-
No.66 Gaojia, Xingfu Village, Sanqi Town, Yuyao, Ningbo,China
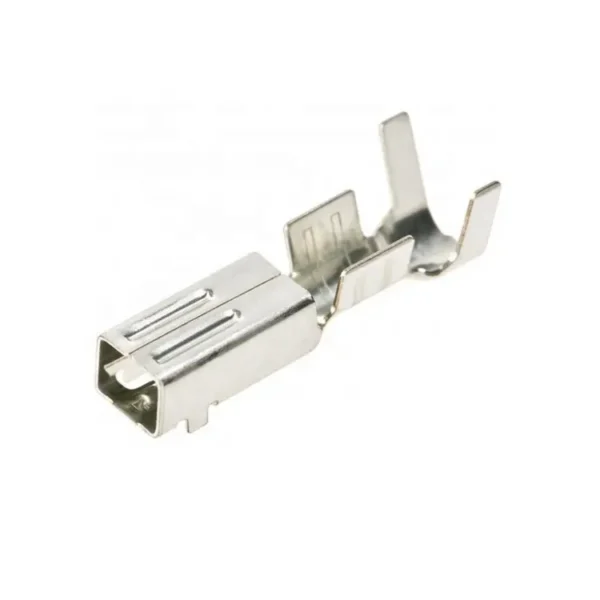
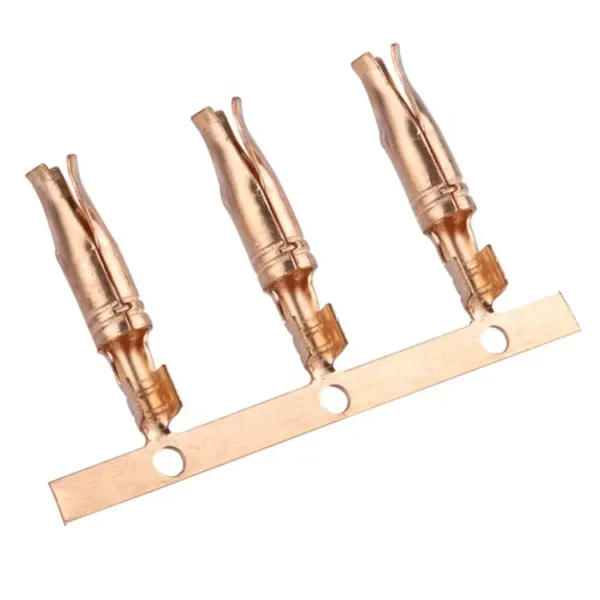
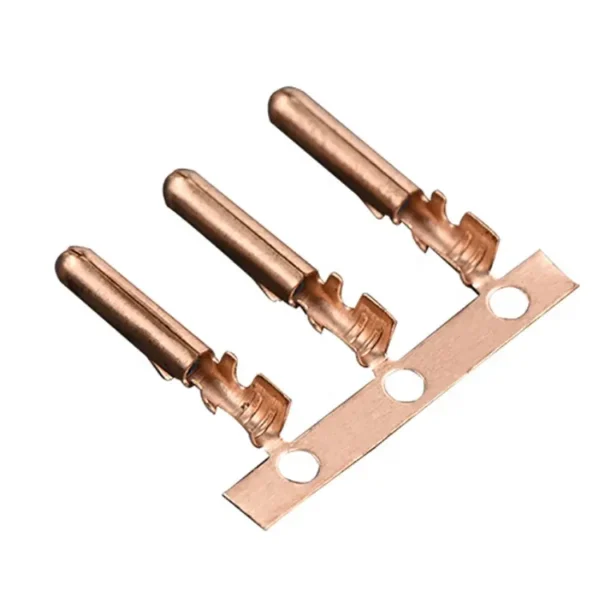
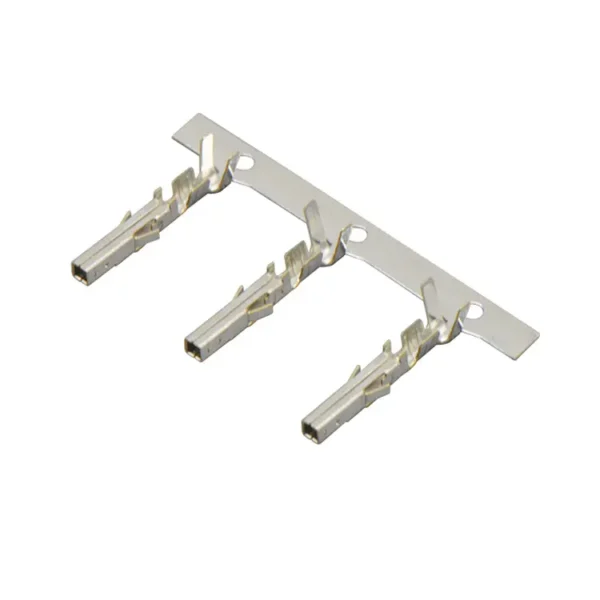
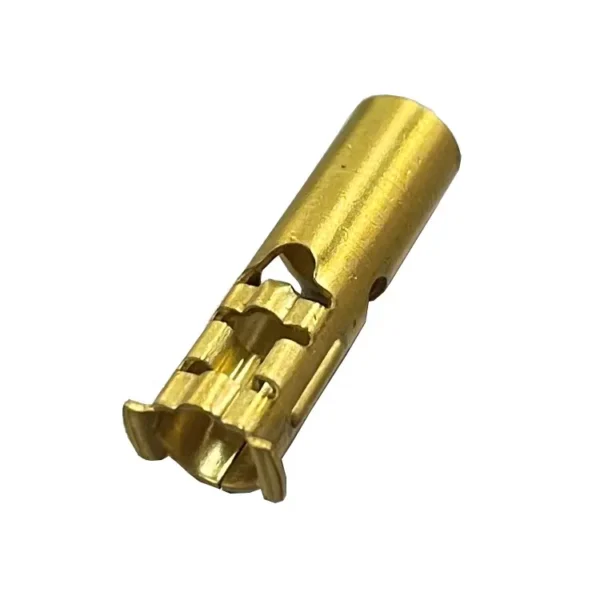
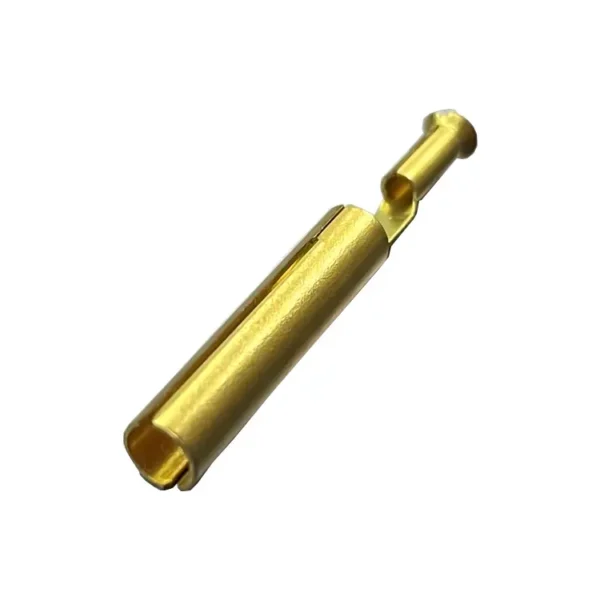
Electric Cable Copper Stamping
Model Number OEM
Product name Terminal connector
Material Copper
Surface treatment Tin plating
Thickness 0.1-1mm
Tolerance ±0.03mm
Equipment 25-200 Tons
Mold/Die/Tooling Strong In-house
Precision Electric Cable Copper Stamping: Revolutionizing Wire Connectivity
Electric cable copper stamping is a crucial component in modern electrical systems, offering unparalleled conductivity and durability for various applications. This innovative product combines the excellent properties of copper with precision metal stamping techniques, resulting in high-quality connectors that ensure reliable electrical connections. Let’s explore why these stamped copper components are essential for your wire and cable needs.
