-
No.66 Gaojia, Xingfu Village, Sanqi Town, Yuyao, Ningbo,China
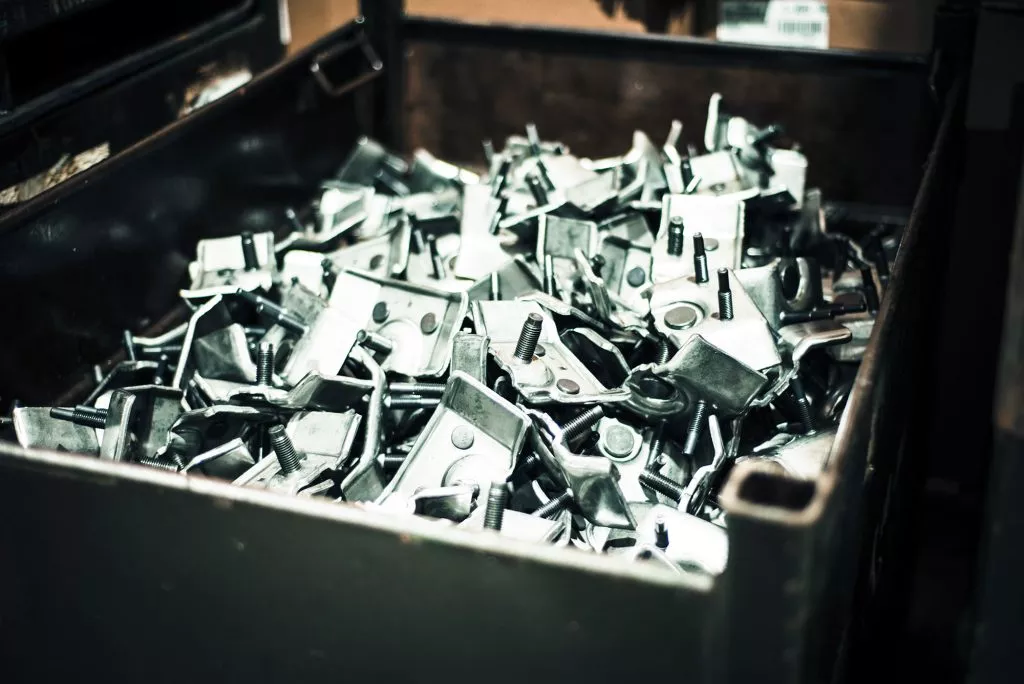
What is called stamping a product?
In today’s manufacturing landscape, choosing the right metal forming process is crucial for product success. This comprehensive guide explores the differences between metal stamping and die casting, helping you make informed decisions for your manufacturing needs. Whether you’re an engineer, manufacturer, or product designer, understanding these processes is essential for optimizing production efficiency and cost-effectiveness.
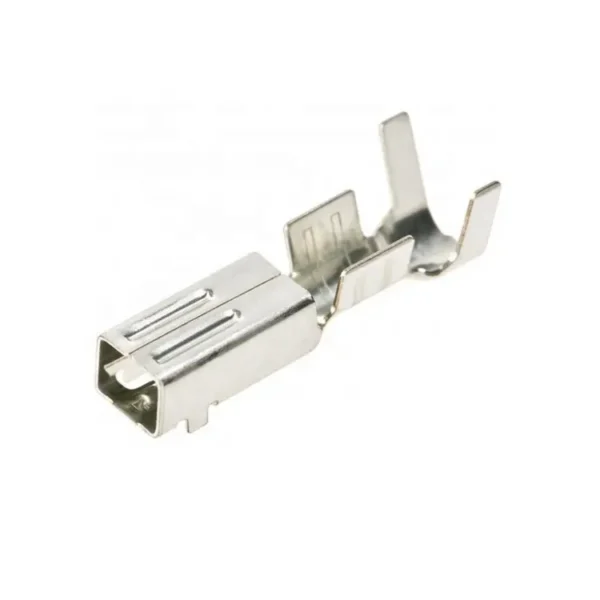
Precision electric cable copper stamping components showcasing intricate metal forming capabilities
What is Metal Stamping and How Does it Work?
Metal stamping is a cold-forming manufacturing process that transforms flat sheet metal into desired shapes using specialized dies and presses. The process begins when raw material, typically in the form of metal sheets or coils, is fed into a stamping press. The press uses tool and die components to perform various operations like cutting, bending, and forming.During the stamping process, a punch or press applies force to shape the workpiece against a die. This creates precise, repeatable parts through plastic deformation of the material. Electric cable copper stamping demonstrates how this process creates intricate electrical components.
