-
No.66 Gaojia, Xingfu Village, Sanqi Town, Yuyao, Ningbo,China
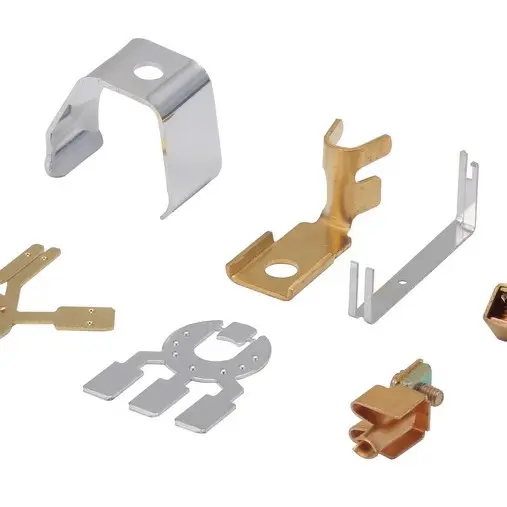
Metal Stamping Master: A Comprehensive Guide to Modern Manufacturing Processes
Metal stamping is a sophisticated manufacturing process that transforms flat metal sheets into precise, functional components. Whether you’re an industry professional, manufacturer, or simply curious about this essential manufacturing technique, this guide will walk you through the fundamentals, applications, and latest innovations in metal stamping technology.
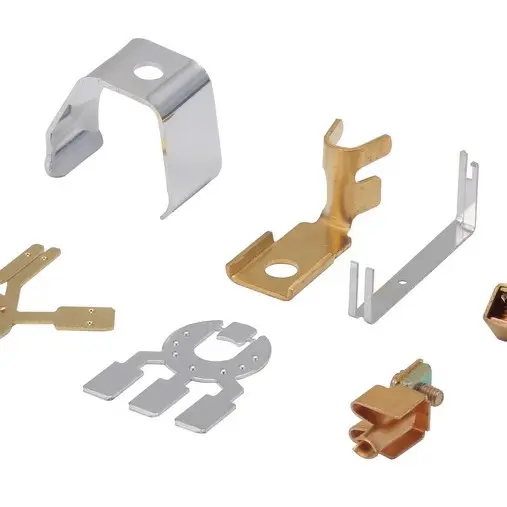
Industrial electrical connectors produced through precision metal stamping
What is Metal Stamping and How Does it Work?
Metal stamping is a cold-forming manufacturing process used to convert flat metal sheets into specific shapes and components. This versatile technique employs specialized tools and dies to shape metal through various operations including punching, bending, and forming. The process begins by placing flat sheet metal into a stamping press, where tremendous pressure transforms the material into the desired shape.During the process, a tool and die work together to create precise indentations and shapes in the metal sheet. The stamping press applies controlled force to achieve the exact specifications required for each component.
What Are the Different Types of Metal Stamping?
Modern metal stamping encompasses several specialized techniques:
- Progressive Die Stamping
- Multiple operations in sequence
- Continuous feed of metal strip
- High-volume production capability
- Transfer Die Stamping
- Ideal for complex parts
- Separate stations for each operation
- Automated transfer between stages
- Four-slide Stamping
- Also known as multi-slide stamping
- Perfect for intricate bent wire forms
- Complex bends and shapes possible
What Industries Rely on Metal Stamping Services?
Metal stamping serves numerous industries with critical components:
- Automotive manufacturing
- Aerospace applications
- Consumer electronics
- Medical device production
- Home appliances
- Construction equipment
How Does the Metal Stamping Process Work?
The metal stamping process involves several key steps:
- Design Phase
- CAD modeling
- Prototype development
- Tool and die design
- Material Selection
- Sheet metal specification
- Material thickness determination
- Surface finish requirements
- Production Setup
- Tool installation
- Press configuration
- Quality control measures
What Are the Advantages of Metal Stamping?
Metal stamping offers numerous benefits:
- High production efficiency
- Consistent quality
- Cost-effective for large volumes
- Precise tolerances
- Versatile applications
What Tools and Equipment Are Used in Metal Stamping?
Essential metal stamping equipment includes:
- Stamping Presses
- Mechanical presses
- Hydraulic presses
- Servo-driven presses
- Tools and Dies
- Progressive dies
- Transfer dies
- Single-station dies
What Materials Can Be Used in Metal Stamping?
Common materials include:
Material | Characteristics | Common Applications |
---|---|---|
Steel | Strong, durable | Automotive parts |
Aluminum | Lightweight, corrosion-resistant | Electronics housings |
Copper | Excellent conductivity | Electrical components |
Brass | Good machinability | Decorative items |
How to Choose the Right Metal Stamping Service?
Consider these factors when selecting a provider:
- Manufacturing capabilities
- Quality certifications
- Production capacity
- Technical expertise
- Industry experience
What Are the Latest Innovations in Metal Stamping?
Recent advances include:
- Automated quality control systems
- Smart manufacturing integration
- Advanced materials processing
- Improved energy efficiency
- Enhanced precision control
Key Takeaways
- Metal stamping is a versatile manufacturing process
- Multiple techniques available for different applications
- Proper material selection is crucial
- Quality control is essential
- Technology continues to advance the field
- Cost-effective for high-volume production
- Wide range of industry applications
Remember that successful metal stamping requires careful planning, proper tool selection, and expertise in material properties and manufacturing processes.