-
No.66 Gaojia, Xingfu Village, Sanqi Town, Yuyao, Ningbo,China
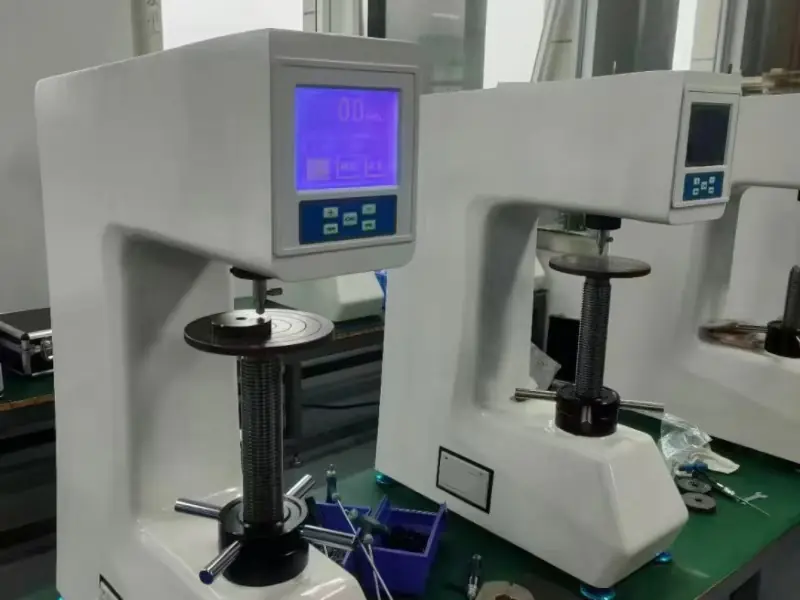
Understanding Metal Hardness Testing: A Complete Guide to Rockwell, Vickers, and Brinell Methods
Metal hardness testing is a crucial aspect of quality control and material characterization in manufacturing. This comprehensive guide explores the three main hardness testing methods – Rockwell, Vickers, and Brinell – helping you understand their applications, differences, and benefits. Whether you’re a quality control professional or involved in metal manufacturing, this guide provides essential insights into hardness testing methods.

Precision metal components requiring specific hardness testing
What is Hardness Testing and Why is it Important?
Hardness testing measures a material’s resistance to permanent indentation. This fundamental property helps determine a material’s durability, wear resistance, and suitability for specific applications. The testing process involves pressing an indenter into the material’s surface under controlled conditions.Modern hardness testing provides:
- Quality control assurance
- Material verification
- Process validation
- Performance prediction
How Does the Rockwell Hardness Test Work?
The Rockwell hardness test is one of the most widely used methods in metal testing. This test method uses different indenters and test loads depending on the material being tested:
Scale | Indenter Type | Applications |
---|---|---|
HRC | Diamond cone | Hardened steel |
HRB | Steel ball | Softer metals |
HRA | Diamond cone | Tungsten carbide |
Learn about precision metal components
What Makes the Vickers Hardness Test Unique?
The Vickers hardness test offers exceptional versatility and accuracy:
- Test Procedure
- Diamond pyramid indenter
- Precise load application
- Microscopic measurement
- Applications
- Thin materials
- Surface treatments
- Microhardness testing
Understanding the Brinell Hardness Test Method
The Brinell test method involves:✓ Larger indentation area ✓ Tungsten carbide ball indenter ✓ Longer test duration ✓ Suitable for inhomogeneous materialsExplore metal testing applications
How to Choose the Right Hardness Test Method?
Selection factors include:
- Material type and thickness
- Required accuracy
- Test location accessibility
- Surface condition
- Production requirements
What Are Common Applications for Each Test Method?
Different methods suit specific applications:
- Rockwell: Production testing, heat treatment verification
- Vickers: Research, thin materials, coatings
- Brinell: Cast iron, large parts, non-uniform materials
View precision manufacturing capabilities
How Do Hardness Values Compare Between Methods?
Understanding hardness conversion:
- Conversion Tables
- Standard reference charts
- Material-specific correlations
- Digital conversion tools
- Limitations
- Approximate conversions
- Material-dependent accuracy
- Range restrictions
What Are the Latest Developments in Hardness Testing?
Modern innovations include:
- Automated testing systems
- Digital measurement
- Portable testers
- Wireless data collection
- Advanced analysis software
How to Ensure Accurate Hardness Testing Results?
Best practices for testing:
- Sample Preparation
- Clean surface
- Proper support
- Correct spacing
- Testing Environment
- Temperature control
- Vibration isolation
- Proper lighting
What Are Common Hardness Testing Mistakes to Avoid?
Key considerations:
- Incorrect test method selection
- Poor surface preparation
- Wrong load application
- Improper spacing of indentations
- Inadequate calibration
Key Takeaways
• Choose the appropriate test method for your application • Proper sample preparation is crucial • Understanding conversion limitations • Regular calibration is essential • Modern technology enhances accuracy • Proper training ensures reliable results
This comprehensive guide provides insights into metal hardness testing methods and applications. For specific testing requirements or detailed information, consult with experienced materials testing professionals who can provide tailored solutions for your needs.