-
No.66 Gaojia, Xingfu Village, Sanqi Town, Yuyao, Ningbo,China
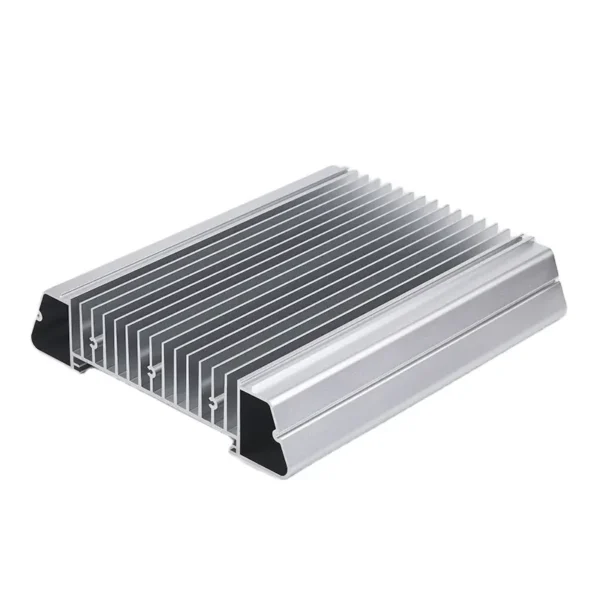
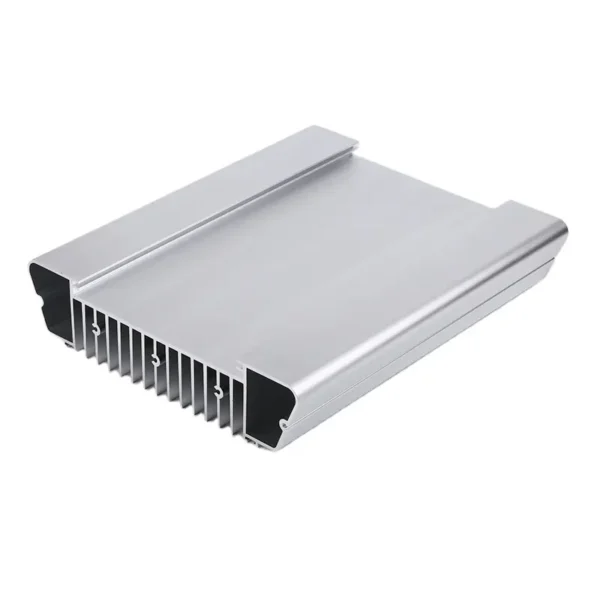
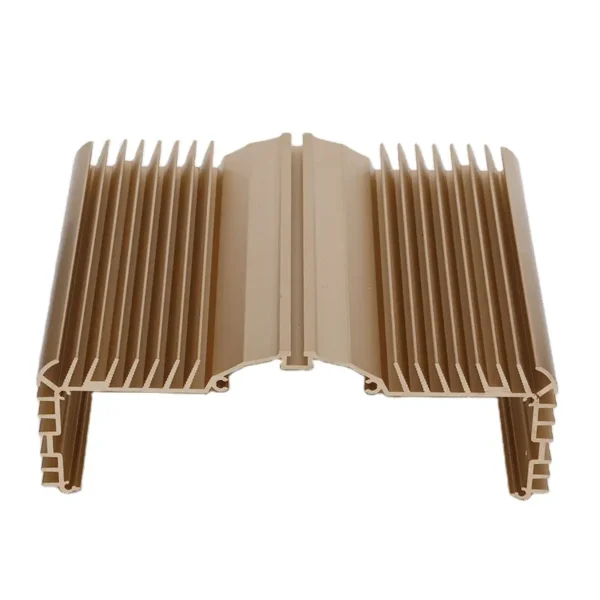
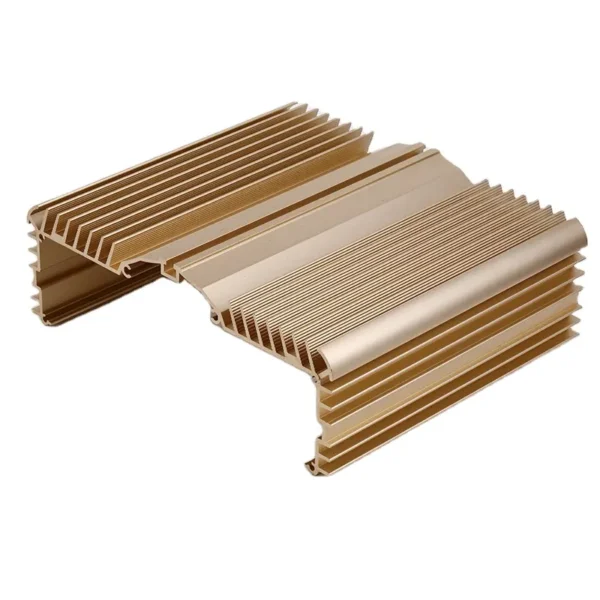
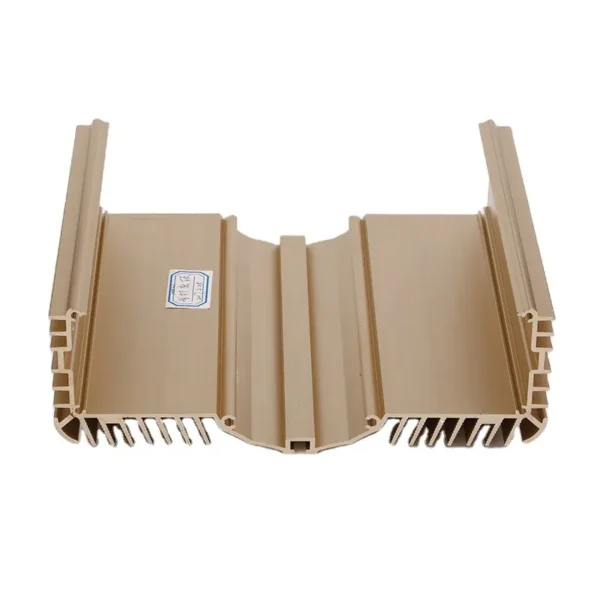

Custom Aluminum Heatsink
Model Number Custom
Product name Custom Aluminum Heatsink
Material Aluminum
Surface finish Powder Coating, Lacquer Coating
Size Customers’ Drawing
Drawing format pdf stp x_t
Tolerance 0.01mm
Service Customized OEM
Custom Aluminum Heatsinks: Revolutionizing Thermal Management for Your Electronics
