-
No.66 Gaojia, Xingfu Village, Sanqi Town, Yuyao, Ningbo,China
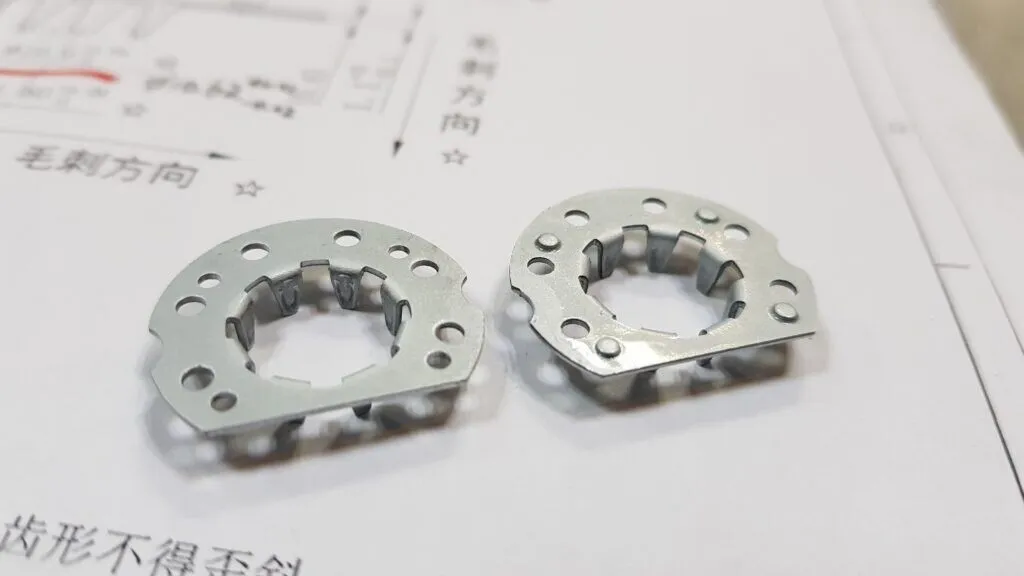
Metal Stamping: Essential Processes, Techniques, and Industry Best Practices
Metal stamping is a fascinating manufacturing process that transforms flat metal sheets into precise, three-dimensional components used in countless industries. This comprehensive guide will walk you through everything you need to know about metal stamping, from basic concepts to advanced techniques. Whether you’re a manufacturer, engineer, or simply curious about this vital industrial process, this article will provide valuable insights into the world of metal stamping.
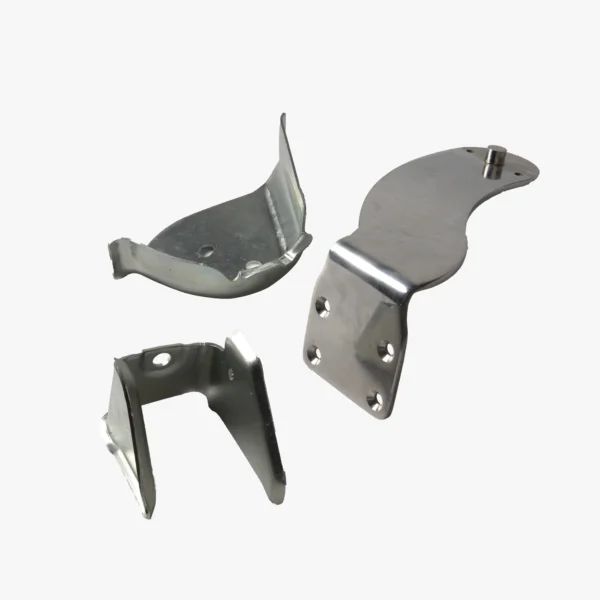
Precision-engineered stamped chassis brackets showcase the capabilities of modern metal stamping
What Is Metal Stamping and Why Is It Important?
Metal stamping is a manufacturing process that uses specialized tools and dies to transform flat metal sheets into specific shapes and components. This versatile technique is crucial in various industries, from automotive manufacturing to consumer electronics. The stamping process involves using a punch and die to shape, cut, and form metal pieces into desired configurations.The importance of metal stamping cannot be overstated, as it enables:
- High-volume production of consistent parts
- Cost-effective manufacturing solutions
- Precise component creation with tight tolerances
- Versatility in working with different metal types
How Does the Metal Stamping Process Work?
The metal stamping process works through a series of carefully controlled steps. It begins with flat metal sheets that are fed into a stamping press, where specialized tools shape the material. The process can include multiple operations such as:
- Blanking
- Piercing
- Bending
- Forming
- Coining
Each step in the process involves using specific stamping tools to achieve the desired outcome, with quality control measures implemented throughout.
What Are the Different Types of Metal Stamping Techniques?
Several metal stamping techniques are commonly used in modern manufacturing:
Progressive Die Stamping
- Performs multiple operations in sequence
- Ideal for high-volume production
- Creates complex parts efficiently
Deep Draw Stamping
- Forms deep, hollow shapes
- Perfect for creating containers and enclosures
- Requires specialized tooling and expertise
Four-Slide Stamping
- Allows for multiple bends and forms
- Ideal for complex geometric shapes
- Cost-effective for certain applications
Learn more about stamped chassis brackets for automotive applications.
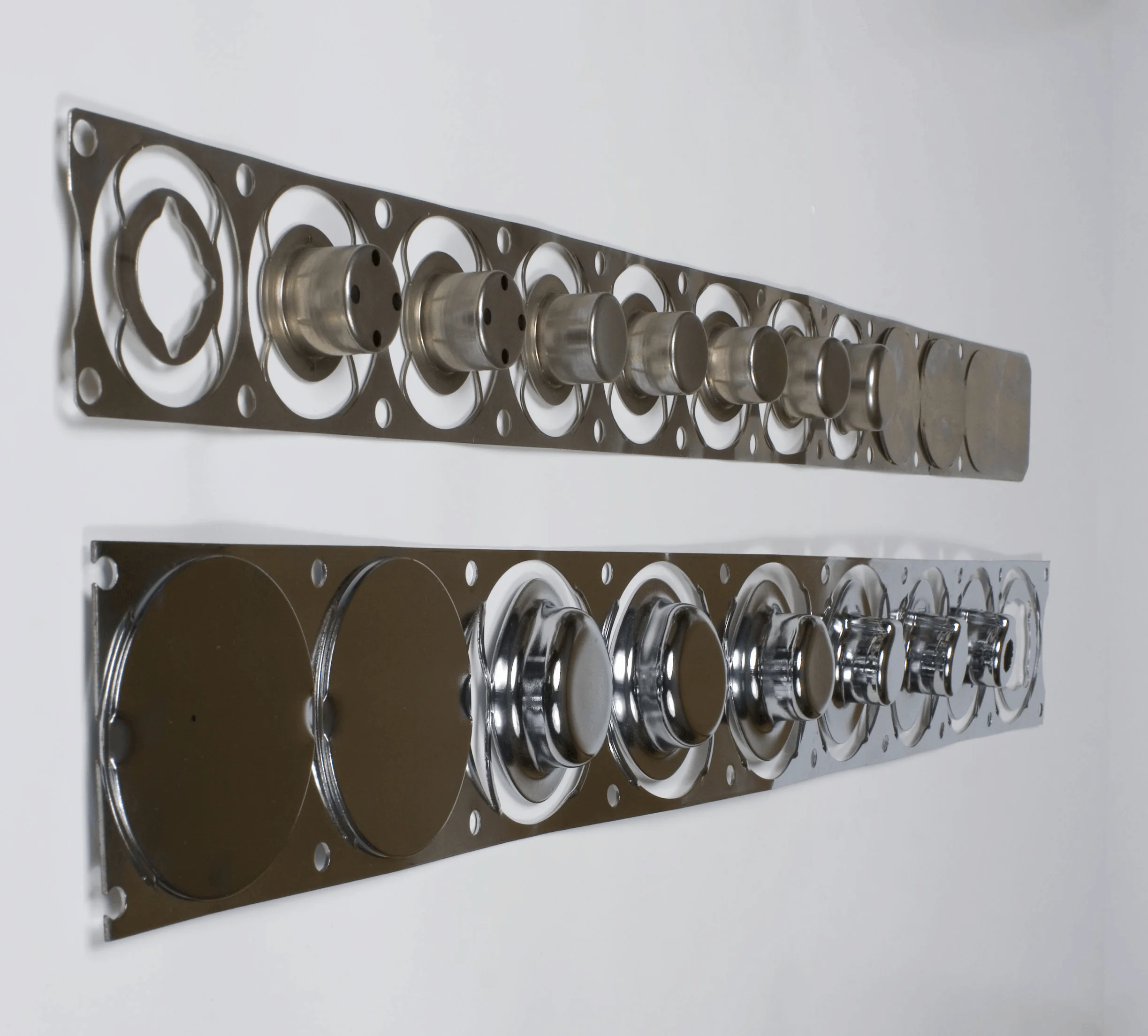
What Materials Are Commonly Used in Metal Stamping?
The type of metal chosen for stamping depends on various factors:
Metal Type | Common Applications | Key Properties |
---|---|---|
Steel | Automotive parts, structural components | Strength, durability |
Aluminum | Electronics, lightweight components | Light weight, corrosion resistance |
Copper | Electrical components, connectors | Electrical conductivity |
Brass | Decorative items, plumbing fixtures | Aesthetic appeal, workability |
What Are the Key Considerations in Metal Stamping Design?
When designing for metal stamping, several factors must be considered:
- Material thickness and grain direction
- Bend radius and tolerance requirements
- Tool design and wear considerations
- Production volume requirements
Explore our selection of electrical connectors stamping for design inspiration.
How to Ensure Quality in Metal Stamping?
Quality control in metal stamping involves:
- Material Selection
- Proper material testing
- Certificate verification
- Grain structure analysis
- Process Control
- Tool maintenance
- Die alignment
- Press calibration
- Inspection Methods
- Dimensional verification
- Surface finish evaluation
- Functionality testing
What Industries Rely on Metal Stamping?
Metal stamping plays a crucial role in numerous industries:
- Automotive manufacturing
- Aerospace
- Electronics
- Consumer goods
- Medical devices
- Construction
Check out our plumbing fixture stamping solutions for industry applications.
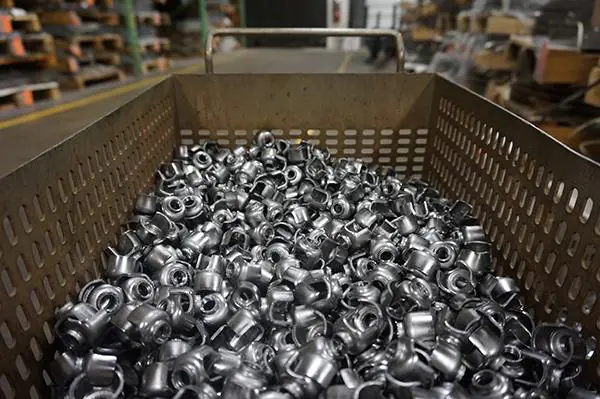
What Are Common Challenges in Metal Stamping?
Manufacturers often face several challenges:
- Material waste management
- Tool wear and maintenance
- Quality consistency
- Production efficiency
- Cost control
How to Choose the Right Metal Stamping Partner?
Consider these factors when selecting a metal stamping manufacturer:✓ Technical capabilities ✓ Quality certifications ✓ Production capacity ✓ Industry experience ✓ Customer service ✓ Cost competitiveness
Future Trends in Metal Stamping
The metal stamping industry continues to evolve with:
- Advanced automation systems
- Smart manufacturing integration
- Sustainable practices
- New material developments
- Improved quality control methods
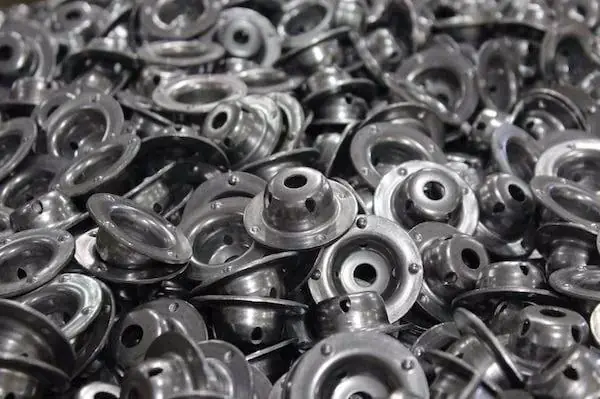
Key Takeaways
- Metal stamping is a versatile manufacturing process essential for many industries
- Various techniques and materials can be used depending on application needs
- Quality control and proper design are crucial for successful outcomes
- The industry continues to evolve with new technologies and practices
- Choosing the right partner is essential for project success
Remember these important points when working with metal stamping:
- Always consider material properties and limitations
- Maintain proper tool maintenance schedules
- Implement robust quality control measures
- Stay updated with industry developments
- Partner with experienced manufacturers
With this comprehensive understanding of metal stamping, you’re better equipped to make informed decisions about your manufacturing needs and requirements.