-
No.66 Gaojia, Xingfu Village, Sanqi Town, Yuyao, Ningbo,China
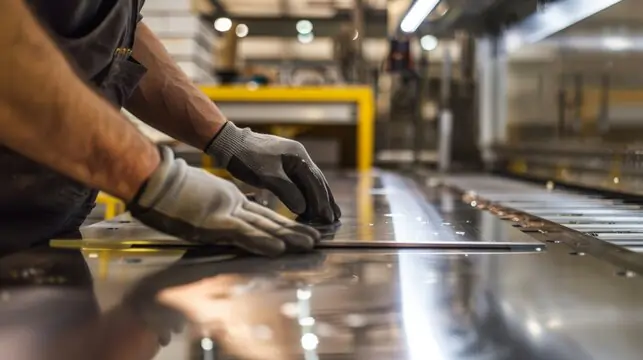
What does stamping mean in manufacturing?
Metal stamping is a critical manufacturing process that transforms flat sheet metal into precise, functional components used across industries. Whether you’re an engineer, manufacturer, or someone interested in industrial processes, this comprehensive guide will help you understand the intricacies of metal stamping and its vital role in modern manufacturing.
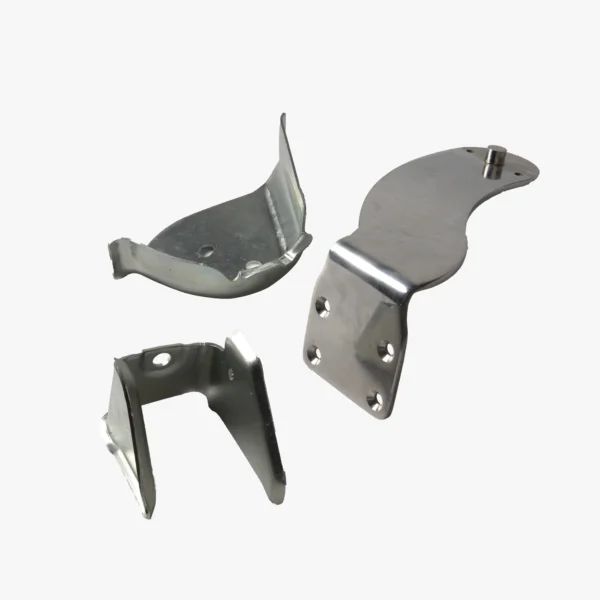
Precision-engineered stamped chassis brackets showcasing the capabilities of modern metal stamping
What is Metal Stamping and Why is it Important?
Metal stamping is a versatile manufacturing process that uses specialized tools and dies to transform flat metal sheets into specific shapes. This forming process is essential for producing components used in automotive parts manufacturing, consumer electronics, and aerospace applications. The process involves placing flat sheet metal into a stamping press, where tools shape the metal through various operations like cutting, bending, and forming.
How Does the Metal Stamping Process Work?
The metal stamping process begins with selecting the appropriate material and thickness. A stamping press applies pressure to a metal blank, using specially designed dies to create the desired shape. The workpiece moves through several stages:
- Blanking: Cutting the initial shape
- Piercing: Creating holes or openings
- Forming: Bending and shaping
- Finishing: Secondary processes as needed
What Are the Different Types of Metal Stamping Techniques?
Several stamping techniques are used depending on the complexity and requirements of the final product:
- Progressive stamping
- Transfer die stamping
- Deep drawing
- Four-slide stamping
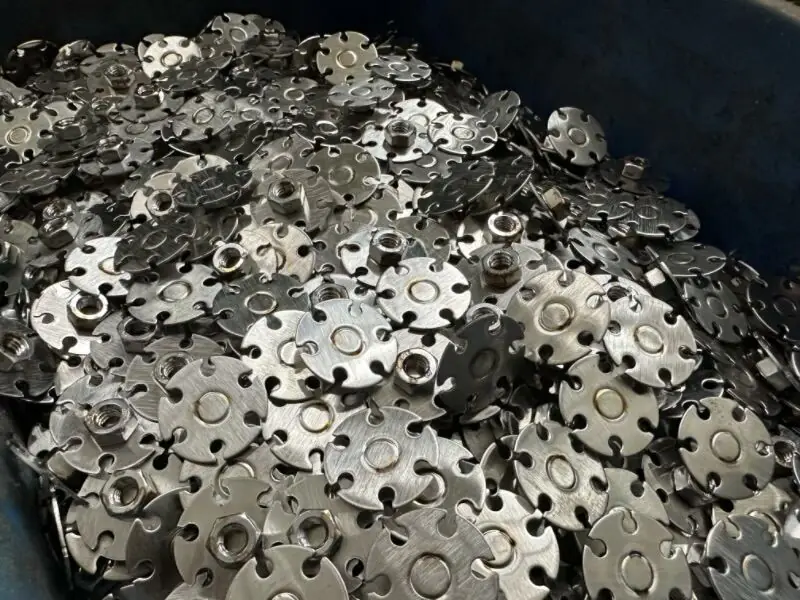
Which Industries Rely on Metal Stamping?
