-
No.66 Gaojia, Xingfu Village, Sanqi Town, Yuyao, Ningbo,China
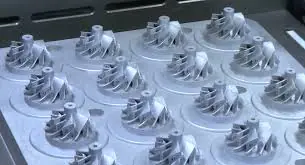
Metal 3D Printing: Everything You Need to Know
Metal 3D printing, also known as metal additive manufacturing, has revolutionized the manufacturing industry, offering unprecedented design freedom and the ability to create complex metal parts directly from digital designs. This comprehensive guide explores the fascinating world of 3D printing metal, covering everything from the various printing processes to the materials used, advantages, limitations, and exciting applications. Whether you’re a seasoned engineer, a hobbyist, or just curious about the potential of 3D printing, this article provides valuable insights into this transformative technology.
How Does Metal 3D Printing Work?
Metal 3D printing builds three-dimensional objects layer by layer from a digital design. Unlike traditional subtractive manufacturing, where material is removed from a block, 3D printing is an additive manufacturing process. Most metal 3D printing processes involve using a metal powder as the starting material. The 3D printer selectively melts or sinters (fuses) the metal powder according to the digital design, building the object layer by layer. Imagine it like drawing with metal, but in three dimensions! Each layer precisely follows the design blueprint, gradually adding to the part’s shape and complexity. Metal Stamping Terminal designs, for example, could be prototyped rapidly and efficiently using this technology, showcasing its potential in producing intricate shapes.
This process allows for incredible precision, making it possible to create incredibly intricate designs, even internal features that are difficult or impossible with conventional methods. This manufacturing method produces extremely accurate parts.
Different 3D Printing Processes for Metal
Several 3D printing techniques are used for metal:
- Powder Bed Fusion: This category includes processes like Direct Metal Laser Sintering (DMLS) and Selective Laser Melting (SLM), where a laser selectively melts the metal powder in a powder bed. These techniques produce parts with excellent mechanical properties and a good surface finish.
- Binder Jetting: In this process, a binding agent is sprayed onto the metal powder to hold the shape. The printed part then undergoes sintering to solidify it. Binder jetting is ideal for large parts and complex geometries but may require post-processing. Metal binder jetting is sometimes called “3D printing”, but technically the process only forms the “green” part. This means that the part will require post-processing, which often includes sintering in a furnace.
- Directed Energy Deposition: This method deposits molten metal onto a substrate, building the part up layer by layer.
- Material Extrusion: This involves extruding a metal filament or paste through a nozzle to build the object.
- Sheet Lamination: Layers of sheet metal are bonded and cut to shape. This method utilizes thin sheets rather than powders.
Each method has its own pros and cons in terms of speed, cost, and the ability to create different kinds of shapes.
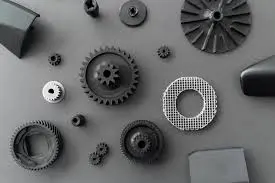
Materials Used in Metal 3D Printing
Various metals and metal alloys are used in 3D printing, including:
- Stainless Steel: Known for its corrosion resistance and strength. The versatility of stainless steel lends itself to diverse applications.
- Aluminum: Lightweight and strong, commonly used in aerospace applications. It’s ideal for parts where weight is critical.
- Titanium: Biocompatible, strong, and lightweight, often used in medical and aerospace industries. Titanium’s biocompatibility opens up possibilities in medical implants and devices.
- Nickel Alloys: These offer high strength and heat resistance, making them suitable for demanding applications.
- Cobalt Chrome: Known for hardness and biocompatibility, commonly used in medical and dental implants.
The choice of material depends on the required material properties, such as strength, corrosion resistance, and biocompatibility. The 3D printing technique also influences material choice.
Advantages of Metal 3D Printing
Metal 3D printing offers several advantages:
- Design Freedom: You can create almost any geometry you can imagine. This flexibility unlocks innovation in product design.
