-
No.66 Gaojia, Xingfu Village, Sanqi Town, Yuyao, Ningbo,China
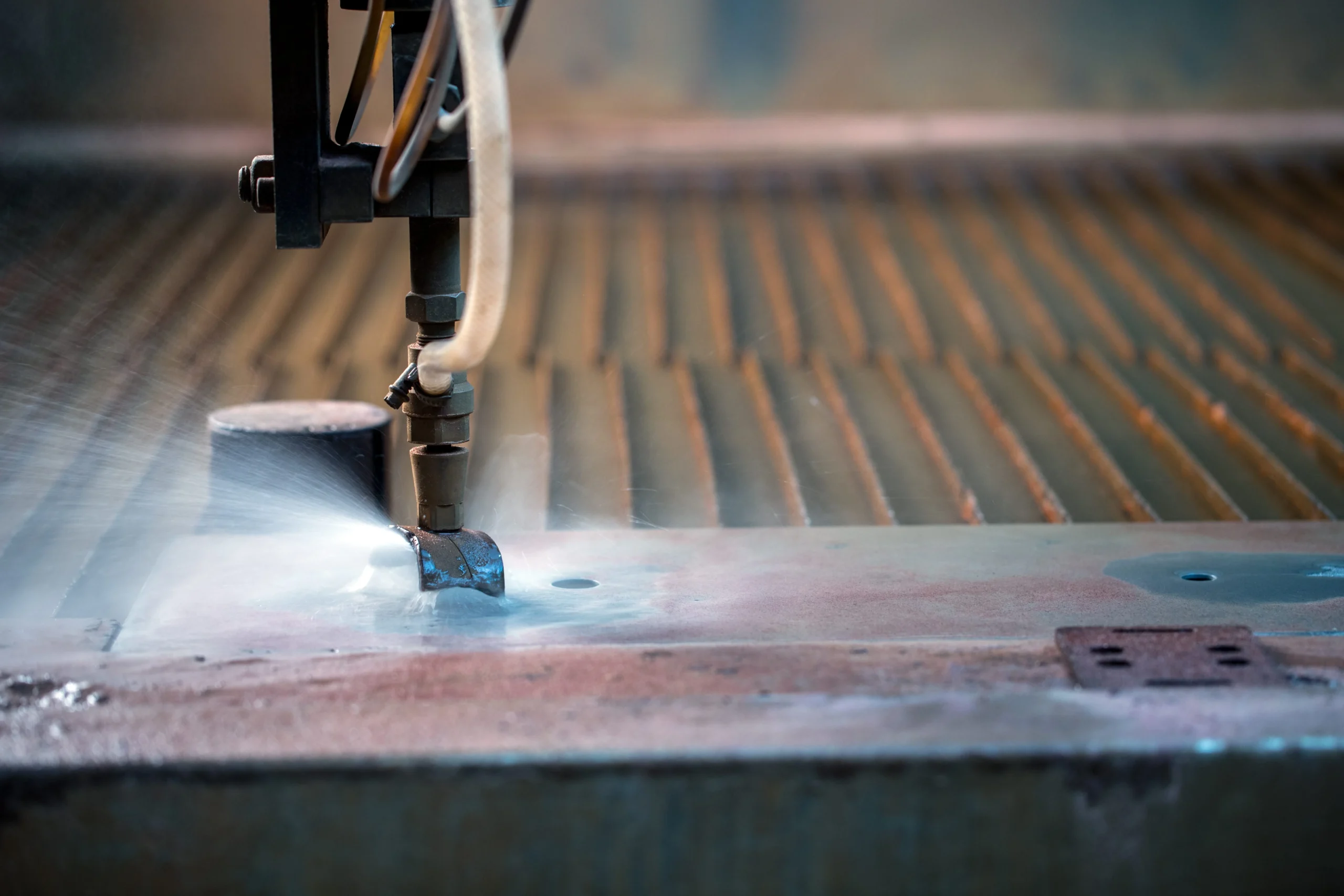
Laser Cutting vs. Waterjet Cutting: A Comprehensive Guide
When it comes to precision cutting, two powerful technologies often come to mind: laser cutting and waterjet cutting. Both methods offer unique advantages and are used across various industries for cutting a wide range of materials. This article provides an in-depth look at both techniques, exploring their differences, capabilities, and ideal applications. Whether you’re an engineer, a designer, or simply curious about these cutting-edge cutting technologies, this guide will equip you with the knowledge you need to make informed decisions. Let’s dive into the world of laser and waterjet cutting!
What is Laser Cutting?
Laser cutting is a precise thermal cutting method that uses a focused laser beam to melt, burn, or vaporize material. The laser beam, generated by a laser machine, is highly concentrated and can achieve a very small cutting slit. This allows for intricate designs and incredibly accurate cut parts. Laser cutting is widely used on various materials, including metals, plastics, wood, and fabrics. The process is controlled by a computer program, which guides the laser along a predefined path, allowing for complex shapes and patterns. Laser cutting is much faster than many other traditional cutting methods, offering efficiency and high repeatability for production.
The laser itself can be either a CO2 laser or a fiber laser, with each type having specific advantages for different materials and applications. Fiber lasers are known for their energy efficiency and precision when working with metals, while CO2 lasers are more versatile for cutting various non-metallic materials, in addition to some metals. The laser cutting process is versatile enough for various cutting work from small intricate designs to large complex parts. Steel Sheet Metal Stamping Enclosure parts, for instance, often require precise laser cuts for vents or access points, highlighting the method’s accuracy in creating complex shapes.
What is Waterjet Cutting?
Waterjet cutting is a cold cutting method that uses a high-pressure stream of water, often mixed with an abrasive material like garnet, to erode away material. The waterjet machine forces pressurized water through a small nozzle, creating an extremely powerful and focused stream of water that is capable of cutting a wide range of materials, from metals and composites to stone and glass. Because it uses water as its cutting medium, waterjet cutting is a “cold cutting” process, meaning that it does not use heat to cut, therefore it doesn’t have a heat-affected zone, which some other methods can.
Waterjet cutting is incredibly versatile and excels at cutting thick or heat-sensitive materials where thermal methods like laser or plasma cutting may not be suitable. The addition of abrasives enhances the cutting ability, allowing waterjet cutting to handle even the toughest materials. The waterjet cutting process is known for its ability to produce smooth, precise cuts without causing heat-related deformation or changes to the material properties. Appliance Parts Metal Brackets might utilize waterjet cutting if they require specific cutouts or shapes in thicker materials where thermal deformation is a concern.
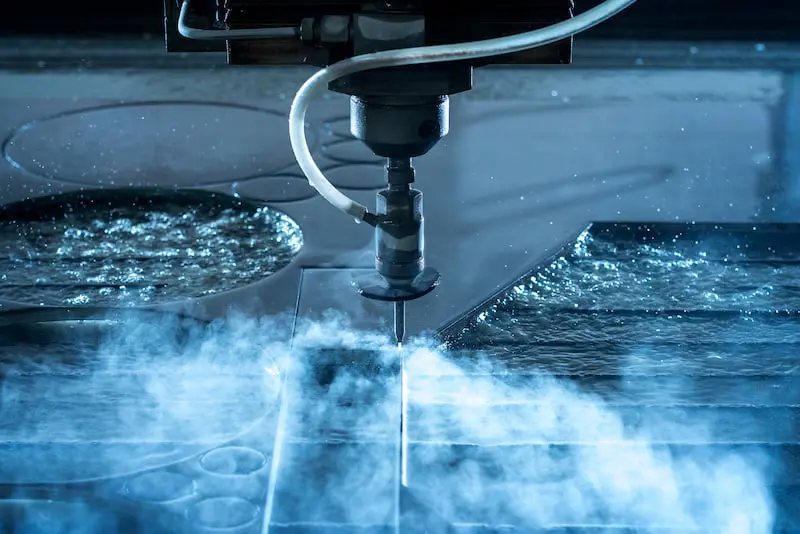
Laser Cutting vs. Waterjet Cutting: Key Differences
Here’s a table summarizing the key differences between laser cutting and waterjet cutting:
Feature | Laser Cutting | Waterjet Cutting |
---|---|---|
Cutting Method | Thermal (melting, burning, vaporizing) | Mechanical (erosion) |
Cutting Medium | Focused laser beam | Pressurized water (with or without abrasives) |
Material Range | Primarily thinner materials (metals, plastics, wood) | Wide range, including thick, heat-sensitive, and hard materials |
Precision | Very high | High |
Heat-Affected Zone | Yes | No (cold cutting) |
Material Thickness | Limited | Can cut much thicker materials |
Cutting Speed | Generally faster for thinner materials | Generally slower, but effective for thicker materials |
Kerf Width (Cutting Slit) | Very narrow | Wider |
Material Waste | Minimal | Can be higher |
Versatility | Good for intricate designs | Excellent for diverse materials and thicknesses |
Operating Cost | Lower for thinner materials | Higher, especially with abrasives |
Material Compatibility: What Can They Cut?
- Laser Cutting: Excels at cutting metals like mild steel, stainless steel, and aluminum, as well as plastics, wood, acrylic, and fabrics. It’s ideal for cutting thinner materials and intricate designs. Laser cutting is much more suited for thin materials.
- Waterjet Cutting: Handles a much wider range of materials, including metals (thick steel, aluminum, titanium), composites, stone, glass, rubber, and foam. It’s known for its ability to cut thick, hard, and heat-sensitive materials, something a laser machine struggles with.
Precision and Cutting Quality
Laser cutting offers superior precision and a narrower cutting slit, resulting in cleaner and more intricate cut parts, especially in thinner materials. It’s often the preferred choice for applications requiring very high precision, such as electronics and fine art.
Waterjet cutting, while also precise, generally has a wider cutting slit and may have a slightly less refined edge finish, especially on thicker materials. However, it produces a smooth finish without heat-affected zones. The cutting tolerance of a waterjet is generally less than that of laser cutting, but this is usually not an issue.
Cutting Speed and Efficiency
In general, laser cutting is faster for thinner materials compared to waterjet cutting, making it more efficient for mass production. Fiber laser cutting is particularly fast for cutting metals.
Waterjet cutting, while slower, is more effective when cutting thicker materials, especially hard and abrasive ones. The waterjet cutting process excels at cutting materials that a laser cutter would find difficult or impossible to cut.
Operating Cost Considerations
The operating cost of laser cutting is generally lower than waterjet cutting, particularly for thinner materials. Laser machines typically have lower maintenance costs. However, the initial cost of the laser equipment is usually higher than a waterjet machine.
Waterjet cutting has higher running costs due to the consumption of abrasive materials and the need for regular maintenance on high-pressure pumps and nozzles. However, waterjet cutting is very versatile and the cost of cutting thicker materials is usually lower than with laser cutting. A waterjet is capable of cutting a wider variety of materials and thicknesses than a laser machine.
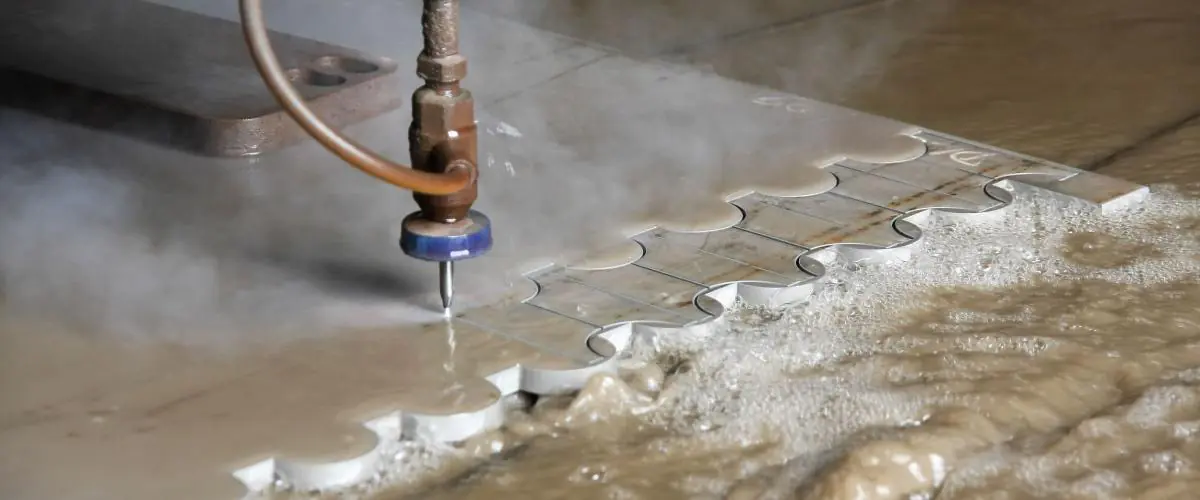
Applications for Laser and Waterjet Cutting
Laser cutting finds extensive use in:
- Sheet metal fabrication
- Electronics manufacturing
- Signage and displays
- Automotive and aerospace
- Textile and garment industry
- Engraving and marking
Waterjet cutting is widely used in:
- Aerospace and defense
- Automotive manufacturing
- Stone and tile fabrication
- Food processing
- Gasket and seal manufacturing
- Architectural and construction
When to Choose Laser Cutting?