The automotive industry heavily depends on metal stamping for producing various components. Other sectors include:
- Aerospace
- Electronics
- Home appliances
- Medical devices
- Construction
What Materials Can Be Used in Metal Stamping?
Common materials include:
Material Type | Common Applications | Key Benefits |
---|---|---|
Steel | Automotive parts | Strength, cost-effective |
Aluminum | Electronics housing | Lightweight, corrosion-resistant |
Copper | Electrical components | Excellent conductivity |
Brass | Decorative items | Good machinability |
How to Choose the Right Metal Stamping Process?
Consider these factors when selecting a stamping process:
- Production volume requirements
- Material specifications
- Part complexity
- Tolerance requirements
- Cost considerations
What Are the Benefits of Metal Stamping?
Metal stamping offers numerous advantages:
- High-volume production capability
- Cost-effective for large runs
- Consistent quality
- Tight tolerances
- Minimal material waste
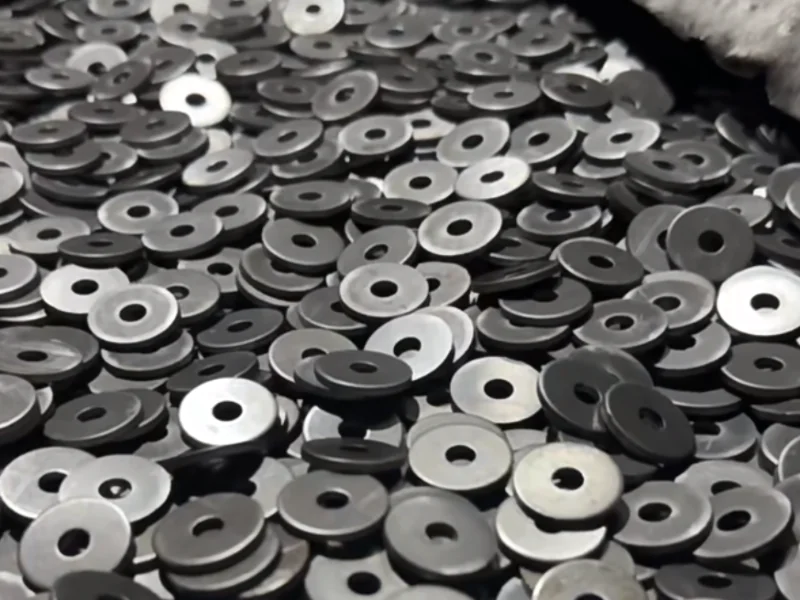
Common Challenges in Metal Stamping and How to Overcome Them
Key challenges include:
- Material selection issues
- Tool wear and maintenance
- Quality control
- Cost management
Latest Innovations in Metal Stamping Technology
Recent advancements include:
- CNC integration
- Automated quality control systems
- Advanced die designs
- Improved material handling
How to Ensure Quality in Metal Stamped Parts?
Quality control measures include:
- Regular tool inspection
- Material testing
- Dimensional verification
- Surface finish evaluation
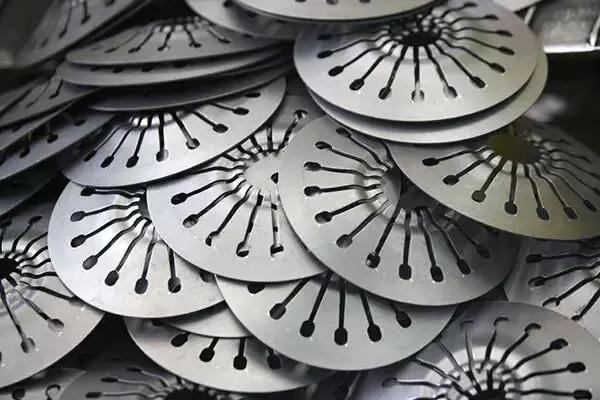
Key Points to Remember:
- Metal stamping is vital for modern manufacturing
- Various techniques suit different applications
- Material selection impacts final product quality
- Quality control is crucial throughout the process
- Technology continues to advance the field
Internal Links Used: