-
No.66 Gaojia, Xingfu Village, Sanqi Town, Yuyao, Ningbo,China
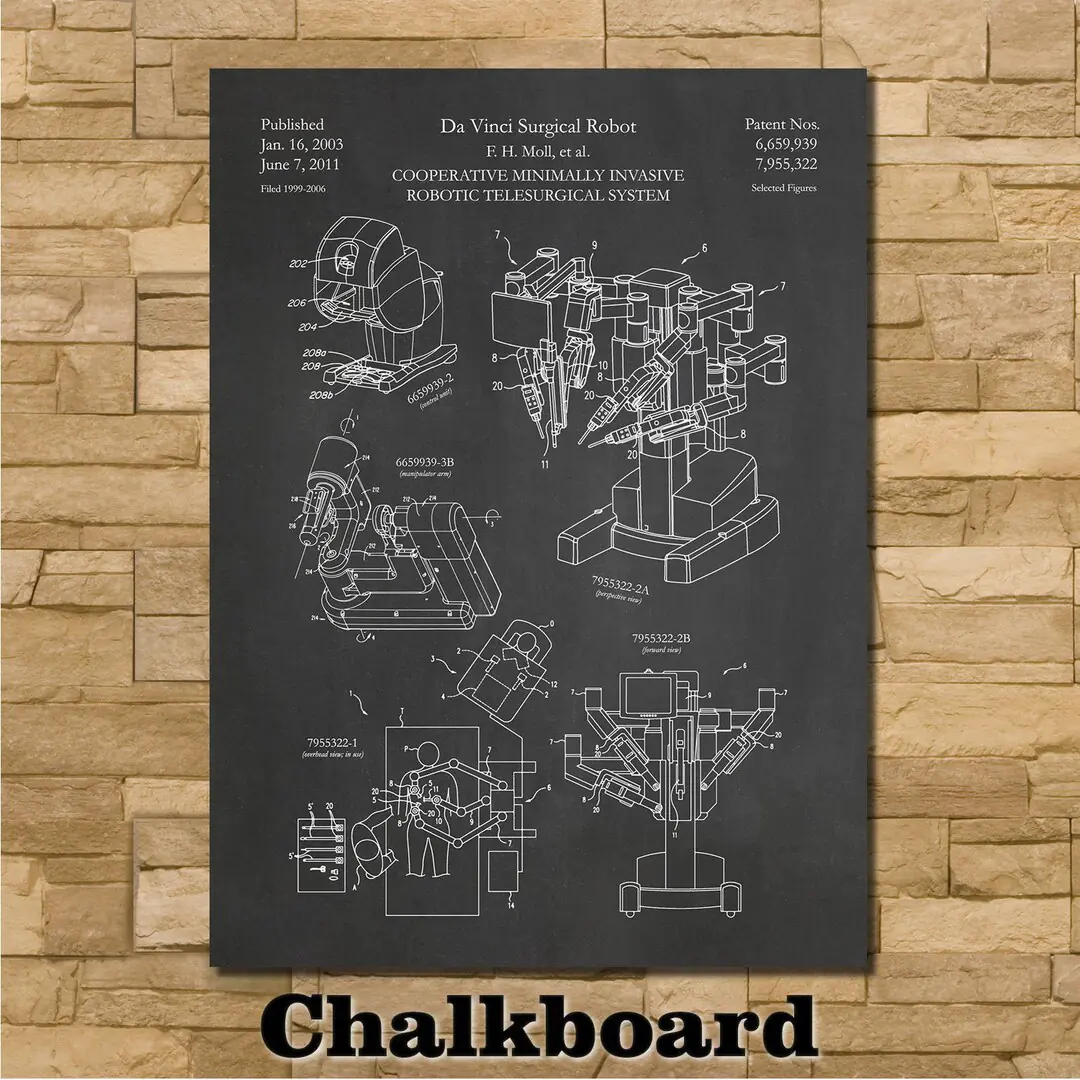
Revolutionizing Surgery: Metal Stamping in Robotic Surgical Instruments
The intersection of metal stamping and robotic surgical instruments represents a groundbreaking advancement in medical technology. This comprehensive guide explores how precision metal stamping is transforming the manufacturing of robotic surgical instruments, improving surgical outcomes, and driving innovation in minimally invasive procedures.
