-
No.66 Gaojia, Xingfu Village, Sanqi Town, Yuyao, Ningbo,China
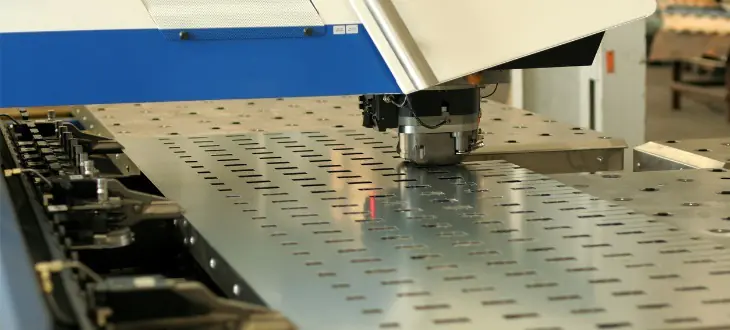
Sheet Metal Punching and Stamping: A Comprehensive Guide to Modern Metal Fabrication
Understanding sheet metal punching and stamping is crucial for anyone involved in metal fabrication. This comprehensive guide explores the differences, applications, and benefits of these essential metalworking processes. Whether you’re a manufacturer, engineer, or curious learner, this article will help you understand how these processes shape the products we use daily.
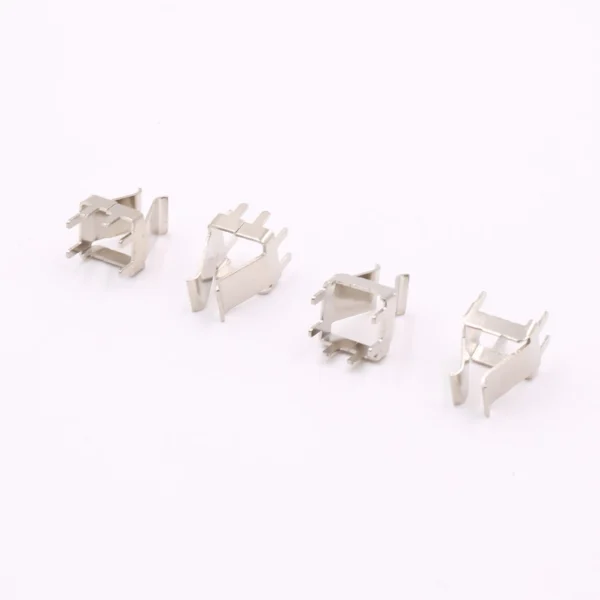
Precision-engineered metal stamping terminals demonstrating advanced manufacturing capabilities
What Is Sheet Metal Punching?
Sheet metal punching is a forming process that uses a punch press to create holes, shapes, and cutouts in metal sheets. This metalworking process involves:
- Using specialized tooling to create specific shapes
- Removing material through controlled force
- Creating precise holes and patterns
- Processing various metal thicknesses
The punch and die work together to create clean, accurate cuts in the workpiece.
How Does Metal Stamping Compare to Punching?
Metal stamping and punching are related but distinct processes:Stamping:
- Forms shapes without breaking the metal piece
- Creates three-dimensional forms
- Uses dies realizing any kind of shape
- Suitable for complex geometries
Punching:
- Removes material completely
- Creates holes and cutouts
- Uses punch presses and dies
- Focuses on material removal
Explore our precision metal components for examples of both processes.
