-
No.66 Gaojia, Xingfu Village, Sanqi Town, Yuyao, Ningbo,China
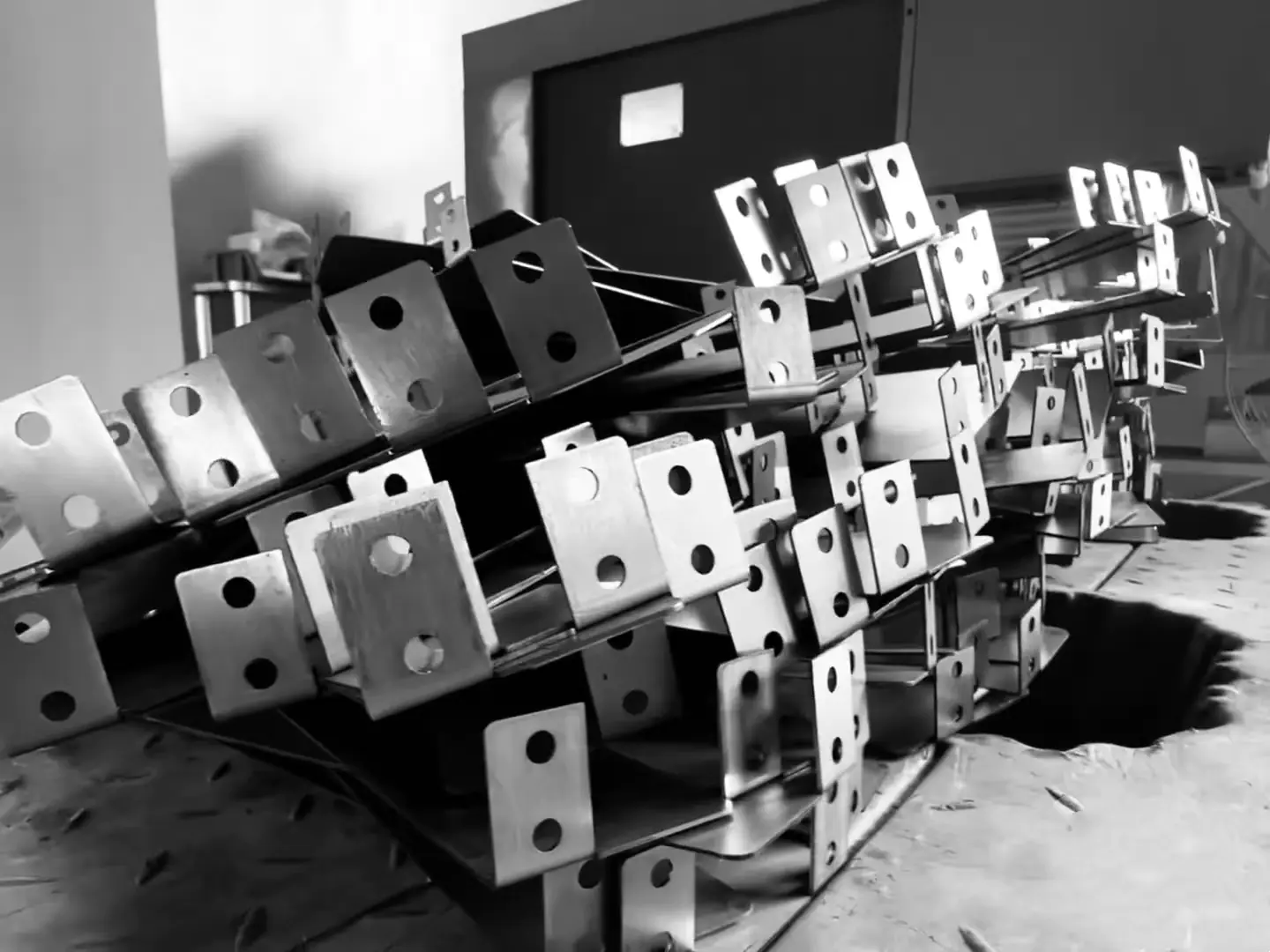
Metal Stamping vs Die Casting: A Comprehensive Comparison Guide for Manufacturers
Understanding the differences between metal stamping and die casting is crucial for making informed manufacturing decisions. This detailed guide explores the unique characteristics, advantages, and optimal applications of both processes to help you choose the right method for your specific needs.
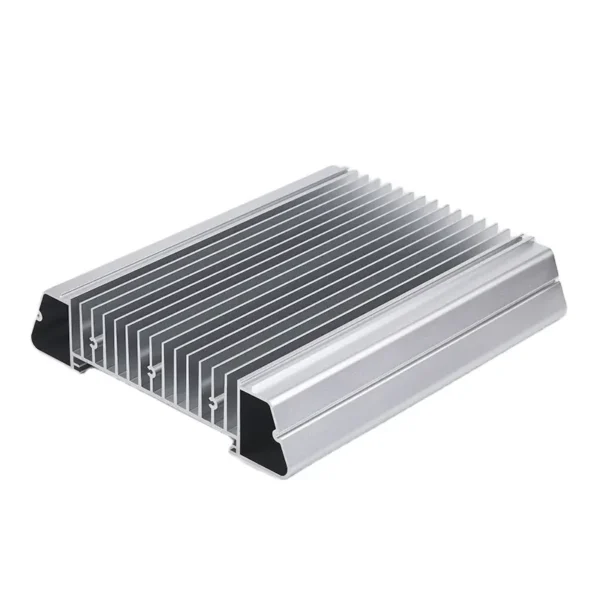
Custom aluminum heatsink showing precision manufacturing capabilities
What Are the Fundamental Differences Between Metal Stamping and Die Casting?
Metal stamping involves shaping flat metal sheets through mechanical force, while die casting utilizes molten metal injected into molds. The key differences include:
Characteristic | Metal Stamping | Die Casting |
---|---|---|
Material State | Solid sheet metal | Molten metal |
Process Type | Cold forming | Hot forming |
Material Options | Both ferrous and non-ferrous | Primarily non-ferrous |
Production Speed | Faster | Moderate |
Learn more about metal stamping processes
How Do Manufacturing Costs Compare?
The cost structure varies significantly between these processes:
Metal Stamping Costs:
- Lower initial tooling costs
- Higher material efficiency
- Cost-effective for high volumes
- Lower energy consumption
Die Casting Costs:
- Higher tooling investments
- More complex setup requirements
- Higher energy usage
- Better for complex geometries
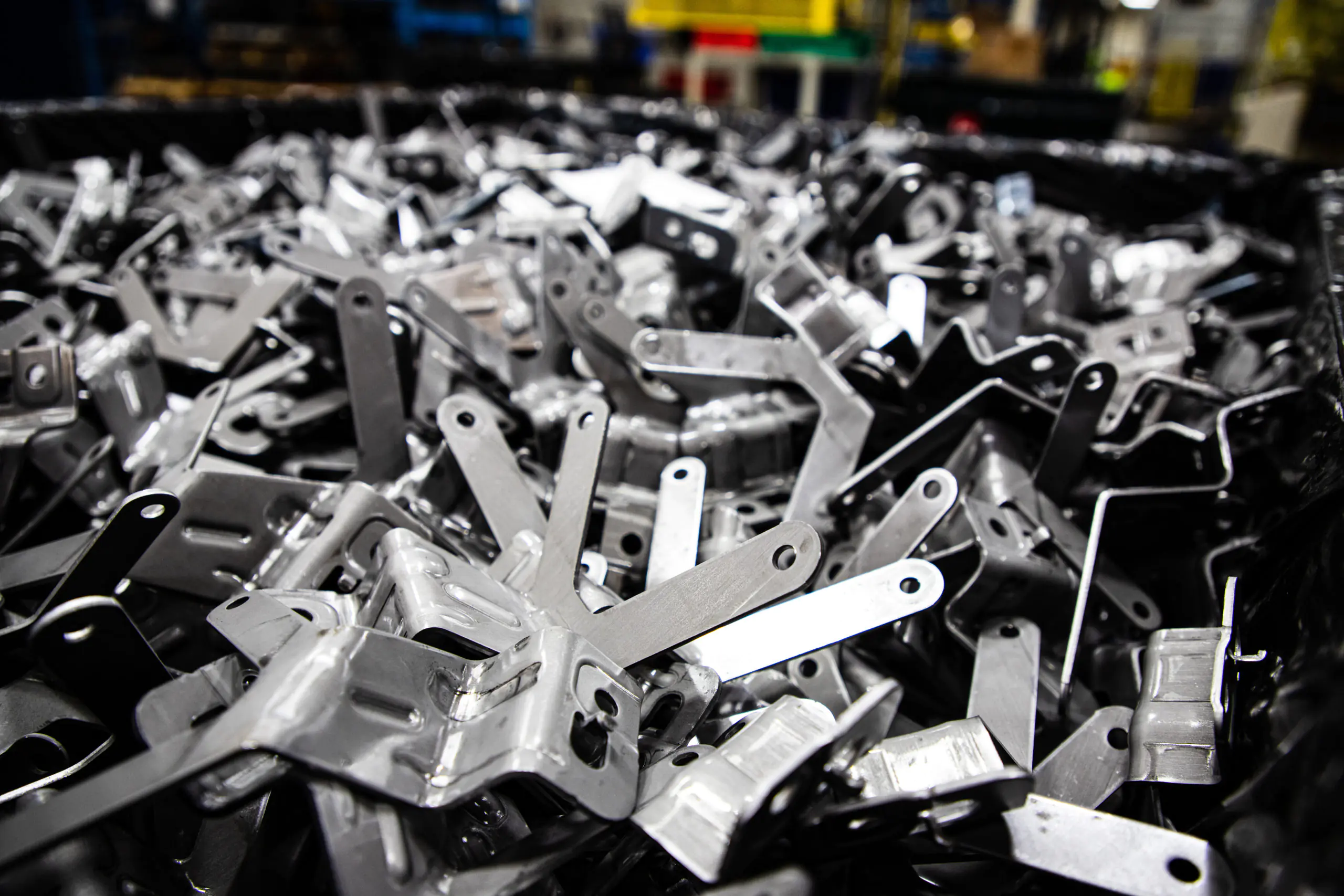
What Are the Material Considerations?
Material selection plays a crucial role in both processes:
Metal Stamping Materials:
- Steel
- Aluminum
- Copper
- Brass
- Various sheet metal options
Die Casting Materials:
- Aluminum alloys
- Zinc
- Magnesium
- Non-ferrous metals
Which Process Offers Better Quality and Precision?
Both processes can achieve high quality, but their strengths differ:Metal Stamping:
- Excellent dimensional accuracy
- Consistent part reproduction
- Superior surface finish
- Precise component manufacturing
Die Casting:
- Complex internal features
- Thin wall capabilities
- Excellent detail reproduction
- Smooth surface finish
What Are the Production Volume Considerations?
Understanding production volumes is essential:
High Volume Production:
- Metal stamping is ideal for large runs
- Lower per-piece costs
- Faster cycle times
- Automated processes
Medium to Low Volume:
- Die casting may be more economical
- Better for complex parts
- More flexible design options
- Lower tooling wear
How Does Design Complexity Impact Process Selection?
Design requirements influence process choice:
Simple Designs:
- Metal stamping excels
- Lower tooling costs
- Faster production
- Less material waste
Complex Designs:
- Die casting preferred
- Better internal features
- More design freedom
- Superior strength
What Industries Benefit Most from Each Process?
Different industries favor specific processes:
Metal Stamping Industries:
- Automotive components
- Electronics
- Telecommunications
- Appliance manufacturing
Die Casting Industries:
- Aerospace
- Consumer goods
- Medical devices
- Automotive powertrain
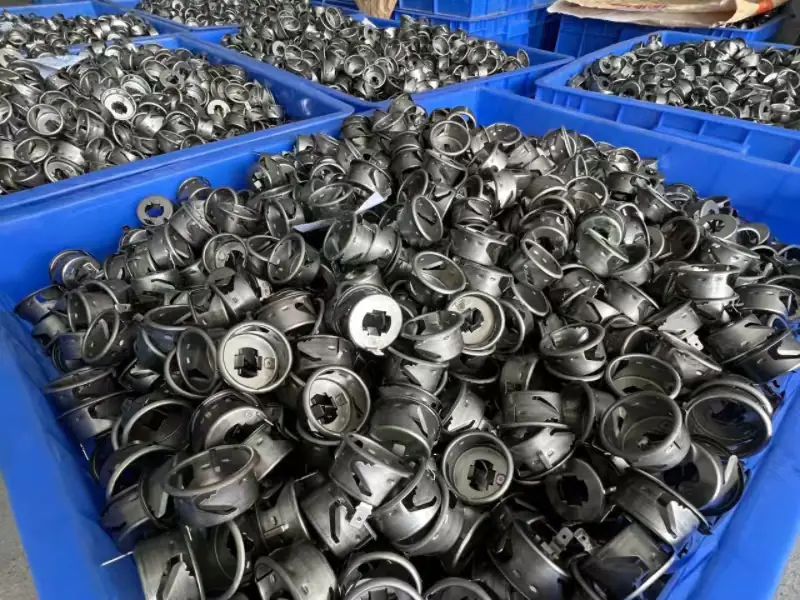
Key Takeaways:
• Choose metal stamping for:
- High-volume production
- Simple to moderate designs
- Cost-effective manufacturing
- Quick turnaround times
• Select die casting for:
- Complex geometries
- Internal features
- Strength requirements
- Non-ferrous applications
• Consider factors like:
- Production volume
- Material requirements
- Design complexity
- Cost constraints
Remember these points when selecting between metal stamping and die casting for your manufacturing needs.