-
No.66 Gaojia, Xingfu Village, Sanqi Town, Yuyao, Ningbo,China
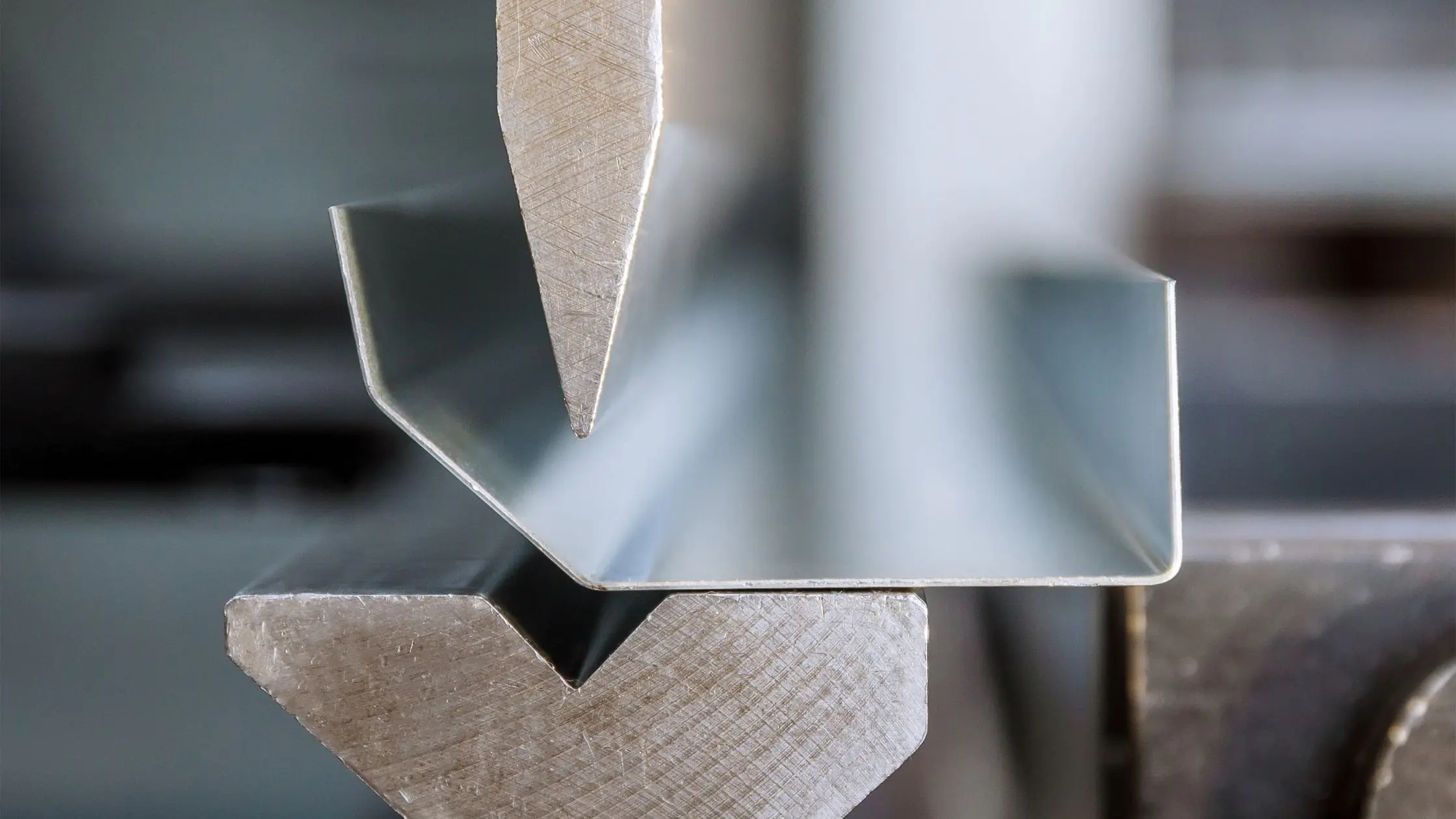
What is better for sheet metal forming, stamping or hammering?
In today’s manufacturing landscape, metal forming and sheet metal stamping stand as cornerstone processes that shape our modern world. From automotive components to household appliances, these techniques transform flat metal sheets into complex, functional parts with precision and efficiency. This comprehensive guide will explore the intricacies of metal forming processes, helping you understand their applications, benefits, and technical considerations.
