-
No.66 Gaojia, Xingfu Village, Sanqi Town, Yuyao, Ningbo,China
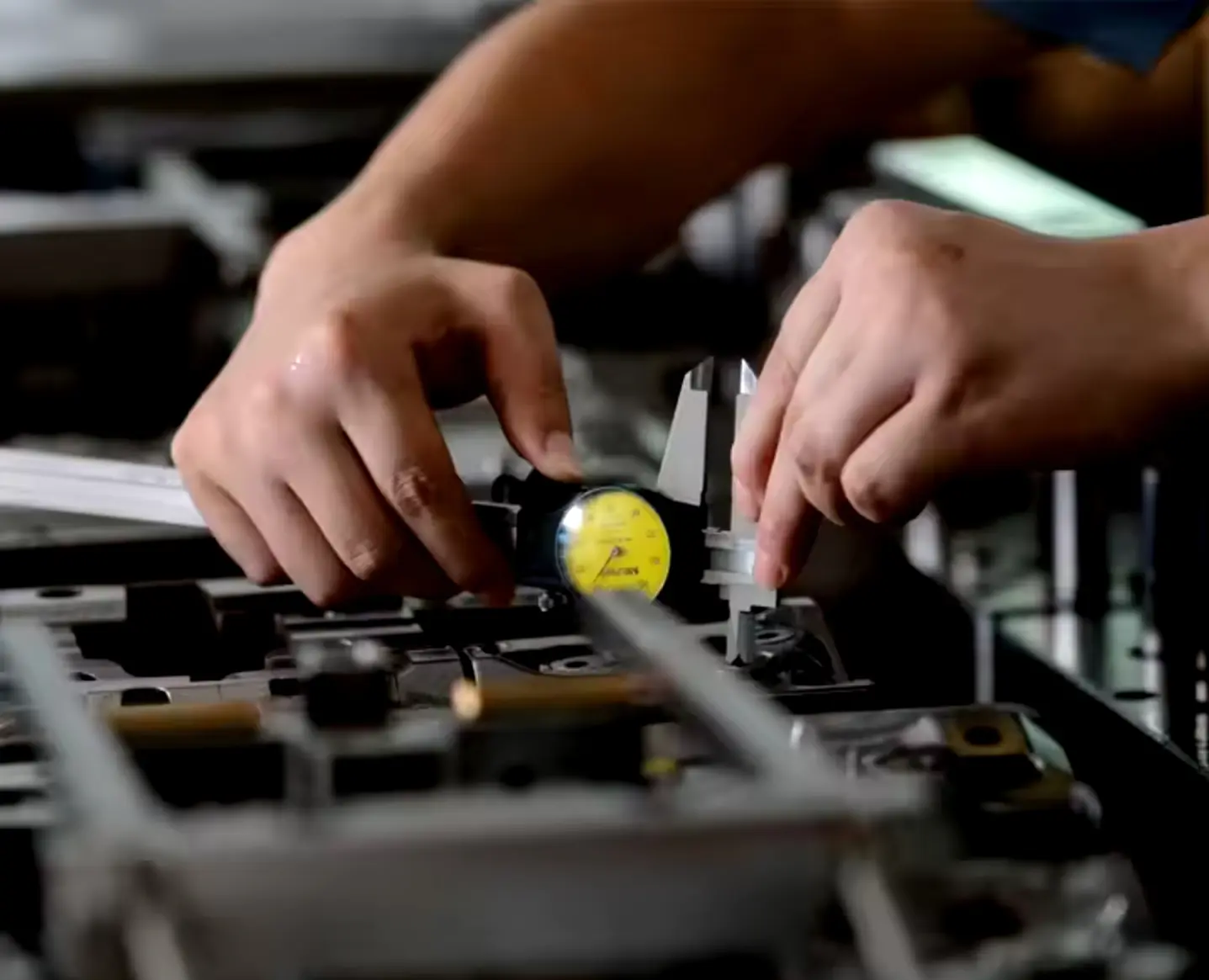
Progressive Die Stamping: Revolutionizing Metal Part Production
Progressive die stamping represents a cornerstone of modern manufacturing, offering unparalleled efficiency in producing metal parts at high volumes. This comprehensive guide explores how this innovative process transforms flat metal sheets into complex components, while maintaining precise tolerances and cost-effectiveness.
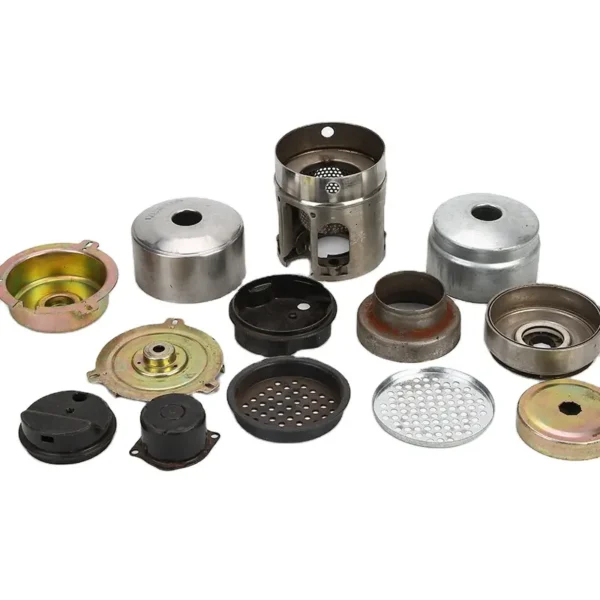
What Makes Progressive Die Stamping Different?
Progressive die stamping stands out from traditional stamping methods through its unique ability to perform multiple operations in sequence. Metal stamping processes have evolved significantly, with progressive die stamping leading the way in efficiency and precision. This advanced technique allows for continuous production, reducing labor costs while maintaining tight tolerances.Key advantages include:
- Automated continuous production
- Reduced handling between operations
- Higher production speeds
- Improved part consistency
- Lower per-piece costs
How Does the Progressive Die Stamping Process Work?
The process begins with a coil of metal sheet fed into the press. Through a series of carefully designed stamping stations, the material undergoes multiple operations:
- Initial Operations
- Blanking
- Piercing
- Forming
- Secondary Operations
- Bending
- Coining
- Threading
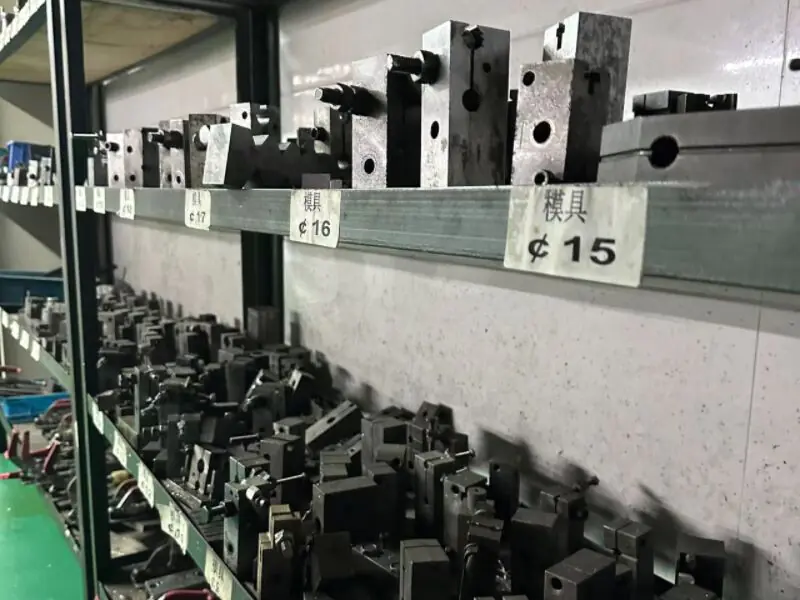
What Types of Parts Can Be Produced?
Progressive die stamping can create a wide range of components:
Industry | Common Applications | Key Features |
---|---|---|
Automotive | Brackets, clips | High strength |
Electronics | Connectors, shields | Precision |
Appliances | Housing components | Cost-effective |
Medical | Device components | Clean finish |
How Does Tool Design Impact Quality?
Tool design is crucial for successful progressive die stamping. Factors include:
- Material flow analysis
- Strip layout optimization
- Die station spacing
- Scrap removal systems
- Pilot hole placement
What Role Does Material Selection Play?
The choice of material significantly impacts the stamping process and final product quality. Custom metal stamping requires careful material consideration:
- Material thickness consistency
- Mechanical properties
- Surface finish requirements
- Cost considerations
- Formability characteristics
How Are Tolerances Maintained?
Maintaining tight tolerances requires:
- Process Controls
- Regular tool maintenance
- Material verification
- Quality checks
- Equipment Calibration
- Press alignment
- Feed system accuracy
- Sensor verification
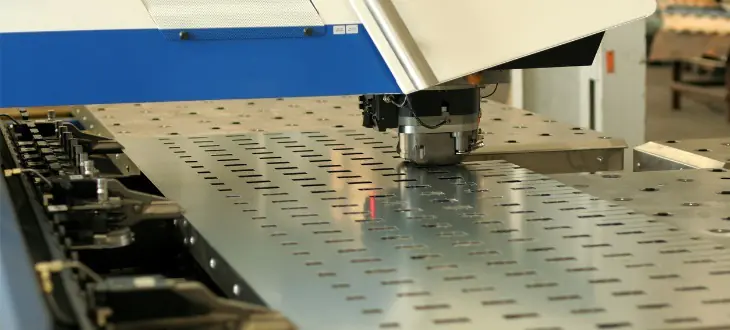
What Are the Cost Considerations?
Understanding cost factors helps optimize production:
- Initial tooling investment
- Material costs
- Production volume requirements
- Secondary operations
- Maintenance expenses
How Does Automation Enhance Production?
Modern progressive die stamping relies heavily on automation:
- Automated feed systems
- In-line quality monitoring
- Robotic part handling
- Integrated packaging systems
- Real-time process control
What Are Common Quality Challenges?
Quality challenges include:
- Material variations
- Tool wear
- Process consistency
- Part ejection issues
- Surface finish requirements
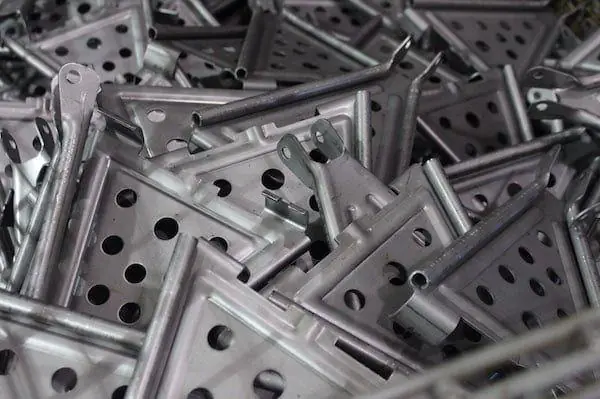
What’s the Future of Progressive Die Stamping?
The future holds exciting possibilities:
- Advanced materials processing
- Smart manufacturing integration
- Improved automation
- Enhanced quality control
- Sustainable practices
Key Takeaways:
- Progressive die stamping offers superior efficiency
- Tool design is crucial for success
- Material selection impacts quality
- Automation enhances productivity
- Quality control requires constant attention
- Cost optimization drives competitiveness