-
No.66 Gaojia, Xingfu Village, Sanqi Town, Yuyao, Ningbo,China
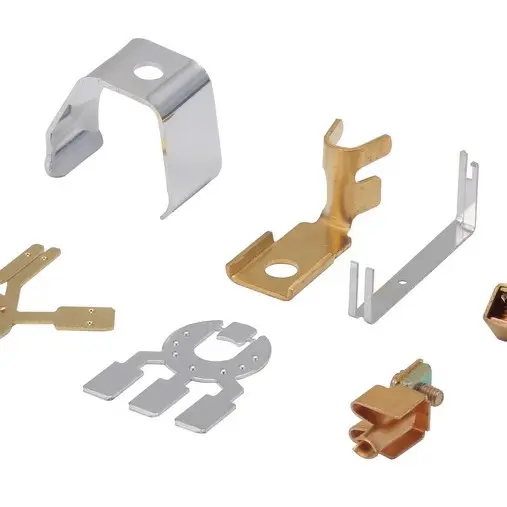
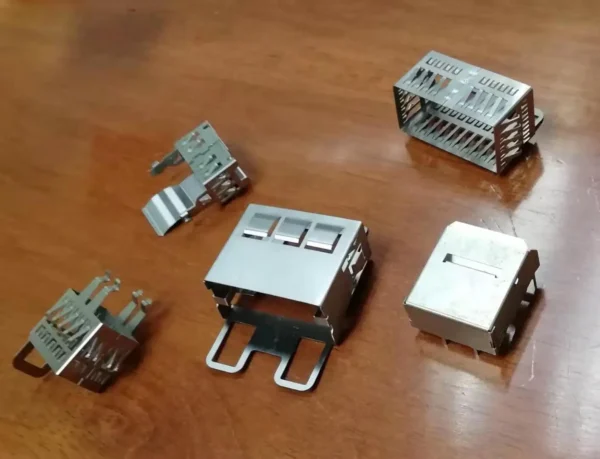
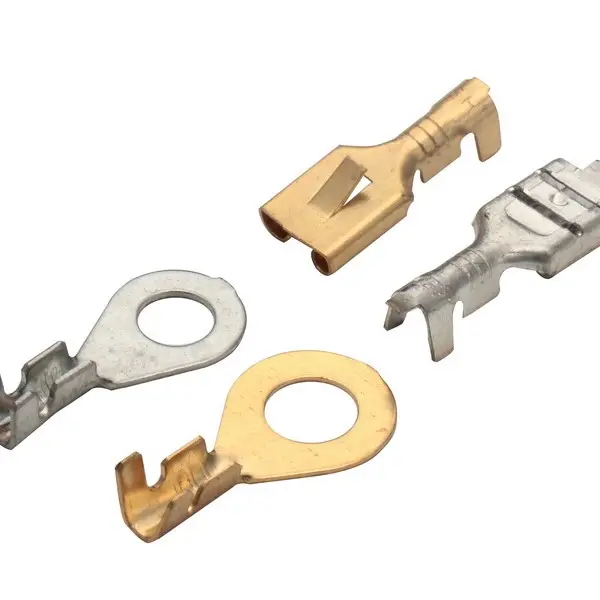
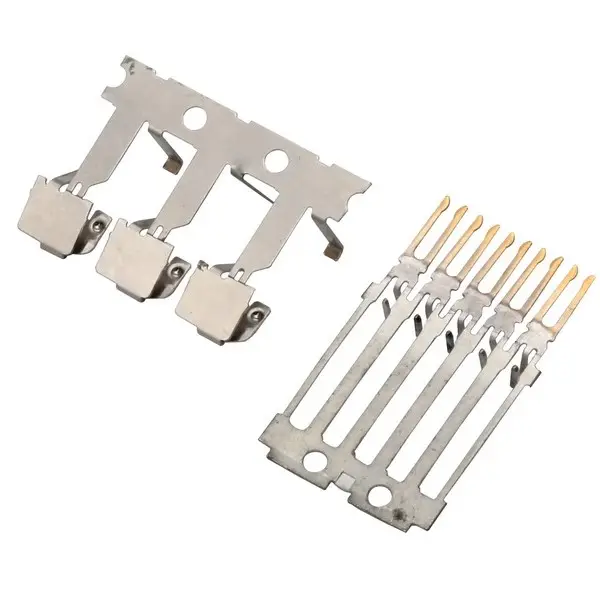

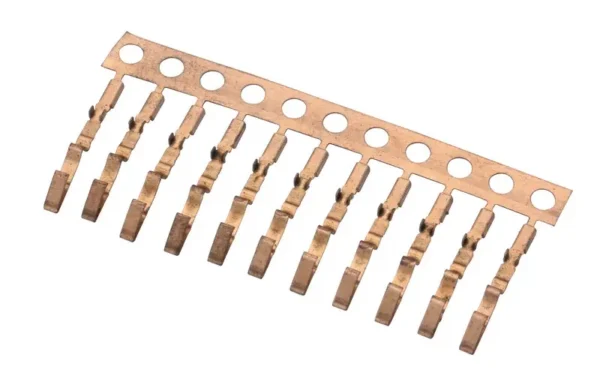
Electrical Connectors stamping
Material aluminum alloy,stainless steel, brass,copper,Spring steel etc
Finish anodizing,sandblasting,powder coating,polishing etc
Process Stamping, punching, bending, welding
Size Customized Sized Acceptable
Tolerance +/-0.01- +/-0.05
Application Industrial, Furniture, Automobile, Motorcycle, etc.
Keywords metal stamping service
Approach Metal stamping, Cutting / Punching / Bending / Welding / Deep Drawing;
MOQ Accept 1 pcs sample.
Stamped Electrical Terminals: Powering Connectivity in Modern Electronics
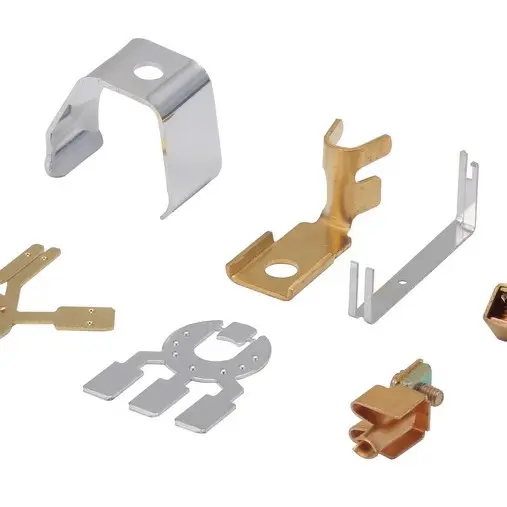
Stamped electrical terminals are the unsung heroes of our interconnected world, providing reliable and efficient connections in countless electronic devices and systems. These precision-engineered components are essential for transferring electrical current from power sources to various electrical systems, ensuring seamless operation across a wide range of applications. In this comprehensive guide, we’ll explore the world of stamped electrical terminals, their benefits, and why they’re an indispensable part of modern electronics.
What Are Stamped Electrical Terminals?
Stamped electrical terminals are conductive components used to transfer electrical current from a power or grounding source to an electrical system. These terminals are typically made through a precision metal stamping process, which allows for high-volume production of accurate and consistent parts. Stamped electrical terminals come in various shapes and sizes, designed to meet the specific requirements of different electrical circuits and connectors.
Why Choose Stamped Electrical Terminals?
- Cost-effective production: The metal stamping process allows for high-volume production at a lower cost compared to other manufacturing methods.
- Precision and consistency: Stamping techniques ensure that each terminal conforms to exact specifications, resulting in reliable performance.
- Versatility: Stamped terminals can be designed for a wide range of applications and industries.
- Durability: When made from high-quality materials, stamped terminals offer excellent durability and longevity.
How Are Stamped Electrical Terminals Manufactured?
The production process for stamped electrical terminals involves several key steps:
- Material selection
- Design and engineering
- Tool and die preparation
- Stamping
- Secondary operations (if required)
- Quality control and inspection
Precision metal stamping techniques are employed to ensure that each terminal meets the exact specifications required for its intended application.
What Materials Are Used for Stamped Electrical Terminals?
Stamped electrical terminals are typically made from conductive metals such as:
- Copper
- Brass
- Phosphor bronze
- Beryllium copper
- Stainless steel
The choice of metal stamping materials depends on factors such as electrical conductivity, corrosion resistance, and mechanical properties required for the specific application.
What Types of Stamped Electrical Terminals Are Available?
There is a wide range of stamped electrical terminals available, including:
- Spade terminals
- Ring terminals
- Fork terminals
- Bullet terminals
- Pin terminals
- Deutsch stamped and formed contacts
Each type is designed for specific connector configurations and electrical requirements.
How Do Stamped Electrical Terminals Compare to Other Connection Methods?
Stamped electrical terminals offer several advantages over other connection methods:
- Reliability: Stamped terminals provide a secure and stable connection.
- Ease of use: They can be quickly and easily inserted or removed from connectors.
- Customization: Stamped terminals can be designed to meet specific application requirements.
- Cost-effectiveness: High-volume production makes stamped terminals an economical choice for many applications.
What Industries Rely on Stamped Electrical Terminals?
Stamped electrical terminals are used in a variety of industries, including:
- Automotive
- Aerospace
- Consumer electronics
- Industrial equipment
- Telecommunications
- Medical devices
These industries rely on stamped electrical contacts and terminals for their robust and reliable performance in various electrical systems.
How Are Stamped Electrical Terminals Assembled?
The assembly process for stamped electrical terminals typically involves:
- Crimping: Attaching the terminal to a wire or cable
- Insertion: Placing the terminal into a connector housing
- Locking: Securing the terminal in place within the connector
Stamping assembly processes are designed to ensure a secure and reliable connection between the terminal and the wire or connector.
What Quality Control Measures Are Used in Stamped Terminal Production?
To ensure superior quality, manufacturers implement rigorous quality control processes, including:
- 3D modeling and tooling simulation
- First article inspection
- In-process monitoring
- Final inspection and testing
These measures help to ensure that stamped electrical terminals meet or exceed industry standards and customer specifications.
How Do Surface Coatings Affect Stamped Electrical Terminals?
Surface coating applications play a crucial role in enhancing the performance and longevity of stamped electrical terminals. Common coatings include:
- Tin plating
- Gold plating
- Silver plating
- Nickel plating
These coatings can improve conductivity, corrosion resistance, and wear resistance, depending on the specific requirements of the application.
What Are the Future Trends in Stamped Electrical Terminal Technology?
The field of stamped electrical terminals continues to evolve, with trends including:
- Miniaturization: Smaller terminals for compact electronic devices
- High-temperature materials: Terminals capable of withstanding extreme conditions
- Environmental considerations: Development of lead-free and eco-friendly terminals
- Smart connectors: Integration of sensors and diagnostics capabilities
These advancements will help meet the demands of emerging technologies and industries.In conclusion, stamped electrical terminals are critical components in modern electronics, offering a blend of reliability, cost-effectiveness, and versatility. As a supplier of stamped metal parts, we understand the importance of precision and quality in every terminal we produce. Whether you’re working on automotive systems, industrial equipment, or consumer electronics, choosing the right stamped electrical terminals can make a significant difference in the performance and longevity of your electrical connections.
“The quality of your connections determines the quality of your results.” – This applies not just to networking, but also to the physical connections in your electrical systems.
For more information on our range of stamped electrical terminals and connectors, or to discuss your specific requirements, please contact us today. Our team of experts is ready to help you find the perfect solution for your electrical connection needs.