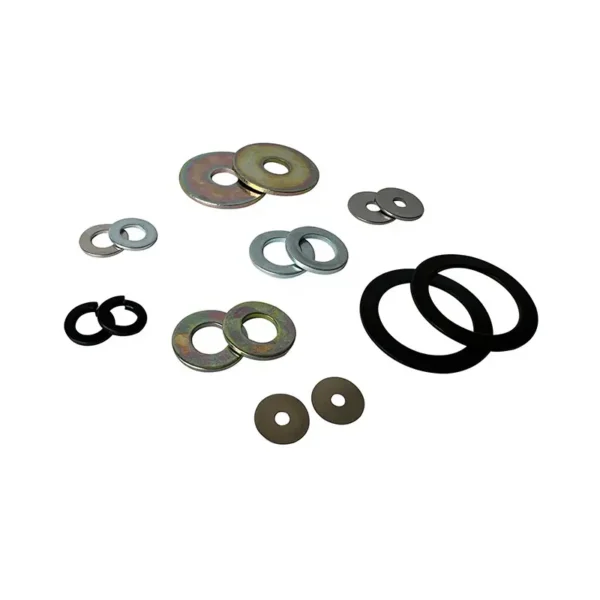
Advanced metal forming techniques demonstrated in rapid prototype spacer manufacturing
What is Metal Forming and How Does it Work?
Metal forming is a manufacturing process that shapes metal sheets into desired forms without removing material. This process involves applying force to a piece of metal to deform it into specific shapes while maintaining its mass and material properties. The working process typically uses specialized tools and machinery to achieve precise results.Two primary approaches define metal forming:
- Cold working (performed at room temperature)
- Hot working (performed at elevated temperatures)
Essential Sheet Metal Forming Techniques
Modern sheet metal forming encompasses several key techniques:
- Bending
- Creates angles and curves in flat metal
- Uses specialized tooling for precise angles
- Common in architectural applications
- Drawing
- Forms deep cavities and complex shapes
- Requires careful material flow control
- Essential for automotive body panels
Explore our stamped chassis brackets for automotive applications.
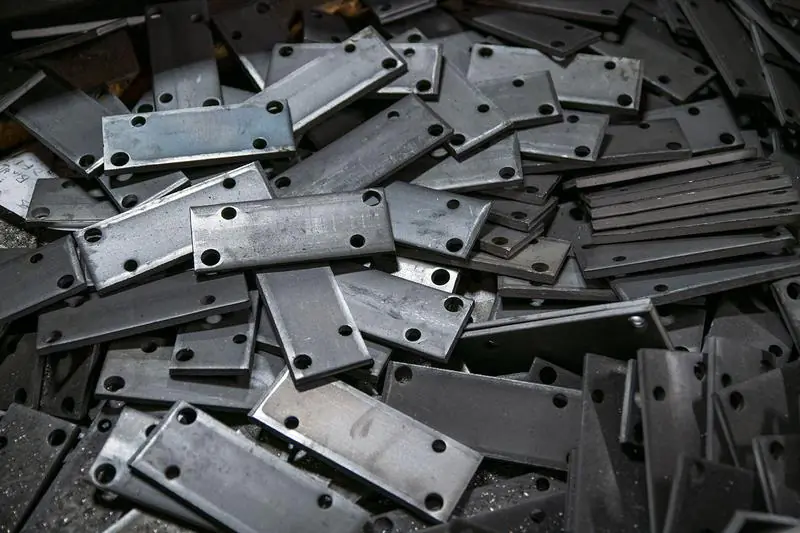
The Role of Stamping Press in Metal Fabrication
A stamping press serves as the cornerstone of metal stamping operations. These powerful machines:
- Generate high forces for forming operations
- Accommodate various die sets
- Enable high-volume production
- Maintain consistent quality
Advanced Metal Forming Technologies
Modern metal forming has evolved to include sophisticated techniques:
Technology | Application | Benefits |
---|---|---|
Progressive Dies | Complex parts | High production rate |
Transfer Press | Large components | Flexibility |
Servo Press | Precision parts | Enhanced control |
Check out our electrical connectors stamping solutions
How Does Tool and Die Selection Impact Results?
The choice of tool and die significantly affects:
- Part quality
- Production efficiency
- Tooling cost
- Material waste
- Surface finish
Metal Forming in Various Industries
Metal forming techniques find applications across multiple sectors:✓ Automotive manufacturing ✓ Aerospace components ✓ Consumer electronics ✓ Construction materials ✓ Medical devicesView our plumbing fixture stamping products
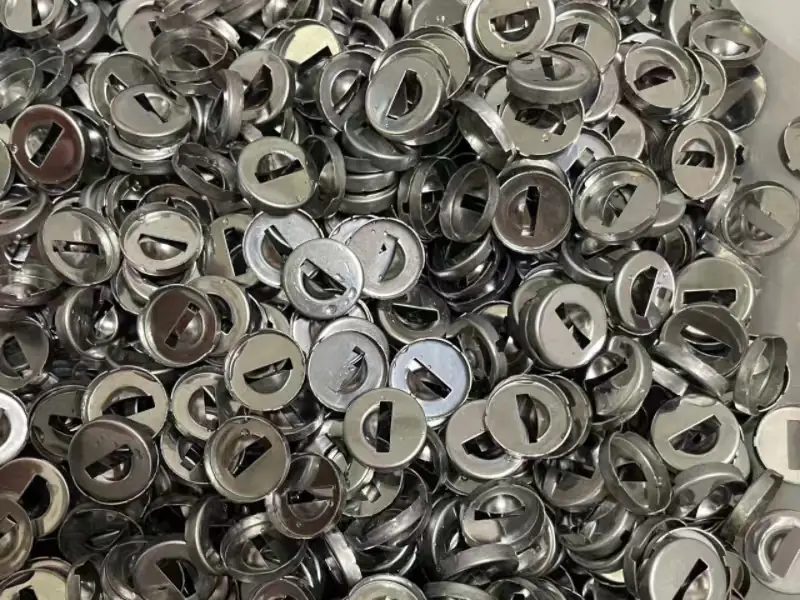
Optimizing Sheet Metal Fabrication Processes
To achieve optimal results:
- Material Selection
- Consider material properties
- Account for forming limits
- Evaluate cost factors
- Process Planning
- Design appropriate tooling
- Determine forming sequence
- Plan quality control steps
Common Challenges in Metal Forming
Key challenges include:
- Material springback
- Tool wear
- Quality consistency
- Production costs
- Complex geometries
Future Trends in Metal Forming
The industry continues to evolve with:
- Advanced automation
- Smart manufacturing
- Sustainable practices
- New material developments
- Improved simulation tools
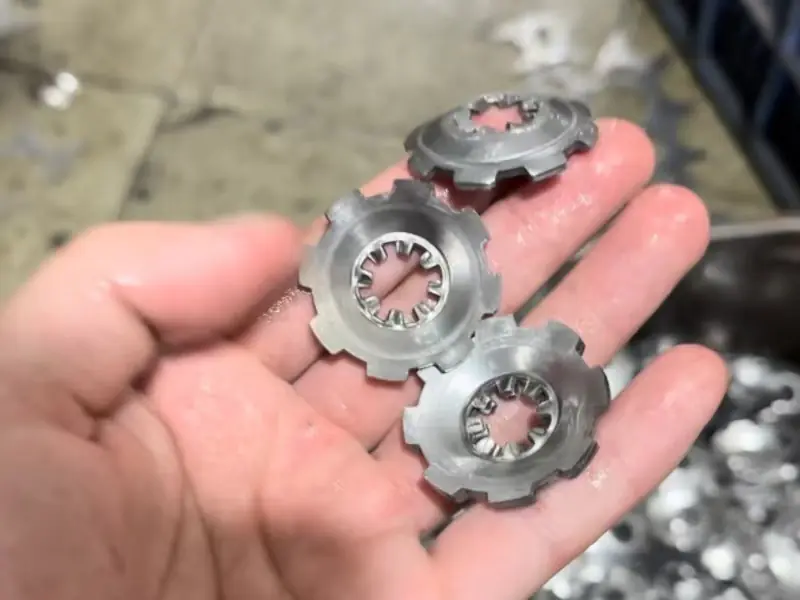
Key Takeaways
- Metal forming transforms flat metal sheets into complex components
- Various techniques suit different applications
- Proper tool selection is crucial for success
- Quality control ensures consistent results
- Industry trends point toward automation and sustainability
Remember these critical points: • Choose appropriate forming techniques • Consider material properties • Implement quality controls • Maintain proper tooling • Stay current with technologyThis comprehensive overview equips you with essential knowledge about metal forming and stamping processes, helping you make informed decisions for your manufacturing needs.