-
No.66 Gaojia, Xingfu Village, Sanqi Town, Yuyao, Ningbo,China
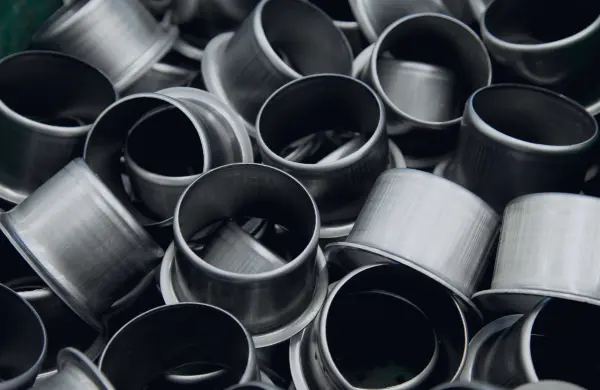
Metal Stamping-MSM: Your Guide to the Metal Stamping Process
Metal stamping is a crucial process in the manufacturing world, responsible for shaping and cutting metal into a vast array of components used in countless products. This comprehensive guide, “Metal Stamping 101,” provides an in-depth look into the fascinating world of metal stamping, covering the various techniques, processes, and applications involved. Whether you’re a seasoned engineer, a manufacturing enthusiast, or simply curious about how everyday metal objects are made, this article will provide valuable insights into the intricacies of metal stamping.
Table of Contents
What is Metal Stamping?
Metal stamping is a cold-forming manufacturing process that uses dies and stamping presses to transform flat metal sheets into specific shapes. It’s a versatile process capable of producing a wide range of parts, from simple brackets to complex automotive components. The metal stamping process involves placing flat sheet metal, in either blank or coil form, into a stamping press where a tool and die surface form the metal into a net shape. This process allows for the creation of intricate designs and precise dimensions, making metal stamping a popular choice for mass production. It’s a very versatile method of creating metal parts.
Metal stamping is known for its efficiency, accuracy, and cost-effectiveness, particularly for high-volume production runs. The process can be used to create a wide variety of shapes and sizes, and it can be performed on a variety of metals, including steel, aluminum, copper, and brass. You can create very intricate shapes using metal stamping. Metal Stamping Terminal components, for instance, are often produced using this method due to its ability to create precise, small-scale parts.
Types of Metal Stamping Techniques
Several types of metal stamping techniques are used, each with its own unique capabilities and applications:
- Progressive Die Stamping: This technique utilizes a series of stamping stations, each performing a specific operation on the metal as it moves through the die. Progressive die stamping is ideal for producing complex parts that require multiple operations, such as cutting, bending, and coining. This process is often used for stamping smaller parts.
- Transfer Die Stamping: Similar to progressive die stamping, transfer die stamping uses multiple stations. However, in this method, the metal part is transferred from one station to the next by a mechanical transfer system, rather than being carried through on a continuous strip. Transfer die stamping is often used for larger parts.
- Deep Draw Stamping: This technique is used to form metal into deep, seamless shapes, such as cups, shells, and containers. Deep draw stamping involves stretching the metal sheet over a die using a punch, creating a three-dimensional form. This method is particularly useful for creating parts with depth and complexity.
- Multi-Slide Stamping: This versatile method uses multiple slides, each carrying a forming tool, to shape the metal from different directions. Multi-slide stamping is ideal for creating complex parts with intricate bends and forms. It’s a highly efficient process for producing small, intricate parts.
These stamping techniques provide manufacturers with a wide range of options for shaping and forming metal. Choosing the appropriate technique depends on factors such as part complexity, material properties, and production volume.
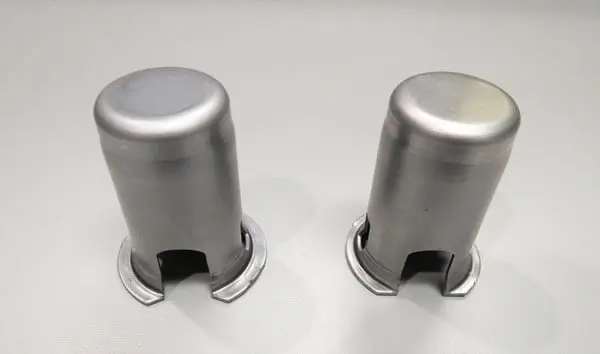
The Metal Stamping Process: A Step-by-Step Guide
The metal stamping process typically involves the following steps:
- Design: The desired metal part is designed using computer-aided design (CAD) software. The metal stamping process requires a very specific design in order to ensure that the part is produced correctly.
