-
No.66 Gaojia, Xingfu Village, Sanqi Town, Yuyao, Ningbo,China
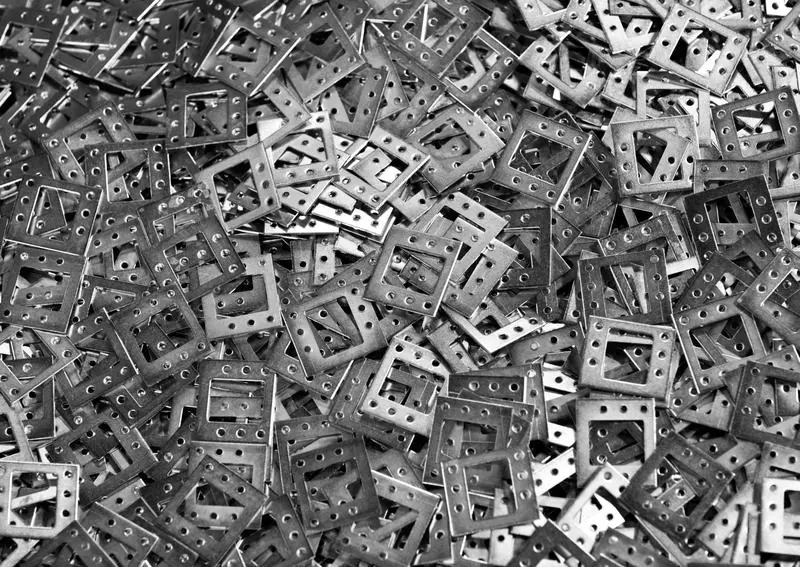
Understanding and Preventing Wrinkles in Metal Stamping: A Comprehensive Guide
Metal stamping is a crucial manufacturing process, but wrinkles can significantly impact product quality and production efficiency. This comprehensive guide explores the causes of wrinkles in metal stamping and provides practical solutions to prevent these common defects. Whether you’re a manufacturer, engineer, or quality control specialist, this article will help you understand and address wrinkling issues in your stamping operations.
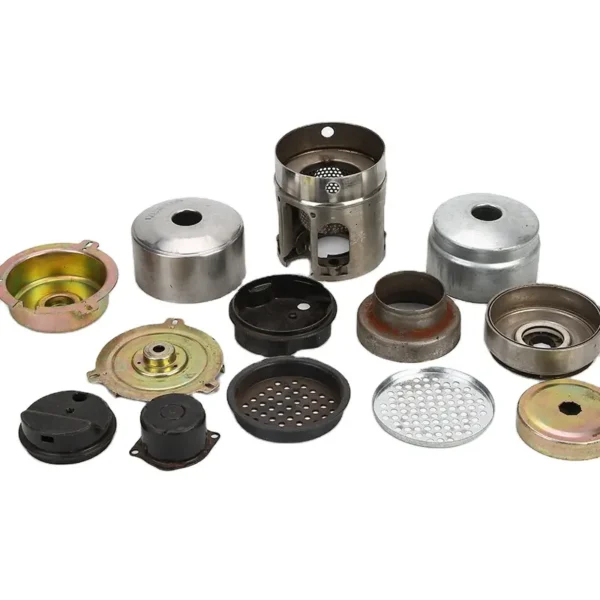
Deep drawn stamping components showing proper forming without wrinkles
What Causes Wrinkles in Metal Stamping?
The formation of wrinkles during the metal stamping process can be attributed to several factors. The material during the stretching process experiences uneven distribution of forces, leading to deformation resistance. When the pressing force is insufficient or unevenly applied, the sheet material may develop wrinkles.Key factors contributing to wrinkle formation:
- Uneven material flow
- Insufficient blank holder pressure
- Improper die design
- Material thickness variations
How Does Deep Drawing Affect Wrinkle Formation?
Deep drawing is particularly susceptible to wrinkle formation due to the complex material flow involved. During the deep drawing process, the blank undergoes significant deformation as it’s formed into the desired shape. The drawing depth and material properties play crucial roles in determining whether wrinkles will develop.
“The deeper the draw, the greater the risk of wrinkling. Proper control of material flow is essential for successful deep drawn stamping.” – Metal Forming Industry Expert
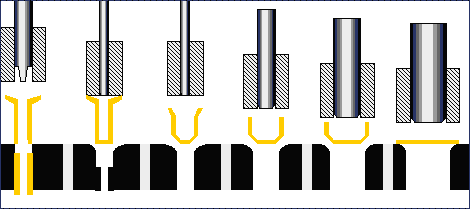
Common Types of Metal Stamping Defects
Metal stamping defects include various issues beyond just wrinkles:
- Sidewall wrinkles
- Flange wrinkles
- Cracks and splits
- Surface defects
- Dimensional inaccuracies
What Role Does Material Selection Play?
The choice of sheet material significantly impacts wrinkle formation. Different materials exhibit varying levels of:
- Tensile strength
- Formability
- Thickness consistency
- Surface finish
Learn more about material selection for stamping
Critical Process Parameters to Prevent Wrinkles
To effectively prevent wrinkles in stamping parts, several key parameters must be controlled:
Parameter | Optimal Range | Impact on Wrinkles |
---|---|---|
Blank Holder Force | 25-35% of press capacity | Prevents flange wrinkling |
Drawing Ratio | 1.6-2.2 | Affects material flow |
Die Radius | 4-10x material thickness | Influences stress distribution |
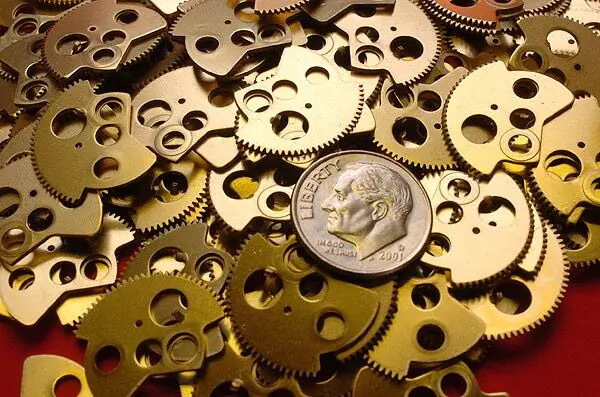
How to Optimize Die Design?
Proper die design is crucial for preventing wrinkles. The stamping die must be carefully engineered with consideration for:
- Proper radius selections
- Adequate clearances
- Optimal blank holder pressure
- Surface finish requirements
Explore our stamping solutions
Advanced Techniques for Wrinkle Prevention
Modern manufacturing employs several sophisticated approaches to prevent wrinkling:
- Computer Simulation
- FEA analysis
- Material flow prediction
- Stress distribution modeling
- Process Controls
- Real-time force monitoring
- Temperature control
- Lubrication management
When Should Draw Beads Be Used?
Draw beads are essential tools for controlling material flow and preventing wrinkles. They’re particularly effective when:
- Deep drawing complex shapes
- Working with thin materials
- Dealing with challenging geometries
View our deep drawing capabilities
Troubleshooting Common Wrinkling Issues
When wrinkles occur, systematic troubleshooting is essential:
- Analysis Phase
- Document defect patterns
- Review process parameters
- Check material properties
- Corrective Actions
- Adjust blank holder pressure
- Modify die geometry
- Optimize lubrication
Future Trends in Wrinkle Prevention
The metal forming industry continues to evolve with new technologies:
- AI-powered process control
- Advanced materials development
- Improved simulation capabilities
- Real-time quality monitoring
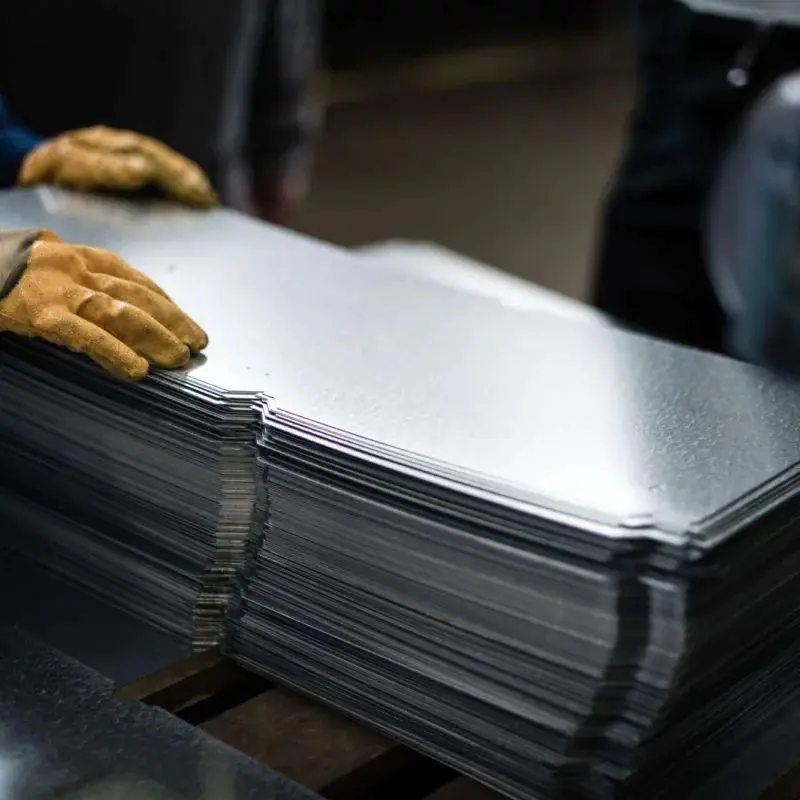
Key Takeaways:
- Proper material selection and die design are crucial for preventing wrinkles
- Regular monitoring and maintenance help maintain optimal stamping conditions
- Advanced technologies provide new solutions for wrinkle prevention
- Process parameter control is essential for quality outcomes
- Systematic troubleshooting helps resolve wrinkling issues quickly