You should choose laser cutting if:
- You want to cut thinner materials, especially metals and plastics.
- You require very high precision and intricate details.
- You need a fast and efficient cutting process for high production runs.
- You are working with materials that are not heat-sensitive.
- You require a minimum cutting slit size.
When to Choose Waterjet Cutting?
You should choose waterjet cutting if:
- You need to cut thick, hard, or heat-sensitive materials.
- You are working with a wide range of diverse materials.
- You require a cold cutting process with no heat-affected zone.
- The cutting work requires no changes in the physical properties of the cut material.
- You need to cut very large and thick materials that are not possible with a laser machine.
Hybrid Systems: Combining the Best of Both Worlds
Some cutting machines combine laser cutting and waterjet cutting technologies in a single system, providing maximum versatility. These hybrid systems allow users to switch between the two cutting methods as needed, depending on the cut material and application requirements. This enables manufacturers to cut a wide range of materials and thicknesses on the same machine.
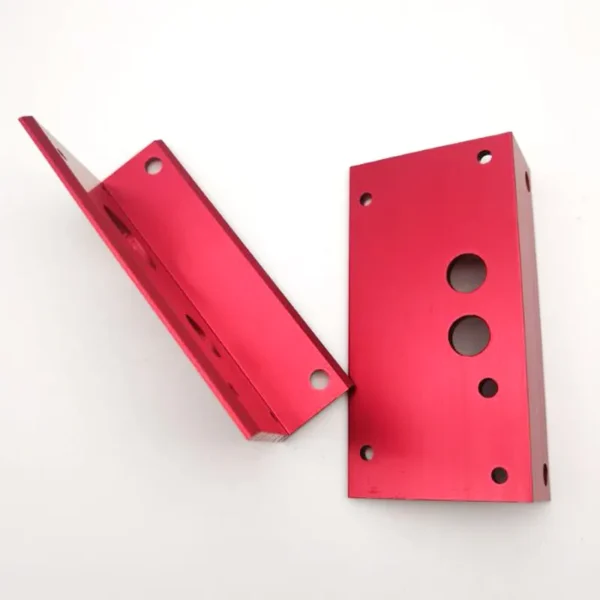
Key Takeaways: Laser vs. Waterjet Cutting
- Laser cutting uses a focused laser beam to melt or vaporize material, ideal for thinner materials and intricate designs.
- Waterjet cutting uses a high-pressure stream of water, with or without abrasives, to erode material, best for thicker and heat-sensitive materials.
- Laser cutting is generally faster and more precise for thinner materials, while waterjet cutting excels at cutting thicker, harder, and more diverse materials.
- Laser cutting typically has a lower operating cost for thinner materials, but waterjet cutting is more versatile.
- The choice between laser cutting and waterjet cutting depends on the specific application requirements, including the type and thickness of material, precision needs, and production volume.
Understanding the strengths and limitations of both laser and waterjet cutting is critical for selecting the best cutting method for your specific project. For instance, while laser cutting might be ideal for precise Electrical Connectors stamping components, waterjet cutting may be preferred for thicker, more robust Stamped Chassis Brackets or similar parts requiring cutting processes with minimal heat effect.