-
No.66 Gaojia, Xingfu Village, Sanqi Town, Yuyao, Ningbo,China
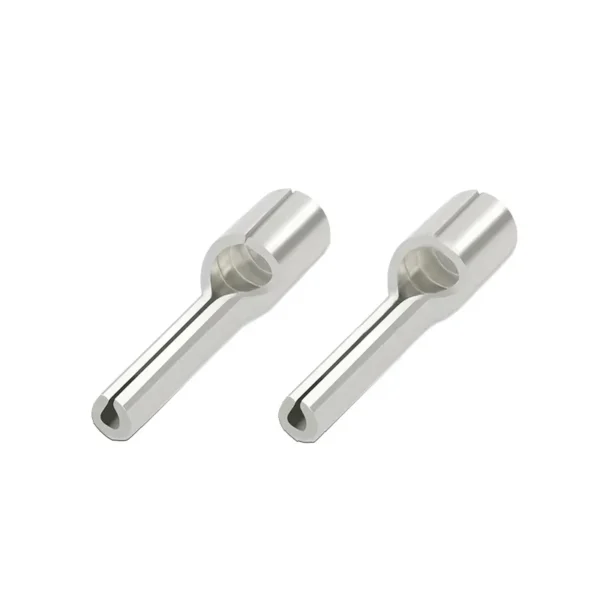
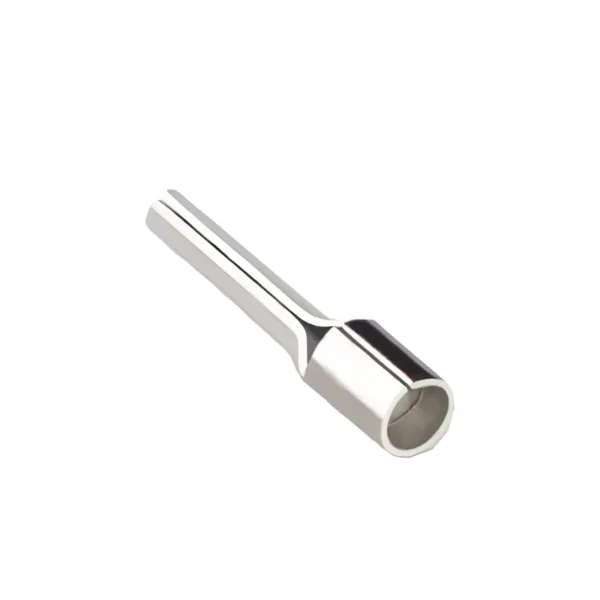

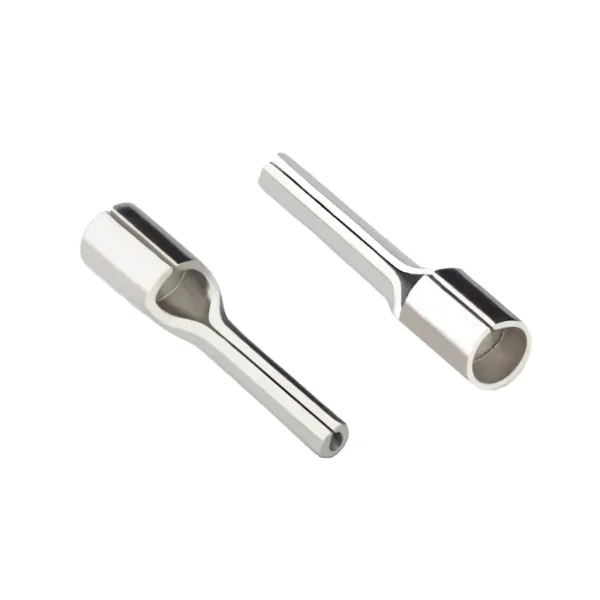
cold-pressed terminal stamping
Type Mold development/Stamp sheet metal/deep drawing/ cnc
Tolerance 0.003 mm – 0.01 mm
Quality control 100% full inspection
Color and Surface treatment Custom Color/anodizing/polishing/plating/painting/Coating
Material Anti rust/strong strength/cost competitive
Drawing Formats STEP, DWG,PDF
Feature Anti rust/strong strength/cost competitive
MOQ Support Small Batch
High-Precision Cold-Pressed Terminal Stamping: Revolutionizing Electrical Connections
Cold-pressed terminal stamping represents a cutting-edge approach to manufacturing electrical connectors, offering unparalleled precision and reliability. These stamped terminals are essential components in various industries, from automotive to consumer electronics, providing secure and efficient electrical connections. In this comprehensive guide, we’ll explore the benefits, applications, and manufacturing process of cold-pressed terminal stamping, highlighting why it’s become the go-to choice for discerning manufacturers and engineers.
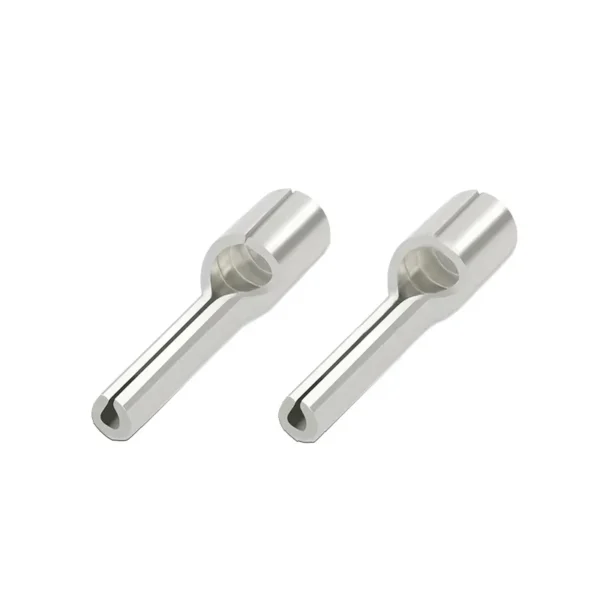
What Are Cold-Pressed Terminal Stampings?
Cold-pressed terminal stampings are precision-engineered electrical connectors produced through a specialized metal stamping process. This method involves shaping metal, typically brass or copper, at room temperature to create terminals with exact specifications and tight tolerances.
“Cold-pressed terminal stamping has revolutionized the way we approach electrical connections, offering unprecedented precision and reliability.” – Industry Expert
Why Choose Cold-Pressed Terminal Stampings?
Cold-pressed terminal stampings offer several advantages over traditional manufacturing methods:
- Superior electrical conductivity
- Enhanced durability and longevity
- Precise dimensions for perfect fit
- Cost-effective production for high volumes
- Versatility in design and application
The Manufacturing Process: How Are Cold-Pressed Terminals Made?
The cold-pressed terminal stamping process involves several key steps:
- Material selection (usually brass or copper)
- Cutting the metal to size
- Stamping the terminal shape
- Forming additional features (if required)
- Quality control and inspection
This process ensures consistent quality and precise dimensions for every terminal produced.
Applications of Cold-Pressed Terminal Stampings
Cold-pressed terminal stampings find use in a wide range of industries and applications, including:
- Automotive electrical systems
- Consumer electronics
- Industrial machinery
- Telecommunications equipment
- Aerospace and defense technologies
What Sets Our Cold-Pressed Terminal Stampings Apart?
At Metal Stamp Master, we pride ourselves on delivering superior quality cold-pressed terminal stampings. Our products stand out due to:
- Precision engineering with tolerances of ±0.003mm
- Use of high-grade materials for optimal conductivity
- Advanced stamping capabilities with high-speed production
- Customization options to meet specific requirements
- Rigorous quality control measures
Frequently Asked Questions About Cold-Pressed Terminal Stampings
Q: What materials are used for cold-pressed terminal stampings?
A: We primarily use brass and copper for their excellent electrical conductivity and formability. However, we can also work with other materials based on specific requirements.
Q: Can cold-pressed terminals be customized?
A: Absolutely! We offer OEM services and can customize terminals according to your specifications, including size, shape, and plating options.
How to Choose the Right Cold-Pressed Terminal for Your Application
When selecting cold-pressed terminals, consider the following factors:
- Current and voltage requirements
- Environmental conditions (temperature, humidity, etc.)
- Connection type (crimp, solder, etc.)
- Wire gauge compatibility
- Plating options for corrosion resistance
The Importance of Quality in Cold-Pressed Terminal Stampings
High-quality cold-pressed terminal stampings are crucial for ensuring:
- Reliable electrical connections
- Extended product lifespan
- Compliance with industry standards
- Optimal performance in demanding applications
Customer Testimonials: What Our Clients Say About Our Cold-Pressed Terminals
“The precision and reliability of these cold-pressed terminals have significantly improved our product’s performance.” – John D., Automotive Engineer
“We’ve been using Metal Stamp Master’s cold-pressed terminals for years, and their quality is consistently top-notch.” – Sarah L., Electronics Manufacturer
How to Order Our Cold-Pressed Terminal Stampings
Ordering our cold-pressed terminal stampings is simple:
- Browse our product catalog
- Select the desired terminal type and specifications
- Request a quote or place an order directly
- Discuss any customization needs with our team
- Confirm your order and shipping details
For large orders or specialized requirements, please contact us directly for personalized service.
The Future of Cold-Pressed Terminal Stamping: Innovations on the Horizon
As technology advances, so does the field of cold-pressed terminal stamping. Future innovations may include:
- Integration of smart materials for enhanced functionality
- Nano-scale precision for miniaturized electronics
- Eco-friendly materials and production processes
- Advanced plating techniques for improved conductivity
Conclusion: Elevate Your Electrical Connections with Our Cold-Pressed Terminals
Investing in high-quality cold-pressed terminal stampings is crucial for ensuring the reliability and efficiency of your electrical systems. Our terminals offer:
- Unmatched precision and quality
- Versatility across various applications
- Cost-effective solutions for high-volume production
- Customization options to meet specific needs
Ready to enhance your electrical connections? Explore our range of cold-pressed terminal stampings and experience the difference in quality and performance.For more information on our metal stamping capabilities, including custom aluminum heatsinks and electrical bus bars, visit our website or contact our team of experts today. Let’s work hand in hand to create a win-win situation for your next project!