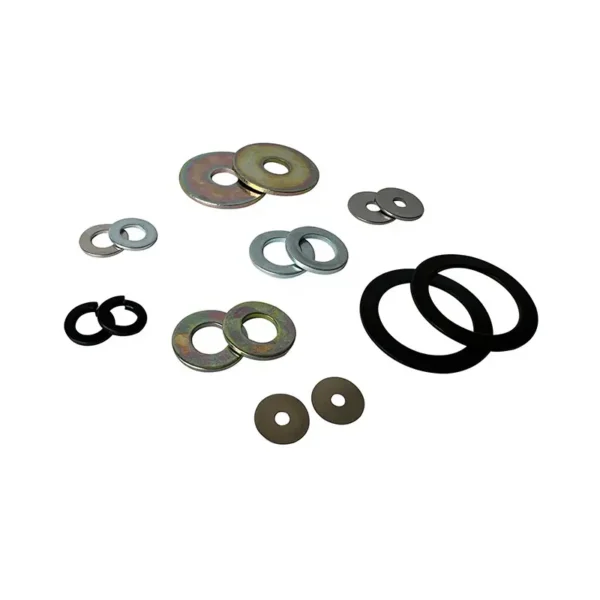
How is Metal Stamping Revolutionizing Robotic Surgical Instruments?
The manufacturing of robotic surgical instruments demands exceptional precision and reliability. Precision metal stamping plays a crucial role in creating components that meet strict medical-grade requirements. These parts must maintain tight tolerances while ensuring consistent performance during critical surgical procedures.Modern robotic surgical systems rely on precisely stamped components for:
- Instrument articulation mechanisms
- End-effector components
- Surgical tool housings
- Control system interfaces
What Makes Precision Critical in Surgical Robotics?
In robotic surgical instruments, tolerance levels are incredibly strict – often requiring accuracy within 0.005 inches or less. This level of precision ensures:
- Smooth operation of robotic arms
- Accurate instrument positioning
- Reliable control system response
- Consistent surgical performance
How Does Progressive Metal Stamping Support Surgical Innovation?
Progressive metal stamping has become integral to surgical instrument manufacturing. This efficient process allows for:
- High-volume production of complex parts
- Consistent quality across components
- Cost-effective manufacturing
- Reduced assembly requirements
What Role Does Material Selection Play?
The choice of materials for robotic surgical instruments is critical. Common materials include:
Material Type | Primary Benefits | Common Applications |
---|---|---|
Surgical Steel | Corrosion resistance | Instrument bodies |
Titanium Alloys | Lightweight strength | Actuator components |
Medical-grade Aluminum | Weight reduction | Housing elements |
How Are Quality Standards Maintained in Production?
Quality control in surgical instrument manufacturing involves:
- Rigorous Testing Protocols
- Dimensional verification
- Material certification
- Functional testing
- Documentation Requirements
- Process validation
- Material traceability
- Quality certifications
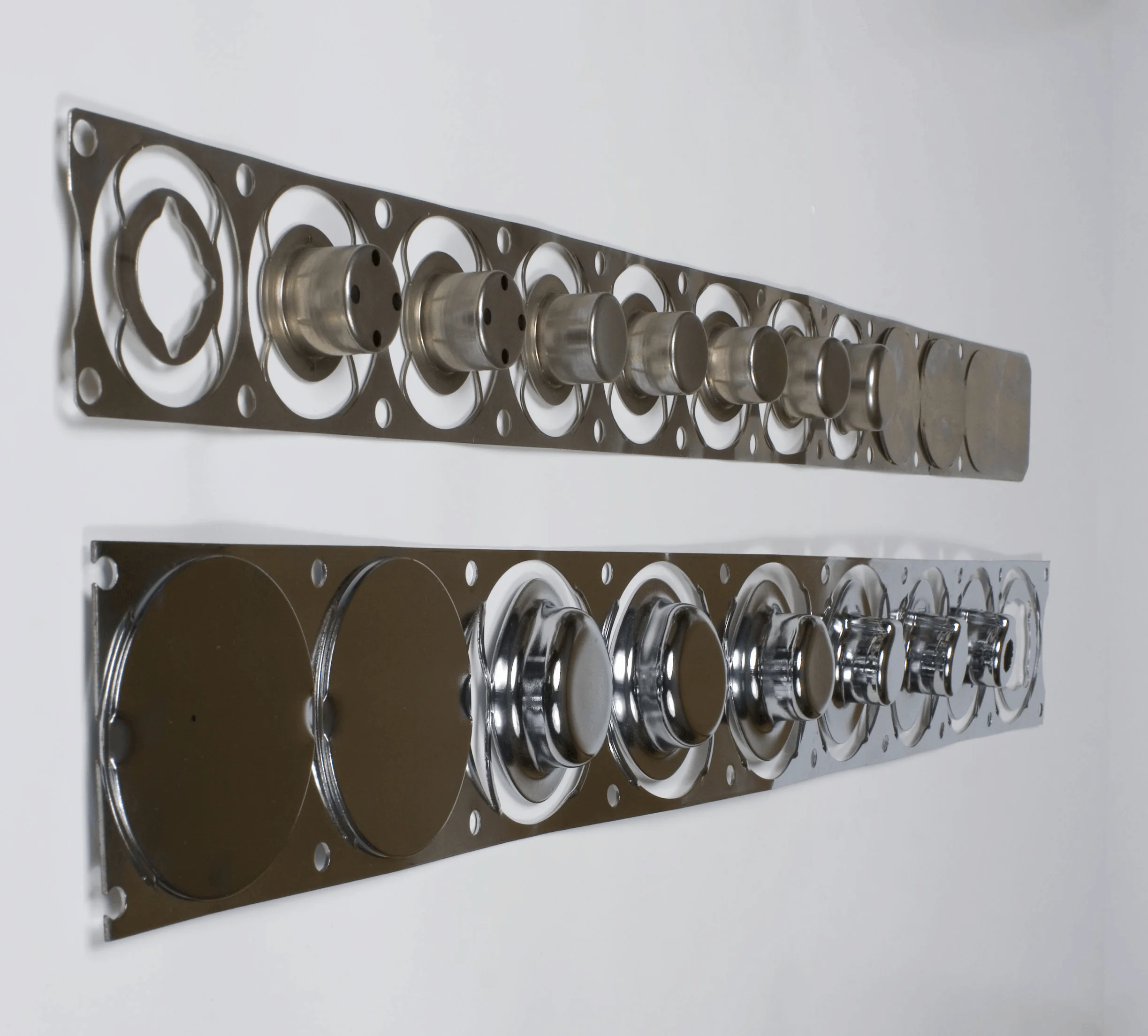
What Innovations are Driving Future Development?
The future of robotic surgical instruments relies heavily on advanced manufacturing techniques. Custom metal stamping solutions are evolving to meet these demands through:
- Advanced automation systems
- Enhanced material capabilities
- Improved process control
- Integration of smart technologies
How Does Sterilization Impact Design and Manufacturing?
Sterilization requirements significantly influence component design and material selection:
- Materials must withstand repeated sterilization
- Designs must prevent fluid trapping
- Surface finishes must maintain cleanliness
- Components must resist corrosion
What Are the Key Manufacturing Challenges?
Manufacturers face several challenges in producing robotic surgical instruments:
- Maintaining precise tolerances
- Ensuring material compatibility
- Meeting regulatory requirements
- Managing production costs
- Scaling production efficiently
How Do Toolmakers Ensure Precision?
Expert toolmakers employ various strategies to maintain precision:
- Advanced CAD/CAM systems
- High-precision machining
- Regular tool maintenance
- Quality verification processes
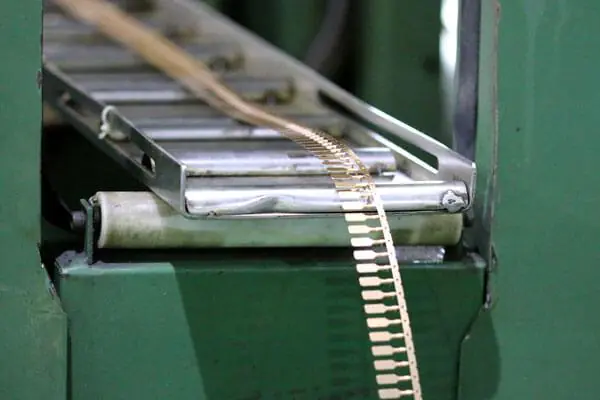
What’s Next for Robotic Surgical Instruments?
The future holds exciting possibilities:
- Enhanced miniaturization
- Improved articulation
- Better haptic feedback
- Advanced control systems
- Increased automation
Key Takeaways:
- Precision metal stamping is crucial for robotic surgical instruments
- Material selection significantly impacts performance
- Quality control is paramount throughout production
- Innovation drives continuous improvement
- Sterilization requirements influence design
- Future developments focus on enhanced capabilities