-
No.66 Gaojia, Xingfu Village, Sanqi Town, Yuyao, Ningbo,China
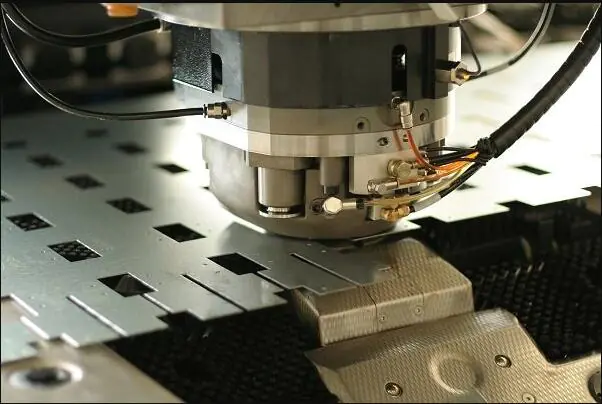
Unlocking High-Performance Metal Stamping Materials: Your Essential Selection Guide
In today’s precision-driven manufacturing world, selecting the right metal stamping material can make or break your project’s success. This comprehensive guide explores the various metals suitable for stamping processes, their unique properties, and optimal applications. Whether you’re a manufacturer, engineer, or product designer, this article will help you make informed decisions about metal selection for your stamping projects.
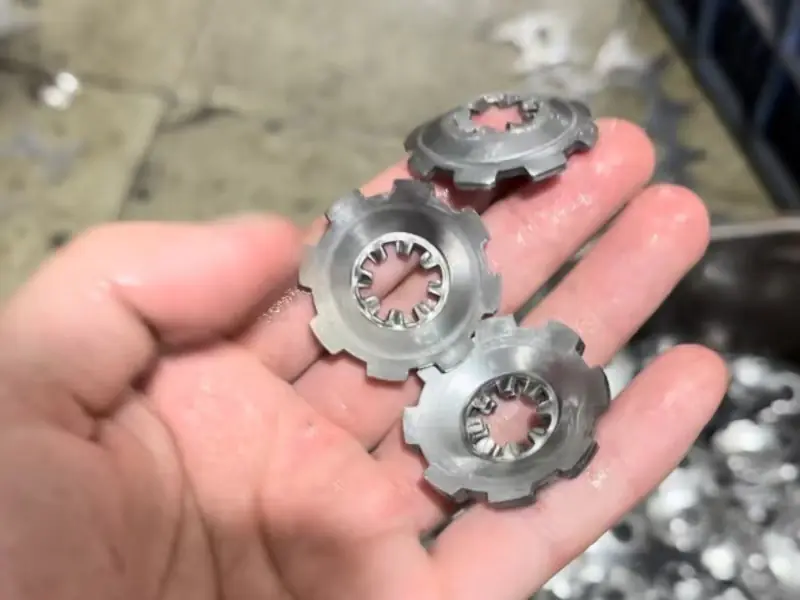
What Makes a Metal Suitable for Stamping?
The stamping process requires materials with specific properties to ensure successful outcomes. Two critical factors determine a metal’s suitability for stamping: formability and malleability. Materials must withstand the intense pressures of the metal forming process while maintaining their structural integrity.A metal’s hardness and tensile strength play crucial roles in determining its stampability. Materials that are too hard may crack or break during forming, while those too soft might not maintain their shape. The best raw materials for stamping combine good strength with excellent formability.
How Does Steel Compare to Other Metals in Stamping Applications?
Steel remains one of the most commonly used materials in metal stamping, particularly in precision metal stamping applications. Its versatility and cost-effective nature make it an excellent choice for various industries. Different steel alloys offer unique combinations of strength, durability, and corrosion resistance.
Steel Type | Key Properties | Best Applications |
---|---|---|
Carbon Steel | High strength, good machinability | Automotive parts |
Stainless Steel | Corrosion-resistant, hygienic | Medical devices |
Tool Steel | Wear resistance, high hardness | Industrial tools |
What Role Does Brass Play in Modern Metal Stamping?
Brass, a copper alloy, offers unique properties that make it suitable for specific stamping applications. Its excellent conductivity and corrosion resistance make it ideal for electrical components and decorative items. Brass’s malleability allows for complex parts with high repeatability in the stamping process.Many manufacturers choose brass for its antimicrobial properties, making it perfect for medical and food industry applications. Its smooth surface finish and aesthetic appeal also make it popular for custom jewelry and decorative components.
Why Consider Aluminum for Your Stamping Project?
Aluminum’s high strength-to-weight ratio makes it an increasingly popular choice in modern metal stamping. This non-ferrous metal offers excellent formability and corrosion resistance while maintaining good strength properties. Check out our aluminum lab lift products for practical applications.The material’s lightweight nature and temperature resistance make it ideal for aerospace and automotive applications. Additionally, aluminum’s good conductivity makes it suitable for electrical components and heat sinks.
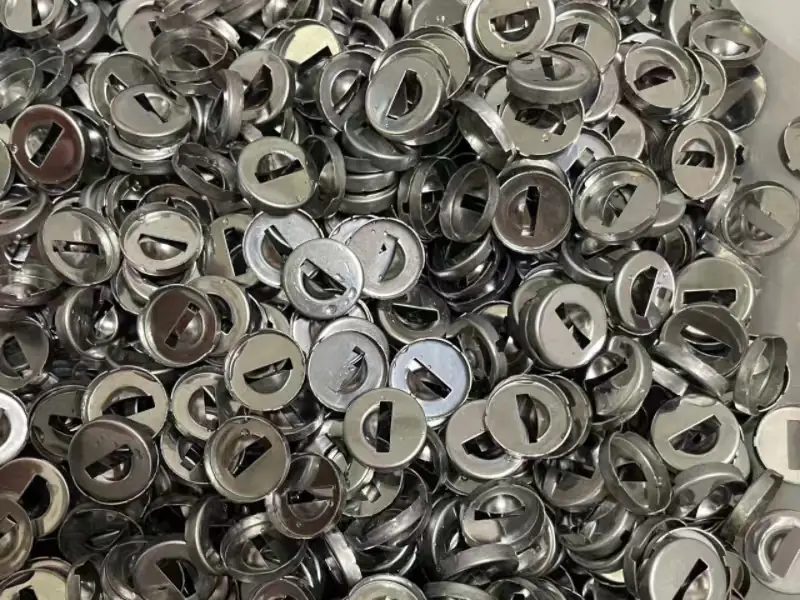
How Do Copper and Its Alloys Perform in Stamping Operations?
Copper’s exceptional conductivity and formability make it invaluable in electrical applications. The metal forming process for copper requires specific expertise due to its unique properties. Phosphor bronze and other copper alloys offer enhanced mechanical properties while maintaining copper’s beneficial characteristics.These materials are used extensively in electrical connectors and bus bars, where high conductivity and durability are essential. Their resistance to corrosion and good machinability make them ideal for complex stamped components.
What Are the Advantages of Non-Ferrous Metals in Stamping?
Non-ferrous metals like nickel silver and pewter offer unique advantages in specific applications. Their non-magnetic properties and corrosion resistance make them suitable for specialized industrial applications. These metals often provide good strength and wear resistance while maintaining excellent formability.
How Does Material Selection Impact Custom Metal Stamping?
Choosing the right material for custom metal stamping requires careful consideration of various factors:
- End-use requirements
- Environmental conditions
- Cost constraints
- Production volume
- Finishing requirements
The success of custom stamping projects often depends on proper material selection aligned with specific application needs.
What Are the Latest Trends in Metal Stamping Materials?
Modern metal stamping continues to evolve with new alloys and materials being developed. High-performance materials with enhanced properties are becoming more common in various industries. These innovations allow for more complex parts with high precision and repeatability.
How to Ensure Quality in Metal Stamped Components?
Quality control in metal stamping starts with proper material selection and extends through the entire manufacturing process. Regular testing and inspection ensure stamped parts meet specifications. Working with experienced metal stamping professionals helps maintain consistent quality across production runs.
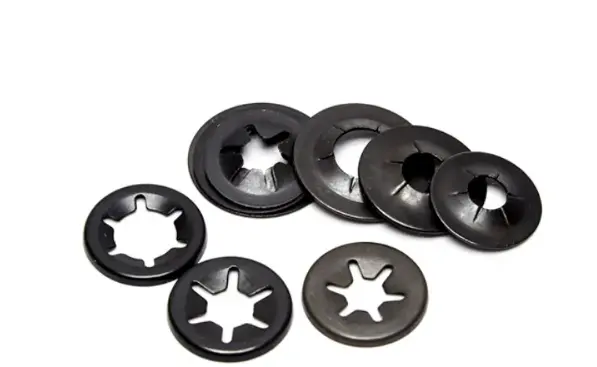
Key Takeaways:
- Material selection significantly impacts stamping success and final product quality
- Steel remains the most versatile and widely used stamping material
- Non-ferrous metals offer unique properties for specialized applications
- Proper material selection must consider multiple factors including end-use requirements
- Quality control is essential throughout the stamping process
- Modern trends favor high-performance materials for complex applications
- Working with experienced manufacturers ensures optimal material selection and quality
Remember to consult with experienced metal stamping professionals for guidance on material selection for your specific application.