-
No.66 Gaojia, Xingfu Village, Sanqi Town, Yuyao, Ningbo,China
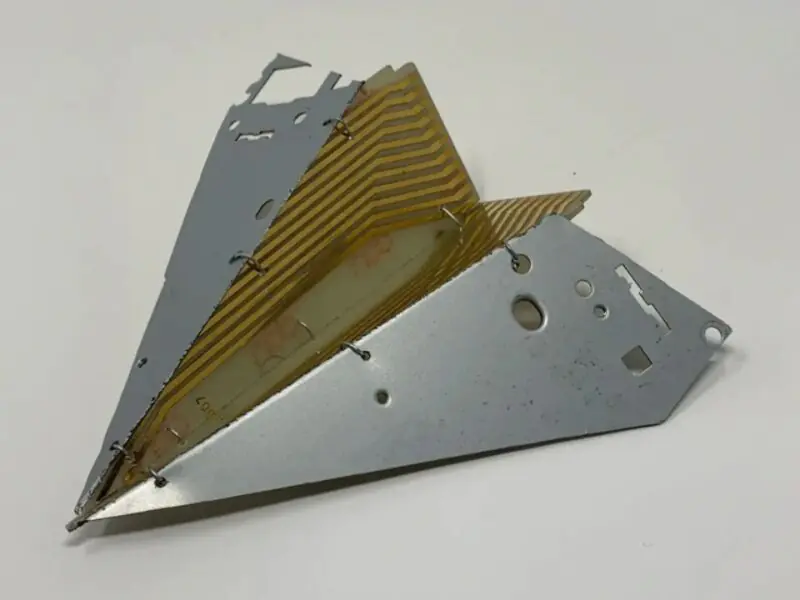
Metal Stamping Process: A Complete Guide to Advantages and Disadvantages in Manufacturing
Metal stamping is a crucial manufacturing process that shapes our modern world, from the cars we drive to the appliances in our homes. This comprehensive guide explores the benefits and limitations of metal stamping, helping manufacturers and buyers make informed decisions about their production needs. Whether you’re new to manufacturing or looking to optimize your current processes, this article will provide valuable insights into the world of metal stamping.
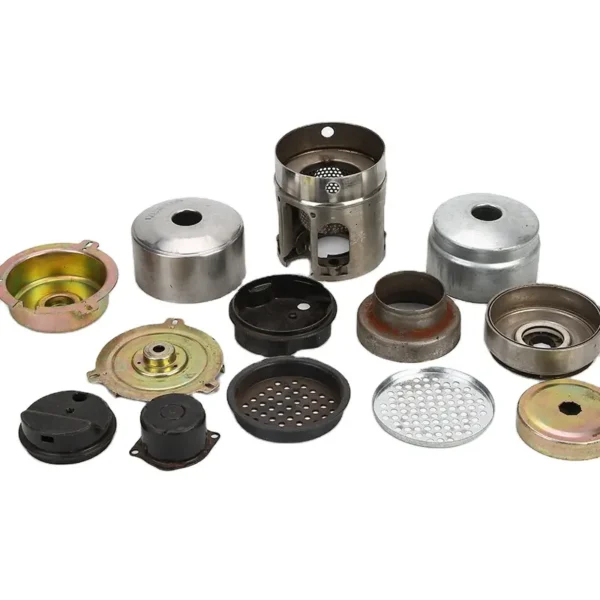
Advanced deep draw stamping components showcasing precision manufacturing capabilities
What is Metal Stamping and How Does it Work?
Metal stamping is a manufacturing process that uses specialized tools and dies to transform sheet metal into specific shapes. This process involves placing a metal blank into a stamping press, where tremendous force shapes the material into the desired form. The electrical connectors stamping process exemplifies how precise this technique can be for creating complex components.Modern stamping operations utilize various techniques, including:
- Progressive die stamping
- Transfer die stamping
- Four-slide stamping
- Deep draw stamping
What Are the Main Advantages of Metal Stamping?
Cost-Effectiveness in High-Volume Production
Metal stamping offers significant cost advantages, especially in high-volume production scenarios. Once the initial tooling is set up, the cost per unit decreases dramatically, making it an economical choice for large production runs.
Speed and Efficiency
The stamping process is remarkably efficient, with modern machinery capable of producing hundreds of parts per minute. This high-speed production capability makes sheet metal fabrication products particularly cost-effective for large-scale manufacturing needs.
What Are the Primary Disadvantages of Metal Stamping?
Initial Tooling Costs
One significant disadvantage is the high initial investment required for dies and tooling. These costs can range from several thousand to hundreds of thousands of dollars, depending on complexity.
Limited Flexibility
Once a die is created, it can only produce one specific part design. Any design changes require new tooling, which adds to costs and production time.
Types of Metal Stamping Processes
Different stamping processes serve various manufacturing needs:
- Progressive Die Stamping
- Multiple operations in sequence
- Ideal for high-volume production
- Continuous material feed
- Deep Draw Stamping
- Creates three-dimensional parts
- Suitable for containers and enclosures
- Complex forming capabilities
Industries That Rely on Metal Stamping
Metal stamping serves numerous industries, including:
Industry | Common Applications | Key Requirements |
---|---|---|
Automotive | Body panels, brackets | High precision, durability |
Electronics | Housings, connectors | Tight tolerances |
Aerospace | Structural components | Premium materials |
Consumer Goods | Appliance parts | Cost-effectiveness |
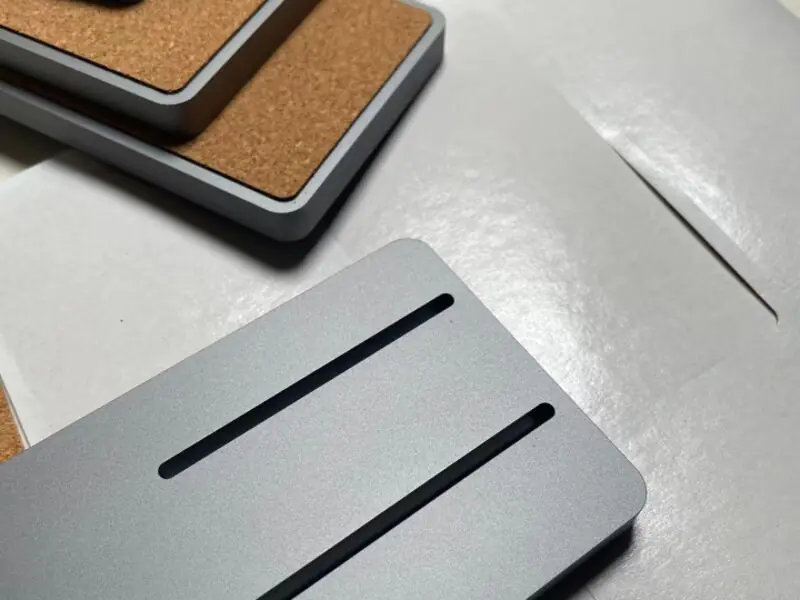
How to Choose the Right Metal Stamping Process?
Selecting the appropriate stamping process depends on several factors:
- Production volume requirements
- Part complexity
- Material specifications
- Budget constraints
- Quality standards
Future Trends in Metal Stamping Technology
The metal stamping industry continues to evolve with:
- Advanced automation systems
- Smart manufacturing integration
- Improved material utilization
- Enhanced quality control methods
Quality Considerations in Metal Stamping
Quality control in metal stamping involves:
- Precision Measurements
- Dimensional accuracy
- Surface finish
- Material properties
- Process Controls
- Tool wear monitoring
- Material feed consistency
- Press force optimization
Cost Analysis of Metal Stamping Projects
Understanding costs involves evaluating:
- Material expenses
- Tooling investments
- Labor requirements
- Production volume
- Secondary operations
Environmental Impact and Sustainability
Modern metal stamping emphasizes:
- Material waste reduction
- Energy efficiency
- Recyclable materials
- Sustainable practices
Key Takeaways: • Metal stamping offers excellent cost-effectiveness for high-volume production • Initial tooling costs can be significant but are offset by production efficiency • Different processes suit various manufacturing needs • Quality control is crucial for successful stamping operations • Environmental considerations are increasingly importantElectric cable copper stamping represents just one example of how versatile and precise modern metal stamping can be in creating specialized components for various industries.