-
No.66 Gaojia, Xingfu Village, Sanqi Town, Yuyao, Ningbo,China
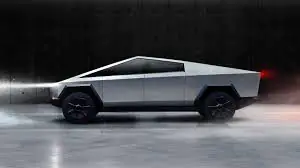
The Essential Role of Metal Stamping in Electric Vehicle Manufacturing: A Complete Guide
The rapid evolution of the electric vehicle (EV) industry has revolutionized automotive manufacturing, with metal stamping emerging as a crucial process in this transformation. This comprehensive guide explores how stamping technology is shaping the future of EV production, offering insights into processes, advantages, and industry trends that are essential for manufacturers, engineers, and industry professionals.
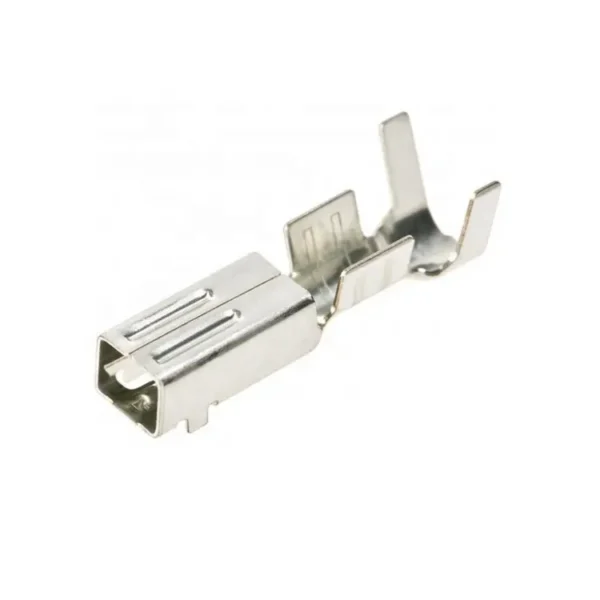
What Makes Metal Stamping Critical for Electric Vehicle Production?
The electric vehicle industry relies heavily on precision metal stamping to produce various components. This manufacturing process involves using specialized tools and presses to transform metal sheets into specific parts with high accuracy. Custom metal stamping services play a vital role in creating components that meet the exacting standards required for EVs.
How Does the EV Stamping Process Differ from Traditional Automotive Stamping?
Electric vehicle stamping requires greater precision and different specifications compared to conventional vehicle manufacturing. The process involves:
- Higher tolerance requirements
- Specialized materials for battery enclosures
- Advanced automation systems
- Enhanced quality control measures
What Are the Key Components Created Through EV Stamping?
Metal stamping produces numerous essential parts for electric vehicles:
- Battery enclosures
- Motor housings
- Electrical connectors
- Structural components
- Chassis elements
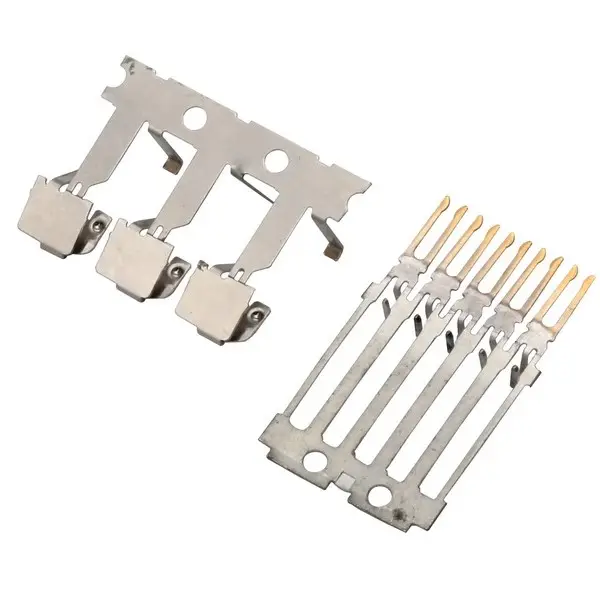
How Does Progressive Die Stamping Benefit EV Manufacturing?
