-
No.66 Gaojia, Xingfu Village, Sanqi Town, Yuyao, Ningbo,China
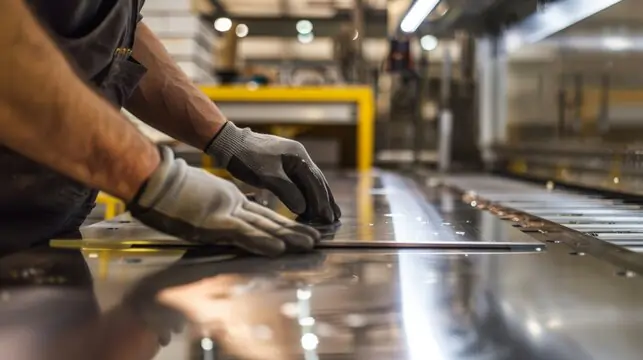
Metal Stamping vs. Casting vs. Die Casting: A Comprehensive Guide
Metal forming is essential for creating countless products we use every day. But with various methods available, choosing the right one can be tricky. This article dives deep into three popular techniques – metal stamping, casting, and die casting – to help you understand their differences, advantages, and ideal applications. Whether you’re an engineer, a product designer, or simply curious about manufacturing, you’ll find valuable insights here. Let’s explore the fascinating world of metal forming together!
What Exactly is Metal Stamping?
Metal stamping is a versatile manufacturing process that involves shaping flat metal sheet into desired forms using a stamping press and specialized tooling. Think of it like using cookie cutters, but with a lot more force and precision! The stamping process starts with a sheet of metal, either ferrous or non-ferrous, fed into a stamping press. The press is equipped with a tool, or die, that contains the desired shape. When the press closes, the tool forcefully cuts and shapes the metal. This process is also known as pressing. The force used can be hydraulic or mechanical, depending on the complexity and thickness of the metal. Metal stamping offers high precision, repeatability, and is ideal for high-volume production of parts with consistent wall thickness and intricate designs. For example, Power Cable Bundle Clamps are made using precise metal stamping, highlighting the method’s ability to produce detailed and consistent components.
One of the primary benefits of metal stamping is its ability to produce parts with high accuracy and excellent surface finish. Since the metal is shaped in a cold state, there’s minimal risk of warping or distortion. This makes stamping an excellent choice for applications where tight tolerances are required. The stamping process also allows for the creation of complex shapes, including bends, flanges, and embossed features. Furthermore, metal stamping is highly efficient for large production runs because once the tool is set up, the process can be automated to produce a large quantity of parts quickly.
However, metal stamping is not without its limitations. The initial cost of the tool and die can be significant, especially for complex parts. Also, while stamping is great for producing parts with uniform thickness, it may not be suitable for parts that require significant variations in thickness or intricate internal geometries. Finally, the stamping process can generate a large amount of scrap material, particularly when creating parts with complex cutouts or irregular shapes, although much of this scrap can be recycled.
Understanding the Casting Process: An Overview
Casting, also known as metal casting, is one of the oldest manufacturing processes, dating back thousands of years. Unlike stamping, which shapes solid metal sheet, casting involves melting the metal and pouring it into a mold cavity that corresponds to the desired shape. Once the molten metal cools and solidifies, the mold is removed, revealing the cast part. The casting process allows for the creation of complex shapes and is suitable for a wide range of metal parts and components. There are several variations of the casting process, including sand casting, investment casting, and die casting, each with its own advantages and disadvantages. For instance, the process for creating a Support Stand Base (Cast Iron) 14.75 in (375 mm) highlights the versatility of casting in producing robust and complex forms.
The choice of casting process depends on several factors, including the type of metal, the complexity of the part, the required surface finish, and the production volume. Sand casting, for example, is a versatile and relatively low-cost process that uses sand molds, making it suitable for large parts and low to medium production volumes. Investment casting, on the other hand, uses a ceramic mold created from a wax pattern, allowing for very intricate details and excellent surface finish. This process is often used for high-precision parts, such as those used in the aerospace and medical industries. The casting process utilizes both ferrous and non-ferrous materials.
A significant advantage of casting is its ability to create parts with complex internal geometries and varying wall thicknesses that would be difficult or impossible to achieve with stamping. Furthermore, casting can accommodate a wide range of metal alloys, including those with high melting points that are not easily formed by other processes. However, casting might result in lower dimensional accuracy and a rougher surface finish compared to stamping or die casting. Casting also tends to be more labor-intensive and may require additional machining or finishing operations to achieve the desired tolerances and surface quality. Porosity can sometimes be an issue with cast metal.
Delving into Die Casting: Precision and Efficiency
Die casting is a specialized casting process that utilizes a reusable mold, or die, to produce metal parts. In the die casting process, molten metal is injected into the die cavity under high pressure. This pressure ensures that the molten metal fills the entire cavity and produces a part with fine details and a smooth surface finish. The die is typically made of hardened steel and can withstand multiple casting cycles. The die-casting machine precisely controls the injection speed, pressure, and cooling rate to ensure consistent part quality. The die-casting produces high-volume, intricate metal parts.
One of the key advantages of die casting is its ability to produce parts with excellent dimensional accuracy and a superior surface finish. The high pressure injection ensures that the molten metal fills every corner of the die, resulting in parts with sharp edges and intricate details. Die casting is also highly efficient for high-volume production, as the rapid injection and cooling cycles allow for a high production rate. Furthermore, die casting produces parts with good mechanical properties, as the rapid solidification results in a fine-grained microstructure.
However, die casting also has some limitations. The initial cost of the die is high, making it economical only for large production runs. Also, die casting is primarily suited for non-ferrous metals with low melting points, such as aluminum, zinc, and magnesium alloys. Ferrous metals, like steel, require specialized die materials and higher injection pressures, which can increase the cost and complexity of the process. Finally, the size and weight of die-cast parts are limited by the capacity of the die casting machine. Parts that take a long time to cool down may not be suitable for this process.
Casting vs. Stamping: A Detailed Comparison
When deciding between casting and stamping, several factors need to be considered. Here’s a breakdown to help you make the right choice:
Feature | Casting | Stamping |
---|---|---|
Metal Form | Molten | Solid Sheet |
Part Complexity | High (intricate internal geometries) | Moderate (uniform thickness) |
Dimensional Accuracy | Lower | Higher |
Surface Finish | Rougher (may require finishing) | Smoother |
Production Volume | Low to high (depending on the process) | High (especially for large runs) |
Tooling Cost | Lower for sand casting, higher for die casting | High for complex dies |
Material Range | Wide (including high melting point alloys) | Primarily ductile metals |
Lead Time | Longer | Shorter |
Cost per Part | Lower for high volume, higher for small runs | Lower for large volume, higher for small runs |
Casting is generally preferred for parts with complex shapes, internal cavities, or varying wall thicknesses. The molten metal can flow into intricate mold shapes, allowing for designs that would be difficult or impossible to achieve with stamping. On the other hand, stamping is better suited for parts that require high dimensional accuracy, excellent surface finish, and are produced in large volumes. The cold-working nature of stamping ensures consistent part quality and minimizes the need for secondary finishing operations. Telecom Brackets exemplify parts ideally suited for metal stamping due to their need for uniformity and precise dimensions in high-volume production.
For example, engine blocks, pump housings, and intricate sculptures are often produced by casting, while automotive body panels, brackets, and electrical connectors are typically manufactured by stamping. The choice also depends on the type of metal, required production volume, and overall project budget. Casting involves a foundry for large cast metal parts. Casting is also a cost effective way to create a steel part.
Die Casting vs. Stamping: When to Choose Which?
Die casting and stamping are both high-volume manufacturing processes, but they have distinct advantages and disadvantages. Here’s a comparison:
Feature | Die Casting | Stamping |
---|---|---|
Metal Form | Molten | Solid Sheet |
Part Complexity | High (intricate details, thin walls) | Moderate (uniform thickness) |
Dimensional Accuracy | Excellent | High |
Surface Finish | Excellent | Smooth |
Production Volume | Very high | High |
Tooling Cost | Very high | High |
Material Range | Primarily non-ferrous metals (Al, Zn, Mg) | Ductile metals, ferrous and non-ferrous |
Lead Time | Longer | Shorter |
Cost per Part | Low for very high volume | Low for high volume |
Die casting excels at producing parts with intricate details, thin walls, and excellent surface finish. The high-pressure injection ensures that the molten metal fills the die cavity completely, resulting in parts with sharp features and tight tolerances. Die casting is ideal for applications where aesthetics and precision are critical, such as automotive components, electronic housings, and consumer products. It’s a very cost-effective manufacturing process for high volumes, often used for automotive and aerospace parts. The lower cost is due to the automation and high-volume capabilities.
Stamping, on the other hand, is more versatile in terms of material selection and part size. It can handle both ferrous and non-ferrous materials and is suitable for a wider range of part geometries. While stamping may not achieve the same level of intricate detail as die casting, it offers excellent dimensional accuracy and is highly efficient for large production runs. Stamping is often preferred for parts that require high strength, ductility, and structural integrity. The choice between die casting and stamping is dictated by factors like the alloy used, desired precision, production volume, and cost considerations.
As an example, a delicate heat sink with numerous fins and thin walls would be best produced by die casting, while a structural bracket with mounting holes and bends would be more suited for stamping. Both require different machinery and tooling, the die-casting machine and the stamping press and related tooling components. It’s also important to consider the material costs, as die-cast alloys are often more expensive than sheet metal.
Die Casting vs. Casting: Exploring the Nuances
While both die casting and general casting involve pouring molten metal into a mold, there are significant differences between the two processes:
Feature | Die Casting | Casting (e.g., Sand Casting) |
---|---|---|
Mold Type | Reusable steel die | Expendable mold (e.g., sand, ceramic) |
Pressure | High pressure injection | Gravity or low pressure |
Dimensional Accuracy | Excellent | Lower |
Surface Finish | Excellent | Rougher |
Production Volume | Very high | Low to medium |
Tooling Cost | Very high | Lower |
Part Complexity | High (thin walls, intricate details) | High (complex internal geometries) |
Material Range | Primarily non-ferrous metals | Wide range (ferrous and non-ferrous) |
Lead Time | Shorter (once die is made) | Longer |
Cost per Part | Low for very high volume | Higher for small runs, lower for large runs |
Die casting, with its reusable steel die and high-pressure injection, offers superior dimensional accuracy, surface finish, and production rates. Die casting utilizes specialized machines for injecting molten metal into a die under high pressure, which requires a specific type of metal. The rapid cooling rate also results in parts with excellent mechanical properties. However, the high cost of the die limits its use to high-volume production. Die casting produces parts that have a high level of repeatability. This is an important aspect in manufacturing, which die casting has over other casting methods.
General casting processes, such as sand casting and investment casting, utilize expendable molds and lower pressures. This allows for greater flexibility in part size and complexity, as well as the ability to cast a wider range of materials, including ferrous alloys with high melting points. The lower tooling costs make casting suitable for smaller production runs and prototype parts. However, the dimensional accuracy and surface finish are generally lower than those achieved with die casting, and additional machining or finishing operations may be required. The casting are two different processes suitable for different tasks. Casting allows the manufacturer to produce larger parts. Also, you have a wider selection of metal when using a casting process.
The choice between die casting and general casting depends on the specific requirements of the application. If high precision, excellent surface finish, and high-volume production are needed, die casting is the preferred choice. If complex internal geometries, a wide range of materials, or lower production volumes are required, then general casting may be more suitable. Also, consider the cost of the dies, as higher precision molds translate to a higher cost of production. Die components have to be more durable and made of stronger metal and alloys. This increases the cost of dies.
Stamped Steel vs. Cast Metal: A Strength and Durability Perspective
Stamped steel and cast metal exhibit different mechanical properties due to their distinct manufacturing processes and resulting microstructures.
Stamped steel, being cold-worked, generally possesses higher strength and ductility compared to cast metal. The cold-working process introduces strain hardening, which increases the yield and tensile strength of the material. Stamped steel parts also tend to have a more uniform microstructure, which contributes to their consistent mechanical properties. The ability to control the grain flow during the stamping process further enhances the strength and fatigue resistance of stamped steel components. Stamped Chassis Brackets showcase the strength and durability achievable through metal stamping, making them ideal for demanding applications. Steel Stamping has a strong advantage when it comes to cost and speed.
Cast metal, on the other hand, can exhibit varying mechanical properties depending on the casting process and the alloy used. Sand-cast parts, for example, may have lower strength and ductility due to their coarser grain structure and potential for porosity. However, investment-cast parts and die-cast parts can achieve mechanical properties comparable to or even exceeding those of stamped steel, especially when using high-strength alloys. The microstructure of cast metal is also more isotropic, meaning it has uniform properties in all directions, which can be beneficial in certain applications. The molten metal is often used with various alloys in order to enhance the physical properties of the cast part.
In general, if high strength and ductility are primary concerns, stamped steel is often the preferred choice. However, cast metal offers greater flexibility in terms of alloy selection and the ability to create complex shapes with varying wall thicknesses. The final decision depends on the specific application requirements, including load-bearing capacity, impact resistance, and fatigue life.
The Role of Molds and Dies in Metal Forming
Molds and dies are essential tooling components in both casting and stamping processes. However, their function and construction differ significantly.
In casting, a mold is a cavity that defines the external shape of the part. Molds can be permanent, as in die casting, or expendable, as in sand casting and investment casting. The mold must be able to withstand the temperature and pressure of the molten metal and allow for easy removal of the solidified part. The design of the mold must also account for shrinkage of the metal during solidification and include features such as gates, risers, and vents to ensure proper filling and minimize defects. Some casting dies require a heating and cooling process to increase manufacturing times. The die surface has to be lubricated in order to prevent damage to the die.
In stamping, a die is a set of tools that cuts, shapes, and forms the flat metal sheet. A die typically consists of a punch and a die block, which work together to create the desired shape. Dies can be simple, for basic blanking and piercing operations, or complex, for multi-stage forming operations. The design of the die must account for the material thickness, springback, and the desired tolerances of the finished part. Die require careful maintenance to ensure that they continue to produce parts to the required specifications. Tool and die makers play an important role in the manufacturing process.
The quality and precision of the mold or die directly impact the quality of the final part. Poorly designed or manufactured molds and dies can lead to defects, dimensional inaccuracies, and poor surface finish. Therefore, significant investment is made in the design and fabrication of these tooling components. The cost of the dies can be a major factor in the overall cost of the manufacturing process, especially for complex parts or high-volume production. The cost of the die is one of the driving factors in deciding the process. Tooling costs are an important factor to keep in mind when deciding on which manufacturing process to utilize.
Material Selection: Choosing the Right Metal for the Job
The choice of material is crucial in both casting and stamping processes. Different metals and alloys have varying properties, such as strength, ductility, melting point, and corrosion resistance, which affect the suitability of the material for a particular application. The selection of the type of metal and its physical properties is an important aspect of manufacturing.
For casting, a wide range of ferrous and non-ferrous alloys can be used. Ferrous alloys, such as cast iron and steel, are known for their high strength and wear resistance, making them suitable for structural components, engine blocks,and gears. Non-ferrous alloys, such as aluminum, zinc, and magnesium, offer advantages such as lightweight, good corrosion resistance, and excellent castability, making them suitable for applications like automotive parts, electronic housings, and consumer products. Casting utilizes different types of metal and can use ferrous and non-ferrous metals. Molten metal is injected into a mold and allowed to cool. The casting allows the manufacturer to produce very complex parts that can’t be made using other methods. Casting involves pouring molten metal into a mold.
For stamping, the material choice is primarily limited to ductile metals that can be easily formed into complex shapes without cracking or tearing. Common stamping materials include steel, aluminum, copper, and brass. Steel is often chosen for its high strength, while aluminum offers a good balance of strength and lightweight. Copper and brass are favored for their electrical conductivity and corrosion resistance. High-strength steel alloys are often used for automotive components, while aluminum alloys are commonly used for electronic enclosures and consumer products. Stamping often utilizes a metal sheet of steel or aluminum, the sheet of metal is then formed using a stamping press. Stamping is a very efficient process for large production runs, and is a popular manufacturing process for various industries. Different metal types can be used in the stamping process.
The choice of material depends on several factors, including the intended application, required mechanical properties, corrosion resistance, and cost. For instance, if high strength and wear resistance are required, a ferrous alloy like steel would be a good choice for casting. If lightweight and corrosion resistance are priorities, then a non-ferrous alloy like aluminum would be more suitable. For stamping, the material must be ductile enough to undergo the forming process without cracking. Also, stamping creates metal parts with very dimensional stability. Stamping and die casting are usually chosen when production runs are expected to be higher than usual. Stamped steel parts are often used in automotive and construction applications. Cast steel parts are also used in the automotive industry.
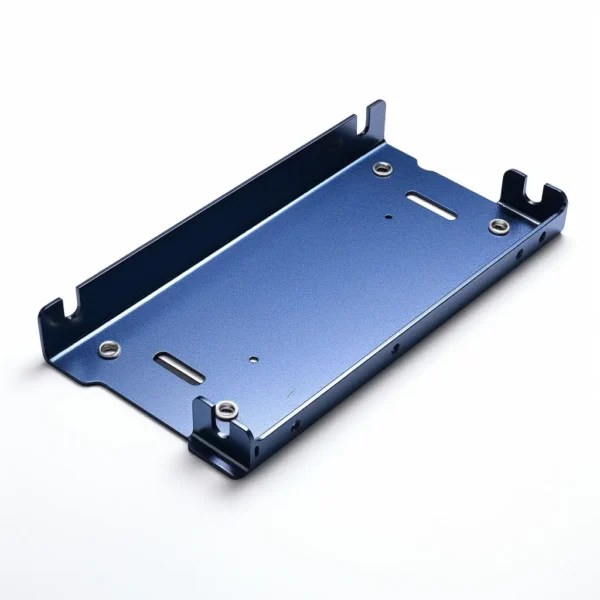
Cost Considerations in Metal Forming
Cost is a critical factor in any manufacturing process, and both casting and stamping have their own cost structures. The overall cost of a part depends on several factors, including material cost, tooling cost, labor cost, and overhead.
In casting, the material cost is directly proportional to the weight of the part and the cost of the alloy used. Tooling costs for sand casting are relatively low, as sand molds are expendable. However, tooling costs for die casting are significantly higher, as permanent steel dies are expensive to design and manufacture. Labor costs can vary depending on the level of automation and the complexity of the process. Sand casting often involves more manual labor than die casting, which can be highly automated. Die casting uses a die-casting machine which injects molten metal into a permanent die. The die is typically made of hardened steel and is a significant cost factor. Casting is also used in conjunction with die casting for some applications. For very large parts that require a quick cooling time, sand casting can be used. Casting dies for sand casting can be very cost-effective. Sand casting is often used for small production runs.
In stamping, the material cost is determined by the area of the sheet metal used and the cost of the material. Tooling costs can be high for complex dies, but the cost per part decreases with increasing production volume. Labor costs in stamping are generally lower than in casting, as the process is highly automated. Stamping is a cold forming process that creates metal parts from a sheet metal blank. The blank is placed between two dies and then a hydraulic press forms the metal into shape. Stamping allows for complex shapes and high tolerances and dimensional stability. The tooling costs can be very high but the unit cost of production is low and makes it a cost-effective solution for high-volume production.
For both casting and stamping, overhead costs include factors such as facility rent, utilities, and equipment maintenance. The production volume plays a significant role in the overall cost per part. For high-volume production, the tooling cost is amortized over a large number of parts, resulting in a lower cost per part. For low-volume production, the tooling cost has a greater impact on the overall cost per part. When manufacturing high-volume parts using the die casting method, the dies must be carefully designed to minimize the wear and tear on the die surface.
Emerging Trends in Metal Forming
The field of metal forming is continuously evolving, with new technologies and techniques emerging to improve efficiency, precision, and sustainability.
Additive manufacturing, also known as 3D printing, is increasingly being used for creating complex metal parts directly from digital designs. This technology allows for rapid prototyping and the production of intricate shapes that would be difficult or impossible to achieve with traditional casting or stamping methods.
Hybrid manufacturing processes, which combine additive and subtractive techniques, are also gaining traction. These processes offer greater flexibility and allow for the creation of parts with intricate internal features and complex external geometries.
Furthermore, there’s a growing emphasis on sustainable manufacturing practices. This includes using recycled materials, reducing energy consumption, and minimizing waste. New techniques such as near-net-shape casting and precision stamping are being developed to reduce the need for secondary machining operations and minimize material waste.
Key Takeaways: Choosing the Right Metal Forming Process
- Metal stamping is ideal for high-volume production of parts with uniform thickness and precise dimensions.
- Casting is versatile for creating complex shapes with varying wall thicknesses but may require additional finishing.
- Die casting produces high-precision parts with excellent surface finish but is typically limited to non-ferrous metals and high volumes.
- Material selection depends on the desired mechanical properties, corrosion resistance, and cost.
- Tooling costs are a major factor in the overall cost of the manufacturing process.
- Emerging trends like additive manufacturing and hybrid processes are shaping the future of metal forming.
For inquiries regarding your specific metal forming needs, consider reaching out to a company with extensive experience, such as Metal Stamp Master, which boasts 30 years of experience. They can provide expert advice and customized solutions for your projects.