-
No.66 Gaojia, Xingfu Village, Sanqi Town, Yuyao, Ningbo,China
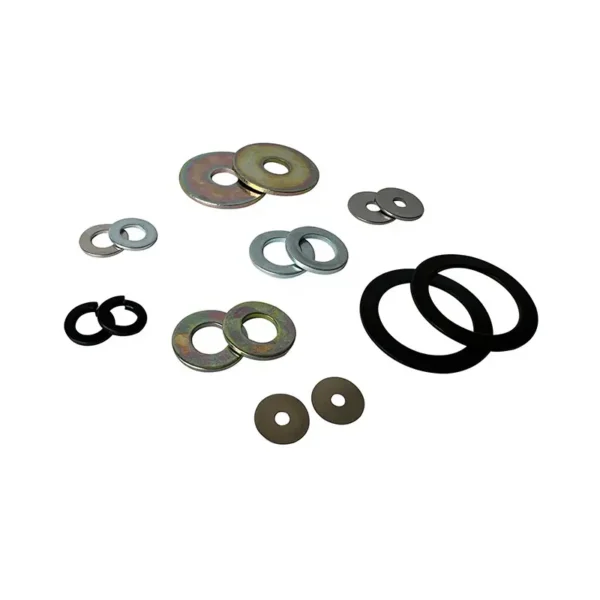
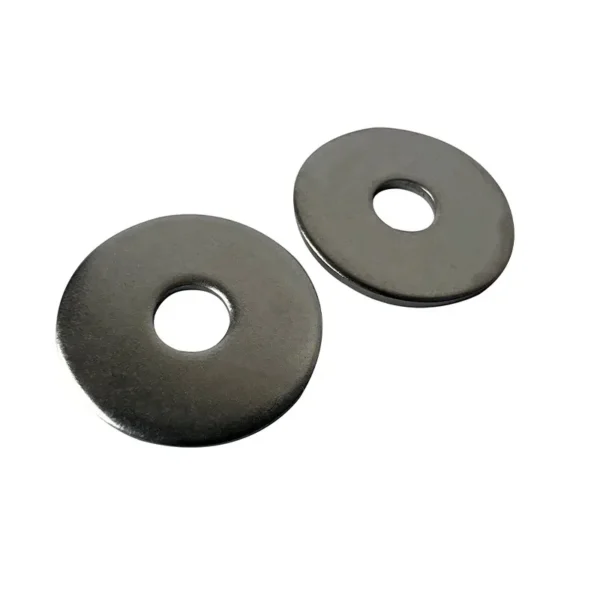
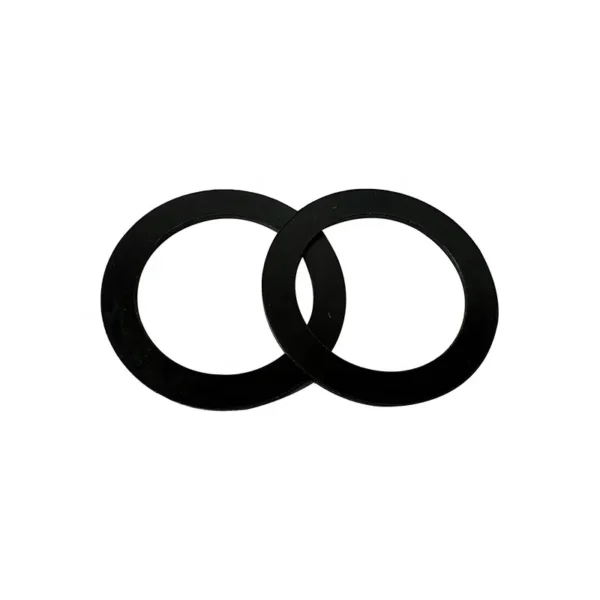
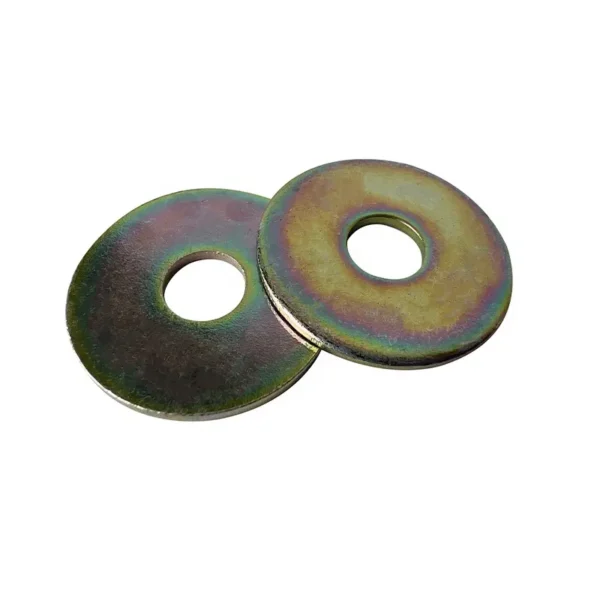
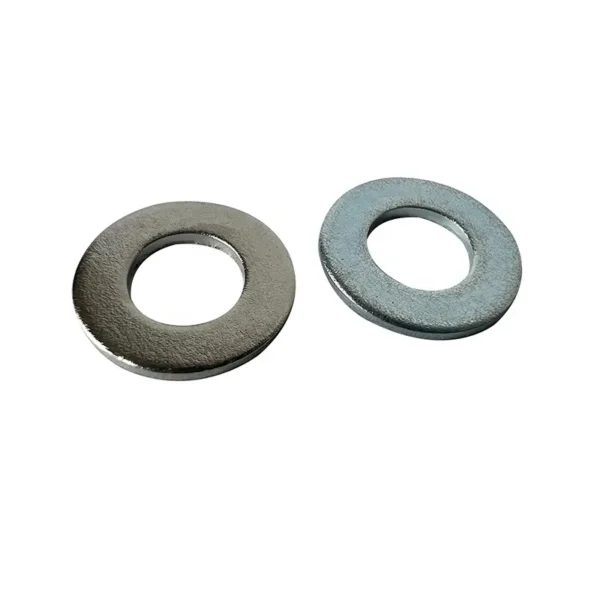
Rapid Prototype Parts Spacer
MOQ Low Moq Acceptable
Drawing Format 2D/(PDF/CAD/DWG/DXF)3D(IGES/STEP/VDA)
Shape Support On-demand Customization
Quality Control 100% Inspection
Size Customized Size\Client’s Drawings
Material Capabilities Steel/Aluminum/copper/Stainless Steel 316/etc
Dimensions Custmer’s Drawings
Rapid Prototype Parts Spacer: Precision CNC Machined Components for Custom Applications
Rapid prototype parts spacers are essential components in various industries, offering precision-engineered solutions for prototyping and custom manufacturing needs. These versatile parts are designed to provide accurate spacing, alignment, and support in a wide range of applications. With the ability to be quickly produced through CNC machining processes, these spacers offer a perfect blend of quality, customization, and rapid turnaround times. In this comprehensive guide, we’ll explore the features, benefits, and applications of rapid prototype parts spacers, helping you make informed decisions for your project requirements.
What are Rapid Prototype Parts Spacers?
Rapid prototype parts spacers are precision-engineered components created through advanced CNC machining processes. These spacers are designed to provide precise spacing and alignment in various assemblies, prototypes, and custom applications. Typically made from materials such as aluminum, plastic, or brass, these spacers can be quickly produced to meet specific design requirements and tight tolerances.
Why Choose CNC Machined Rapid Prototype Parts Spacers?
CNC machined rapid prototype parts spacers offer several advantages:
- Precision: CNC machining ensures high accuracy and consistent quality.
- Customization: Easily tailored to specific project requirements.
- Quick Turnaround: Rapid prototyping allows for fast production and iteration.
- Material Versatility: Can be machined from a wide range of materials.
How Are These Spacers Manufactured?
The manufacturing process of rapid prototype parts spacers typically involves:
- Design: Creating detailed 3D models and technical drawings.
- Material Selection: Choosing the appropriate material based on application requirements.
- CNC Machining: Utilizing precision CNC mills and lathes to create the spacers.
- Quality Control: Rigorous inspection to ensure adherence to specifications.
What Are the Key Features of Rapid Prototype Parts Spacers?
- Materials: Commonly made from aluminum, plastic, brass, or stainless steel
- Tolerances: Typically held to tight tolerances (±0.001″ or better)
- Customization: Easily modified for specific dimensions, shapes, and features
- Surface Finish: Can be tailored to application requirements (e.g., smooth, textured)
How Do CNC Machined Spacers Compare to Other Manufacturing Methods?
Method | Advantages | Disadvantages |
---|---|---|
CNC Machining | High precision, material versatility, quick turnaround | Higher cost for large quantities |
3D Printing | Complex geometries possible, low setup costs | Limited material options, lower precision |
Injection Molding | Cost-effective for high volumes, consistent quality | High initial tooling costs, less flexible for changes |
What Are the Common Applications of Rapid Prototype Parts Spacers?
These spacers find use in various industries and applications, including:
- Aerospace prototyping
- Automotive component development
- Medical device testing
- Electronics assembly
- Industrial machinery design
How to Choose the Right Rapid Prototype Parts Spacer for Your Project?
When selecting a rapid prototype parts spacer, consider the following factors:
- Material: Choose based on strength, weight, and environmental requirements.
- Dimensions: Specify precise measurements for your application.
- Tolerance: Determine the level of precision needed for your project.
- Surface Finish: Select the appropriate finish for your application.
- Quantity: Consider prototype quantities and potential production scaling.
What Are the Benefits of Using CNC Machined Rapid Prototype Parts Spacers?
- Design Flexibility: Easily modify designs for prototyping and testing.
- Rapid Iteration: Quick turnaround allows for fast design improvements.
- Material Options: Choose from a wide range of materials to suit your needs.
- Precision: Achieve tight tolerances for critical applications.
- Scalability: Seamlessly transition from prototyping to production.
How to Integrate Rapid Prototype Parts Spacers into Your Design Process?
Integrating these spacers into your design process typically involves:
- Concept Development: Identify spacing and alignment needs in your design.
- 3D Modeling: Create detailed CAD models of the spacers.
- Material Selection: Choose the appropriate material for your application.
- Prototyping: Utilize CNC machining for rapid production of prototype spacers.
- Testing and Iteration: Evaluate spacer performance and make necessary adjustments.
“Rapid prototype parts spacers are invaluable tools in the product development process, allowing designers and engineers to quickly test and refine their ideas with precision-engineered components.” – Product Design Expert
Where to Source Quality Rapid Prototype Parts Spacers?
When looking to purchase or manufacture rapid prototype parts spacers, consider the following options:
- CNC Machining Services: Specialized shops offering rapid prototyping capabilities
- Custom Manufacturing Partners: Companies with expertise in precision parts production
- Rapid Prototyping Firms: Specialists in quick-turn prototype components
- Online Marketplaces: Platforms connecting buyers with manufacturing services
How to Ensure Quality in Rapid Prototype Parts Spacers?
To maintain high quality in your rapid prototype parts spacers:
- Clear Specifications: Provide detailed technical drawings and requirements.
- Material Certification: Ensure materials meet necessary standards and specifications.
- Inspection: Implement rigorous quality control processes.
- Testing: Conduct functional tests to verify spacer performance.
- Documentation: Maintain records of design iterations and quality checks.
In conclusion, rapid prototype parts spacers are versatile and essential components in the product development process. By leveraging CNC machining capabilities, these spacers offer precision, customization, and quick turnaround times, making them invaluable for prototyping and custom applications. Whether you’re working on aerospace projects, automotive innovations, or medical device development, choosing the right rapid prototype parts spacers can significantly impact your design process, product performance, and time-to-market.For more information on precision-engineered components and CNC machining services, visit our homepage. If you have any questions or need assistance in selecting the perfect rapid prototype parts spacers for your project, don’t hesitate to contact us. Our team of experts is always ready to help you find the best solution for your prototyping and manufacturing needs.