-
No.66 Gaojia, Xingfu Village, Sanqi Town, Yuyao, Ningbo,China
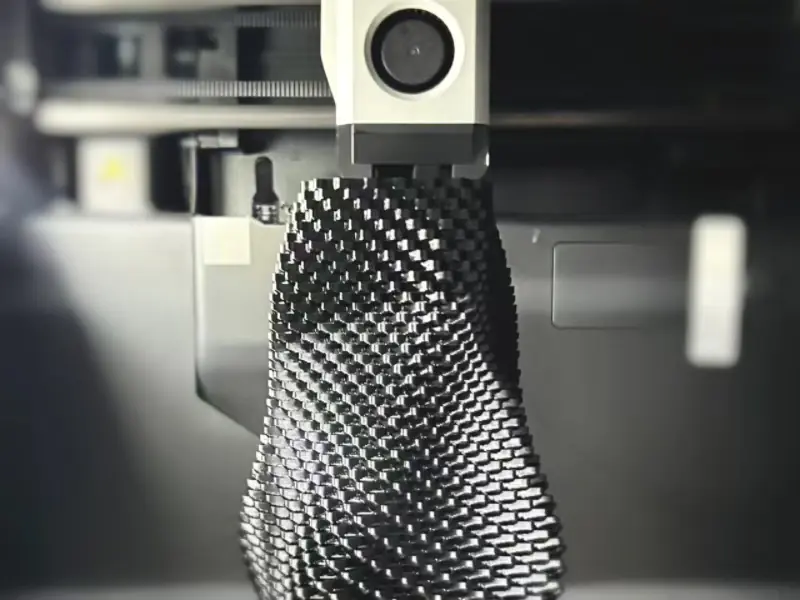
Revolutionizing Quality Control: How 3D Printed Inspection Fixtures Transform CMM Processes
In today’s precision-driven manufacturing landscape, the integration of 3D printing technology with inspection fixtures has revolutionized quality assurance processes. This comprehensive guide explores how 3D printed fixtures are transforming coordinate measuring machine (CMM) inspection, offering faster, more cost-effective, and highly accurate solutions for quality control.
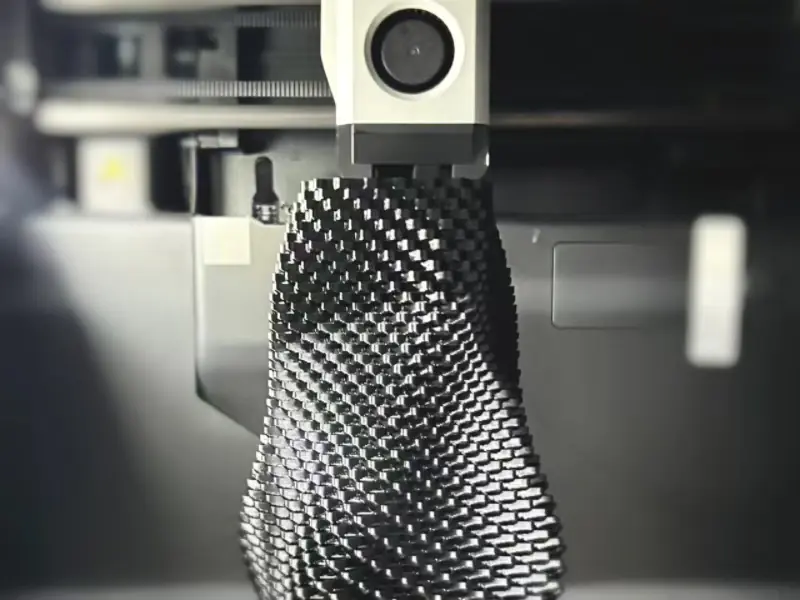
Advanced 3D printed inspection fixtures enable precise measurements
What Are 3D Printed Inspection Fixtures?
3D printed inspection fixtures are custom-designed tools that hold parts in place during measurement and inspection processes. These fixtures combine the precision of rapid prototyping technologies with the flexibility of additive manufacturing, offering several advantages:
- Rapid design and production
- Complex geometry capabilities
- Cost-effective customization
- Lightweight yet durable construction
How Does CMM Fixturing Benefit from 3D Printing?
The integration of 3D printing with CMM fixturing has transformed quality control processes in several ways:
- Reduced lead times from weeks to days
- Lower production costs
- Enhanced design flexibility
- Improved measurement accuracy
The Role of FDM Technology in Fixture Creation
FDM (Fused Deposition Modeling) technology plays a crucial role in creating inspection fixtures:
Feature | Benefit |
---|---|
Material options | Multiple choices including Nylon 12 |
Strength | Fiber reinforcement capability |
Accuracy | High dimensional precision |
Cost | Fraction of traditional methods |
Why Choose 3D Printed Fixtures for Quality Assurance?
Custom inspection tooling created through 3D printing offers numerous advantages:
- Quick iteration and optimization
- Reduced material waste
- Complex geometries possible
- Excellent repeatability
Designing Effective 3D Printed Inspection Fixtures
Creating effective fixtures requires consideration of several factors:
- Part geometry and features
- Measurement requirements
- Material selection
- Print orientation
- Support structures
The Impact on Manufacturing Workflow
3D printed fixtures streamline the inspection process by:
- Reducing setup time
- Improving measurement consistency
- Enabling faster part changeover
- Minimizing operator error
Applications Across Industries
These fixtures find use in various sectors:
- Aerospace
- Automotive
- Medical device manufacturing
- Consumer electronics
- Defense
Comparing Traditional vs. 3D Printed Fixtures
A detailed comparison reveals significant advantages:
- Cost Savings
- Traditional: High machining costs
- 3D Printed: Significant reduction in material and labor
- Lead Time
- Traditional: Weeks of production time
- 3D Printed: Hours to days
- Design Freedom
- Traditional: Limited by manufacturing constraints
- 3D Printed: Complex geometries possible
Future Trends in 3D Printed Inspection Tooling
The future looks promising with:
- Advanced materials development
- Improved printing technologies
- Integration with smart manufacturing
- Enhanced automation capabilities
Key Takeaways:
- 3D printed fixtures significantly reduce lead times and costs
- Complex geometries are easily achievable
- Quality and accuracy match traditional methods
- Perfect for both prototype and production applications
- Enables rapid design iterations
- Supports various industry applications
By embracing 3D printed inspection fixtures, manufacturers can significantly improve their quality control processes while reducing costs and lead times. This technology continues to evolve, offering even more possibilities for the future of manufacturing inspection.