What is Electric Cable Copper Stamping?
Electric cable copper stamping refers to the process of creating precision-engineered copper components for electrical applications using metal stamping techniques. These stamped parts are typically used as connectors, terminals, or other elements in wire and cable assemblies. The stamping process allows for high-speed production of intricate shapes with tight tolerances, making it ideal for manufacturing electrical connectors and related components.
Copper is the material of choice for these stampings due to its excellent electrical conductivity, malleability, and corrosion resistance. The most commonly used copper alloy for electrical applications is C11000, also known as electrolytic tough pitch (ETP) copper, which offers a perfect balance of conductivity and strength.
Why Choose Copper Stamping for Electrical Connections?
Copper stamping offers several advantages for electrical connections:
- Excellent Electrical Conductivity: Copper is one of the best conductors of electricity, ensuring efficient power transmission.
- Corrosion Resistance: Copper naturally resists corrosion, extending the service life of electrical components.
- Malleability: Copper’s malleability allows for complex shapes to be stamped without compromising structural integrity.
- Cost-Effective: The stamping process is highly efficient, resulting in cost savings compared to other manufacturing methods.
- Precision: Metal stamping enables the production of high-precision parts with tight tolerances.
These unique properties make copper stamping an ideal choice for various electrical applications, from automotive wiring to consumer electronics.
How Are Electric Cable Copper Stampings Manufactured?
The manufacturing process for electric cable copper stampings involves several steps:
- Design: Engineers create detailed designs using CAD software.
- Tool Creation: Custom progressive dies are manufactured for the stamping process.
- Material Selection: High-quality copper sheet or strip is chosen based on the application requirements.
- Stamping: The copper is fed through a stamping press, which uses the progressive die to create the desired shapes.
- Quality Control: Stamped parts undergo rigorous inspection using camera vision systems and sensor technology.
- Finishing: If required, additional processes like plating or heat treatment may be applied.
- Assembly: The stamped parts are often integrated into larger wire and cable assemblies.
This high-speed, precision manufacturing process ensures consistent quality and high yield, making it suitable for both small and large production runs.
What Are the Common Applications of Electric Cable Copper Stampings?
Electric cable copper stampings find use in a wide range of applications:
- Automotive wiring harnesses
- Consumer electronics
- Industrial machinery
- Electrical Connectors stamping
- Power distribution systems
- Telecommunications equipment
- Electric Cable Copper Stamping for various industries
- EV battery connections
- Sensor and control systems
- Appliance Parts Metal Brackets
The versatility of copper stampings makes them indispensable in modern electrical systems across multiple industries.
How Do Copper Stampings Contribute to Improved Electrical Performance?
Copper stampings play a crucial role in enhancing electrical performance:
- Low Resistance: Copper’s high conductivity minimizes power loss in electrical circuits.
- Consistent Contact: Precision stamping ensures uniform contact surfaces for reliable connections.
- Heat Dissipation: Copper’s thermal conductivity helps dissipate heat, preventing overheating in high-current applications.
- Durability: The corrosion resistance of copper maintains performance over time, even in harsh environments.
- Flexibility: Stamped copper components can be designed to accommodate movement and vibration in dynamic applications.
These factors contribute to more efficient and reliable electrical systems, making copper stampings a preferred choice for OEM and tier manufacturers.
What Quality Control Measures Are Applied to Electric Cable Copper Stampings?
Ensuring the highest quality of electric cable copper stampings is paramount. Manufacturers employ various quality control measures:
- Dimensional Inspection: Using high-precision measuring tools to verify part dimensions.