Custom aluminum heatsinks are essential components in modern electronics, providing efficient thermal management solutions for a wide range of applications. These precision-engineered devices are designed to dissipate heat quickly and effectively, ensuring optimal performance and longevity of electronic systems. With their superior thermal conductivity, durability, and customizable designs, aluminum heatsinks have become the go-to choice for engineers and manufacturers seeking reliable cooling solutions.
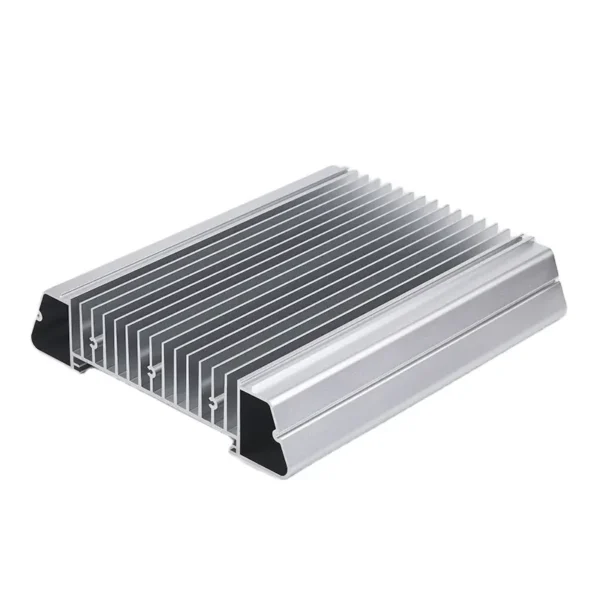
Custom Aluminum Heatsink designed for optimal heat dissipation
What Are Custom Aluminum Heatsinks and How Do They Work?
