-
No.66 Gaojia, vila de Xingfu, cidade de Sanqi, Yuyao, Ningbo, China
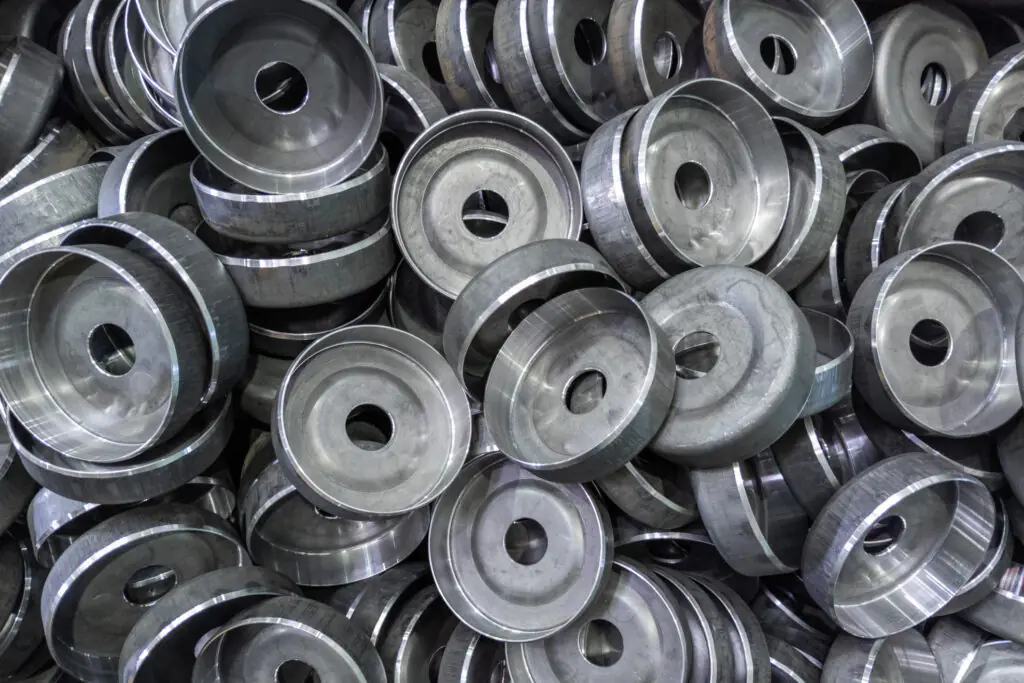
Dominando o processo de estampagem de metal: um guia abrangente para prensas de estampagem e o processo de estampagem
Este artigo fornece uma visão geral abrangente de estampagem de metal, com foco no processo de estampagem e o papel crucial do prensa de estampagem. Ele se aprofunda nas complexidades dessa técnica essencial de fabricação, explicando como ela funciona, suas vantagens e suas diversas aplicações. Seja você um engenheiro, um fabricante ou simplesmente curioso sobre como os objetos de metal do dia a dia são feitos, este guia oferece insights valiosos sobre o mundo da estampagem de metal, tornando-se uma leitura valiosa para qualquer pessoa interessada neste setor industrial fundamental. processo.
Índice
O que é estampagem de metal e como ela funciona?
Estamparia de metal é uma manufatura processo usado para converter plano folhas de metal em formas específicas. É um processo de conformação a frio que faz uso de ferramenta e superfícies de matriz para formar o metal. O processo começa com o matéria-prima, geralmente um metal bobina ou em branco, que é colocado em um prensa de estampagem. Dentro do imprensa, o ferramenta e morrer da forma metal para dentro do forma desejada. Isso pode envolver várias operações, como puncionamento, estampagem, dobra, cunhagem, gofragem e flangeamento.
O processo de estampagem é conhecido por sua eficiência, especialmente em produção de alto volume. Ele é capaz de produzir formas complexas com alta precisão e repetibilidade, o que o torna adequado para uma ampla gama de aplicações, desde pequenos componentes eletrônicos até grandes painéis de carroceria automotiva. Estamparia de metal é um processo versátil que pode funcionar com uma variedade de materiais metálicos, incluindo aço, alumínio, cobre e latão. Você pode ver estampagem de metal em ação no estampagem de metal página. A versatilidade e eficiência de estampagem de metal torná-lo uma pedra angular da fabricação moderna. Isto processo de formação desempenha um papel crucial em vários setores.
Explorando os diferentes tipos de prensas de estampagem
Prensas de estampagem são os cavalos de batalha do estampagem de metal processo. Estes máquinas aplicar a força necessária para moldar o metal em branco usando um ferramenta e morrer. Existem dois principais tipos de prensas de estampagem: prensas mecânicas e prensas hidráulicas.
Prensas mecânicas use um volante motorizado para armazenar energia e transferi-la para o carneiro, que então força o ferramenta para dentro do metal em branco. Eles são conhecidos por sua velocidade e são adequados para produções de alto volume. Prensas hidráulicas, por outro lado, usam pressão hidráulica para mover o aríete. Eles oferecem maior controle sobre o curso e são frequentemente usados para operações de estampagem profunda ou para trabalhar com materiais mais espessos. Prensas hidráulicas pode gerar forças muito maiores do que prensas mecânicas, mas eles são tipicamente mais lentos. A escolha entre um prensa mecânica e um prensa hidráulica depende do específico estampagem aplicação, incluindo o tipo de metal, a complexidade da peça e o volume de produção necessário. Algumas operações usam custom ferramenta e conjuntos de matrizes.
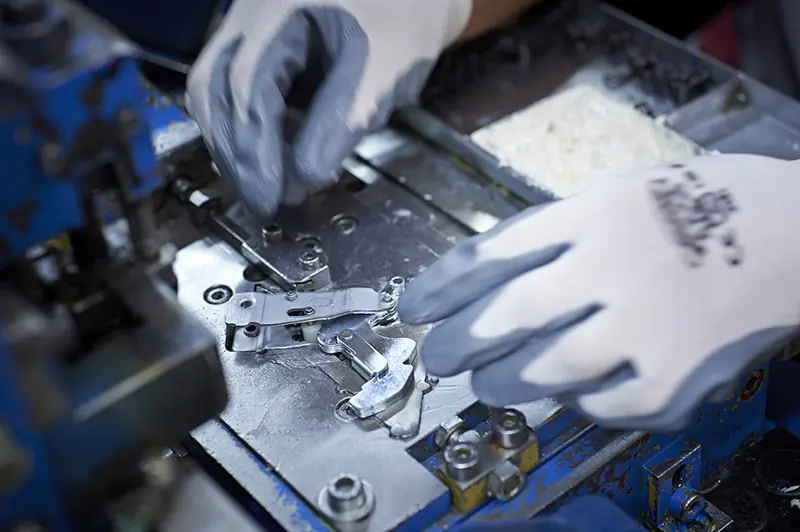
Quais são os tipos comuns de operações de estampagem?
Diversos tipos comuns de estampagem operações são usadas em estampagem de metal, cada um servindo a um propósito específico na formação do peça de metal. Essas operações podem ser realizadas individualmente ou em combinação, dependendo da complexidade da peça e do resultado desejado. Aqui está uma olhada em algumas das técnicas mais prevalentes:
- Obturação: Esta operação consiste em cortar a chapa metálica para criar o contorno ou a silhueta da parte desejada. A peça cortada, ou em branco, é então usado para processamento posterior. A periferia do corte é o contorno final da peça.
- Socos: Semelhante ao blanking, mas a parte cortada é sucata e o restante tira de metal progride para a próxima operação. A perfuração cria furos ou outras formas no folha de metal.
- Dobrando: Como o nome sugere, esta operação consiste em dobrar o metal ao longo de um eixo reto para criar ângulos ou curvas.
- Cunhagem: Este processo usa alta pressão para criar características elevadas ou rebaixadas no metal superfície, como letras, logotipos ou designs complexos.
- Relevo: Semelhante à cunhagem, a gravação em relevo cria um desenho em relevo na metal superfície, geralmente para fins decorativos ou de identificação.
- Desenho: Esta operação constitui o metal em uma peça cilíndrica ou em forma de caixa, puxando-a através de uma matriz.
- Obturação fina: Proporciona bordas excepcionalmente suaves e tolerâncias rigorosas, sendo usado para peças de precisão.
Estes são apenas alguns exemplos dos muitos estampagem operações usadas na indústria. Cada operação requer ferramentas e expertise específicas para garantir que o resultado desejado seja alcançado.
Compreendendo o papel da ferramenta e da matriz na estampagem de metais
Em estampagem de metal, o ferramenta e a matriz são componentes essenciais que ditam a forma e a qualidade da peça acabada. ferramenta, também conhecido como soco, é o componente macho que aplica força ao metal em branco. O dado é o componente feminino que suporta o metal e fornece a forma desejada.
O projeto e a construção do ferramenta e morrer são essenciais para o sucesso do processo de estampagem. O o design deve considere fatores como o tipo de metal, a complexidade da peça, as tolerâncias necessárias e a prensa de estampagem sendo usado. Matrizes de estampagem são normalmente feitos de aço temperado para suportar as altas pressões e forças repetitivas envolvidas estampagem. Um bem projetado ferramenta e o conjunto de matrizes pode produzir milhares ou até milhões de peças com qualidade e precisão consistentes. ferramenta e as matrizes são frequentemente feitas sob medida para cada peça específica, tornando estampagem de metal personalizada um campo especializado que requer um alto nível de conhecimento. Um mal projetado ferramenta resultará em um componente malfeito.
O que é estampagem progressiva e como ela se diferencia de outros métodos?
Estampagem progressiva é um conformação de metais método que utiliza uma série de estações de estampagem para executar várias operações em um tira de metal. À medida que a tira se move através do dado progressivo, cada estação executa um corte diferente, soco, dobrar ou outra operação. Isso permite a criação de peças complexas com alta precisão e eficiência. É uma operação muito específica tipo de estampagem.
Comparado com outros métodos de estampagem, como estágio único estampagem onde cada operação requer uma operação separada imprensa e morrer, estampagem progressiva oferece várias vantagens. É mais rápido porque várias operações são realizadas simultaneamente, é mais econômico para produção de alto volume. Esse método de estampagem reduz o desperdício de material porque a peça permanece presa ao tira de metal até a fase final. No entanto, estampagem progressiva requer um processo mais complexo e caro ferramenta e configuração da matriz. O investimento inicial é maior, mas a economia de custos a longo prazo pode ser significativa para grandes tiragens de produção. dado progressivo em si é uma maravilha da engenharia, com cada estação cuidadosamente projetada e sincronizada para trabalhar em harmonia com as outras. É uma estação mais complexa operação de estampagem.
Como a indústria automotiva utiliza a estampagem de metal?
O automotivo a indústria é uma das maiores usuárias de estampagem de metal. Esse processo de formação é usado para criar uma ampla gama de componentes de veículos, desde painéis de carroceria e peças estruturais até suportes e suportes menores. Um exemplo é carimbado painéis de portas de automóveis, que são moldados a partir de planos folhas de metal usando grande prensas de estampagem e matrizes especializadas.
Estamparia de metal oferece diversas vantagens para automotivo fabricação. Permite a produção de peças leves, porém fortes, contribuindo para a eficiência de combustível e segurança. É também um método econômico para produzir grandes quantidades de peças idênticas com alta precisão, o que é essencial para a produção em massa de veículos. automotivo a indústria depende de estampagem de metal para atender aos seus rigorosos padrões de qualidade e demandas de produção. Avanços em estampagem de metal tecnologia, como o uso de aços avançados de alta resistência e processos automatizados prensas de estampagem, continuam a impulsionar a inovação na fabricação automotiva. Muitas empresas de automóveis usam estampagem de metal personalizada para peças específicas.
Quais são as principais considerações na estampagem de metal personalizada?
Estampagem de metal personalizada envolve a criação de algo único peças de metal adaptado às necessidades específicas do cliente. Isto processo de fabricação muitas vezes requer uma colaboração estreita entre o cliente e o carimbo de metal para garantir que o produto final atenda às especificações desejadas. Várias considerações importantes entram em jogo estampagem de metal personalizada projetos.
Primeiro, o design da peça deve ser otimizado para o processo de estampagem. Isso envolve considerar fatores como as propriedades do material, a complexidade da forma e as tolerâncias necessárias. Em segundo lugar, o ferramenta e a matriz deve ser projetada e fabricada de acordo com os mais altos padrões para garantir a precisão e a consistência do carimbado partes. Terceiro, o apropriado prensa de estampagem e outros equipamentos devem ser selecionados com base nos requisitos específicos do projeto. Finalmente, medidas de controle de qualidade devem ser implementadas em todo o processo de estampagem para garantir que as peças acabadas atendam às especificações do cliente. Estampagem de metal personalizada requer um alto nível de especialização e atenção aos detalhes. Existem muitos serviços de estampagem de metal disponível.
O que está envolvido no processo de fabricação de metal?
Fabricação de metais é um termo amplo que abrange vários processos usados para moldar, cortar e montar metal em um produto final. Estamparia de metal é apenas uma das muitas técnicas utilizadas em fabricação de metais. Outros comuns fabricação Os processos incluem corte, dobra, soldagem, usinagem e acabamento.
O específico processo de fabricação usado depende do tipo de metal, a forma e o tamanho desejados da peça e as tolerâncias necessárias. Para exemplo, o corte pode ser feito usando vários métodos, como cisalhamento, serragem, corte a laser ou corte a plasma. A dobra pode ser obtida usando freios de prensa ou outros métodos de dobra máquinas. A soldagem é frequentemente usada para unir múltiplos metal peças juntas. Operações de usinagem, como fresamento, furação e torneamento, podem refinar ainda mais a forma e as dimensões da peça. O produto acabado da fabricação de metais é frequentemente um componente usado para compor um produto maior.
O processo de fabricação geralmente começa com desenhos de engenharia ou modelos CAD que fornecem especificações detalhadas para a peça. Esses projetos orientam a seleção de materiais, a escolha de fabricação técnicas e o sequenciamento das operações. Fabricação de metais frequentemente envolve uma combinação de diferentes processos para atingir o produto final. Para exemplo, um invólucro de metal pode envolver corte chapa metálica para dimensionar, estampagem ou perfurar furos e outras características, dobrando o metal para formar o formato do gabinete, soldando as costuras e aplicando um acabamento. Gabinete para estampagem de chapas de aço é um bom exemplo.
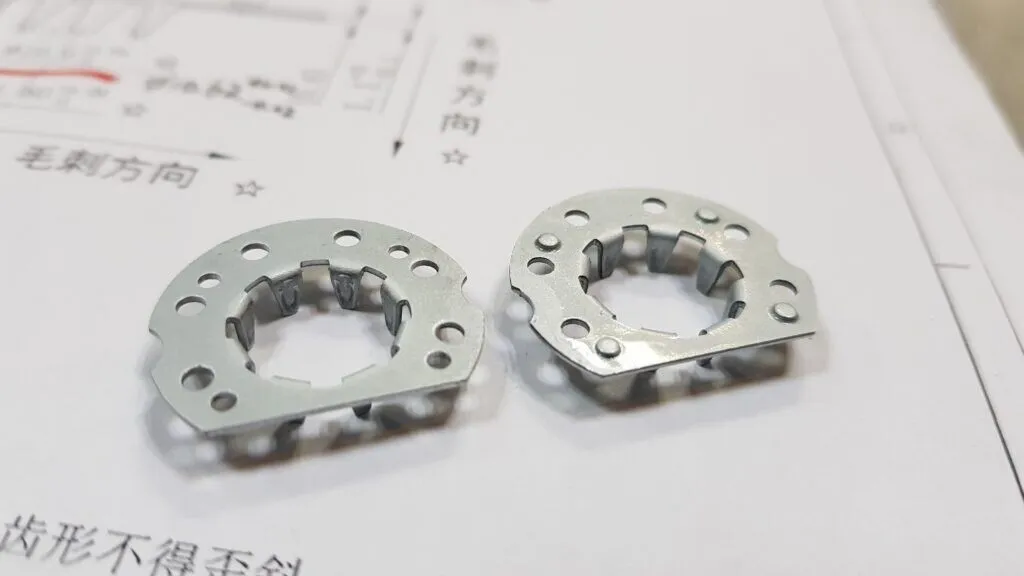
Explorando diferentes tipos de prensas de estampagem: mecânicas e hidráulicas
Conforme mencionado anteriormente, existem dois principais tipos de prensas de estampagem: mecânico e prensas hidráulicas. Cada tipo tem suas próprias características, vantagens e limitações únicas, tornando-os adequados para diferentes aplicações de estampagem.
Prensas mecânicas são conhecidos por sua velocidade e eficiência. Eles usam um volante para armazenar energia e uma embreagem para engatar o imprensa acidente vascular cerebral. Eles são tipicamente mais rápidos do que prensas hidráulicas e são bem adequados para produção de alto volume de peças mais simples. No entanto, eles oferecem menos controle sobre o curso e a força em comparação com prensas hidráulicas. A tonelagem, ou capacidade de força, de um prensa mecânica é mais alto na parte inferior do curso, tornando-os menos ideais para operações de estampagem ou conformação profunda que exigem força constante durante todo o curso.
Prensas hidráulicas, por outro lado, usam cilindros hidráulicos para gerar força. Eles oferecem maior controle sobre o imprensa curso, velocidade e força, tornando-os adequados para uma gama mais ampla de aplicações, incluindo estampagem profunda, conformação de formas complexas e trabalho com materiais mais espessos ou de alta resistência. materiais metálicos. Prensas hidráulicas podem fornecer força constante durante todo o curso, o que é vantajoso para certas operações de conformação. Eles também são capazes de lidar com tonelagens maiores do que prensas mecânicas. No entanto, eles são normalmente mais lentos do que prensas mecânicas e pode exigir mais manutenção. Você pode aprender mais sobre prensas hidráulicas no Dissipador de calor de alumínio personalizado página.
Compreendendo o papel do corte fino na estampagem de metais de precisão
Obturação fina é um especialista processo de estampagem que produz peças com bordas excepcionalmente suaves, tolerâncias apertadas e alta precisão. Ao contrário das convencionais estampagem, que pode deixar bordas ásperas ou cortadas, obturação fina cria peças que muitas vezes não requerem operações de acabamento secundário. Isso o torna um processo ideal para produzir precisão componentes metálicos usado em indústrias como automotivo, aeroespacial e dispositivos médicos. Isto processo é frequentemente mais lento que outros métodos.
O obturação fina processo utiliza uma tripla ação especializada imprensa que incorpora um anel de impacto em forma de V para segurar o metal firmemente no lugar durante a operação. Isso evita que metal de rasgar ou deformar, resultando em limpeza, arestas afiadas. Obturação fina pode produzir peças com tolerâncias tão apertadas quanto +/- 0,01 mm e planicidade de até 0,005 mm, dependendo do material e da geometria da peça. É particularmente adequado para produzir peças pequenas e intrincadas com formas complexas.
Enquanto obturação fina oferece precisão superior e qualidade de ponta, é normalmente mais caro do que o convencional estampagem devido ao equipamento especializado e ferramental necessário. No entanto, a eliminação de operações secundárias, como rebarbação ou retificação, pode frequentemente compensar os custos iniciais mais altos, tornando-se uma solução econômica para certas aplicações. Isso processo de formação é usado quando é necessária alta precisão.
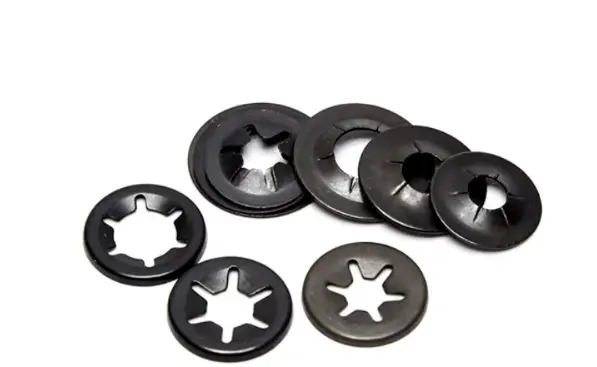
Principais conclusões:
- Estamparia de metal é versátil processo de fabricação que utiliza prensas e matrizes para transformar planos folhas de metal em formas desejadas.
- O processo de estampagem envolve várias operações como estampagem, puncionamento, dobra, cunhagem e estampagem, que podem ser realizadas individualmente ou em combinação.
- Prensas de estampagem são mecânicos ou hidráulicos, cada um com suas próprias vantagens e limitações em termos de velocidade, força e controle.
- Estampagem progressiva é um método altamente eficiente que realiza múltiplas operações em um tira de metal à medida que se move através de uma série de estações de estampagem.
- O automotivo a indústria é uma grande utilizadora de estampagem de metal, empregando-o para produzir uma ampla gama de componentes, desde painéis de carroceria até peças estruturais.
- Estampagem de metal personalizada envolve a criação de algo único peças de metal adaptado às necessidades específicas do cliente, exigindo design, ferramentas e controle de processo cuidadosos.
- Fabricação de metais abrange vários processos, incluindo corte, dobra, soldagem, usinagem e acabamento, muitas vezes usados em combinação para criar um produto final.
- Obturação fina é um especialista processo de estampagem que produz peças com bordas excepcionalmente suaves e tolerâncias rigorosas, ideais para componentes de precisão.
- A escolha entre diferentes estampagem métodos e imprensa tipos dependem de fatores como propriedades do material, complexidade da peça, volume de produção e considerações de custo.
- O processo de estampagem de metal é um processo complexo.
- Estamparia de metal é muito importante processo de fabricação.
- Existem muitos diferentes tipos de prensas de estampagem.
- Peças de estampagem de iluminação profundamente estampadas são um ótimo exemplo de um produto feito usando o processo de estampagem de metal.
- O processo de estampagem de metal é usado em muitos setores diferentes.
Ao compreender as complexidades de estampagem de metal, dos diferentes tipos de prensas e operações às técnicas especializadas como corte fino, os fabricantes podem tomar decisões informadas para otimizar seus processos de produção e atingir a qualidade e eficiência desejadas para suas aplicações específicas. Esse conhecimento é crucial para qualquer pessoa envolvida no design, produção ou aquisição de componentes metálicos.