- Visual Inspection: Checking for surface defects or irregularities.
- Electrical Testing: Verifying conductivity and resistance properties.
- Plating Thickness Measurement: For plated components, ensuring proper coating thickness.
- Tensile Strength Testing: Evaluating the mechanical properties of the stamped parts.
- X-Ray Fluorescence (XRF) Analysis: Confirming the material composition.
Many manufacturers also implement comprehensive quality management systems, such as ISO 9001, to ensure consistent product quality throughout the production process.
How Do Copper Stampings Compare to Other Materials for Electrical Connections?
When compared to other materials, copper stampings offer several advantages:
Material | Conductivity | Corrosion Resistance | Cost | Formability |
---|---|---|---|---|
Copper | Excellent | Good | Moderate | Excellent |
Aluminum | Good | Fair | Low | Good |
Silver | Excellent | Excellent | High | Good |
Gold | Excellent | Excellent | Very High | Fair |
Tin | Fair | Good | Low | Good |
While precious metals like silver and gold offer superior properties, their high cost makes them impractical for most applications. Aluminum is cheaper but lacks the conductivity and corrosion resistance of copper. This makes copper the ideal balance of performance and cost for most electrical applications.
What Are the Environmental Considerations for Copper Stampings?
Copper stampings have several environmental advantages:
- Recyclability: Copper is 100% recyclable without loss of quality, promoting sustainable practices.
- Energy Efficiency: The high conductivity of copper reduces energy loss in electrical systems.
- Longevity: The durability of copper components reduces the need for frequent replacements.
- Minimal Waste: The stamping process is highly efficient, minimizing material waste.
However, it’s important to note that copper mining and processing can have environmental impacts. Responsible sourcing and recycling practices are crucial for minimizing these effects.
How to Choose the Right Supplier for Electric Cable Copper Stampings?
Selecting the right supplier for your electric cable copper stamping needs is crucial. Consider the following factors:
- Experience: Look for suppliers with a proven track record in electrical component manufacturing.
- Quality Certifications: Ensure the supplier has relevant quality management certifications like ISO 9001.
- Technical Capabilities: Evaluate their stamping press capabilities, tool design expertise, and finishing options.
- Lead Times: Assess their ability to meet your production schedules and delivery times.
- Customer Service: A cooperative and responsive supplier can streamline your production processes.
- Cost-Effectiveness: While price is important, consider the total value, including quality and service.
“Choosing the right supplier is not just about the product; it’s about finding a partner who understands your unique requirements and can deliver consistently high-quality components.” – Industry Expert
What’s the Future of Electric Cable Copper Stamping?
The future of electric cable copper stamping looks promising, driven by several trends:
- Miniaturization: As electronic devices shrink, there’s a growing demand for smaller, more precise copper stampings.
- Electric Vehicles: The EV revolution is creating new opportunities for high-performance copper connectors.
- 5G Infrastructure: The rollout of 5G networks requires advanced copper components for high-frequency applications.
- Smart Homes: The increasing connectivity in homes is driving demand for reliable copper connectors.
- Renewable Energy: Solar and wind power systems rely heavily on efficient copper components.
As these trends evolve, we can expect to see continued innovation in copper stamping technology, including advancements in progressive die design, integration of smart manufacturing techniques, and development of new copper alloys tailored for specific applications.
In conclusion, electric cable copper stamping represents a critical technology in the realm of electrical connectivity. Its combination of excellent conductivity, durability, and cost-effectiveness makes it an indispensable component in modern electrical systems. As industries continue to evolve and demand ever-more efficient and reliable electrical connections, the importance of precision-engineered copper stampings will only grow.
For those seeking high-quality electric cable copper stampings, consider exploring the offerings from reputable suppliers like Metal Stamp Master. Their expertise in metal stamping production and commitment to quality can help ensure that your electrical components meet the highest standards of performance and reliability.