-
No.66 Gaojia, Xingfu Village, Sanqi Town, Yuyao, Ningbo,China
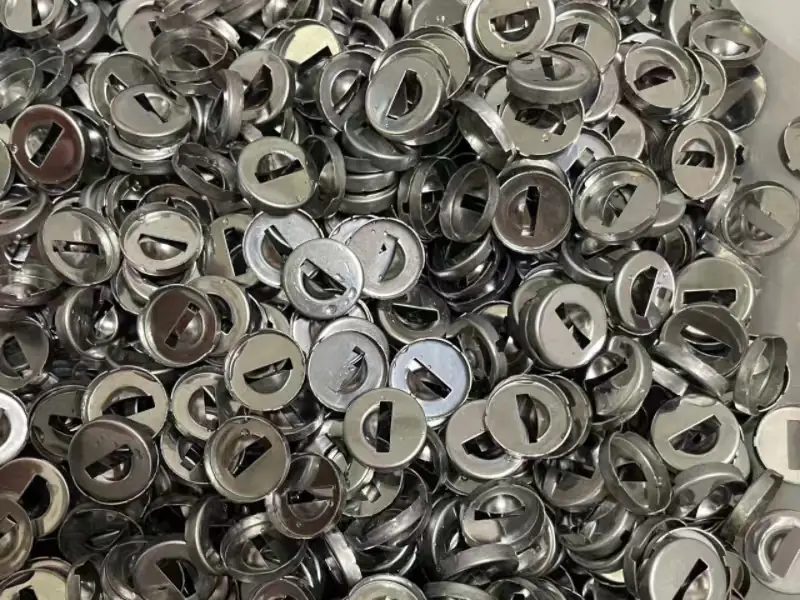
Sheet Metal Stamping vs Alternative Manufacturing Methods: A Complete Comparison Guide
In today’s competitive manufacturing landscape, choosing the right production method can make or break your project’s success. While sheet metal stamping remains a popular choice, understanding its alternatives is crucial for making informed decisions about your manufacturing process. This guide explores various alternatives to sheet metal stamping, helping you determine the best approach for your specific needs.
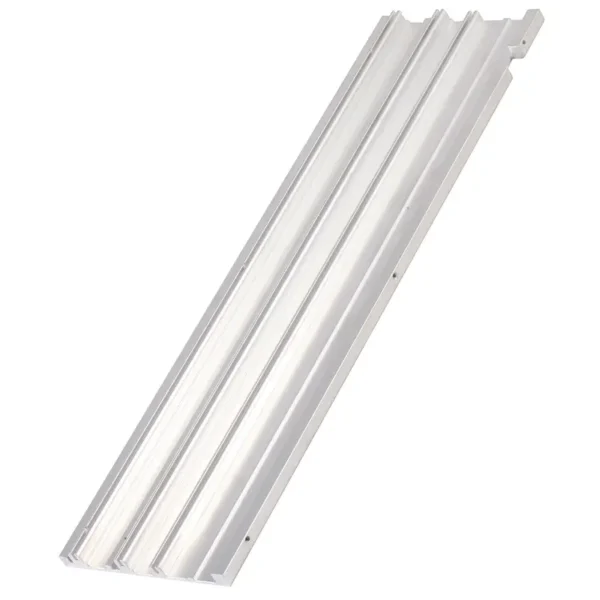
Advanced manufacturing techniques for precision metal components
What Is Traditional Sheet Metal Stamping?
Sheet metal stamping is a manufacturing process that transforms flat metal sheets into specific shapes using specialized tools and dies. This process involves:
- Cutting, forming, and shaping metal sheets
- Using mechanical force through stamping presses
- Creating precise, repeatable parts in high volumes
The metal stamping terminal products showcase the precision possible with traditional stamping methods.
Why Consider Alternatives to Sheet Metal Stamping?
Several factors might lead manufacturers to explore alternatives:
- Production volume requirements
- Tooling costs
- Design complexity
- Material utilization concerns
- Time constraints
Laser Cutting: A Modern Alternative
Laser cutting has emerged as a powerful alternative to traditional stamping, offering:
- High precision cutting capabilities
- Minimal material waste
- Quick setup times
- Flexibility for small batch production
The custom aluminum heatsink demonstrates the precision possible with laser cutting technology.
How Does Hydroforming Compare to Traditional Stamping?
Hydroforming uses fluid pressure to form metal parts and offers several advantages:Benefits:
- Complex geometries possible
- Reduced tooling costs
- Better material utilization
- Excellent part consistency
Limitations:
- Slower cycle times
- Higher equipment costs
- Limited material options
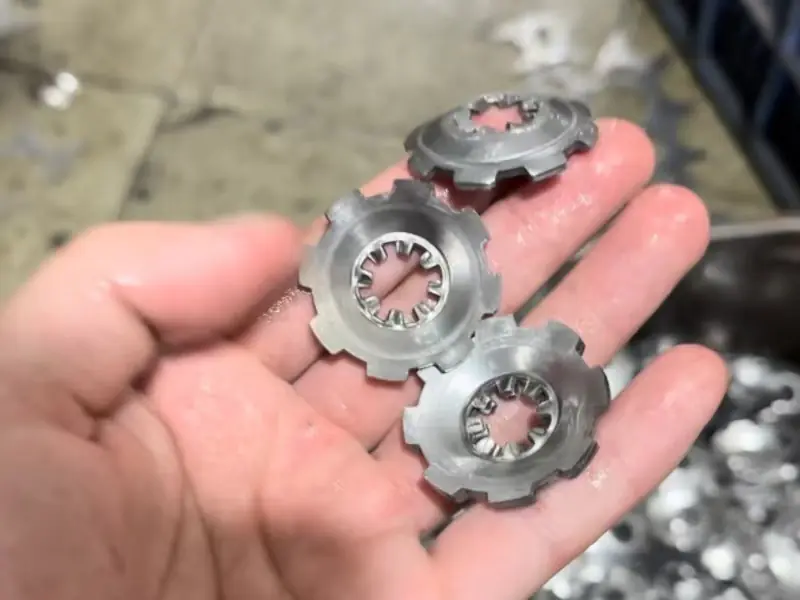
Is Die Casting a Viable Alternative?
Die casting presents unique advantages for certain applications:
Aspect | Die Casting | Sheet Metal Stamping |
---|---|---|
Setup Cost | Higher | Lower |
Production Speed | Very Fast | Fast |
Material Options | Limited | Extensive |
Surface Finish | Excellent | Good |
The Role of CNC Machining in Metal Forming
CNC machining offers:
- High precision capabilities
- Excellent for prototyping
- Flexibility in design changes
- Wide material compatibility
The mounting bracket parts showcase the versatility of modern manufacturing methods.
How Does Automation Impact Manufacturing Choices?
Automation considerations include:
- Initial investment costs
- Production volume requirements
- Labor savings potential
- Quality consistency
- Long-term ROI
What About Hybrid Manufacturing Solutions?
Many manufacturers combine multiple processes for optimal results:
- Laser cutting + forming
- Stamping + welding
- CNC machining + assembly
Cost Considerations: Making the Right Choice
Factor in these elements when choosing a manufacturing method:
- Tooling costs
- Production volume
- Material costs
- Labor requirements
- Quality control needs
Future Trends in Metal Manufacturing
Emerging technologies and trends include:
- Advanced automation systems
- Smart manufacturing integration
- Sustainable practices
- Hybrid manufacturing solutions
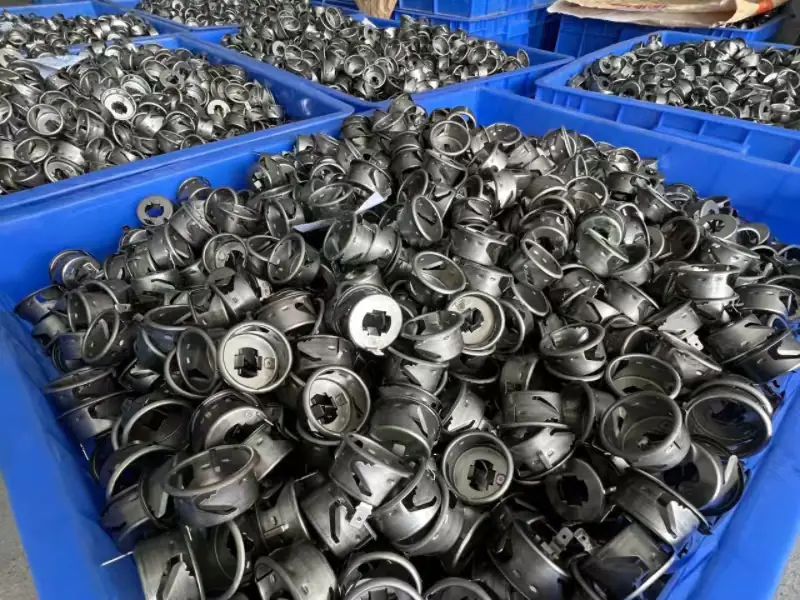
Key Takeaways:
• Consider production volume when choosing manufacturing methods • Evaluate total cost of ownership, not just initial investment • Match manufacturing process to product requirements • Consider combining multiple processes for optimal results • Factor in future scalability needsNeed help determining the best manufacturing method for your project? Contact us for expert guidance and support.
“The key to successful manufacturing is not just choosing the right process, but understanding how different methods can complement each other to achieve optimal results.”
Remember that each manufacturing method has its unique advantages and limitations. The best choice depends on your specific requirements, including production volume, material specifications, quality standards, and budget constraints.