Understanding Die Casting: Process and Applications
Die casting involves injecting molten metal into a mold cavity under high pressure. Unlike stamping, this process works with liquid metal that solidifies within the die to create complex parts. The process is particularly effective for:
- Complex geometries
- High-volume production
- Parts requiring excellent surface finish
- Components with internal features
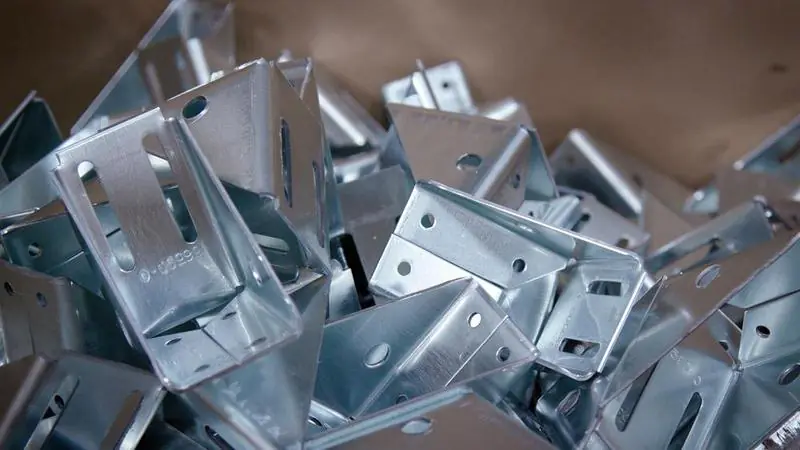
Types of Metal Stamping Operations
Several stamping techniques are available depending on part requirements:
- Progressive Die Stamping
- Multiple operations in sequence
- Continuous production
- Ideal for high volumes
- Transfer Die Stamping
- Separate dies for each operation
- Suitable for larger parts
- More flexible than progressive stamping
- Four-way stamping
- Multiple tools working simultaneously
- Efficient for complex parts
- Reduces cycle time
Advantages and Disadvantages of Each Process
Metal Stamping Benefits:
- Lower cost per part in high volumes
- Excellent material strength
- Fast production rates
- Consistent quality
Die Casting Benefits:
- Complex geometries possible
- Excellent surface finish
- Good dimensional accuracy
- Wide range of alloys available
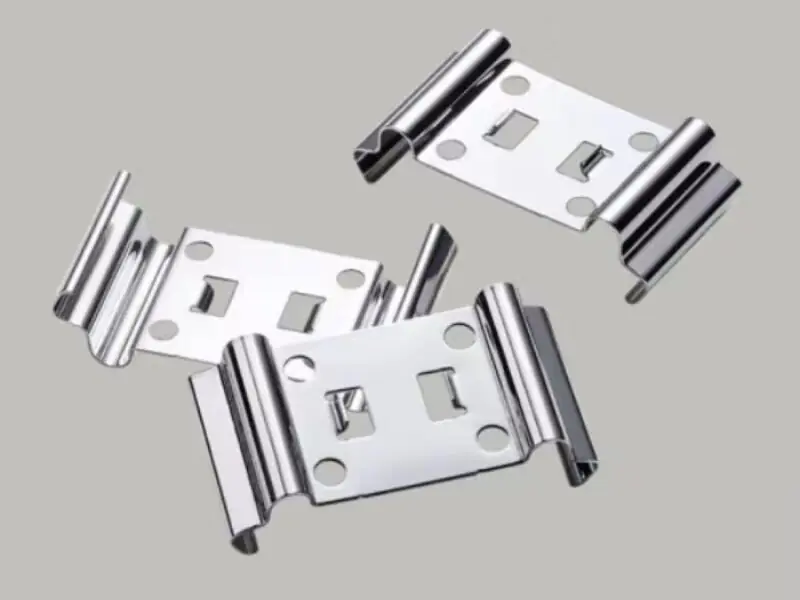
Key Factors in Choosing Between Stamping and Die Casting
Consider these aspects when selecting a process:
Factor | Metal Stamping | Die Casting |
---|---|---|
Production Volume | High volumes | Medium to high |
Part Complexity | Moderate | High |
Material Options | Sheet metals | Various alloys |
Tooling Costs | Lower | Higher |
Lead Time | Shorter | Longer |
Common Applications and Industries
Both processes serve various industries:
- Metal Stamping Applications:
- Automotive brackets and chassis components
- Electrical connectors
- Consumer electronics housings
- Die Casting Applications:
- Engine components
- Pump housings
- Telecommunications equipment
Important Considerations for Manufacturing Success
To ensure successful production:
- Consider design for manufacturability
- Evaluate material selection carefully
- Account for tooling costs
- Plan for appropriate production volumes
- Factor in secondary operations
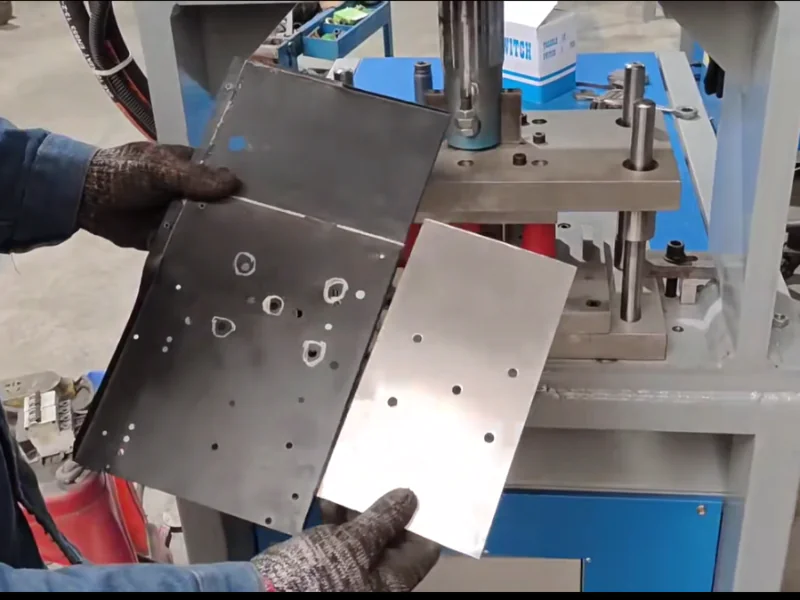
Key Takeaways:
- Metal stamping excels in high-volume sheet metal production
- Die casting is optimal for complex geometries
- Material selection impacts process choice
- Production volume affects cost-effectiveness
- Both processes have distinct advantages for specific applications
Internal Links Used: