-
No.66 Gaojia, Xingfu Village, Sanqi Town, Yuyao, Ningbo,China
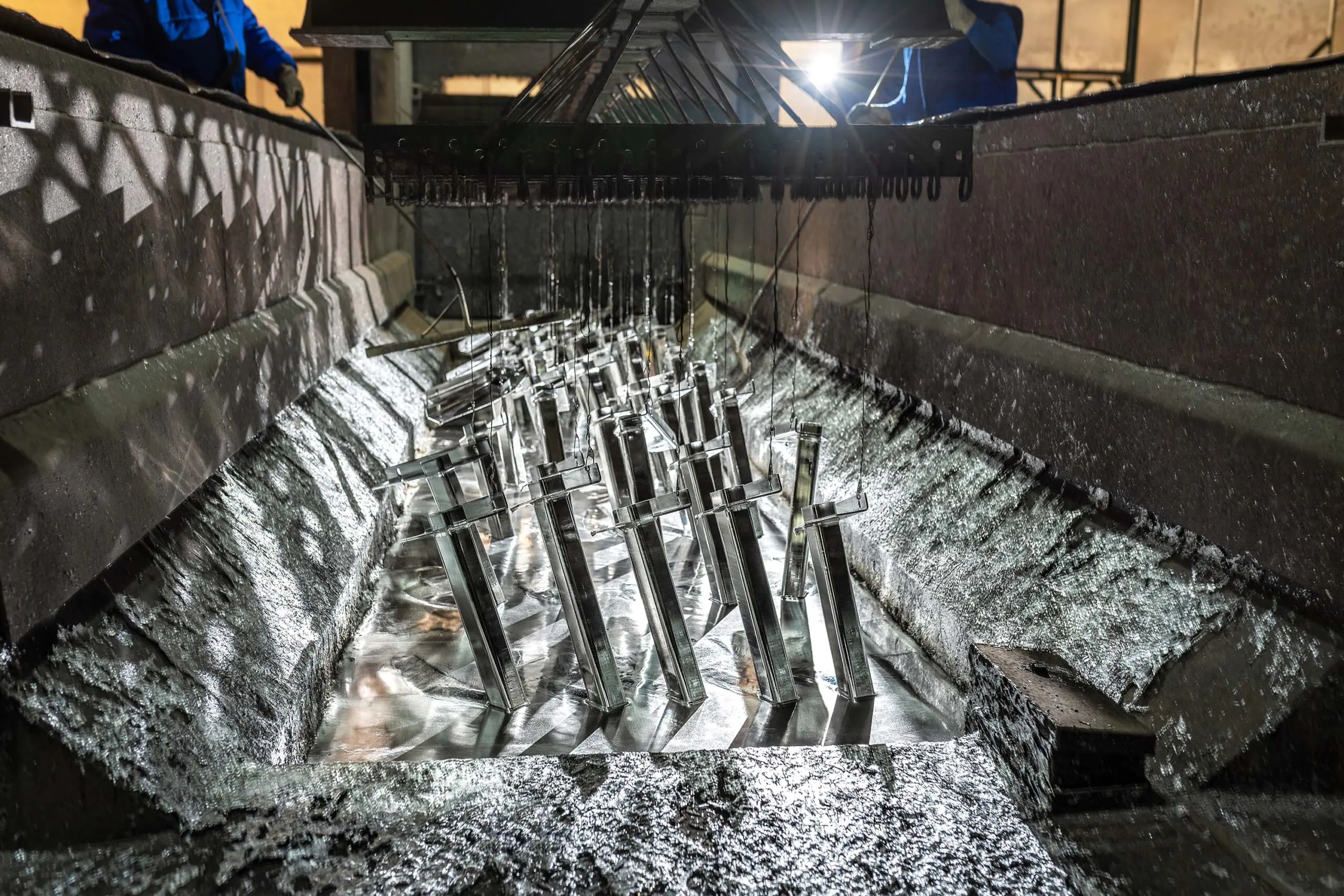
Precision Metal Plating: Essential Guide for Stamped Parts Manufacturing
Metal plating plays a vital role in enhancing the performance, durability, and appearance of stamped metal parts. This comprehensive guide explores various plating processes, their applications, and why they’re crucial for precision metal stamping. Whether you’re a manufacturer or buyer, understanding metal plating can help you make informed decisions about your stamped components.
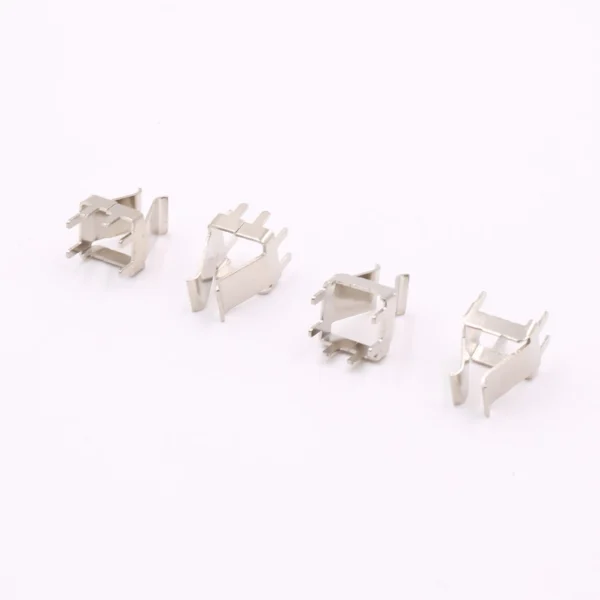
What is Metal Plating and Why is it Important?
Metal plating is a process that deposits a thin layer of metal onto another parent metal to improve its properties. This critical manufacturing step:
- Enhances corrosion resistance
- Improves wear resistance
- Increases conductivity
- Provides aesthetic appeal
Metal stamping components often require plating to meet specific performance requirements and industry standards.
What Are the Different Types of Metal Plating?
Several plating methods are available for stamped parts:
Plating Type | Primary Benefits | Common Applications |
---|---|---|
Zinc Plating | Corrosion resistance | Automotive parts |
Nickel Plating | Wear resistance | Electronic components |
Gold Plating | Conductivity | Electrical contacts |
Chrome Plating | Aesthetics & durability | Decorative finishes |
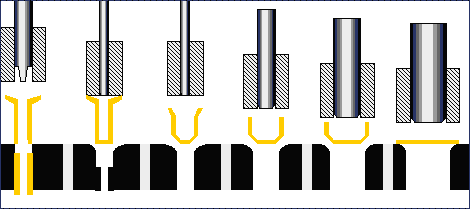
How Does the Metal Plating Process Work?
The plating process typically involves:
- Surface preparation
- Cleaning and activation
- Immersion in electrolytic plating solution
- Post-plating treatment
- Quality inspection
Custom stamping parts often undergo specialized plating processes to meet specific requirements.
Which Plating Method is Best for Precision Stamped Parts?
The choice of plating method depends on several factors:
- Part geometry
- Base material
- Performance requirements
- Cost considerations
- Production volume
What Role Does Barrel Plating Play in Metal Stamping?
Barrel plating is particularly effective for:
- High-volume production
- Small parts processing
- Cost-effective finishing
- Uniform coating application
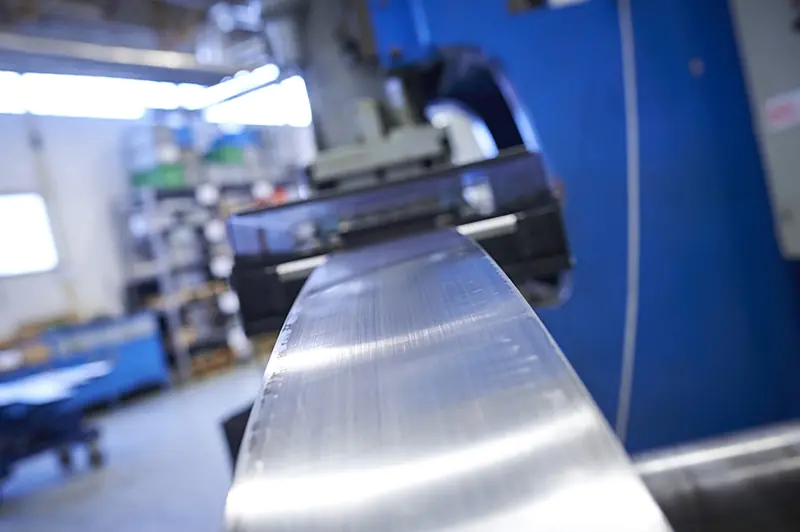
How Does Rack Plating Compare to Other Methods?
Rack plating offers several advantages:
- Better control over plating thickness
- Ideal for complex geometries
- Superior finish quality
- Suitable for delicate parts
Electrical connectors stamping often requires precise rack plating for optimal performance.
What Are the Latest Trends in Metal Plating Technology?
Modern plating innovations include:
- Environmentally friendly processes
- Automated plating systems
- Advanced quality control
- Smart coating solutions
How to Choose the Right Plating Process?
Consider these factors:
- Part specifications
- Performance requirements
- Production volume
- Budget constraints
- Environmental regulations
What Quality Control Measures Are Essential?
Key quality control aspects include:
- Thickness testing
- Adhesion testing
- Corrosion resistance testing
- Visual inspection
- Documentation
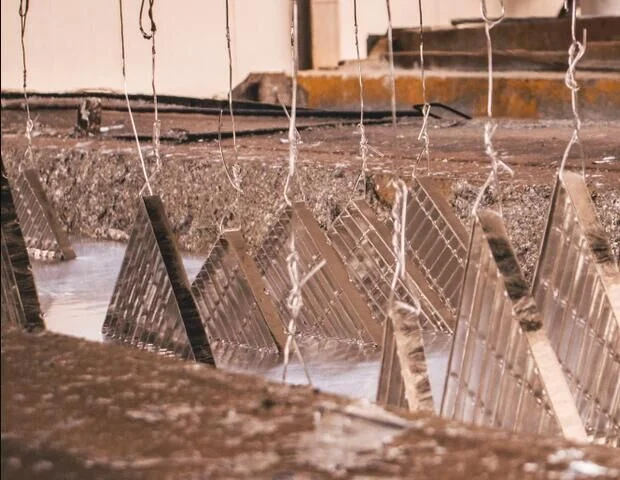
What Are Common Plating Challenges and Solutions?
Challenges often include:
- Uneven coating
- Poor adhesion
- Contamination issues
- Environmental compliance
Key Takeaways:
- Choose plating methods based on specific application needs
- Consider both technical requirements and cost factors
- Implement robust quality control measures
- Stay compliant with environmental regulations
- Work with experienced plating providers
- Regular maintenance ensures optimal results
Remember that successful metal plating requires careful attention to detail and proper process control throughout the manufacturing cycle.