Progressive die stamping offers several advantages for electric vehicle production:
- Increased production efficiency
- Reduced material waste
- Consistent quality across components
- Lower per-unit costs at high volumes
What Role Does Automation Play in EV Stamping?
Modern EV stamping facilities utilize advanced automation technologies:
- Computer-aided design (CAD) systems
- Robotic handling systems
- Automated quality inspection
- Smart manufacturing processes
What Are the Quality Control Measures in EV Stamping?
Quality assurance in EV stamping involves:
Aspect | Method | Importance |
---|---|---|
Dimensional Accuracy | 3D scanning | Critical |
Material Integrity | NDT testing | Essential |
Surface Quality | Visual inspection | Important |
Structural Strength | Load testing | Vital |
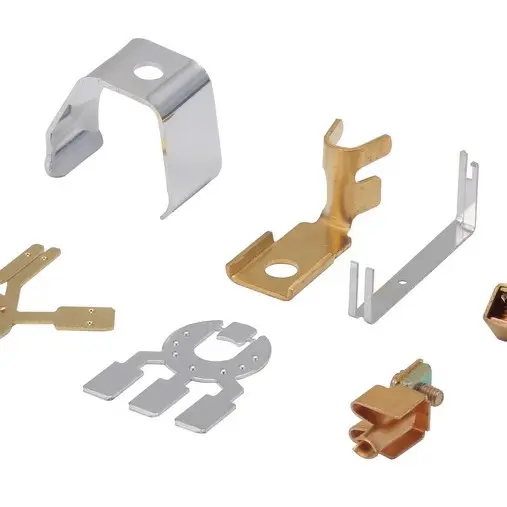
How Is Sustainability Addressed in EV Stamping?
The stamping industry for EVs emphasizes environmental responsibility through:
- Material optimization
- Energy-efficient processes
- Waste reduction strategies
- Recyclable materials usage
What Are the Future Trends in EV Stamping?
The future of EV stamping shows promising developments:
- Advanced materials integration
- Smart manufacturing solutions
- Increased automation
- Enhanced efficiency methods
What Challenges Face the EV Stamping Industry?
Key challenges include:
- Material cost fluctuations
- Technical skill requirements
- Equipment investment needs
- Quality standard maintenance
How to Choose the Right EV Stamping Partner?
Consider these factors when selecting a stamping manufacturer:
- Technical capabilities
- Quality certifications
- Production capacity
- Industry experience
- Innovation focus
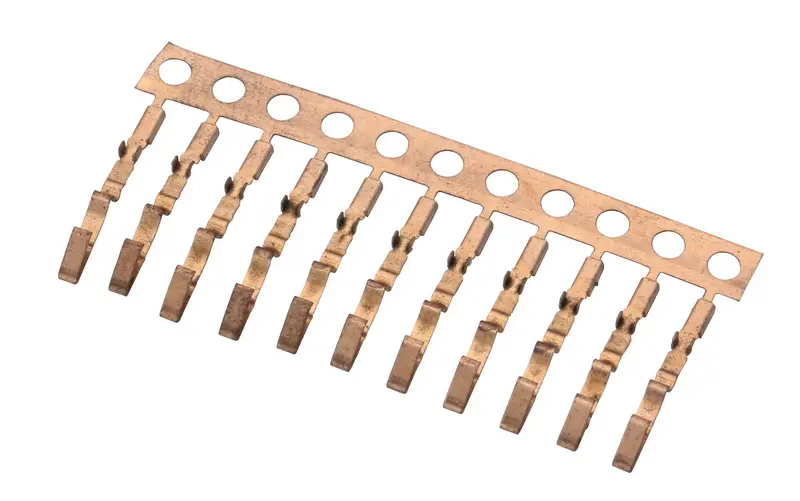
Key Takeaways:
- Metal stamping is fundamental to EV manufacturing
- Advanced automation enhances production efficiency
- Quality control is paramount
- Sustainability drives innovation
- Partner selection is crucial for success
Internal Links: