-
No.66 Gaojia, Xingfu Village, Sanqi Town, Yuyao, Ningbo,China
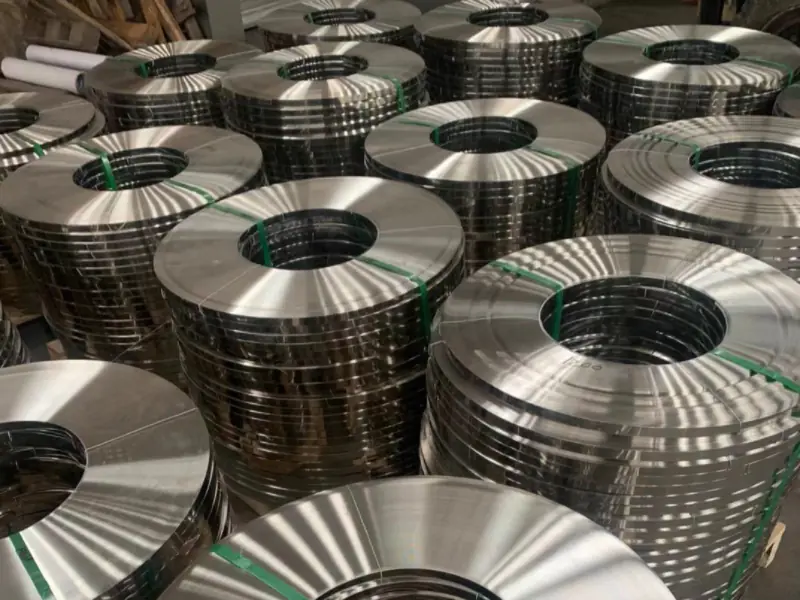
The Definitive Guide to Sheet Metal Stamping: Exploring Gauge, Thickness, and Processes
Metal stamping transforms flat metal sheets into functional components through precise manufacturing processes. This comprehensive guide explores everything from material selection to production techniques, helping you understand how thickness and gauge affect the stamping process. Whether you’re a manufacturer, engineer, or curious learner, this guide provides valuable insights into successful metal stamping operations.
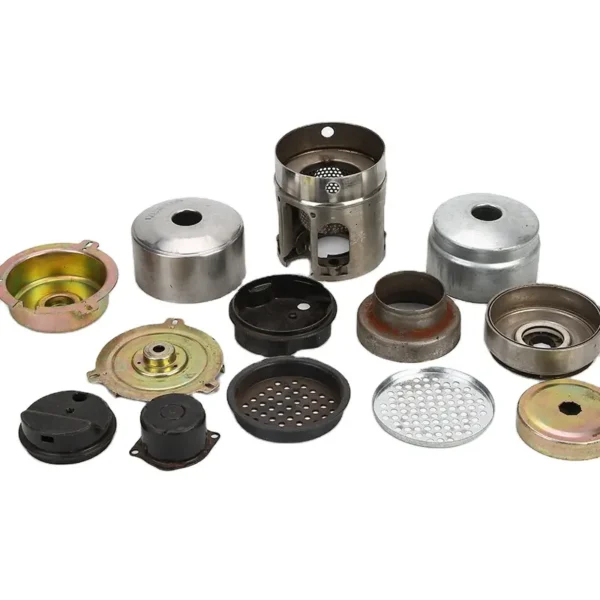
Precision metal stamping showcased in LED lighting components
Understanding Metal Gauge and Thickness in Stamping
Metal gauge refers to the standardized measurement of metal thickness. The relationship between gauge and actual thickness varies by material type:
Material | Gauge | Thickness (mm) |
---|---|---|
Steel | 24 | 0.6 |
Stainless Steel | 24 | 0.635 |
Aluminum | 24 | 0.508 |
How Does Material Selection Impact Stamping Success?
The choice of material significantly influences stamping outcomes. Common materials include:
- Stainless steel for corrosion resistance
- Carbon steel for structural strength
- Aluminum for lightweight applications
- Copper alloys for electrical conductivity
What Are the Critical Factors in Sheet Metal Thickness?
