-
No.66 Gaojia, Xingfu Village, Sanqi Town, Yuyao, Ningbo,China
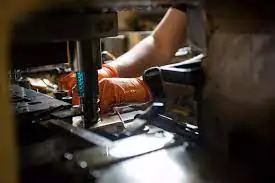
Is blanking the same as stamping?
When it comes to precision metal forming, understanding the differences between fine blanking and conventional stamping is crucial for manufacturers and engineers. This comprehensive guide explores these two distinct processes, their applications, advantages, and when to use each method. Whether you’re planning a new production run or optimizing existing processes, this information will help you make informed decisions.
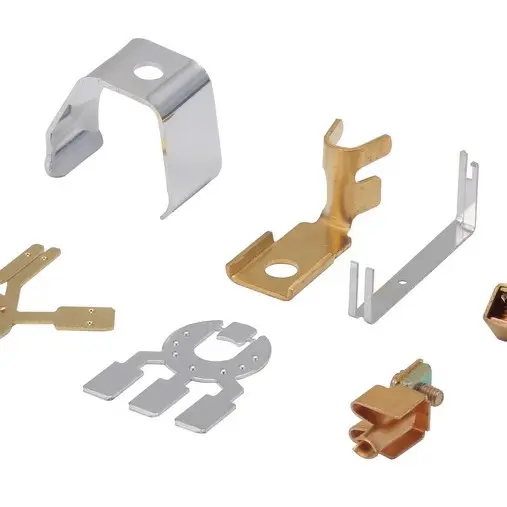
High-precision electrical connectors produced through advanced stamping techniques
What Sets Fine Blanking Apart from Conventional Stamping?
Fine blanking is a specialized metal forming process that produces parts with superior edge quality and dimensional accuracy compared to conventional stamping. While traditional stamping often results in some distortion and rough edges, fine blanking creates components with smooth, perpendicular edges and tight tolerances.The process employs three distinct forces:
- Blanking force
- Counter pressure
- V-ring indenter force
How Does the Fine Blanking Process Work?
The fine blanking process begins with specialized equipment that applies precise pressure control. Unlike conventional stamping, fine blanking uses a hydraulic press with additional mechanisms to hold the material firmly during cutting. This results in:
- Exceptional edge quality
- Minimal material distortion
- Consistent part geometry
What Are the Key Advantages of Fine Blanking?
Fine blanking offers several benefits over conventional stamping:
Feature | Fine Blanking | Conventional Stamping |
---|---|---|
Edge Quality | Superior | Variable |
Tolerance | ±0.001″ | ±0.005″ |
Production Speed | Moderate | High |
Tool Cost | Higher | Lower |
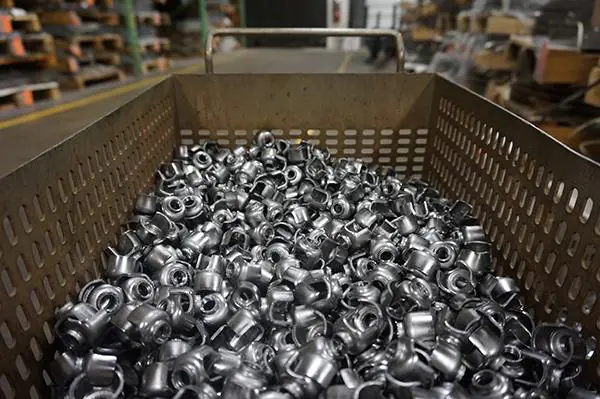
Which Industries Benefit Most from Fine Blanking?
Several sectors rely heavily on fine blanking for critical components:
- Automotive parts manufacturing
- Aerospace components
- Medical devices
- Precision electrical components
What Materials Work Best with Fine Blanking?
Fine blanking performs exceptionally well with:
- Carbon steel
- Stainless steel
- Aluminum alloys
- High-strength materials
How to Choose Between Fine Blanking and Conventional Stamping?
Consider these factors when selecting your process:
- Part Requirements
- Dimensional accuracy needs
- Edge quality specifications
- Surface finish requirements
- Production Factors
- Volume requirements
- Cost considerations
- Lead time constraints
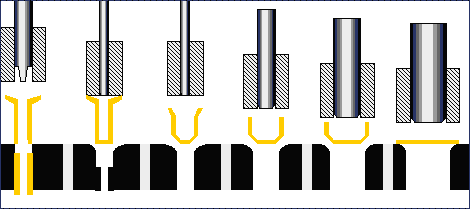
What Are the Common Challenges in Fine Blanking?
Key challenges include:
- Higher tooling costs
- Slower production speeds
- Material thickness limitations
- Equipment complexity
How Does Cost Compare Between the Two Processes?
Cost factors to consider:
- Initial tooling investment
- Production volume requirements
- Secondary operation needs
- Material waste
What Are the Latest Innovations in Fine Blanking Technology?
Recent advancements include:
- Computer-controlled pressure systems
- Advanced material handling
- Improved die designs
- Enhanced monitoring capabilities
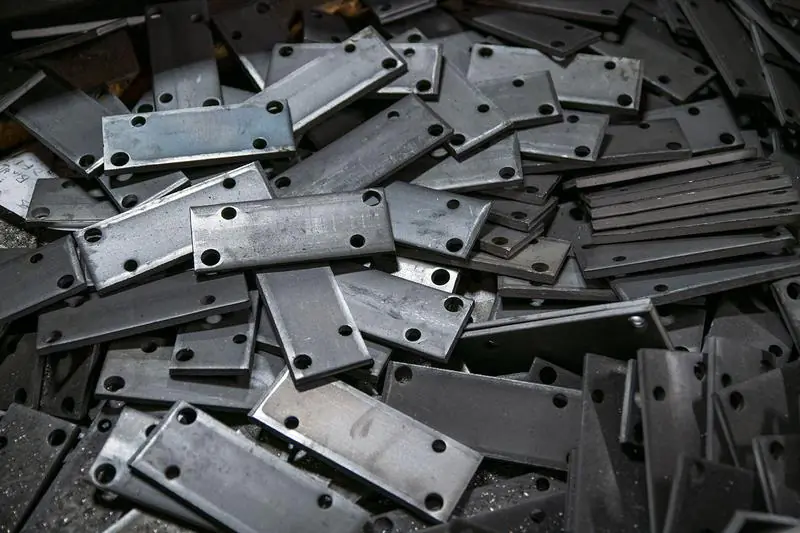
Key Points to Remember:
- Fine blanking produces superior edge quality
- Conventional stamping offers faster production speeds
- Material selection impacts process success
- Production volume affects cost-effectiveness
- Each process has specific ideal applications
Internal Links Used: