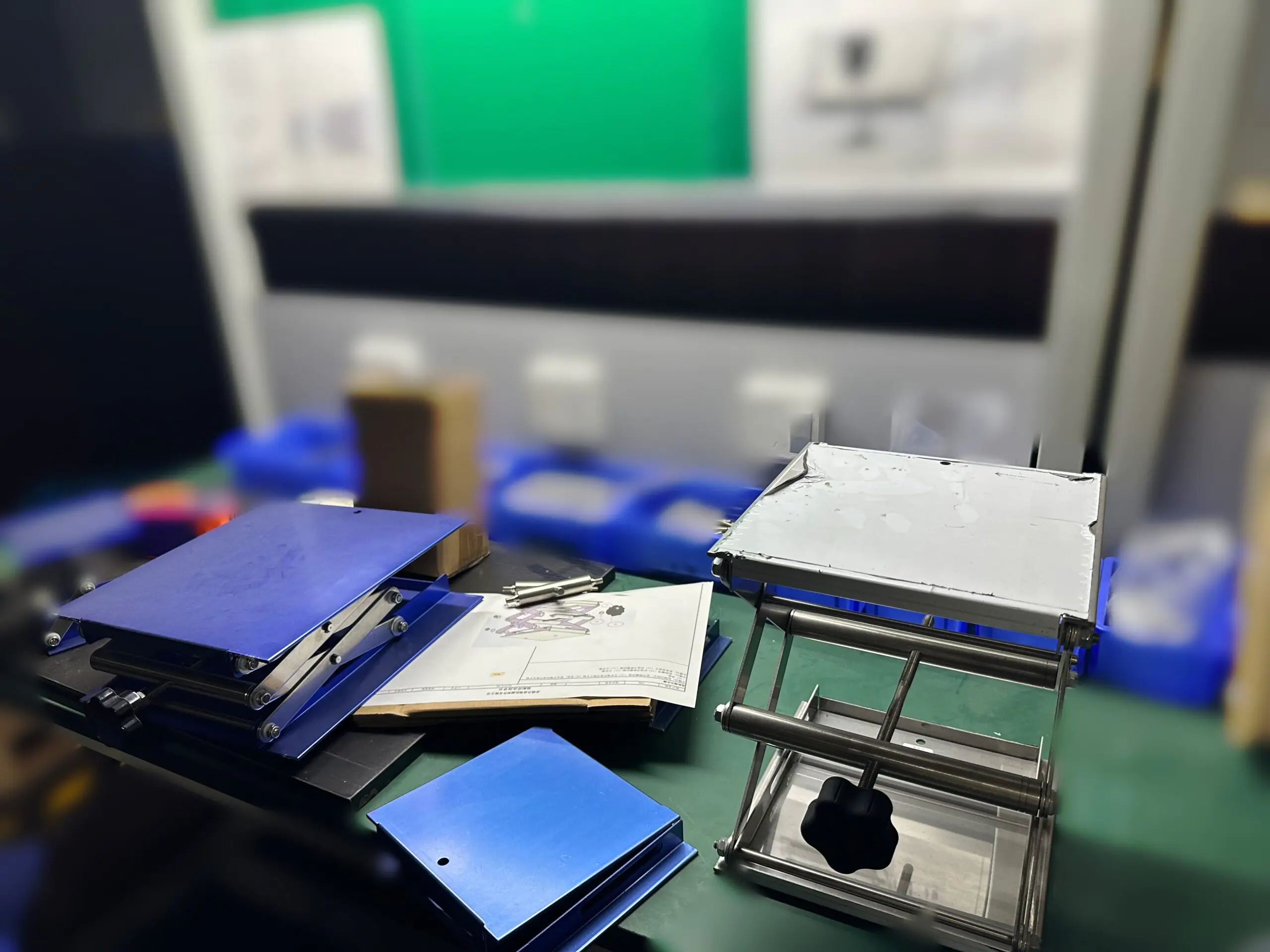
How to Choose the Right Metal Stamping Supplier
Finding the right metal stamping supplier can make or break your manufacturing project. This comprehensive guide will walk you through the essential factors to consider when selecting a metal stamping partner. Whether you’re in automotive, aerospace, or medical devices manufacturing, these insights will help you make an informed decision that aligns with your production needs and quality standards.
