-
No.66 Gaojia, Xingfu Village, Sanqi Town, Yuyao, Ningbo,China
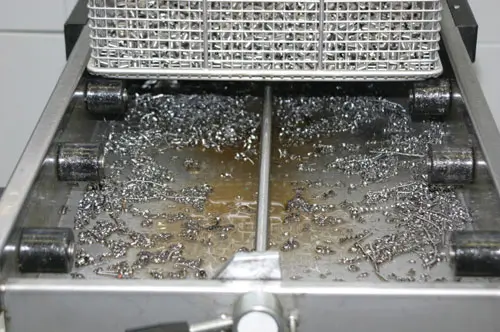
Ultrasonic Cleaning of Stainless Steel: Advantages and Disadvantages
Ultrasonic cleaning has revolutionized how we clean intricate parts, especially those made of stainless steel. This method, known for its efficiency and effectiveness, uses high-frequency sound waves to create microscopic bubbles that implode and dislodge contaminants. This article explores the ins and outs of ultrasonic cleaning for stainless steel, discussing its many benefits and potential drawbacks. We’ll delve into the science behind the process, explore its applications, and offer practical tips for achieving optimal cleaning results. Whether you’re in manufacturing, healthcare, or simply curious about this innovative cleaning technology, you’ll find valuable insights here.
What is Ultrasonic Cleaning?
Ultrasonic cleaning is a specialized cleaning method that uses high-frequency sound waves, typically between 20 and 40 kHz, to create cavitation bubbles in a liquid. These bubbles implode near the surface of an object submerged in the cleaning solution, generating tiny but powerful shock waves that dislodge dirt, grime, and other contaminants. Think of it as a microscopic power wash! Unlike traditional cleaning methods that rely on scrubbing or brushing, ultrasonic cleaning can reach even the most intricate and hard-to-access areas, making it ideal for cleaning complex parts. It is especially effective on stainless steel, a durable and corrosion-resistant material commonly used in various industries.
Ultrasonic cleaning offers a deep and thorough clean, removing even microscopic particles that other methods might miss. It is highly efficient and can significantly reduce cleaning time compared to traditional methods. Plus, it is environmentally friendly, often using less detergent and water than other cleaning techniques. Push Nut Fasteners, often made from stainless steel and requiring meticulous cleaning, highlight the efficacy of ultrasonic methods in intricate part preparation.
Advantages of Ultrasonic Cleaning
Ultrasonic cleaning offers numerous advantages, making it a popular choice across various industries:
- Thorough Cleaning: The cavitation bubbles reach even the tiniest crevices and blind holes, ensuring a deep and thorough clean that surpasses traditional chemical cleaning. It’s the best choice for objects with intricate shapes.
- Efficient and Fast: Ultrasonic cleaning significantly reduces cleaning time compared to manual scrubbing or soaking. It’s a speedy solution for busy industries.
- Gentle on Parts: While the microscopic bubbles are powerful against dirt, they are gentle on the parts being cleaned, minimizing the risk of damage or deformation. This is especially important for delicate components.
- Versatile Applications: From medical instruments to automotive parts, ultrasonic cleaning finds applications in various industries. It’s adaptable to different materials and cleaning tasks.
- Environmentally Friendly: Ultrasonic cleaning often uses less water and detergent than traditional methods, minimizing environmental impact. This aligns with increasing demands for sustainable practices.
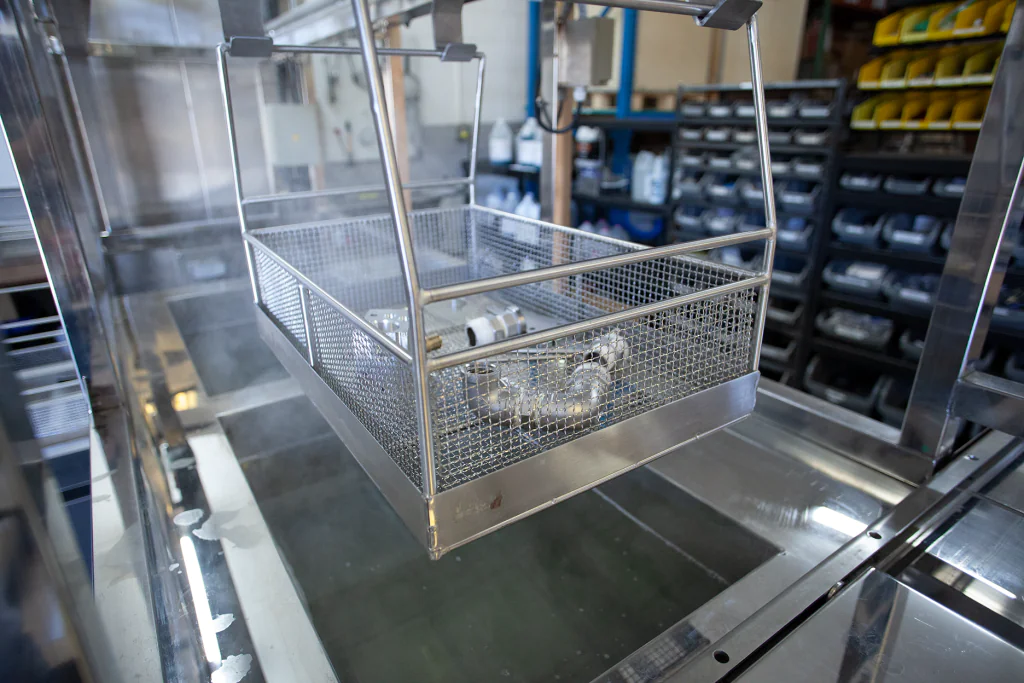
Disadvantages of Ultrasonic Cleaning
While ultrasonic cleaning offers many advantages, it’s essential to be aware of its limitations:
- Not Suitable for All Materials: Some materials, like certain plastics and soft metals, may be damaged by ultrasonic cavitation. It’s essential to choose the right materials for the process.
- Can Cause Corrosion: Ultrasonic cleaning can accelerate corrosion in some metals, especially if the cleaning solution is not carefully chosen. Proper solution selection is vital.
- Parameter Optimization: Achieving optimal results requires careful consideration of factors like ultrasonic frequency, cleaning time, temperature, and detergent concentration. Some fine-tuning may be needed for specific cleaning tasks.
- Noise: Ultrasonic cleaning machines generate high-frequency noise that can be uncomfortable for some people. Proper sound insulation or ear protection might be necessary.
- Initial Investment: Ultrasonic cleaning equipment can be more expensive than traditional cleaning tools. However, the long-term benefits often outweigh the initial cost.
The Science Behind Ultrasonic Cavitation
Ultrasonic cavitation, the core principle behind ultrasonic cleaning, is a fascinating phenomenon. The ultrasound waves, generated by the machine at frequencies above 20 kHz, create alternating high and low-pressure cycles in the cleaning solution. During the low-pressure cycles, microscopic bubbles form and grow. These bubbles then rapidly collapse during the high-pressure cycles. This implosion creates powerful shock waves and microjets that dislodge contaminants from the surface of the submerged object. This process, happening millions of times per second, provides the deep cleaning action characteristic of ultrasonic technology.
The effectiveness of the process depends on factors such as ultrasonic frequency, power, temperature, and the type of cleaning solution used. Higher frequencies generate smaller bubbles, resulting in finer cleaning, while lower frequencies create larger bubbles, suitable for removing larger particles or stubborn contaminants. Ultrasonic cleaning utilizes high-frequency sound waves to generate microscopic bubbles in the liquid solution. These bubbles implode near the surface creating a shock wave that removes contaminants from the surface.
Applications of Ultrasonic Cleaning for Stainless Steel
Ultrasonic cleaning finds numerous applications for stainless steel components:
- Medical Instruments: Surgical instruments, dental tools, and other medical devices made of stainless steel benefit from the thorough and sterile cleaning provided by ultrasonic cleaners. Lab Lift (Stainless Steel) 3 in x 3 in (76 mm x 76 mm) exemplifies equipment that might utilize this cleaning process for its precision and hygiene requirements.
- Automotive Parts: Engine components, fuel injectors, and other automotive parts made of stainless steel can be effectively cleaned using ultrasonic technology.
- Aerospace Components: Ultrasonic cleaning is used to remove grease, oil, and other contaminants from stainless steel parts used in aircraft and spacecraft.
- Food Processing Equipment: Stainless steel tanks, pipes, and other equipment used in food processing can be thoroughly cleaned and sanitized using ultrasonic cleaning. This helps maintain hygiene and prevent contamination.
- Electronics Manufacturing: Ultrasonic cleaning removes flux residue and other contaminants from stainless steel components used in electronic devices.