Custom aluminum heatsinks are specialized thermal management devices designed to efficiently remove heat from electronic components. They work by conducting heat away from the source and dissipating it into the surrounding air through an increased surface area. The process involves:
- Heat absorption from the electronic component
- Heat conduction through the aluminum body
- Heat dissipation via fins or other surface area-increasing structures
Aluminum is the material of choice due to its excellent thermal conductivity, lightweight nature, and cost-effectiveness. Custom heatsinks can be tailored to specific applications, ensuring optimal thermal performance for various electronic devices.
Why Choose Aluminum for Custom Heatsinks?
Aluminum stands out as the preferred material for custom heatsinks due to several advantages:
- High thermal conductivity: Aluminum efficiently transfers heat, making it ideal for rapid heat dissipation.
- Lightweight: Compared to other metals like copper, aluminum is significantly lighter, reducing overall product weight.
- Corrosion resistance: Aluminum naturally forms a protective oxide layer, enhancing durability.
- Cost-effective: Aluminum offers an excellent balance between performance and affordability.
- Ease of manufacturing: Aluminum is easily extruded, machined, and formed into complex shapes.
These properties make aluminum alloys, particularly 6063 aluminum, a popular choice for custom heatsink manufacturing.
What Are the Different Types of Custom Aluminum Heatsinks?
Custom aluminum heatsinks come in various designs to suit different cooling requirements:
- Extruded Aluminum Heatsinks: These are the most common type, offering a good balance of performance and cost.
- Stamped Fin Heatsinks: Ideal for high-volume production with moderate cooling needs.
- Bonded Fin Heatsinks: Offer high thermal performance for demanding applications.
- Folded Fin Heatsinks: Provide excellent cooling in compact spaces.
- Skived Fin Heatsinks: Deliver superior thermal performance for high-power applications.
Each type has its unique advantages, and the choice depends on factors such as thermal requirements, space constraints, and budget considerations.
How Are Custom Aluminum Heatsinks Manufactured?
The manufacturing process for custom aluminum heatsinks typically involves the following steps:
- Design: Engineers create a 3D model based on thermal requirements and space constraints.
- Material Selection: High-quality aluminum alloys are chosen, often 6063 aluminum for its excellent extrusion properties.
- Extrusion: Aluminum billets are heated and forced through a die to create the basic heatsink profile.
- Cutting: Extruded profiles are cut to the required length.
- Machining: CNC machines are used for additional features like mounting holes or surface finishes.
- Surface Treatment: Anodizing or other finishes may be applied to enhance corrosion resistance and appearance.
- Quality Control: Rigorous testing ensures the heatsinks meet thermal and mechanical specifications.
Metal Stamp Master employs state-of-the-art manufacturing techniques to produce high-quality custom aluminum heatsinks tailored to your specific needs.
What Factors Influence the Design of Custom Aluminum Heatsinks?
Several key factors come into play when designing custom aluminum heatsinks:
- Thermal Requirements: The amount of heat to be dissipated determines the overall size and fin design.
- Space Constraints: Available space in the electronic device influences the heatsink’s dimensions and shape.
- Airflow: The presence of natural or forced airflow affects the fin design and orientation.
- Material Properties: The thermal conductivity of the chosen aluminum alloy impacts overall performance.
- Manufacturing Limitations: Certain designs may be constrained by extrusion or machining capabilities.
- Cost Considerations: Budget constraints may influence material choice and manufacturing methods.
Balancing these factors is crucial for creating an efficient and cost-effective custom heatsink solution.
How Do Custom Aluminum Heatsinks Compare to Other Cooling Solutions?
Custom aluminum heatsinks offer several advantages over alternative cooling methods:
Cooling Solution | Advantages | Disadvantages |
---|---|---|
Custom Aluminum Heatsinks | – High thermal efficiency |
- Customizable designs
- Passive cooling (no moving parts)
- Long lifespan | – May require additional airflow for optimal performance
- Can be bulky for high-power applications | | Heat Pipes | – Excellent heat transfer
- Can transport heat over distances | – More complex design
- Higher cost | | Liquid Cooling | – Very high cooling capacity
- Ideal for high-power systems | – Risk of leaks
- Requires maintenance
- More expensive | | Thermoelectric Cooling | – Precise temperature control
- Can cool below ambient temperature | – Lower efficiency
- Requires power input |
For many applications, custom aluminum heatsinks provide the best balance of performance, reliability, and cost-effectiveness.
What Industries Benefit Most from Custom Aluminum Heatsinks?
Custom aluminum heatsinks find applications across various industries:
- Electronics: Cooling CPUs, GPUs, and power supplies in computers and consumer electronics.
- LED Lighting: Managing heat in high-power LED fixtures and displays.
- Automotive: Thermal management for electric vehicle components and engine control units.
- Telecommunications: Cooling base station equipment and network servers.
- Industrial Automation: Maintaining optimal temperatures in control systems and motor drives.
- Aerospace: Thermal management for avionics and satellite components.
- Medical Devices: Ensuring reliable operation of diagnostic and treatment equipment.
The versatility of custom aluminum heatsinks makes them indispensable across these diverse sectors.
How to Choose the Right Custom Aluminum Heatsink for Your Application?
Selecting the appropriate custom aluminum heatsink involves considering several factors:
- Thermal Requirements: Calculate the total heat load and required thermal resistance.
- Space Constraints: Measure the available space for the heatsink in your device.
- Airflow Conditions: Determine if natural convection is sufficient or if forced air cooling is needed.
- Environmental Factors: Consider operating temperature, humidity, and potential exposure to corrosive elements.
- Budget: Balance performance requirements with cost constraints.
- Manufacturing Capabilities: Ensure the design is feasible for production with available technologies.
Consulting with experienced heatsink manufacturers like Metal Stamp Master can help you make the best choice for your specific needs.
What Are the Latest Innovations in Custom Aluminum Heatsink Technology?
The field of custom aluminum heatsinks continues to evolve with new innovations:
- Advanced Fin Designs: Optimized fin shapes and arrangements for improved heat dissipation.
- Hybrid Materials: Combining aluminum with other materials like copper or graphene for enhanced performance.
- Phase Change Materials: Integrating PCMs into heatsinks for improved thermal management during peak loads.
- 3D Printing: Exploring additive manufacturing techniques for complex heatsink geometries.
- Surface Treatments: Developing new coatings to enhance thermal conductivity and corrosion resistance.
- Simulation Software: Utilizing advanced thermal modeling tools for more accurate heatsink designs.
These innovations are pushing the boundaries of what’s possible in thermal management, enabling more efficient and compact electronic devices.In conclusion, custom aluminum heatsinks play a crucial role in modern electronics, offering tailored thermal management solutions across various industries. Their versatility, efficiency, and cost-effectiveness make them an indispensable component in the design of reliable and high-performance electronic systems. As technology continues to advance, custom aluminum heatsinks will undoubtedly evolve to meet the increasingly demanding thermal challenges of tomorrow’s devices.For more information on how custom aluminum heatsinks can benefit your specific application, contact our experts at Metal Stamp Master. We specialize in designing and manufacturing high-quality custom heatsinks tailored to your unique requirements.