-
No.66 Gaojia, Xingfu Village, Sanqi Town, Yuyao, Ningbo, Kina
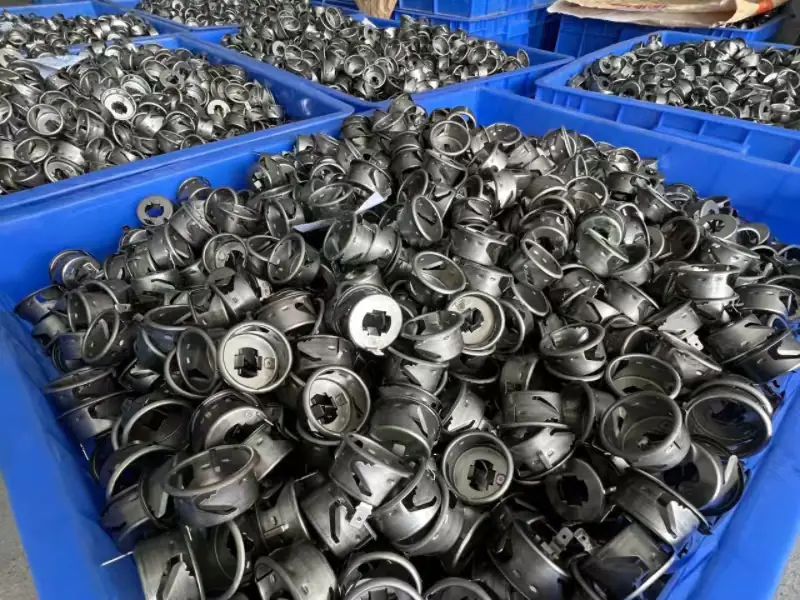
3 kritiska lösningar för att eliminera högvolymsmetallstämplingsdefekter
I dagens snabba tillverkningslandskap är förståelse och förebyggande av metallstämplingsdefekter avgörande för att upprätthålla kvalitet och effektivitet i högvolymproduktion. Den här omfattande guiden utforskar de vanligaste utmaningarna i metallstämplingsprocesser och ger praktiska lösningar för att hjälpa tillverkare att uppnå konsekventa resultat av hög kvalitet.
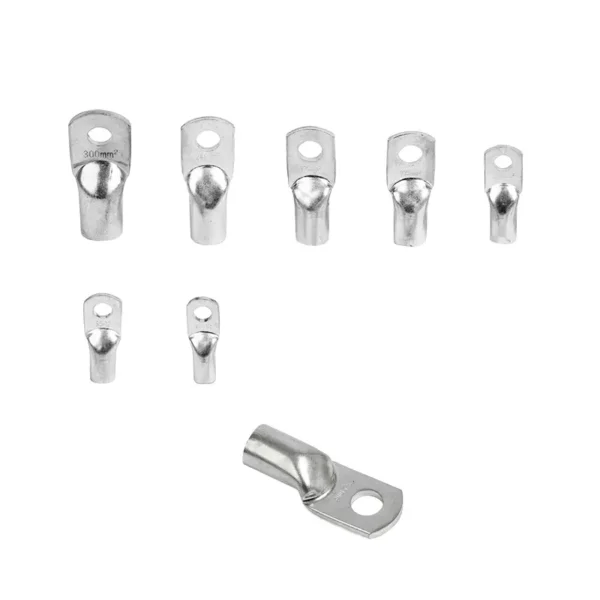
Precisionsmetallstämplingskomponenter kräver noggrann kvalitetskontroll
Vilka är de vanligaste metallstämplingsdefekterna?
Metallstämplingsdefekter kan avsevärt påverka produktionskvaliteten och effektiviteten. De vanligaste problemen inkluderar:
- Materialdeformation
- Dimensionella felaktigheter
- Ytbehandlingsproblem
- Verktygsslitage och brott
Dessa utmaningar blir särskilt uppenbara i högvolymproduktion av komplexa delar, där konsekvent produktion är avgörande.
Hur påverkar verktygsslitage stämplingskvaliteten?
Sambandet mellan verktygsslitage och stämplingskvalitet är direkt och betydande. Stämplingsformar upplever slitage under extrema förhållanden, vilket leder till:
- Minskad dimensionsnoggrannhet
- Inkonsekvent ytfinish
- Ökad stilleståndstid
- Högre produktionskostnader
Regelbundet underhåll och övervakning av stämplingsverktyg är avgörande för att upprätthålla kvalitetsstandarder.
Materialvalets roll i förebyggande av defekter
Att välja rätt material spelar en avgörande roll för att förebygga defekter. Tänk på dessa faktorer:
- Material duktilitet
- Höga krav på draghållfasthet
- Specifikationer för ytfinish
Produkter för tillverkning av plåt kräver noggrant materialval för att säkerställa optimala resultat.
Kvalitetskontrollåtgärder vid högvolymproduktion
Att implementera robusta kvalitetskontrollprocesser är avgörande för:
- Realtidsövervakning
- Statistisk processkontroll
- Dimensionell verifiering
- Ytkvalitetskontroll
Avancerad teknik för att förebygga defekter
Modern metallstämpling drar nytta av tekniska framsteg inklusive:
Teknologi | Förmån |
---|---|
Datorstödd design | Förbättrad noggrannhet |
Realtidsövervakning | Omedelbar feedback |
Automationssystem | Konsekventa resultat |
Varför är processkontroll kritisk?
Processkontroll vid metallstämpling kräver:
- Exakt parameterövervakning
- Regelbunden kalibrering av utrustning
- Standardiserade rutiner
- Dokumentation och spårning
Hur hanterar man vanliga utmaningar inom metallformning?
Effektiva lösningar inkluderar:
- Implementering av förebyggande underhållsscheman
- Regelbunden inspektion och byte av verktyg
- Operatörsutbildningsprogram
- Kvalitetssäkringsprotokoll
Automatiseringens inverkan på kvalitetssäkring
Modern stämplingsteknik dra nytta av automatisering genom:
- Minskade mänskliga fel
- Konsekvent utgång
- Förbättrad produktivitet
- Bättre kvalitetskontroll
Lösningar för att optimera stämplingsresultat
Tre nyckellösningar för att eliminera defekter:
- Avancerad processövervakning
- Datainsamling i realtid
- Förutsägande underhåll
- Kvalitetsspårningssystem
- Material- och verktygshantering
- Regelbundet verktygsunderhåll
- Optimalt materialval
- Lämpliga lagringsförhållanden
- Utbildning och dokumentation
- Omfattande operatörsutbildning
- Standard driftprocedurer
- Kvalitetskontrolldokumentation
Framtida trender inom kvalitetskontroll av metallstämpling
Tillverkningsindustrin fortsätter att utvecklas med:
- AI-driven kvalitetskontroll
- Smarta sensorer och IoT-integration
- Avancerad materialutveckling
- Förbättrade automationssystem
Viktiga takeaways:
- Implementera robusta kvalitetskontrollåtgärder
- Upprätthåll regelbunden verktygsinspektion och underhåll
- Välj lämpliga material för specifika applikationer
- Använd avancerad övervakningsteknik
- Investera i operatörsutbildning och dokumentation
- Håll dig uppdaterad med tekniska framsteg
Framgången för metallstämplingsoperationer med stora volymer beror på att man tar itu med dessa utmaningar proaktivt samtidigt som man behåller fokus på kvalitet och effektivitet. Genom att implementera dessa lösningar kan tillverkare avsevärt minska risken för defekter och förbättra sina produktionsresultat.