Choosing the Right Ultrasonic Cleaning System
Selecting the right ultrasonic cleaning system depends on various factors:
- Frequency: A frequency of 40 kHz is commonly used for general cleaning, while higher frequencies are suitable for delicate items.
- Power: Higher power results in more intense cavitation and faster cleaning.
- Tank Size: Choose a tank size appropriate for the items being cleaned.
- Features: Some systems offer additional features like temperature control, degassing, and filtration.
- Cleaning Solution: Select a cleaning solution compatible with stainless steel and the type of contaminants being removed. Alkaline or aqueous-based cleaning solutions are often preferred for stainless steel.
Optimizing the Ultrasonic Cleaning Process for Stainless Steel
To maximize the effectiveness of ultrasonic cleaning for stainless steel, consider these factors:
- Proper Degreasing: Ensure thorough degreasing before ultrasonic cleaning to remove oils and greases that can interfere with the cavitation process.
- Optimal Temperature: Maintaining the correct temperature, usually between 50 and 80 degrees Celsius, improves the cleaning solution’s efficiency.
- Degassing: Remove dissolved gases from the cleaning solution to enhance cavitation. This ensures the bubbles are as effective as possible.
- Filtration: Regularly filter the cleaning solution to remove particulate contaminants and extend its life. This keeps the solution clean and prevents recontamination.
- Passivation: After ultrasonic cleaning, passivation can enhance the corrosion resistance of the stainless steel. This adds an extra layer of protection.
Ultrasonic Cleaning vs. Traditional Cleaning Methods
Compared to traditional cleaning methods, ultrasonic cleaning offers several advantages:
Feature | Ultrasonic Cleaning | Traditional Cleaning Methods (e.g., scrubbing, soaking) |
---|---|---|
Thoroughness | Excellent | Limited, especially in hard-to-reach areas |
Speed | Fast | Slow |
Gentleness | Gentle on parts | Can cause damage or scratches |
Versatility | Versatile, suitable for various applications | Limited by part complexity |
Environmental Impact | Lower water and detergent usage | Higher water and detergent usage |
While traditional cleaning methods might be sufficient for simple cleaning tasks, ultrasonic cleaning excels at providing thorough, efficient, and gentle cleaning for complex or delicate parts, such as steel wire components within intricate assemblies.
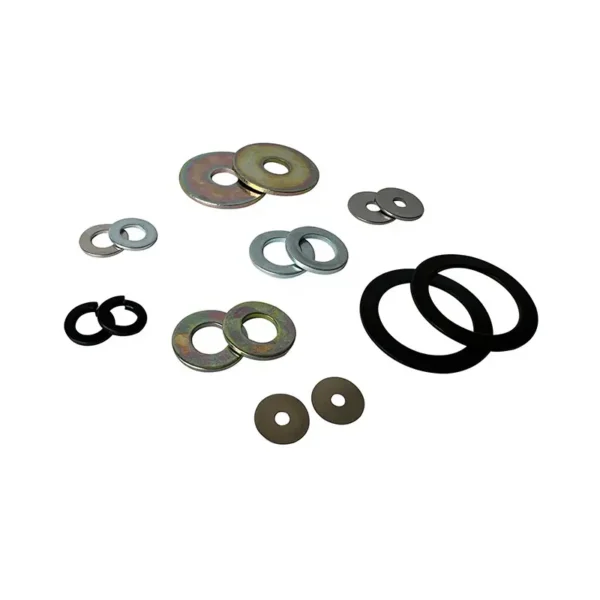
Key Takeaways: Ultrasonic Cleaning for Stainless Steel
- Ultrasonic cleaning is a highly effective and efficient cleaning method for stainless steel.
- Cavitation is the key mechanism behind ultrasonic cleaning, generating microscopic shock waves to remove contaminants.
- Careful consideration of parameters like frequency, power, and cleaning solution is crucial for optimal results.
- Ultrasonic cleaning offers numerous advantages over traditional cleaning methods.
- From medical devices to aerospace components, ultrasonic cleaning finds applications across various industries.
- Regular maintenance and optimization of the ultrasonic cleaner are important for consistent results.
By understanding these key aspects of ultrasonic cleaning, you can harness this powerful technology for effective and efficient cleaning of your stainless-steel components, ensuring their quality, longevity, and performance in various applications. For example, Electric Cable Copper Stamping parts, often made of stainless steel and requiring stringent cleaning, can benefit significantly from ultrasonic cleaning processes.