- Tool and Die Creation: A stamping die, consisting of a punch and die cavity, is created based on the part design. The die is typically made from tool steel and is designed to withstand the high pressures of the stamping process.
- Material Preparation: Flat metal sheets or coils are prepared for the stamping process. The metal is inspected for defects and cut to the appropriate size. The type of sheet metal used will depend on the desired physical properties of the part.
- Stamping: The metal sheet or coil is fed into the stamping press. The press applies force to the punch, which presses the metal into the die cavity, forming the desired shape. This process is repeated for each part.
- Finishing: The stamped parts may undergo additional finishing processes, such as deburring, cleaning, plating, or painting, depending on the application requirements. These finishing touches ensure the part meets the required specifications.
Each step in the metal stamping process requires precision and expertise to ensure the final product meets the required specifications. This involves creating a precise die so that the part is formed perfectly.
Understanding the Stamping Press
The stamping press is the heart of the metal stamping operation. It’s a powerful machine that provides the force needed to shape the metal. Stamping presses can be mechanical or hydraulic, and they come in various sizes and tonnage capacities. A stamping press can be used to form a variety of shapes and sizes. This is a very powerful machine that is capable of applying a great deal of force.
Mechanical presses use a motor and flywheel to generate and store energy, which is then transferred to the punch. Hydraulic presses, on the other hand, use hydraulic pressure to apply force to the punch. The choice of press depends on factors such as the type of stamping operation, the material being stamped, and the required production speed.
Common Stamping Operations
Metal stamping encompasses a wide range of operations, including:
- Blanking: Cutting the sheet metal into a specific shape or outline.
- Piercing: Creating holes in the metal sheet.
- Bending: Forming the metal into a desired angle or curve.
- Coining: Creating a precise shape or pattern by squeezing the metal between the punch and die.
- Embossing: Creating a raised design on the surface of the metal. This is often used for decorative purposes or to add texture to a part.
- Drawing: Stretching the metal sheet to form a three-dimensional shape. This technique is commonly used in deep draw stamping.
These operations can be combined in various ways to create complex metal parts. Push Nut Fasteners, for example, might involve blanking, piercing, and bending operations. The process of metal stamping can be used to create very intricate and precise shapes.
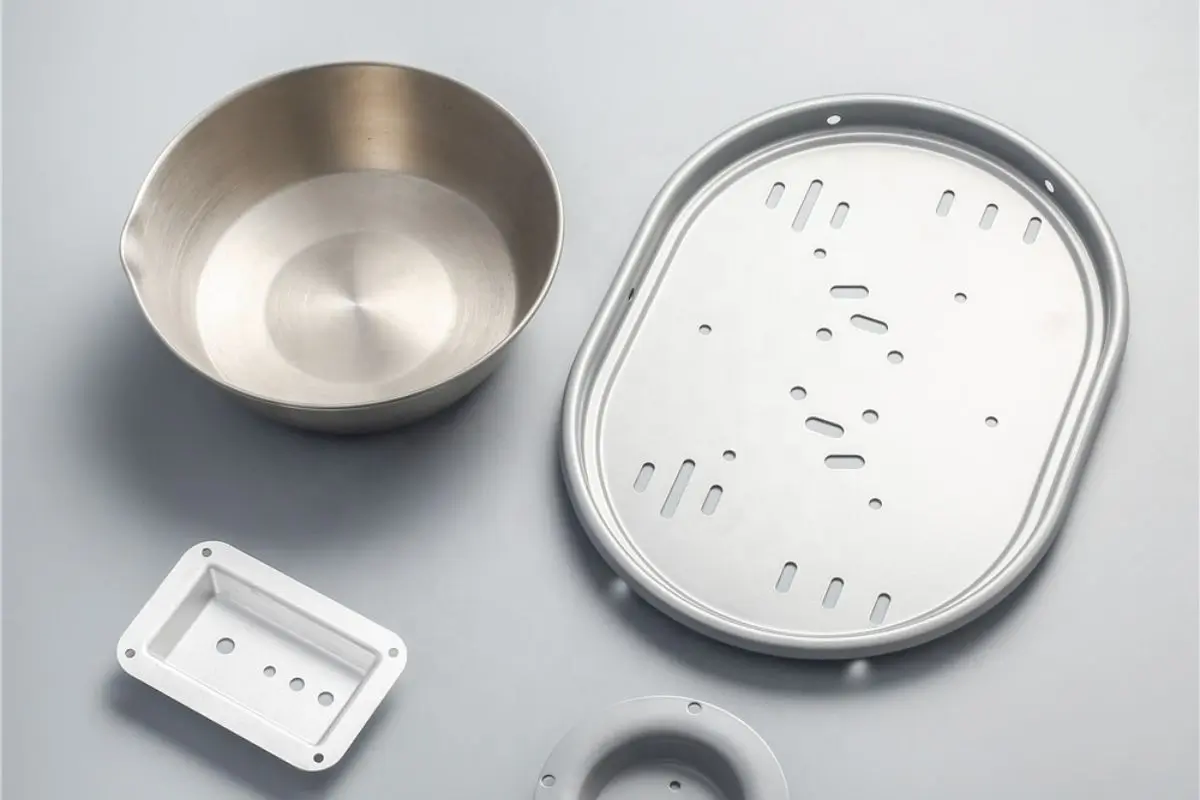
Advantages of Metal Stamping
Metal stamping offers several advantages over other manufacturing processes:
- High Precision: Metal stamping can produce parts with tight tolerances and intricate details.
- Cost-Effectiveness: It’s a cost-effective method, especially for high-volume production.
- Efficiency: Metal stamping is a fast and efficient process, capable of producing large quantities of parts quickly. The stamping process can be automated to increase efficiency.
- Material Versatility: A wide range of metals can be stamped, including steel, aluminum, copper, and brass. You can stamp a wide variety of metals, making it a versatile process.
- Durability: Stamped parts are typically strong and durable. The process of stamping creates durable and long-lasting parts.
These advantages make metal stamping a popular choice for manufacturing a wide range of products. For instance, Plumbing Fixture Stamping parts benefit from the durability and precision offered by this method. It’s ideal for creating a stamped part that will be used for a long time.
Applications of Metal Stamping
Metal stamping is used across a wide range of industries, including:
- Automotive: Body panels, brackets, and other structural components.
- Aerospace: Aircraft parts, engine components, and interior fittings.
- Electronics: Connectors, terminals, enclosures, and heat sinks. Custom Aluminum Heatsink production often utilizes metal stamping for its precision in creating complex shapes.
- Appliances: Housings, panels, and internal components for various appliances.
- Construction: Brackets, fasteners, and other building components.
These are just a few examples of the many applications of metal stamping. The versatility of this process makes it an essential part of modern manufacturing. The process of metal stamping can be used to create parts for a wide variety of applications.
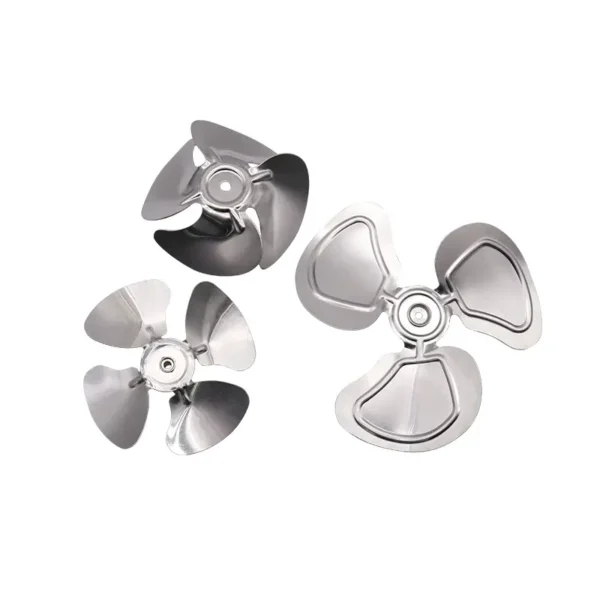
Key Takeaways: Metal Stamping 101
- Metal stamping is a versatile manufacturing process used to shape and cut metal into a wide range of components.
- Different types of metal stamping techniques exist, including progressive die stamping, transfer die stamping, deep draw stamping, and multi-slide stamping.
- The metal stamping process involves design, tool and die creation, material preparation, stamping, and finishing.
- Stamping presses provide the force needed to shape the metal, and they can be mechanical or hydraulic.
- Metal stamping offers advantages such as high precision, cost-effectiveness, efficiency, material versatility, and durability.
- Metal stamping is used across various industries, including automotive, aerospace, electronics, appliances, and construction.
By understanding the fundamentals of metal stamping, you can appreciate the complexity and precision involved in creating the countless metal objects that surround us. From the smallest electronic connector to the largest automotive body panel, metal stamping plays a vital role in shaping our modern world. Whether it’s for creating intricate designs like those found in Galvanizing Steel Metal Stamping Part or for mass-producing components, metal stamping remains a cornerstone of the manufacturing industry.