-
No.66 Gaojia, Xingfu Village, Sanqi Town, Yuyao, Ningbo,China
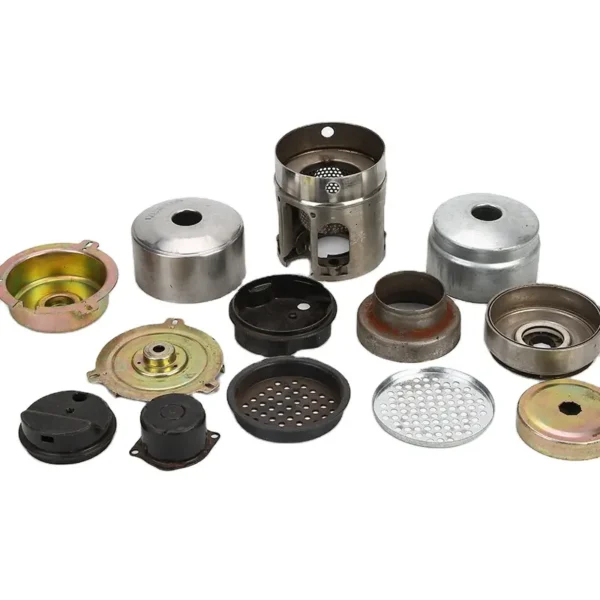
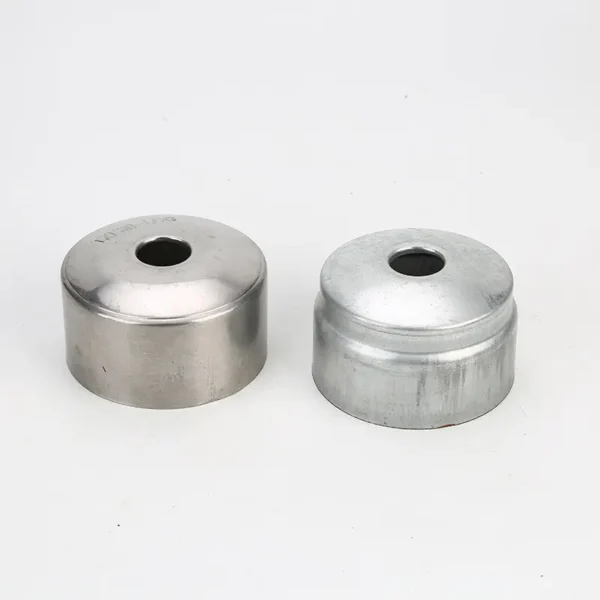
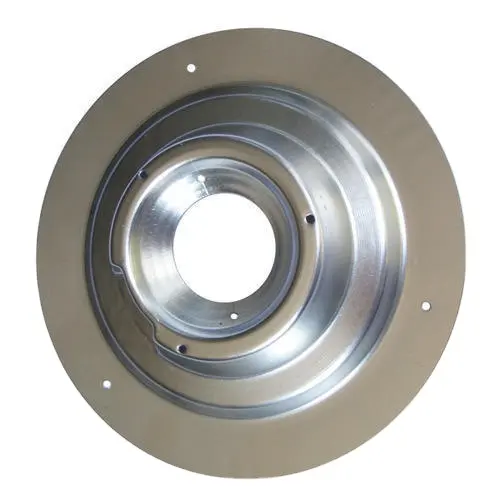
Deep Draw Stamping Part For Lighting
Product name Sheet Metal Fabrication Stamping Bending Welding Parts
Thickness cuatomized
Materials Zinc, aluminum, copper, steel, powder coating, etc.
Surface treatment Electric plating,powder coated,sand blasting,lacquer
Process Punching, stamping, bending, riveting, etc.
Testing Salt spray
OEM/ODM Accept
Color Custom Accepted
Drawing format 2D/3D/CAD/DWG//STEP/PDF/IGS
Revolutionize Your Lighting with Deep Draw Stamping Parts: The Ultimate Guide
Deep draw stamping is a cutting-edge metal forming process that has revolutionized the production of lighting components. This comprehensive guide will explore the intricacies of deep draw stamping parts for lighting, highlighting their benefits and why they are an essential investment for manufacturers in the lighting industry.
Deep draw stamping process in action, creating precision metal components
What is Deep Draw Stamping and How Does it Benefit Lighting Manufacturing?
Deep draw stamping is a specialized metal forming process that creates complex, three-dimensional parts from flat metal sheets
. This technique is particularly valuable in the lighting industry, where precision and durability are paramount. The process involves stretching sheet metal stock, commonly referred to as a blank, around a plug in either a hydraulic or mechanical press
.The benefits of deep draw stamping for lighting parts include:
- High precision and consistency: Deep draw stamping allows for tight tolerances and repeatable results, ensuring that each lighting component meets exact specifications.
- Cost-effective for high volume production: Once the tooling is set up, deep draw stamping can produce large quantities of parts quickly and efficiently.
- Versatility in materials: This process can work with a variety of metals, including aluminum and stainless steel, providing options for different lighting applications.
- Enhanced structural integrity: The forming process can create parts with improved strength-to-weight ratios, ideal for durable lighting fixtures.
How Does the Deep Draw Stamping Process Work for Lighting Components?
The deep draw stamping process for lighting components typically follows these steps:
- Design Review: Engineers analyze the part design to ensure it’s optimized for the deep draw process.
- Tool Design and Fabrication: Custom tools, including the punch and die, are created for the specific lighting part.
- Material Selection: The appropriate metal sheet is chosen based on the lighting component’s requirements.