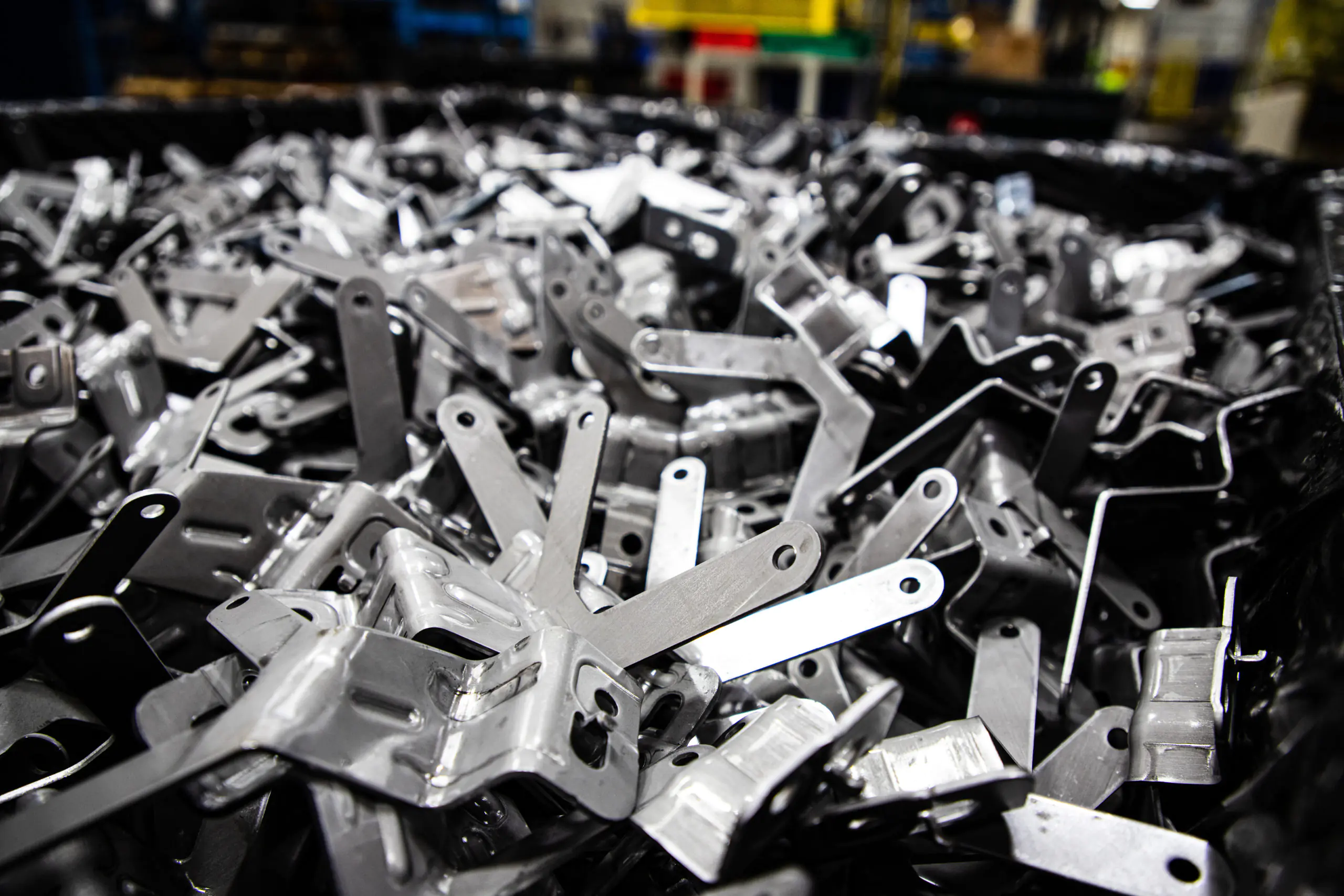
What Are the Key Applications of Sheet Metal Punching?
Sheet metal punching finds applications across a wide range of industries:
- Automotive:
- Body panels
- Structural components
- Mounting brackets
- Aerospace:
- Precision parts
- Ventilation components
- Support structures
View our metal stamping solutions for various applications.
How Does the Punching Process Work?
The punching process involves several key steps:
- Material positioning
- Tool alignment
- Force application
- Scrap removal
The process requires precise clearance between the punch and die for optimal results.
What Equipment Is Used in Sheet Metal Punching?
Modern punching operations utilize various equipment:Manual Equipment:
- Hand-powered punches
- Simple die sets
- Basic tooling
Automated Equipment:
- CNC punch presses
- Automated feed systems
- Sophisticated die sets
What Materials Can Be Punched?
Different materials require specific approaches:Common Materials:
- Steel
- Aluminum
- Copper
- Brass
- Stainless Steel
Learn about our stamping capabilities for various materials.
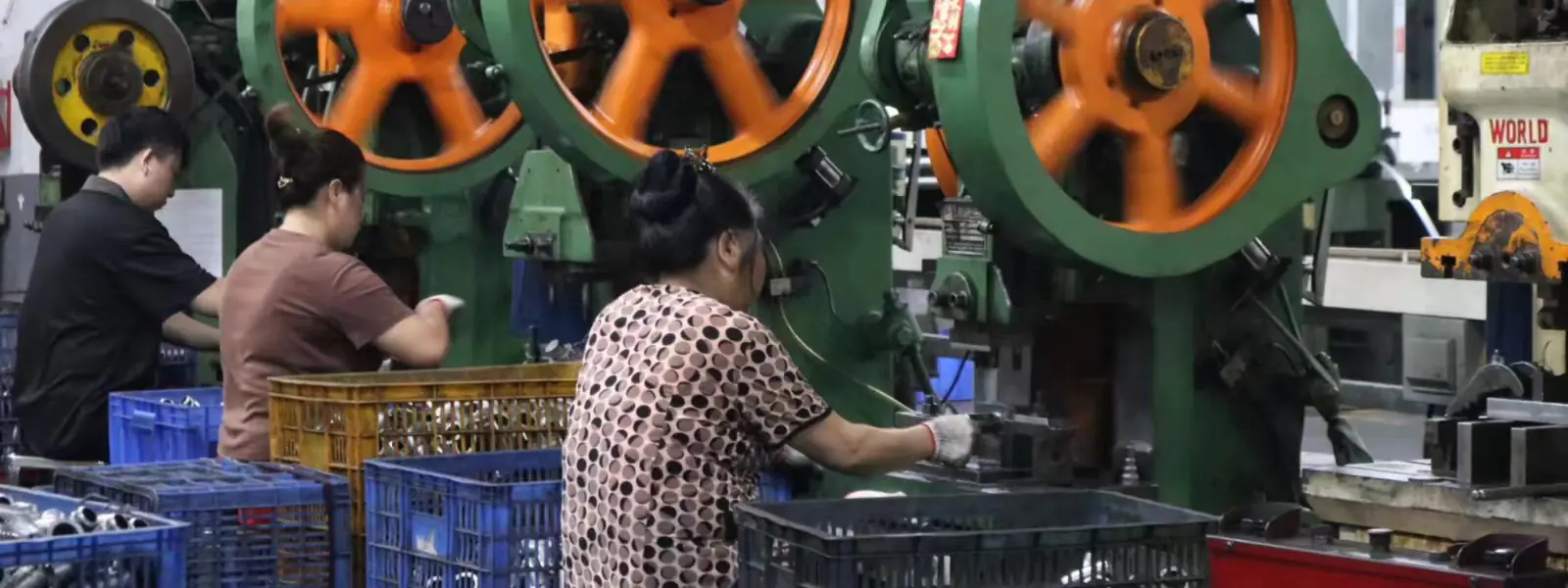
What Are the Quality Considerations?
Quality control in punching operations involves:
- Hole accuracy
- Edge quality
- Burr control
- Material deformation
How Does Automation Impact Punching Operations?
Modern automation has revolutionized punching:
- CNC control systems
- Automated material handling
- Program optimization
- Quality monitoring
What Are the Cost Factors?
Several factors influence punching costs:Setup Costs:
- Tooling investment
- Equipment selection
- Material handling systems
Operating Costs:
- Material usage
- Labor requirements
- Maintenance needs
What Future Trends Are Emerging?
The industry continues to evolve with:
- Advanced automation
- Smart manufacturing
- Sustainable practices
- New material developments
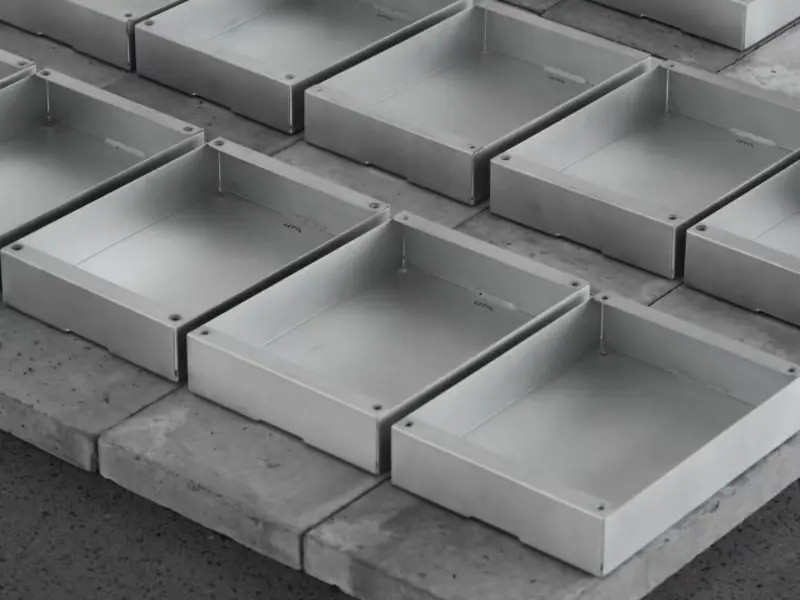
Key Takeaways:
• Punching and stamping serve different but complementary purposes • Material selection impacts process success • Automation enhances productivity and precision • Quality control is crucial for optimal results • Cost considerations vary by application • Future trends promise continued innovation • Equipment selection affects capabilities • Process understanding ensures successRemember that successful metal fabrication requires careful consideration of these processes and their applications in your specific context.