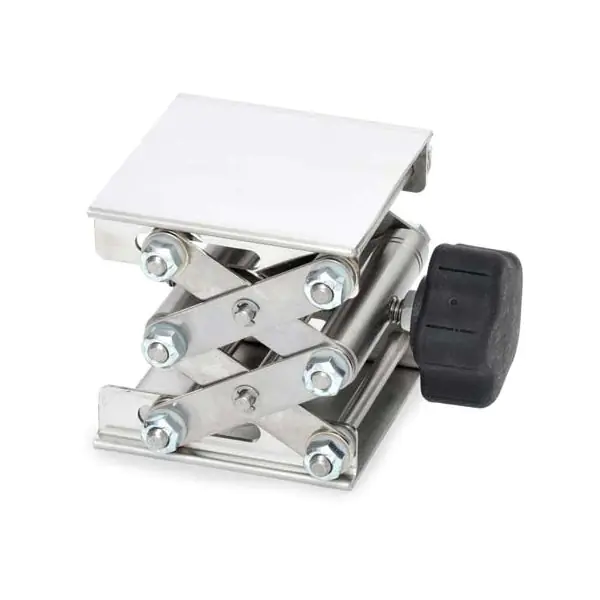
What Makes a Quality Metal Stamping Supplier?
A quality metal stamping supplier combines technical expertise with reliable service. The best companies demonstrate:
- Proven track record in your industry
- ISO 9001 certification
- Consistent quality output
- Strong communication practices
- Competitive pricing without compromising quality
How to Evaluate Technical Capabilities?
When assessing a supplier’s technical capabilities, consider these key factors:
- Equipment and Technology
- Modern stamping presses
- Advanced tool and die design capabilities
- In-house engineering support
- Production Capacity
- Multiple production lines
- Ability to handle various stamping processes
- Flexible manufacturing systems
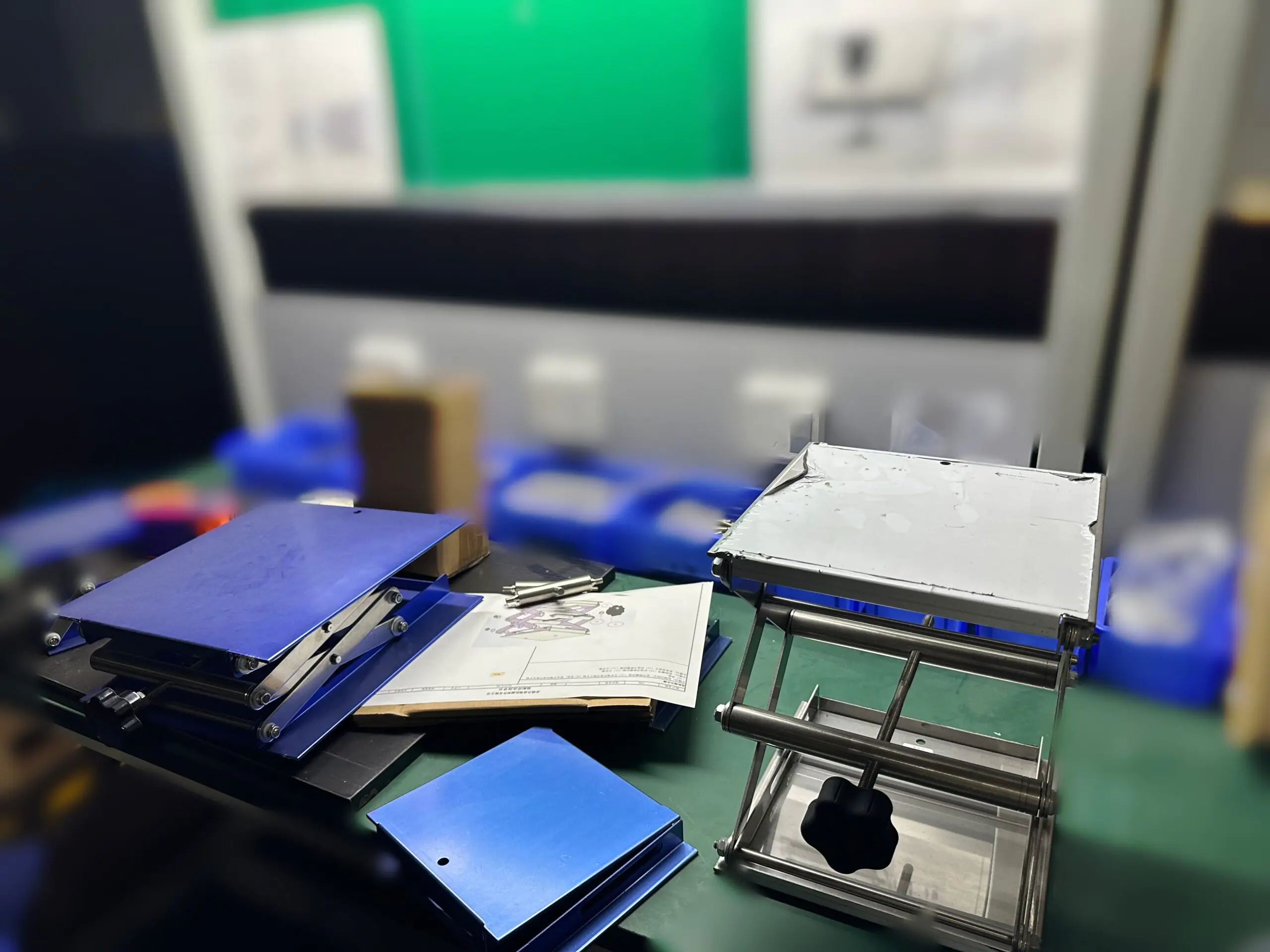
What Quality Assurance Standards Should You Look For?
Quality assurance in metal stamping involves several critical elements:
Quality Aspect | Requirements | Importance |
---|---|---|
Certification | ISO 9001, IATF 16949 | Industry compliance |
Inspection | First article, in-process | Consistency |
Documentation | Material traceability | Quality control |
How Important is Industry Experience?
Industry experience matters significantly when choosing a metal stamping supplier. Look for:
- Specific experience in your industry
- Portfolio of similar projects
- Understanding of industry-specific requirements
- Proven success with comparable applications
What About Production Capacity and Lead Times?
Consider these aspects of production capability:
- Manufacturing Capacity
- Available press tonnage
- Number of production lines
- Automation level
- Lead Time Management
- On-time delivery record
- Emergency response capability
- Supply chain reliability
How to Assess Design and Engineering Capabilities?
Strong design and engineering capabilities include:
- In-house tool and die design
- CAD/CAM expertise
- Prototyping services
- Design for manufacturability (DFM) support
What Role Does Location Play?
Consider these geographical factors:
- Proximity to your facility
- Shipping costs and logistics
- Time zone compatibility
- Communication accessibility
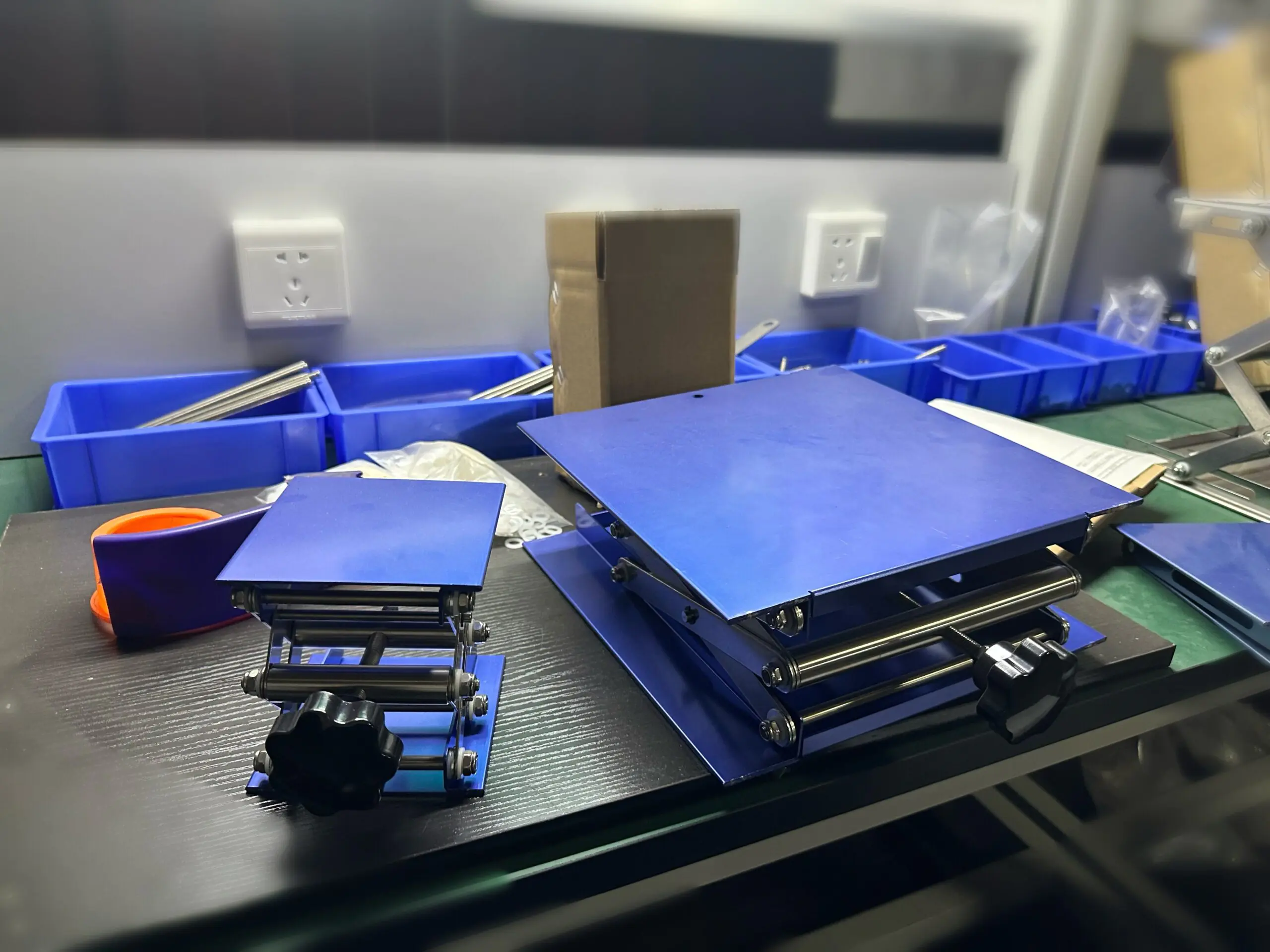
How to Evaluate Cost-Effectiveness?
Look beyond just the price tag:
- Total cost of ownership
- Volume pricing options
- Material cost management
- Value-added services
What Communication Standards Should You Expect?
Effective communication includes:
- Dedicated project managers
- Regular progress updates
- Transparent problem-solving
- Quick response times
How to Make the Final Decision?
Create a decision matrix considering:
- Technical capabilities
- Quality standards
- Cost structure
- Communication effectiveness
- Industry experience
Key Points to Remember:
- Verify quality certifications and standards
- Assess technical capabilities thoroughly
- Consider total cost rather than just price
- Evaluate communication effectiveness
- Check industry-specific experience
- Review production capacity and lead times
- Examine design and engineering capabilities