-
No.66 Gaojia, Xingfu Village, Sanqi Town, Yuyao, Ningbo,China
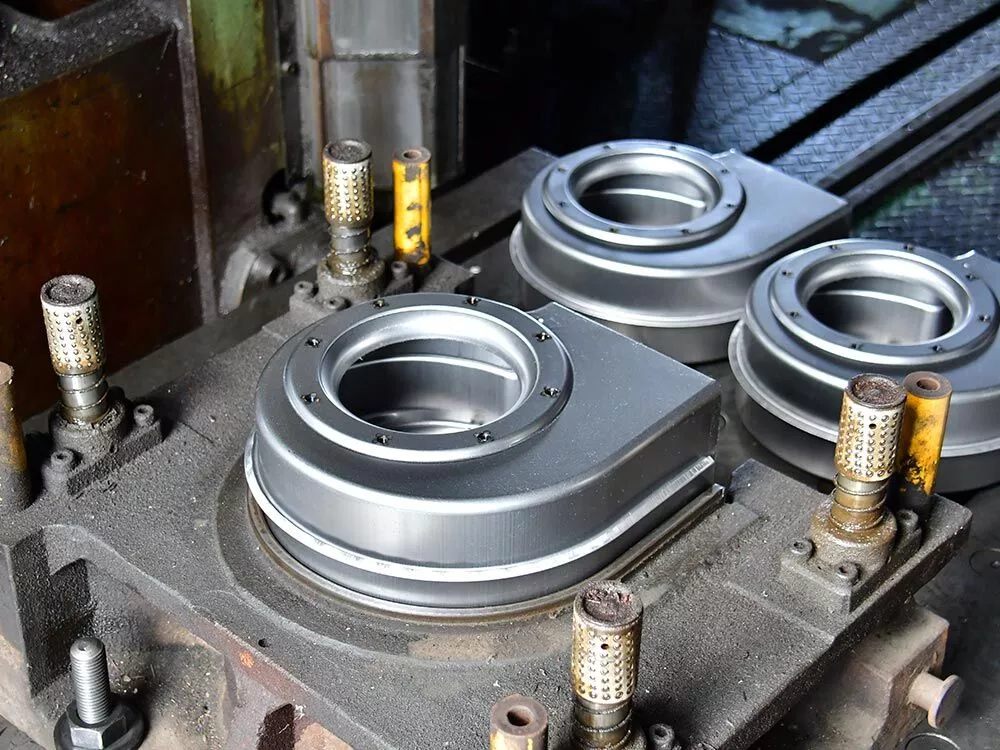
What are the different operations in sheet metal and stamped parts manufacturing?
Metal stamping and sheet metal fabrication are fundamental manufacturing processes that transform flat metal sheets into functional components. This comprehensive guide explores various stamping processes, techniques, and applications, helping you understand how these versatile methods create precision parts for diverse industries. Whether you’re a manufacturer, engineer, or curious about metal forming, this article provides valuable insights into modern metal fabrication.
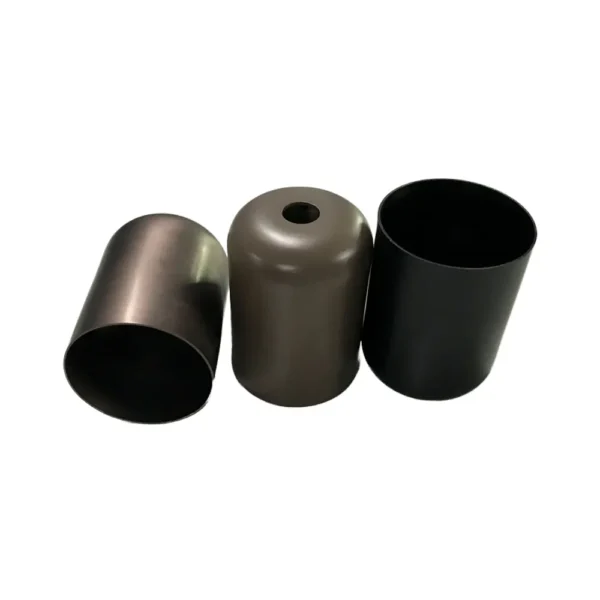
Precision metal stamping demonstrated in custom lamp cup manufacturing
What is Metal Stamping and How Does it Work?
Metal stamping is a manufacturing process that transforms flat sheet metal into specific shapes using specialized tools and dies. This cold-forming process involves placing flat sheet metal into a press, where tools shape the material through various operations. The process can be performed as a single stage operation or through a series of steps.Key aspects include:
- Press operation
- Die design
- Material selection
- Quality control
Explore our sheet metal fabrication products
Types of Metal Stamping Processes
Several stamping processes are commonly used:
- Progressive Die Stamping
- Continuous operation
- Multiple stations
- High production rates
- Transfer Die Stamping
- Separate operations
- Complex parts
- Flexible setup
View our custom stamping parts
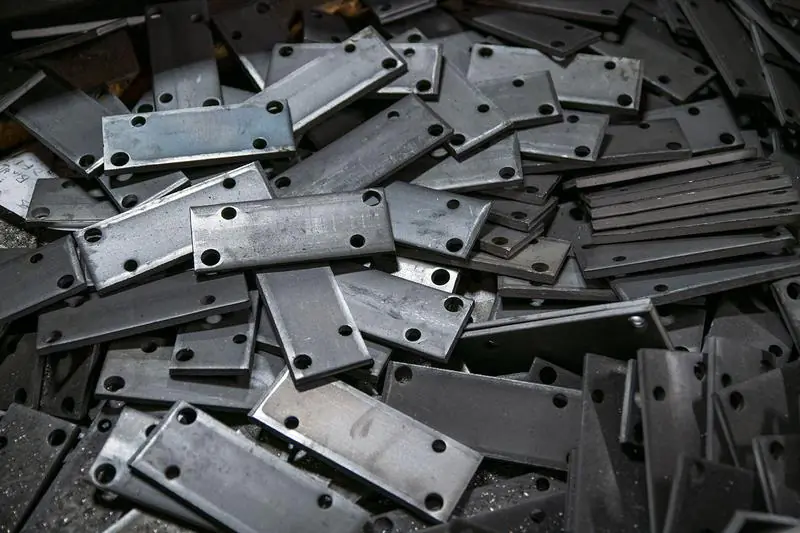
What Are the Advantages and Disadvantages of Metal Stamping?
Advantages:
- High production rates
- Consistent quality
- Cost-effective for large volumes
- Precise tolerances
Disadvantages:
- High initial tooling costs
- Limited design flexibility
- Material waste
- Size limitations
Sheet Metal Fabrication Methods
Common fabrication techniques include:
Method | Application | Benefits |
---|---|---|
Cutting | Part creation | Precise edges |
Forming | Shape generation | Complex geometries |
Bending | Angle creation | Structural strength |
Check out our electrical connectors stamping
Metal Forming Processes and Applications
Metal forming processes serve various industries:✓ Automotive components ✓ Electronics housings ✓ Appliance parts ✓ Construction materials ✓ Consumer goods
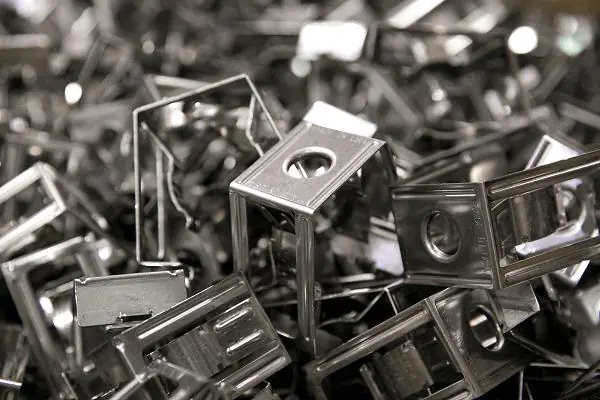
How to Choose the Right Stamping Process?
Consider these factors:
- Production Volume
- Batch size
- Annual requirements
- Lead times
- Part Complexity
- Geometric features
- Tolerances
- Material requirements
Quality Control in Metal Stamping
Essential quality measures include:
- Material inspection
- Die maintenance
- Process monitoring
- Part verification
Advanced Metal Stamping Techniques
Modern techniques include:
- Precision stamping
- Multi-slide forming
- Hybrid processes
- Automated systems
Future Trends in Metal Stamping
Emerging developments include:
- Smart manufacturing
- Sustainable practices
- Advanced materials
- Digital integration
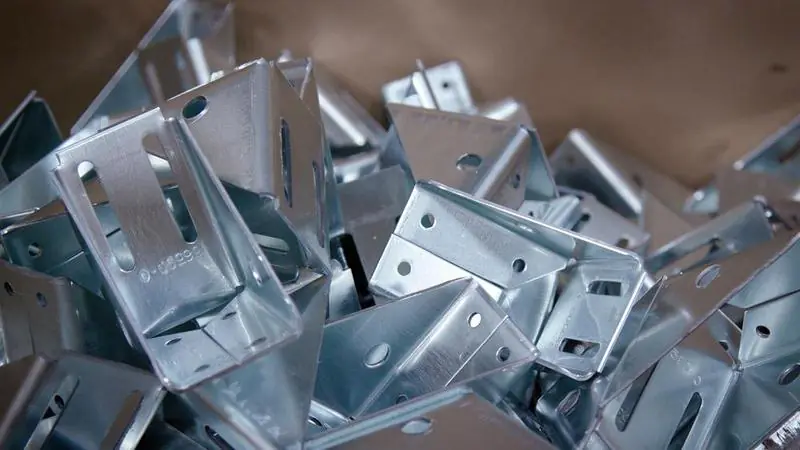
Cost Considerations in Metal Stamping Projects
Key cost factors:
- Material selection
- Tooling design
- Production volume
- Secondary operations
Key Takeaways
- Understanding process selection is crucial
- Quality control ensures consistent results
- Advanced techniques offer new possibilities
- Cost optimization requires careful planning
- Future trends shape industry direction
Remember these critical points: • Choose appropriate processes • Maintain quality standards • Consider production volumes • Plan for tooling costs • Stay current with technologyThis comprehensive guide equips you with essential knowledge about metal stamping and sheet metal fabrication processes.