- Stamping: The metal is drawn into the die by mechanical action, forming the desired shape.
- Finishing: Any necessary post-stamping operations are performed to complete the part.
This process allows manufacturers to produce complex lighting parts with high precision and efficiency.
What Materials Are Commonly Used in Deep Draw Stamping for Lighting?
Deep draw stamping can accommodate a variety of metals, making it versatile for different lighting applications. Common materials include:
- Aluminum: Ideal for lightweight, corrosion-resistant lighting fixtures
- Stainless Steel: Perfect for durable, long-lasting outdoor lighting components
- Copper: Excellent for heat dissipation in LED lighting systems
- Brass: Often used for decorative lighting elements
The choice of material depends on the specific requirements of the lighting part, such as heat resistance, weight, and aesthetic appeal.
How Does Deep Draw Stamping Compare to Other Metal Forming Processes for Lighting Parts?
Deep draw stamping offers several advantages over other metal forming processes when it comes to lighting components:
Process | Advantages | Disadvantages |
---|---|---|
Deep Draw Stamping | High precision, cost-effective for large volumes, complex shapes possible | Higher initial tooling costs |
Traditional Stamping | Simple setup, good for flat parts | Limited depth, less suitable for complex shapes |
Spinning | Good for symmetrical parts | Slower production, limited to round shapes |
Hydroforming | Uniform thickness, complex shapes | Higher equipment costs, slower production |
Deep draw stamping excels in producing complex, three-dimensional lighting parts with high precision and efficiency, making it a preferred choice for many manufacturers.
What Are the Key Considerations in Designing Lighting Parts for Deep Draw Stamping?
When designing lighting parts for deep draw stamping, consider the following factors:
- Material properties: Understanding the metal’s formability and strength is crucial for successful deep drawing.
- Part geometry: Design parts with uniform wall thickness and avoid sharp corners to prevent tearing.
- Draw ratio: The ratio of the blank diameter to the finished part diameter should be optimized for the material and press capabilities.
- Lubrication: Proper lubrication is essential to reduce friction and heat during the stamping process.
- Tooling design: The punch and die must be carefully designed to achieve the desired part shape without defects.
By considering these factors, designers can create lighting parts that are optimized for the deep draw stamping process, ensuring high-quality results.
How Does Deep Draw Stamping Contribute to Sustainability in Lighting Manufacturing?
Deep draw stamping can contribute to sustainability in lighting manufacturing in several ways:
- Material efficiency: The process minimizes material waste compared to subtractive manufacturing methods.
- Energy efficiency: Once set up, deep draw stamping can produce parts quickly with relatively low energy consumption.
- Durability: The high-quality parts produced can lead to longer-lasting lighting products, reducing the need for frequent replacements.
- Recyclability: Many metals used in deep draw stamping, such as aluminum, are easily recyclable at the end of the product’s life.
These factors make deep draw stamping an environmentally friendly choice for lighting manufacturers committed to sustainability.
What Quality Control Measures Are Essential in Deep Draw Stamping for Lighting Parts?
Ensuring the quality of deep-drawn lighting parts is crucial for maintaining product performance and reliability. Key quality control measures include:
- Material inspection: Verifying the quality and properties of the metal sheet before stamping.
- In-process monitoring: Using sensors and cameras to detect defects during the stamping process.
- Dimensional checks: Regularly measuring parts to ensure they meet specified tolerances.
- Surface finish inspection: Examining parts for scratches, dents, or other surface imperfections.
- Functional testing: Verifying that the stamped parts perform as intended in the final lighting assembly.
Implementing these quality control measures helps maintain the high standards required for lighting components.
How Can Manufacturers Optimize Their Deep Draw Stamping Process for Lighting Parts?
To optimize the deep draw stamping process for lighting parts, manufacturers can:
- Invest in advanced tooling: High-quality tools can improve part consistency and reduce wear.
- Implement simulation software: Use computer simulations to predict and prevent potential issues before production.
- Optimize lubrication: Choose the right lubricants to reduce friction and heat during stamping.
- Automate where possible: Introduce automation to increase efficiency and reduce human error.
- Continuous training: Keep operators updated on the latest deep draw stamping techniques and best practices.
By focusing on these areas, manufacturers can enhance their deep draw stamping capabilities and produce higher quality lighting parts more efficiently.
What Are the Future Trends in Deep Draw Stamping for the Lighting Industry?
The future of deep draw stamping in the lighting industry looks bright, with several emerging trends:
- Integration with smart manufacturing: Incorporating IoT sensors and data analytics for real-time process optimization.
- Advanced materials: Exploring new alloys and composites that offer improved properties for lighting applications.
- Miniaturization: Developing techniques to produce smaller, more intricate parts for compact lighting designs.
- Sustainability focus: Increasing emphasis on eco-friendly materials and energy-efficient production methods.
- Customization: Adapting deep draw stamping processes for smaller batch sizes and personalized lighting products.
These trends indicate that deep draw stamping will continue to play a crucial role in the evolution of lighting manufacturing.In conclusion, deep draw stamping is a powerful and versatile process that offers numerous benefits for the production of lighting components. Its ability to create complex, precise parts efficiently makes it an invaluable tool for manufacturers looking to stay competitive in the rapidly evolving lighting industry. By understanding the intricacies of deep draw stamping and staying abreast of emerging trends, lighting manufacturers can leverage this technology to produce high-quality, innovative products that meet the demands of modern consumers.For more information on how deep draw stamping can revolutionize your lighting manufacturing process, contact our metal stamping experts today. Our team at Metal Stamp Master is ready to help you explore the possibilities of deep draw stamping for your specific lighting applications.