Several key considerations determine optimal sheet metal thickness:
- Part design requirements
- Structural integrity needs
- Weight considerations
- Cost constraints
- Manufacturing capabilities
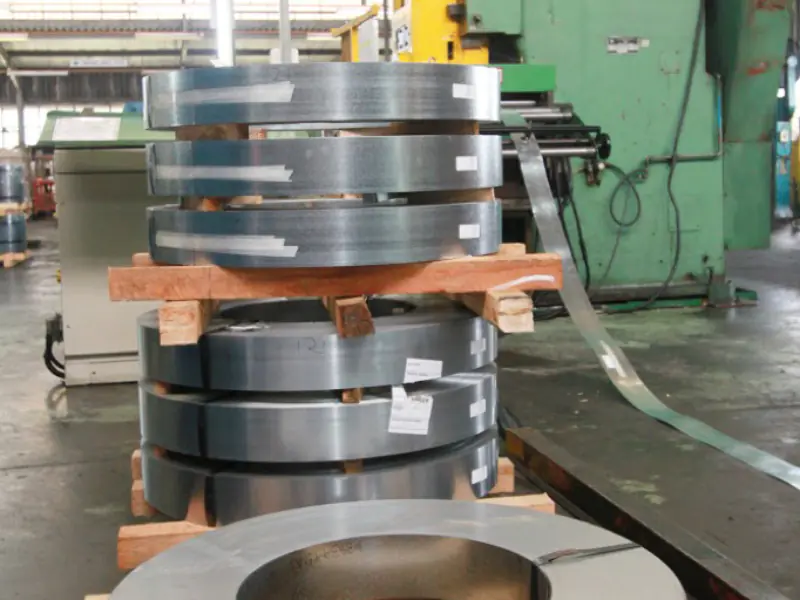
How Do Different Gauges Affect Stamping Operations?
The metal thickness affects various aspects of the stamping process:
Impact Areas:
- Tool design and wear
- Press tonnage requirements
- Production speed
- Quality control measures
- Cost per part
What Equipment Is Needed for Different Material Thicknesses?
Equipment requirements vary based on material thickness:
- Light gauge: Standard presses
- Medium gauge: Enhanced tooling
- Heavy gauge: Specialized machinery
- Ultra-thick: Custom equipment
What Are Common Quality Control Measures?
Quality assurance involves:
- Material certification
- Dimensional inspection
- Surface finish evaluation
- Structural testing
- Documentation
How to Optimize Stamping for Different Thicknesses?
Best practices include:
- Proper tool selection
- Appropriate press settings
- Material handling procedures
- Regular maintenance
- Process monitoring
What Are the Design Considerations for Various Gauges?
Design factors vary by thickness:
- Minimum bend radius
- Maximum draw depth
- Feature limitations
- Tolerance capabilities
- Surface finish requirements
What Industries Use Different Metal Thicknesses?
Applications vary by industry:
- Automotive: Multiple gauges
- Electronics: Light gauge
- Construction: Heavy gauge
- Aerospace: Precision thickness
- Consumer goods: Various thicknesses
How to Choose the Right Stamping Service Provider?
Consider these factors:
- Technical capabilities
- Equipment range
- Quality certifications
- Industry experience
- Cost-effectiveness
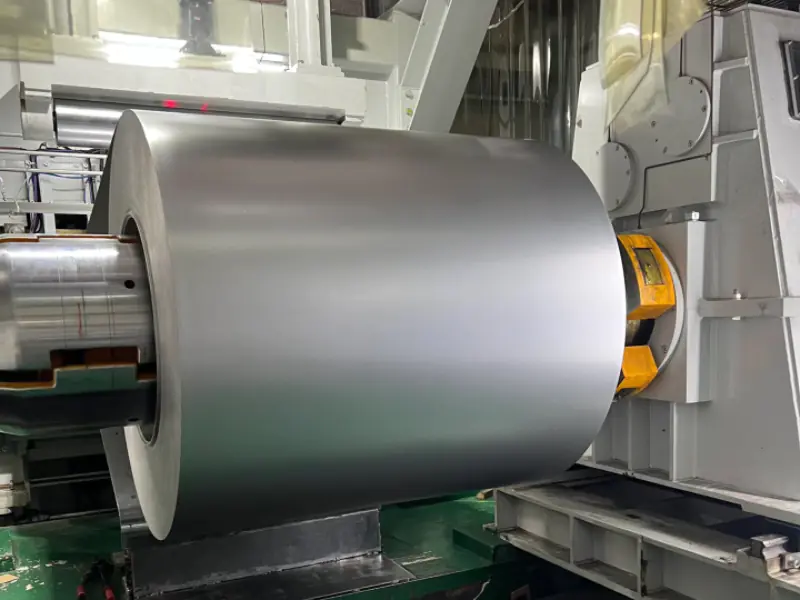
Key Takeaways
Remember these important points:• Material thickness affects all aspects of stamping • Proper equipment selection is crucial • Quality control measures vary by thickness • Design must account for material properties • Provider selection impacts success • Regular maintenance ensures quality
Need expert guidance on your metal stamping project? Contact our team to discuss your requirements and receive a detailed quote.