- Rapid Prototyping: Print parts quickly and easily, allowing for faster design iterations. This speeds up the development process significantly.
- Customization: Produce unique, tailored parts on demand. Each part is made to specific needs.
- Reduced Lead Times: Skip traditional tooling processes and shorten production time. This is essential for time-sensitive projects.
- On-Demand Manufacturing: Print what you need when you need it, eliminating large inventories. This streamlines production and reduces waste.
Limitations of Metal 3D Printing
While 3D printing with metals offers many advantages, it also has limitations:
- Cost: Metal 3D printers and materials can be expensive. High cost can be a barrier for smaller businesses.
- Scalability: Printing large quantities can be time-consuming. 3D printing might not be suitable for very high-volume production.
- Surface Finish: 3D printed parts may require post-processing to achieve the desired surface finish. Additional steps might be needed for a smooth finish.
- Material Selection: The range of available metals for 3D printing is still smaller than traditional manufacturing. Material options are expanding but still limited.
- Size Restrictions: The size of 3D printed parts is constrained by the size of the printer’s build platform. Printing very large parts might require assembly.
Applications of 3D Printing in Metal
Metal 3D printing finds applications in various industries:
- Aerospace: Creating lightweight, high-performance parts for aircraft and spacecraft.
- Medical: Printing custom implants, surgical instruments, and medical devices. Lab Lift (Aluminum) 4 in x 4 in (102 mm x 102 mm) showcases a medical application where aluminum’s lightweight properties, facilitated by 3D printing, could be advantageous.
- Automotive: Prototyping and producing customized car parts and tooling.
- Tooling: Creating molds and dies for manufacturing processes.
- Jewelry: Producing complex and personalized jewelry designs.
The Future of Metal 3D Printing
Metal 3D printing is constantly evolving. New materials, processes, and software are continually being developed, expanding the capabilities and applications of this technology. The future looks bright for metal 3D printing, with ongoing advancements promising faster printing speeds, improved material properties, and greater accessibility for a wider range of industries and individuals.
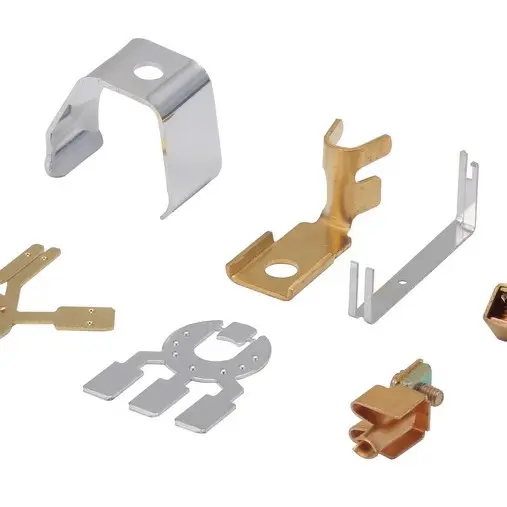
Key Takeaways: Metal 3D Printing
- Metal 3D printing is a revolutionary additive manufacturing technology.
- Several 3D printing processes are available for metal, each with its own strengths and limitations.
- 3D printing enables the creation of complex metal parts directly from digital designs.
- The choice of material depends on the desired mechanical properties and application requirements.
- The 3D printing process involves building an object layer by layer by melting or sintering metal powder.
- Metal 3D printing offers significant advantages over traditional manufacturing, including design freedom, rapid prototyping, and customization.
- Limitations of metal 3D printing include cost, scalability, and material selection.
- The field of 3D printing is rapidly evolving, with continuous advancements promising to further enhance its capabilities.
By understanding these key aspects of metal 3D printing, you can harness the power of this transformative technology to design and manufacture innovative products across a variety of industries. For intricate metal parts requiring complex internal structures, 3D printing is an ideal solution, complementing traditional methods like those used for Sheet Metal Fabrication Products.